introduction
As an emerging industry technology, LED lighting is constantly exploring wider applications. For AC power input applications, flyback topology switching power supplies are currently commonly used. Flyback topology switching power supplies include input rectifier filter circuits, switch control circuits, isolation transformers, and secondary rectifier filter circuits. However, the flyback power supply circuit is not efficient, and some LED lighting applications do not necessarily require isolation. Therefore, it is necessary to develop low-cost and cost-effective non-isolated LED driver circuits.
The International Electrotechnical Commission (IEC) has put forward clear harmonic requirements for lighting fixtures, namely the IEC61000-3-2 standard. At the same time, the latest Energy Star standard requires that the power factor index (PF) of LED lighting products greater than 5W must be greater than 0.7.
This paper proposes a new high power factor non-isolated LED driver circuit, which combines a current-by-current power factor correction circuit and a Buck-boost switching power supply circuit using primary-side control. The circuit structure is simple and meets the requirements of high power factor, high efficiency, compliance with electromagnetic compatibility (EMC) standards, high current control accuracy, high reliability, small size, and low cost of the LED driver power supply.
AP3766 Overview
AP3766 is the latest LED dedicated driver control chip launched by BCD. It uses primary side regulation control (PSR) technology to achieve high-precision constant voltage/constant current (CV/CC) output, eliminating the secondary side optocoupler and constant voltage and constant current control circuit, and does not require a loop compensation circuit to achieve stable control of the circuit. It uses a small SOT-23-6 package, which significantly reduces the system size and reduces the system cost. AP3766 has a patented "sub-microampere starting current" technology, which reduces system power consumption and improves efficiency. It can make the efficiency greater than 80% and the no-load power consumption less than 30mW. AP3766 has built-in external component temperature change compensation and constant current CC tightening technology to achieve vertical CC characteristics, ensuring ±5% output constant current accuracy under mass production. At the same time, AP3766 has built-in soft start, overvoltage protection, and short circuit protection functions to improve system reliability.
AP3766 has strong system adaptability and can be used with passive PFC current-following circuits, output totem pole drive circuits and other peripheral circuits to meet high power factor requirements and higher power output. Therefore, AP3766 can be used not only in GU10 spotlights and E27 bulbs, but also in PAR lamps, straight tube lamps, etc.
Figure 1 is the pin diagram of AP3766.
Figure 1. AP3766 pin diagram
Non-isolated solution system specification requirements
The light efficiency of LED is constantly moving towards higher indicators. At present, one measure to improve the light efficiency is to use multiple small current LED grains in series to form a high-voltage and small current LED package structure. Such a structure not only improves the light efficiency of LED, but also helps to improve the overall efficiency of the switching power supply. However, due to the relatively high operating voltage of LED, the traditional isolated flyback switching power supply is no longer applicable. Because to achieve a very high output voltage, the output winding of the isolation transformer of the flyback switching power supply requires a relatively large number of turns, the volume of the transformer will be greatly increased, the coupling between the primary and secondary sides will decrease, and the circuit efficiency will also decrease. In response to the system specification requirements of high-voltage and low-current output and high efficiency, this article proposes a new Buck-boost switching power supply circuit with high power factor, simple and novel control method, small number of components, small size, and high cost performance. The following will introduce in detail a high power factor non-isolated LED driver power supply with an output specification of 110V/60mA.
Circuit Schematic
Figure 2. Schematic diagram of high power factor non-isolated LED driver circuit based on AP3766
In Figure 2, F1 is a fuse, VR1 is a lightning protection varistor, and C1, L1, and C2 form a π-type EMI filter. C3, C4, D2, D3, and D4 form a current-following circuit to achieve the power factor correction function. The principle of the current-following circuit to improve the power factor of the rectifier circuit is to increase the conduction angle of the rectifier circuit. When the input AC voltage is greater than half of the peak voltage, the rectifier bridge BD1 can be turned on, avoiding the problem of large current spikes and waveform distortion caused by the traditional uncontrolled rectifier circuit that can only be turned on instantaneously near the peak of the AC voltage, thereby reducing the total harmonic distortion, that is, THD.
After passing through the current-by-current circuit, the Buck-boost switching power supply circuit composed of L1, L2, Q1, D1, and C9 completes the buck-boost and constant current output functions, and the control chip U1 realizes the switch control function of the Buck-boost switching power supply circuit. Inductors L1, L2, and L3 are coupled to each other through the magnetic core T1.
The working principle of the Buck-boost switching power supply circuit using the primary switch control method is: set in a switching cycle, the on-time of the output diode D1 is Tons, the off-time is Toffs, the output current peak is Ipk, the number of turns of the coupled inductor L1 winding is N1, and the number of turns of the coupled inductor L2 winding is N2. The control chip U1 controls the switch duty cycle to keep the ratio of the on-time Tons and the off-time Toffs of the output diode D1 constant. Then, in a switching cycle, the average value of the output current is:
Figure 3 shows the current waveform of the Buck-boost switching power supply circuit passing through diode D1
Figure 3 Current waveform of diode D1
According to Ampere's theorem, the output current peak value Ipks when the output diode D1 is just turned on has the following relationship with the switch Q1 current peak value Ipk:
Therefore, the average value of the output current is:
The control chip U1 detects the primary switch current and controls the primary switch current peak value Ipk to be constant. At the same time, it controls the switch duty cycle to keep the ratio of the on time Tons and the off time Toffs of the output diode D1 constant, thereby achieving a constant output current.
In Figure 2, resistors R1 and R9 are the startup resistors of chip U1, connected to the VCC pin of the chip, and provide a certain amount of startup current to the chip after the circuit is powered on. L3 is an auxiliary winding, which forms the power supply circuit of chip U1 with D5 and C7. At the same time, the voltage of the auxiliary winding of L3 is divided by resistors R6 and R7 and connected to the FB pin of the chip as an output voltage detection and protection circuit. R2 is the current detection resistor of switch Q1, connected to the CS pin of the chip, that is, the current sampling pin of U1. Pin 2 GND of chip U1 is connected to the ground potential, and pin 1 is the output drive pin, which outputs a PWM signal with a certain pulse width to control the opening and closing of switch Q1.
In Figure 2, transformer T1 uses EE16 core and has three windings. The inductance of the primary winding L1 is 1mH, and the turns ratio of L1, L2 and L3 is 100:100:28. The circuit is designed to work at a frequency of 65KHz.
Experimental Results
Based on the above circuit design, the experimental test results of relevant performance indicators are as follows:
The conducted EMI test results are shown in Figure 4:
Figure 4 Conducted EMI test results
The test results show that within a wide input voltage range of 85V to 265V, the circuit has a power factor of approximately 0.8 and an efficiency greater than 85%, meeting various LED driver power supply specifications such as EMI standards.
in conclusion:
This paper proposes a high power factor non-isolated LED driver power supply solution based on AP3766. The control method is simple and novel, and it achieves high power factor, high efficiency and constant current output in the full voltage range. It has the outstanding advantages of small number of components, small size and high cost performance. At the same time, it meets the requirements of high power factor, high efficiency, compliance with electromagnetic compatibility EMC standards, high current control accuracy, high reliability, small size and low cost of LED driver power supply.
Previous article:LED lighting provides wireless Internet access
Next article:A brief introduction to intelligent LED lighting systems and sensor technology
Recommended ReadingLatest update time:2024-11-16 22:02
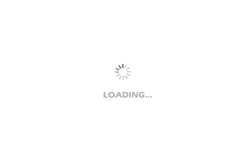
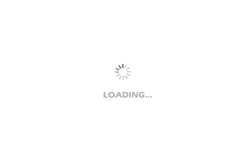
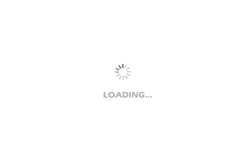
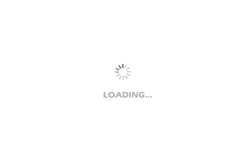
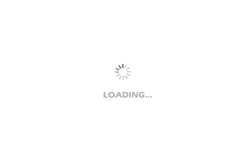
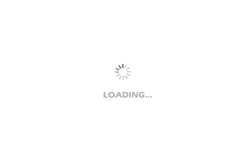
- Popular Resources
- Popular amplifiers
- MathWorks and NXP Collaborate to Launch Model-Based Design Toolbox for Battery Management Systems
- STMicroelectronics' advanced galvanically isolated gate driver STGAP3S provides flexible protection for IGBTs and SiC MOSFETs
- New diaphragm-free solid-state lithium battery technology is launched: the distance between the positive and negative electrodes is less than 0.000001 meters
- [“Source” Observe the Autumn Series] Application and testing of the next generation of semiconductor gallium oxide device photodetectors
- 采用自主设计封装,绝缘电阻显著提高!ROHM开发出更高电压xEV系统的SiC肖特基势垒二极管
- Will GaN replace SiC? PI's disruptive 1700V InnoMux2 is here to demonstrate
- From Isolation to the Third and a Half Generation: Understanding Naxinwei's Gate Driver IC in One Article
- The appeal of 48 V technology: importance, benefits and key factors in system-level applications
- Important breakthrough in recycling of used lithium-ion batteries
- Innolux's intelligent steer-by-wire solution makes cars smarter and safer
- 8051 MCU - Parity Check
- How to efficiently balance the sensitivity of tactile sensing interfaces
- What should I do if the servo motor shakes? What causes the servo motor to shake quickly?
- 【Brushless Motor】Analysis of three-phase BLDC motor and sharing of two popular development boards
- Midea Industrial Technology's subsidiaries Clou Electronics and Hekang New Energy jointly appeared at the Munich Battery Energy Storage Exhibition and Solar Energy Exhibition
- Guoxin Sichen | Application of ferroelectric memory PB85RS2MC in power battery management, with a capacity of 2M
- Analysis of common faults of frequency converter
- In a head-on competition with Qualcomm, what kind of cockpit products has Intel come up with?
- Dalian Rongke's all-vanadium liquid flow battery energy storage equipment industrialization project has entered the sprint stage before production
- Allegro MicroSystems Introduces Advanced Magnetic and Inductive Position Sensing Solutions at Electronica 2024
- Car key in the left hand, liveness detection radar in the right hand, UWB is imperative for cars!
- After a decade of rapid development, domestic CIS has entered the market
- Aegis Dagger Battery + Thor EM-i Super Hybrid, Geely New Energy has thrown out two "king bombs"
- A brief discussion on functional safety - fault, error, and failure
- In the smart car 2.0 cycle, these core industry chains are facing major opportunities!
- The United States and Japan are developing new batteries. CATL faces challenges? How should China's new energy battery industry respond?
- Murata launches high-precision 6-axis inertial sensor for automobiles
- Ford patents pre-charge alarm to help save costs and respond to emergencies
- New real-time microcontroller system from Texas Instruments enables smarter processing in automotive and industrial applications
- When shopping on Taobao, be careful not to cancel the order
- How to understand Howland circuit
- LLC design information collection (for learning only)
- Do the read and write registers of the ds2438 coulomb meter have a lifespan?
- Raspberry Pi based smartphone
- [SC8905 EVM Evaluation] + MCU I2C Communication Experiment
- Share WB-Serial Port Debugging Assistant
- TPS546D24_C23 dynamic voltage regulation
- Application of “C2000+TMS570” dual-chip solution in automotive electric drive functional safety
- Cleaning Techniques for the Pressure Pipe of Intelligent Pressure Controller