Charges high-capacity batteries from any 5V source while maintaining cool operation
Designers of portable electronics face the challenge of developing devices that can do everything and run forever on a single battery charge. While it is impossible to completely solve this problem, each generation of battery technology advances is at least getting closer to the goal. As many portable devices now have large, brightly colored touchscreen displays, multi-core CPUs and graphics processors, and a variety of wireless modems for high-speed communications anywhere on the planet, high-capacity batteries are essential. Battery manufacturers have met these requirements with lightweight, compact batteries that have capacities exceeding 30 watt-hours (Wh).
While USB has become the dominant standard for device interconnection, synchronization, and data exchange, its power delivery capabilities have not kept pace with the demands of batteries. USB 2.0 allowed a maximum load of 2.5W, and USB 3.0 increased that limit to 4.5W. Even with ideal efficiency, and with all the power going directly to the battery, a full charge cycle using USB would still take overnight. While USB is not suitable as a primary power source for large batteries, it is still of great value to have this power source when possible, and to avoid battery drain when the device is connected to a traditional computer.
Best of both worlds
The LTC4155 is a monolithic switching battery charger that efficiently delivers 3.5A of charge current in a compact PCB footprint. Figure 1 shows the components required in a typical application. The 2.25MHz switching frequency allows the use of small inductors and bypass capacitors, minimizing the overall PCB footprint.
Figure 1: I2C controlled high power battery charger/USB power manager
Even at charging currents of several amps, high efficiency (Figure 2) is critical not only for making optimal use of available input power, but also for controlling power dissipation within a portable device. The combination of high power dissipation and subpar thermal performance in a tightly enclosed space will make a device with an inefficient charging solution too hot to be comfortable for the user to hold. To help keep the device running cool, the LTC4155's integrated power switch has an on-resistance well below 100mΩ.
Figure 2: Switching regulator efficiency
Although the LTC4155 power switch is specified to handle currents above the USB limit, the LTC4155 maintains full compatibility with the USB specification for charging. The input current is automatically measured internally and limited to any of 16 I2C user-selectable values. Of these settings, three correspond to guaranteed maximum limits: 100mA and 500mA (for USB 2.0) and 900mA (for USB 3.0). In addition, the automatic input current limit function can also be used with an AC adapter or other power source by selecting any of the other current limit settings up to a maximum of 3A.
The LTC4155 supports a pin-programmable power-up default input current. For high power applications that do not require USB compatibility, a single resistor connected to the CLPROG1 pin sets a default power-up input current. The resistor is selected to correspond to an initial current limit that best suits the specific application and expected power supply capabilities. After power-up, the input current limit can be modified under I2C control to any of 16 other available settings (up to 3A).
For USB applications, the CLPROG1 and CLPROG2 pins can be tied together to set the LTC4155 to implement USB current limiting rules. When external power is applied, the input current limit will default to 100mA. After successful enumeration with the USB host controller, the input current limit setting can be appropriately increased to 500mA or 900mA under I2C control. Figure 3 shows the available current to the system load and battery charger. Note that the switching regulator output current is greater than the input current limited by the USB specification. If the system detects that the power source is an AC adapter, dedicated USB charger, or other non-USB type power source, the input current limit setting can be increased to any other setting (up to 3A) under I2C control.
Figure 3: Available load current per USB specification (before battery discharge)
Seamless handling of multiple input connectors
The LTC4155 can choose to accept input from one of two power sources, thus solving the problem of neatly delivering power to a product from two different physical connectors. When two input sources are connected simultaneously, the decision of which source to use is based on a user-settable priority. As long as each input voltage is within the valid operating range, it is OK to choose either one, regardless of which voltage is higher. For example: This allows a 4.5V/2A AC adapter to take priority over a 5V/500mA USB port. If the USB connection is removed and a 5V/3A AC adapter is connected to the same port, the input power priority can be modified via I2C to switch to the new higher power source.
The LTC4155 supports independent I2C programmable input current limits for each of its two supply inputs. When the higher priority input supply is disconnected, charging continues uninterrupted and is automatically reduced to the new lower maximum input current limit. No direct intervention by the system microcontroller is required.
Depending on the external components selected for the input multiplexer, overvoltage and reverse voltage protection up to ±77V can be easily implemented if the application requires it. In addition, the LTC4155 can generate a USB On-The-Go 5V current limited supply for the USB connector without the use of any additional external components. [page]
Rich programmability and telemetry for implementing advanced charging algorithms
The LTC4155 provides continuous I2C status reporting, providing system software with comprehensive visibility into the state of input supplies, fault conditions, battery charge cycle status, battery temperature and many other performance parameters.
Key charging parameters can be changed under I2C control to implement a custom charging algorithm. Unlike microcontroller-based or other programmable charging algorithms, all possible settings available to the LTC4155 under software I2C control are targeted at the intrinsic safety of the battery. The float voltage can never be set above 4.2V or below 4.05V. Likewise, the battery charge current can be set to one of 15 possible settings, but the software can never raise the limit above the level set by the designer—through a programming resistor selected to match the battery capacity to the maximum charge rate.
Continuous battery temperature data can be provided to the system software to dynamically adjust the system or charger operating state to cope with extreme operating conditions. For example, the float voltage and/or charge current can be reduced under I2C control to increase the battery safety margin at high ambient temperatures. Similarly, the charge current or total system load current can be reduced with high temperature to reduce additional heating inside the product housing.
As with all other aspects of battery charger programmability, the LTC4155 enables an intrinsically safe charging solution that does not require any software intervention. Battery charging is always suspended when the battery temperature drops below 0°C or rises above 40°C. In addition, a fault interrupt can optionally be generated when the battery temperature rises above 60°C. Figure 4 shows the transfer function of the LTC4155 battery temperature data converter and highlights the autonomous charger cut-off temperature thresholds.
Figure 4: Transfer function of the LTC4155 battery temperature data converter (highlighting the autonomous charger cut-off temperature threshold)
Power Path Instant-On Operation
In traditional power architectures, most portable products are connected directly to the battery, so a dead battery is particularly susceptible to failure. When the battery voltage is so low that the system cannot operate, the product may appear unresponsive, even after being connected to an input power source for several minutes, which can lead to many inquiries. This problem is further complicated when the battery capacity is very large compared to the available charging current (for example: USB-powered systems with large capacity batteries).
Linear Technology's PowerPath™ products, such as the LTC4155, isolate the system power rail from the battery to enable instant-on operation and solve the two most frustrating problems caused by deeply discharged batteries.
The first problem is that when the system power rail is connected directly to the battery, the charge current becomes indistinguishable from the system load. When the battery is deeply discharged, battery manufacturers recommend that users use a much reduced initial charge current until the battery voltage reaches a safer level. This trickle charge current must be set to a safe level for the battery, assuming minimal or no system load current.
Second, in a direct-connected battery system, if the system is available during the trickle charge period, a significant portion of the charge current intended for the battery will be diverted to the system power rail. The resulting reduced battery charge current will extend the recovery time accordingly. A large system load will cause the net battery current to reverse, further discharging the battery. In this low-battery condition, the portable system may not respond to user actions due to insufficient voltage on the system power rail. The duration of unresponsiveness will increase by at least 10 times due to the reduced power available to the commonly connected battery and system power rails.
When the battery is deeply discharged, the LTC4155 can provide 3.5V to the system power rail for instant startup. As the battery voltage rises during the pre-charge phase, the LTC4155 seamlessly and automatically transitions to a more efficient mode to speed charging and minimize heat generation. Figure 5 shows the voltage available to the system power rail as a function of the battery voltage.
Figure 5: VOUT voltage vs. battery voltage
The LTC4155 battery charge current is set independently of the input current limit to eliminate the interaction between the battery charge current limit and the input power limit. The input current limit can be set based solely on the input power supply limit. Similarly, the battery charge current can be set based solely on the battery capacity. The LTC4155 always enforces input current limit and prioritizes "powering the system load" over "battery charging" when necessary.
Robustness in the face of non-ideal power supplies
The LTC4155 automatically reduces input current when the input voltage begins to drop to an unacceptable level. This can occur at high charge current levels, when connected to an undersized adapter through a slightly corroded connector using undersized wires, or any number of conditions outside of typical design ranges.
Without intervention, the IC's input voltage will continue to drop and eventually fall below the undervoltage lockout threshold. The IC will then shut down, allowing the input voltage to recover and restart the entire cycle. The LTC4155 does the best of a bad situation. When the input voltage drops to 4.3V, the LTC4155 can smoothly reduce its input power as required to avoid further drops in the input voltage. In this mode, although the current delivered to the system load and battery is less than the programmed value, this value will be smaller if the input voltage oscillation is allowed to continue. In addition, the LTC4155 can also generate an I2C status report and optional interrupt signal to alert the system: the end user may need to take corrective or diagnostic measures to restore the maximum charge current capability.
in conclusion
The LTC4155 combines high current capability and high efficiency with a small monolithic PCB footprint, making it ideal for portable devices with large lithium batteries, where board space is highly valued while minimizing heat and charging time. USB-compatible input current limit settings further extend versatility, allowing charging from ubiquitous but low-power sources. Extensive telemetry enables customized operating states based on changing environmental or application conditions without sacrificing self-contained battery safety. Despite common problems such as deep battery discharge or undersized resistive input power cables, power can still be delivered to the system power rail uninterruptedly. The LTC4155 is available in a 28-pin 4mm x 5mm QFN package.
Previous article:Intelligent lithium battery charging management solution
Next article:Power Management Architecture for Energy Harvesting Applications
Recommended ReadingLatest update time:2024-11-16 15:31
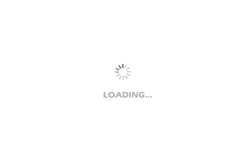
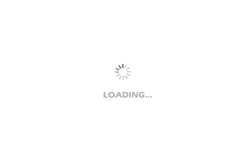
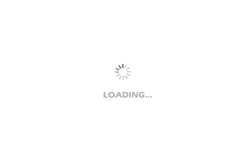
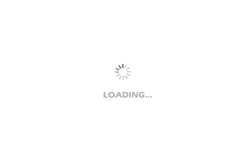
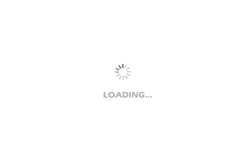
- MathWorks and NXP Collaborate to Launch Model-Based Design Toolbox for Battery Management Systems
- STMicroelectronics' advanced galvanically isolated gate driver STGAP3S provides flexible protection for IGBTs and SiC MOSFETs
- New diaphragm-free solid-state lithium battery technology is launched: the distance between the positive and negative electrodes is less than 0.000001 meters
- [“Source” Observe the Autumn Series] Application and testing of the next generation of semiconductor gallium oxide device photodetectors
- 采用自主设计封装,绝缘电阻显著提高!ROHM开发出更高电压xEV系统的SiC肖特基势垒二极管
- Will GaN replace SiC? PI's disruptive 1700V InnoMux2 is here to demonstrate
- From Isolation to the Third and a Half Generation: Understanding Naxinwei's Gate Driver IC in One Article
- The appeal of 48 V technology: importance, benefits and key factors in system-level applications
- Important breakthrough in recycling of used lithium-ion batteries
- Innolux's intelligent steer-by-wire solution makes cars smarter and safer
- 8051 MCU - Parity Check
- How to efficiently balance the sensitivity of tactile sensing interfaces
- What should I do if the servo motor shakes? What causes the servo motor to shake quickly?
- 【Brushless Motor】Analysis of three-phase BLDC motor and sharing of two popular development boards
- Midea Industrial Technology's subsidiaries Clou Electronics and Hekang New Energy jointly appeared at the Munich Battery Energy Storage Exhibition and Solar Energy Exhibition
- Guoxin Sichen | Application of ferroelectric memory PB85RS2MC in power battery management, with a capacity of 2M
- Analysis of common faults of frequency converter
- In a head-on competition with Qualcomm, what kind of cockpit products has Intel come up with?
- Dalian Rongke's all-vanadium liquid flow battery energy storage equipment industrialization project has entered the sprint stage before production
- Allegro MicroSystems Introduces Advanced Magnetic and Inductive Position Sensing Solutions at Electronica 2024
- Car key in the left hand, liveness detection radar in the right hand, UWB is imperative for cars!
- After a decade of rapid development, domestic CIS has entered the market
- Aegis Dagger Battery + Thor EM-i Super Hybrid, Geely New Energy has thrown out two "king bombs"
- A brief discussion on functional safety - fault, error, and failure
- In the smart car 2.0 cycle, these core industry chains are facing major opportunities!
- The United States and Japan are developing new batteries. CATL faces challenges? How should China's new energy battery industry respond?
- Murata launches high-precision 6-axis inertial sensor for automobiles
- Ford patents pre-charge alarm to help save costs and respond to emergencies
- New real-time microcontroller system from Texas Instruments enables smarter processing in automotive and industrial applications
- 【NXP Rapid IoT Review】Environmental Quality Test
- [ATmega4809 Curiosity Nano Review] Installing MCC
- GD32E231C-START Unboxing
- X-NUCLEO-IKS01A3 sensor test based on STM32F401RE development board 5L
- Simulation failed with no results
- Principle of Dialogue Communication
- Voltage jump problem
- 【McQueen Trial】Main functions corresponding to driver pins
- ti dsp (tms320VC5502) + isp1581 usb2.0 high speed data acquisition solution
- Tesla's electric motor