summary
Average current mode control (CMC) requires the reconstruction of the total current waveform for the control loop. This article shows you some of the steps required to select a specific transformer and how to design a circuit that can meet the requirements of the end application to resist transformer saturation. The model used is a power factor correction (PFC) topology. A commercial current sense transformer will be used in the analysis to determine the required parameters and understand how to use this information to design a circuit that can resist saturation.
Overview
The current signal reconstruction target required to achieve the average CMC for the PFC means that both the current during the power pulse (“on” time) and the current during the idle energy recovery time (“off” time) must be included in the generated current signal. At high power PFC, the losses in the resistive sensor system are very high, so a current transformer is required. In the analysis, we justify the design of this current transformer required in the PFC circuit, as it has more stringent requirements than the standard forward converter.
analyze
Figure 1 shows the model used in this discussion.
Figure 1 Schematic diagram of a power factor control converter power stage, including detailed current sense transformer parameters needed to explain the current sense circuit design.
Table 1 lists the specific details used to correctly identify the two current transformers used in this converter. The IinLpk current indicates that the required current transformer has a primary current handling capability of approximately 20 amps and a switching frequency of 100 kHz. A PA 1005.100 current transformer with a primary current handling capability of 20 amps and a frequency range of 50 kHz to 1 MHz can meet the requirements of this design.
Table 1 Parameters required for PFC design
Table 2 Current transformer product specifications
These two tables list the information needed to distinguish these parameters.
The peak current in the secondary winding can be easily calculated (Equation 1):
IRsenseL = IinLpk/N = 0.183 A
The sense resistor value is calculated using the following equation (Equation 2):
R1 = VRsense / IRsenseL = 5.464 .
Assuming the converter is operating at maximum load and minimum input voltage, the voltage across the secondary winding can be calculated. This total voltage is composed of the voltage across the current sense resistor Rsense (defined as 1 volt), the diode voltage (defined as 0.7 volts), and the voltage across the winding resistance VRwinding, and is calculated as follows ( Equation 3 ):
VRwinding = Rwinding * IRsenseL = 1.007 V
The total inductor voltage is calculated as follows ( Equation 4 ):
Vind = VRsense +Vfd + VRwinding = 2.707 V
The time duration for which this voltage appears across the magnetizing inductance is ( Equation 5 ):
TonL = DL / Fosc = 6.995 s
The change of magnetizing inductance and magnetizing current is ( Equation 6 ):
Imagpk = (TonL * Vind) / Lmag = 9.466 mA
At this point, you need to make sure that the transformer is not saturated. Using the derived values, the calculation equation is as follows ( Equation 7 ):
Bpk = (37.59 * Vind* DL*10 5 )/(N*Fosc*10 -3 ) = (37.59 * 2.707 * 0.699 * 10 5 )/(100 * 10 5 * 10 -3 ) = 711.6
According to the product manual, the maximum permissible flux level is around 30%, or 2000.
Since the flux density for this configuration is obtained under extreme conditions, it is less than half of the flux level that easily produces saturation, so as long as it can be sharply reduced during the "off" time, the magnetizing current can be allowed to increase (in this case almost three times the original value).
To prevent the transformer from "going" to saturation, you need to have a volt-second integral during the off time of Q1. This will balance the volt-second integral during the "on" time. This is accomplished by placing a resistor R1 (called the reset resistor) so that the magnetizing current developed during the "on" period forces a volt across the reset resistor (R1) during the "off" period. Remember that the voltage across this resistor drops as the magnetizing current decreases.
To find the value of R1, set the peak magnetizing current to 2 * DImagpk, and then design the circuit so that the selected resistor reduces the magnetizing current to 0.5 * DImagpk during the "on" period. This ensures normal operation with peak currents below 2 * DImagpk.
The initial current of the magnetizing inductance is set to Iinit = 20 mA, and the final magnetizing current is set to Ifinal = 5 mA. The "off" time is Toff = 3.005 μs, and the magnetizing inductance Lmag of the selected transformer is 2 mH (from the data sheet). Knowing this information, the value of the R1 resistor can be obtained ( Equation 8 ).
R1= ((ln(Iinit/Ifinal)) * Lmag) / Toff) = ((ln(4)) * 2 mH) / (3.005 μs) = 922.6Ω
At this point, half of the solution is complete. You still need to solve the design problem of the current transformer circuit for the boost diode current sensor. The extreme case of the T2 current transformer is the peak maximum line voltage at maximum load.
The main switch "on" time at the high line voltage peak is the maximum conduction time of the rectifier diode D3 and the primary winding of the T2 current transformer. This is the state that will be used for the design.
Since the same primary current requires the same current sense resistor voltage, the Rsense used by both transformers is also the same. The conduction time of the current in the primary winding of T2 is (1-D). The maximum conduction time of the primary winding of the transformer is ( Equation 9 ):
Tondiode = (1-DH) / Fosc = 9.369 μs
The corresponding reset time of the transformer is ( Equation 10 ):
Toffdiode = DH / Fosc = 0.631 μs
Under these conditions (maximum input voltage) the current in the primary winding of the T2 transformer is much lower than at low input voltages. At high line voltage, the maximum current IinHpk is only 5.87 amps.
This gives the sense resistor voltage under these conditions ( Equation 11 ):
VRsencehigh = (IinHpk / N) * R2 = ((5.87 A) / 100) * 5.464 Ω = 0.292 V
The voltage across the internal winding resistance is ( Equation 12 ):
VRwindingH = (IinHpk / N) * Rwinding = 0.294 V
The voltage across the transformer magnetizing inductance is equal to ( Equation 13 ):
VmagHigh = VRsencehigh + Vfd + VRwindingH = 0.292 V + 0.7 V + 0.294 V = 1.285 V
The core flux of a single pulse is ( Equation 14 ):
BpkH = (37.59 * VmagHigh * (1-DH) * 10
5
) / (100 * Fosc *10
-3
)
= (37.59 * 1.285 * .937 *10
5
) / (100 * 10
5
*10
-3
) = 452.6
The flux is about 25% of the allowed flux.
The magnetizing current is calculated as follows ( Equation 15 ):
ImagH = (VmagHigh * Tondiode )/ Lmag = (1.285 V * 9.369μs) / 2 mH = 6.02ma
Now, if we set the magnetizing current limit to twice the peak value of ImagH, the final current will be half of ImagH for a time of TresetH, where TresetH = DH/Fosc, which allows us to calculate the value of R2 ( Equation 16 ):
R2 = ((ln(2/.5)) *Lmag) / TresetH = (1.386 * 2 *10 -3 ) / (.631 * 10 -6 ) = 4.395 kΩ
in conclusion
At this point, we have completed the design of the PFC current sensing circuit. The calculation method used for the average current mode control of the buck converter is similar to this. When using the buck converter peak current mode control, just use the above calculation method and use the main switch duty cycle limitation at maximum load and minimum input voltage.
The PFC controller commonly used in PFC converters above 1 kW is the UCC2817a. At higher powers, the current sensing transformer introduced in this article can be used to measure the current of the power FET and the output diode.
References
The UCC2817a datasheet can be downloaded from www.ti.com/ucc2817a-ca.
For more information on TI power solutions, please visit www.ti.com/power.
Previous article:Transformer cooling method
Next article:Why can't the transformer be used as a symbol to distinguish between two types of UPS?
Recommended ReadingLatest update time:2024-11-16 19:54
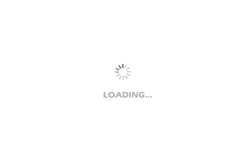
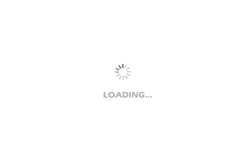
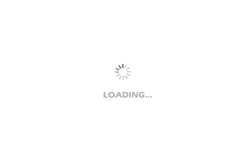
- Popular Resources
- Popular amplifiers
-
Analysis of EMI mechanism and winding method to reduce distributed capacitance of toroidal PFC inductor
-
Switching Power Supply Simulation and Design - Based on SPICE (Second Edition)
-
开关电源设计与制作基础 (蔡宣三,倪本来编著)
-
Introduction to Transformer Natural Language Processing: Solving Problems with Hugging Face Libraries and Models
- MathWorks and NXP Collaborate to Launch Model-Based Design Toolbox for Battery Management Systems
- STMicroelectronics' advanced galvanically isolated gate driver STGAP3S provides flexible protection for IGBTs and SiC MOSFETs
- New diaphragm-free solid-state lithium battery technology is launched: the distance between the positive and negative electrodes is less than 0.000001 meters
- [“Source” Observe the Autumn Series] Application and testing of the next generation of semiconductor gallium oxide device photodetectors
- 采用自主设计封装,绝缘电阻显著提高!ROHM开发出更高电压xEV系统的SiC肖特基势垒二极管
- Will GaN replace SiC? PI's disruptive 1700V InnoMux2 is here to demonstrate
- From Isolation to the Third and a Half Generation: Understanding Naxinwei's Gate Driver IC in One Article
- The appeal of 48 V technology: importance, benefits and key factors in system-level applications
- Important breakthrough in recycling of used lithium-ion batteries
- Innolux's intelligent steer-by-wire solution makes cars smarter and safer
- 8051 MCU - Parity Check
- How to efficiently balance the sensitivity of tactile sensing interfaces
- What should I do if the servo motor shakes? What causes the servo motor to shake quickly?
- 【Brushless Motor】Analysis of three-phase BLDC motor and sharing of two popular development boards
- Midea Industrial Technology's subsidiaries Clou Electronics and Hekang New Energy jointly appeared at the Munich Battery Energy Storage Exhibition and Solar Energy Exhibition
- Guoxin Sichen | Application of ferroelectric memory PB85RS2MC in power battery management, with a capacity of 2M
- Analysis of common faults of frequency converter
- In a head-on competition with Qualcomm, what kind of cockpit products has Intel come up with?
- Dalian Rongke's all-vanadium liquid flow battery energy storage equipment industrialization project has entered the sprint stage before production
- Allegro MicroSystems Introduces Advanced Magnetic and Inductive Position Sensing Solutions at Electronica 2024
- Car key in the left hand, liveness detection radar in the right hand, UWB is imperative for cars!
- After a decade of rapid development, domestic CIS has entered the market
- Aegis Dagger Battery + Thor EM-i Super Hybrid, Geely New Energy has thrown out two "king bombs"
- A brief discussion on functional safety - fault, error, and failure
- In the smart car 2.0 cycle, these core industry chains are facing major opportunities!
- The United States and Japan are developing new batteries. CATL faces challenges? How should China's new energy battery industry respond?
- Murata launches high-precision 6-axis inertial sensor for automobiles
- Ford patents pre-charge alarm to help save costs and respond to emergencies
- New real-time microcontroller system from Texas Instruments enables smarter processing in automotive and industrial applications
- 2. ESP32-S2-Kaluga-1 development environment ESP-IDF construction
- Hikvision overseas version ball camera can not be used
- Today afternoon 14:00 live broadcast [Latest TI C2000 real-time control chip - F28003X]
- SPI slave returns data to the host in dislocation
- SensorTile.box V335 Firmware
- SensorTile.box IoT-related application supplementary content
- Introduction to DDS Principle (Chinese).pdf
- BlueNRG-1 adds DeviceInformation information
- [GD32L233C-START Review] 15. Flash erase and write operations, using FLASH as EEPROM
- [Original] [Ultra-low power STM32U5 IoT Discovery Kit] - 3: BLE-1