ESD electrostatic discharge brings fatal harm to your electronic products. It not only reduces the reliability of the product and increases the maintenance cost, but also affects the sales of the product in Europe if it does not comply with the industrial standard EN61000-4-2 stipulated by the European Community. Therefore, electronic equipment manufacturers usually consider ESD protection circuits in the early stages of circuit design. This article will discuss several methods of ESD protection circuits.
1. Generation and harm of ESD
Electrostatic discharge (ESD) occurs when two objects collide or separate, that is, static charge moves from one object to another. The movement of static charge between two objects with different electric potentials is similar to a small lightning process. The amount of discharge and the duration of the discharge depend on many factors such as the type of object and the surrounding environment. When the ESD has high enough energy, it will cause damage to semiconductor devices. Electrostatic discharge (ESD) may occur at any time, such as plugging and unplugging cables or human body touching the I/O port of the device, or a charged object touching the semiconductor device. The semiconductor device touches the ground, and the electrostatic field and electromagnetic interference generate a high enough voltage to cause electrostatic discharge (ESD).
ESD can basically be divided into three types. The first is ESD caused by various machines, the second is ESD caused by furniture movement or equipment movement, and the third is ESD caused by human contact or equipment movement. All three types of ESD are very important for the production of semiconductor devices and electronic products. Electronic products are most susceptible to damage from the third type of ESD during use, and portable electronic products are particularly susceptible to damage from ESD caused by human contact. ESD generally damages the interface devices connected to it. In another case, the device may not be damaged immediately after being hit by ESD, but its performance may degrade, causing the product to fail prematurely.
When an integrated circuit (IC) is subjected to ESD, the resistance of the discharge loop is usually very small and cannot limit the discharge current. For example, when a cable with static electricity is plugged into a circuit interface, the resistance of the discharge loop is almost zero, resulting in an instantaneous discharge peak current of up to tens of amperes. The instantaneous high current flowing into the corresponding IC pins will seriously damage the IC. The local heat generated may even melt the silicon chip die. ESD damage to the IC generally also includes the burning of internal metal connections, damage to the passivation layer, and burning of transistor units.
ESD can also cause IC latch-up (LATCHUP). This effect is related to the activation of thyristor-like structural units inside CMOS devices. High voltage can activate these structures to form a large current channel, generally from VCC to ground. The latch-up current of serial interface devices can be as high as 1 ampere. The latch-up current will remain until the device is powered off, but by then the IC has usually been burned out due to overheating. There may be two problems that are not easy to detect after an ESD shock. Generally, users and IEC test organizations use traditional loop feedback methods and insertion methods for testing and usually cannot detect these two problems.
1 The receiver in the RS-232 interface circuit generates crosstalk to the transmitter
The ESD protection structure in the RS-232 interface circuit of similar products may fail to a certain waveform of ESD or a certain ESD impulse voltage. After the ESD impulse, a path is formed between the receiver input and the transmitter output, causing the receiver to intermodulate the transmitter. Figure 1. If there is a shutdown circuit in the RS-232 interface circuit, it is more likely to cause intermodulation after the ESD impulse during the shutdown period. The intermodulation will cause communication failure, and even in the shutdown working state, the transmitter still has output, resulting in shutdown failure, putting the other party's RS-232 in the receiving state.
2 RS-232 interface circuit generates reverse drive for power supply
After an ESD shock, the ESD protection structure in some RS-232 interface circuits may form a current path between the input terminal and the power supply Vcc, which will cause a reverse drive on the power supply. If the power supply does not have the ability to absorb current, there is usually a forward diode in the power output loop, which will cause the power supply voltage Vcc to increase, thereby damaging the
The RS-232 interface circuit and other circuits in the system will be damaged because the voltage at the input end of the RS-232 interface circuit is between 5V and 25V, which makes Vcc greater than 9V and exceeds the maximum range of the power supply voltage, thus burning out the circuit.
2 ESD protection circuit
ESD is generated when two objects collide or separate, that is, static charge moves from one object to another. Therefore, the most effective protection against ESD is dielectric isolation, which is to use insulating media to isolate the internal circuit from the outside world. 1mm thick ordinary plastic such as PVC, polyester or ABS can protect 8KV ESD, but the actual medium cannot be without gaps and seams, so the creep of the material and the gap distance are very important. LCD displays, touch screens, etc. have very thick corners of 12mm to isolate the internal circuit.
The second effective method of ESD protection is shielding to prevent large ESD current from impacting the internal circuit. When ESD impacts the metal shielding shell, the voltage will be much higher than the protective ground voltage in the first few milliseconds. The voltage of the shielding shell will drop as the ESD charge is transferred, so a secondary ESD impact will be generated on the internal circuit in the first few milliseconds. Therefore, it is not enough to use only external shielding, but to share the ground with the internal circuit and the shielding shell or to isolate the internal circuit with dielectrics. Electrical isolation is also an effective way to suppress ESD impact on PCB. Although installing optocouplers and transformers on the board cannot completely eliminate ESD shocks, they can effectively suppress ESD shocks in combination with dielectric isolation and shielding. Optocouplers and transformers are especially suitable for the power supply signal path. The best isolation is optical fiber, wireless, and infrared. Another protection method for the signal path is to add resistors and capacitors to each signal line. The series resistor can limit the peak current, and the capacitor connected in parallel to the ground can limit the instantaneous peak voltage. This is low-cost, but the protection capability is limited. The destructive power of ESD is suppressed to a certain extent, but it still exists because the resistors and capacitors cannot reduce the peak value of the peak voltage, but only reduce the slope of the voltage rise. In addition, the resistors and capacitors can cause signal distortion, which limits the length of the communication cable and the communication rate. The external resistors/capacitors also increase the circuit board area.
Another widely used technique is to add a transient suppressor or TransZorb? diode. This protection is very effective, but there are still some disadvantages. The additional device still increases the board area. The capacitive effect of the protection device increases the equivalent capacitance of the signal line. The cost is high. TransZorb? diodes are expensive. About 25 cents/each. Typical 3 rounds/5
The received COM port requires 8 TransZorbs? The diode costs up to $2. An effective method is to use a serial interface device with internal integrated ESD protection function. This device is more expensive than ordinary devices without protection function, but the additional cost is lower than the cost of external protection diodes. The internally integrated ESD protection circuit will not increase the equivalent capacitance of any input and output pins, and also saves circuit board area. MAXIM has developed patented integrated ESD protection technology in recent years and can provide a full range of ESD protection serial interface devices, including products that are fully compatible with standard devices. MAXIM has also applied the same technology to analog switches and switch debounce products. The ESD protection capabilities of all these devices meet the 15kV IEC1000-4-2 air gap discharge 8kV IEC1000-4-2 contact discharge 15kV human body model HBM test standards. The following table shows MAXIM's devices with anti-static function.
3 MAXIM's ESD protection technology
The ESD protection stipulated by the European Community has strict testing standards
For normal operation, the ESD structure must be completely transparent
No latch-up during ESD
Must pass all relevant ESD test standards
15kV ESD Human Body Model Test Standard
8kV ESD IEC 1000-4-2 Contact Discharge Mode Test Standard
15kV ESD IEC 1000-4-2 Air Gap Discharge Mode Test Standard
4kV ESD IEC 1000-4-4 Electrical Fast Transient/Burst Mode Test Standard
The main difference between IEC 1000-4-2 and 15kV Human Body Model test standards is that the absorbed current of IEC 1000-4-2 impulse is more than 5 times higher than that of Human Body Model at the same peak current voltage. The 4kV ESD IEC 1000-4-4 electrical fast transient/burst mode test standard simulates the arc discharge results of switches and relays. MAXIM devices can provide 4kV protection, which is twice the 2kV indicator of the IEC 1000-4-4 standard.
In the real world, the waveforms generated by ESD may be of various types. Regardless of the waveform, MAXIM engineers have designed a highly adaptable structure to provide ESD protection for devices. Because the ESD threshold of each device is different, and the ESD threshold of each device in the normal working state, shutdown state and power-off state is different, MAXIM strictly follows the following steps for testing:
1 Start from 200V and increase by 500V each time. Apply voltage of different polarities to each device 10 times.
2 Check the supply current after each impulse to ensure that the device is not latching up. Check that the transmitter and receiver are working properly.
3 Repeat the above steps until the device is damaged or reaches the ESD tester's limit requirements
4 Repeat the above steps using human body method IEC 1000-4-2 contact discharge IEC 1000-4-2 air gap discharge and IEC 1000-4-4 fast/transient/burst
5 Repeat the test in normal working state, shutdown state and power-off state to ensure that the ESD protection test standard is met and no cross-modulation and back-drive problems occur.
Previous article:Positive Energy Enhances ZNDU Series Combination Power Supply ZNDU45 and ZNDU150 Solutions
Next article:Power Supply Design Tips: Understanding FFT Plots
Recommended ReadingLatest update time:2024-11-16 17:49
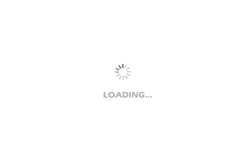
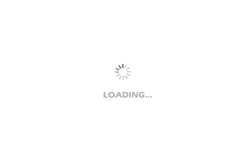
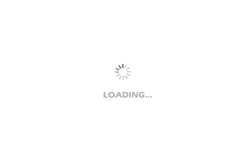
- Popular Resources
- Popular amplifiers
- MathWorks and NXP Collaborate to Launch Model-Based Design Toolbox for Battery Management Systems
- STMicroelectronics' advanced galvanically isolated gate driver STGAP3S provides flexible protection for IGBTs and SiC MOSFETs
- New diaphragm-free solid-state lithium battery technology is launched: the distance between the positive and negative electrodes is less than 0.000001 meters
- [“Source” Observe the Autumn Series] Application and testing of the next generation of semiconductor gallium oxide device photodetectors
- 采用自主设计封装,绝缘电阻显著提高!ROHM开发出更高电压xEV系统的SiC肖特基势垒二极管
- Will GaN replace SiC? PI's disruptive 1700V InnoMux2 is here to demonstrate
- From Isolation to the Third and a Half Generation: Understanding Naxinwei's Gate Driver IC in One Article
- The appeal of 48 V technology: importance, benefits and key factors in system-level applications
- Important breakthrough in recycling of used lithium-ion batteries
- Innolux's intelligent steer-by-wire solution makes cars smarter and safer
- 8051 MCU - Parity Check
- How to efficiently balance the sensitivity of tactile sensing interfaces
- What should I do if the servo motor shakes? What causes the servo motor to shake quickly?
- 【Brushless Motor】Analysis of three-phase BLDC motor and sharing of two popular development boards
- Midea Industrial Technology's subsidiaries Clou Electronics and Hekang New Energy jointly appeared at the Munich Battery Energy Storage Exhibition and Solar Energy Exhibition
- Guoxin Sichen | Application of ferroelectric memory PB85RS2MC in power battery management, with a capacity of 2M
- Analysis of common faults of frequency converter
- In a head-on competition with Qualcomm, what kind of cockpit products has Intel come up with?
- Dalian Rongke's all-vanadium liquid flow battery energy storage equipment industrialization project has entered the sprint stage before production
- Allegro MicroSystems Introduces Advanced Magnetic and Inductive Position Sensing Solutions at Electronica 2024
- Car key in the left hand, liveness detection radar in the right hand, UWB is imperative for cars!
- After a decade of rapid development, domestic CIS has entered the market
- Aegis Dagger Battery + Thor EM-i Super Hybrid, Geely New Energy has thrown out two "king bombs"
- A brief discussion on functional safety - fault, error, and failure
- In the smart car 2.0 cycle, these core industry chains are facing major opportunities!
- The United States and Japan are developing new batteries. CATL faces challenges? How should China's new energy battery industry respond?
- Murata launches high-precision 6-axis inertial sensor for automobiles
- Ford patents pre-charge alarm to help save costs and respond to emergencies
- New real-time microcontroller system from Texas Instruments enables smarter processing in automotive and industrial applications
- A brief discussion on LTE technology and practical application solutions
- What is the drilling process in the Siliton ceramic substrate PCB?
- SD/TF card usage issues
- Download address of Arteli technical resources
- MSP430F249 external interrupt P1.3 port
- It was despised the day before yesterday, it was debunked yesterday, and today... it was blocked.
- J-linK connection problem
- New uses for old phones (1) - Basic method
- How to make the Type-C mobile phone fast charge and listen to music at the same time? Try adding a Type-C PD chip
- GD32E231 DIY Competition - Indoor Environment Monitoring Terminal