2012 is the first year that LEDs have entered indoor and home lighting on a large scale, and it is also the first year that civilian LEDs have begun to be used. As civilian products, more stringent requirements are placed on product performance, price, and reliability. On the one hand, the luminous efficiency of LEDs is required to be continuously improved and the price is continuously reduced. On the other hand, many requirements are also placed on the constant current drive source of LEDs. In the minds of ordinary people, the life of LEDs themselves is already very high, but the actual life is very low, which is often caused by the low life of the power supply. The life of the power supply often depends on the life of the electrolytic capacitor. Because it is generally believed that the life of the electrolytic capacitor is very low. If the constant current source does not have an electrolytic capacitor at all, then its life must be very high. What's more, the power factor can be improved after removing the electrolytic capacitor. Therefore, various constant current sources without electrolytic capacitors have attracted the attention of many people.
1. Simple method without electrolytic capacitor
It's easy enough to remove the electrolytic capacitors and have it work.
However, the life of this circuit is shorter because it does not use constant current measures. Therefore, when the input voltage or temperature increases, the current will increase quickly, so that the LED will be burned out soon. Although adding resistors to limit the current can solve some problems, its efficiency is only 52%-73%. It is completely unacceptable.
Therefore, a constant current must be applied, even if it is the simplest constant current diode.
However, this circuit does not work either. Because the input is a half sine wave, the LED cannot be turned on at low voltage. Although it can maintain constant current when the voltage rises to a certain level, the current waveform is close to a rectangular wave, so its power factor is not satisfactory, because only when the current waveform is the same as the voltage waveform can the power factor be equal to 1. So can we develop a circuit that makes its current waveform as close to the voltage waveform as possible?
2. ExClara’s EXC100 solution
ExClara, a company in Silicon Valley, USA, has proposed a solution that can nearly solve this problem. Because the current can only be flat after using a constant current diode, the sine wave can only be approached by a step wave.
This may seem simple, but it is actually very complicated to achieve. In order to obtain such a current waveform, LED strings with different constant current values must be connected in sequence. The specific block diagram of the EXC100 chip is shown in Figure 4.
It first measures the input voltage, and when the input voltage reaches a certain value, it starts to connect the first string of LEDs with a relatively low constant current; when it reaches a higher voltage, it starts to connect the second string of LEDs behind the first string and keep the current at a higher value; finally, when the voltage is higher, it connects the third string of LEDs and keeps the current at a higher value. So its internal structure is very complicated.
Later, the American company Supertex also developed a CL8801 that can connect 4 strings of LEDs. After using 4 strings, the PF can reach 0.98 and the harmonic distortion can be less than 20%. Its block diagram is shown in Figure 5.
In fact, the circuit for measuring input voltage is not drawn here. This circuit measures the input voltage and compares it with four preset values one by one, and turns on switches 1, 2, 3, and 4 in sequence. These switches must be MOS tubes that can withstand high voltage. Therefore, the entire chip must be made using high-voltage technology. Its cost is very high. The price of EXC100 is about 10 yuan.
Taiwan's AIC company also makes similar products.
There are also many companies in South Korea, Japan and other countries that have similar products. It seems that this kind of product is very popular, but the cost is relatively high.
3. Jingfeng's BP5801
In order to reduce costs, the simplest way is to take the internal high-voltage MOS switch tube out and use discrete components. Jingfeng's BP5108 adopts this method (Figure 6).
At 220V, when the rectified voltage rises to 104.7V, the first string of 40 LEDs begins to conduct (its voltage is 134V); when the voltage increases to 34.89V, the second string of 23 LEDs begins to be connected in series with the first string and conduct (its voltage is 76V); when the voltage increases to 25.21V, the third string of 23 LEDs is connected in series and conducts (its voltage is 76V), and finally the three strings of LEDs are all conducted with a maximum current of 30.8mA (rated current is 20mA). Because the current waveform is closer to a sine wave at this time, and is in phase with the voltage waveform, the power factor can be as high as 0.968, and the efficiency can be 90.6%.
The detailed circuit diagram is shown in Figure 7. The first three components (two protections and one rectifier bridge) are public. An inductor and a capacitor are filters required to reduce electromagnetic interference EMI, because this is a linear constant current source that has become a switch type. Add the 11 resistors, three capacitors and three MOS tubes at the back, a total of 22 components, and the MOS tube needs to use 2N60, which is also a large and expensive device.
4. Advantages and disadvantages of linear constant current source without electrolytic capacitor
This kind of linear constant current source without electrolytic capacitors needs to remove the electrolytic capacitors for two reasons:
1. The life of electrolytic capacitors is short. This is a common misunderstanding. Of course, this misunderstanding is also derived from a large number of examples. The main reason is that the Chinese market is flooded with a large number of low-quality electrolytic capacitors, which do have a short life. But this does not mean that all electrolytic capacitors have a short life.
There are two types of electrolytic capacitors, one with liquid electrolyte and the other with solid electrolyte. Liquid electrolytic capacitors have a shorter lifespan because the liquid will dry up. So new long-life electrolytic capacitors use solid electrolytes. The lifespan of solid electrolytic capacitors is said to be up to 23 years, far exceeding the lifespan of LEDs. However, solid electrolytic capacitors are more expensive.
So does that mean liquid electrolytic capacitors can’t have a long lifespan? Not at all. The industry knows that the lifespan of Japan’s Ruby electrolytic capacitors can reach 10,000 hours at 105°C, and the lifespan doubles with every 10°C drop in temperature. At an ambient temperature of 85°C, the lifespan can reach 40,000 hours, and at 75°C, the lifespan can reach 80,000 hours, which can fully meet the needs of LEDs. And the price is not so expensive that it is unacceptable. Recently, Ruby has developed a small-volume LLE series of electrolytic capacitors with a lifespan that is twice as long. Its lifespan at 105°C is as high as 20,000 hours, which is specially used for small-volume bulbs. In addition, there are already manufacturers in China that can produce liquid electrolytic capacitors comparable to Ruby.
Therefore, the life of electrolytic capacitors is not a problem.
2. The power factor cannot be improved after adding electrolytic capacitors
First, let's look at the national regulations: According to the draft of the Chinese standard for indoor lighting LED bulbs, the power factor must not be less than 0.75, but in the general specification for lighting LED driver power supplies, it is stipulated that <5W is not required, 5W-25W, the first level is >0.85, and the second level is >0.7. The US Energy Star has no requirements for bulbs <5W, but requires PF>0.7 for LED lamps >5W (ANSIC82. 77-2002LM -79-08), 03/22/2010. Therefore, there is no requirement for power factor below 5W. I would also like to say a few fair words here. Our country has no requirements for the power factor of energy-saving lamps below 15W, but there are requirements for those above 15W.
In fact, the power factor should also be considered whether it is capacitive or inductive. Usually, homes and residential areas are dominated by inductive loads, because many white appliances such as refrigerators, washing machines, and air conditioners have motors, which are inductive loads; even black appliances such as televisions and stereos have transformers, which are also inductive loads. As for the inductive ballasts of fluorescent lamps and the electronic ballasts in energy-saving lamps, they are also inductive loads. Electrolytic capacitors are capacitive loads, and the two can be compensated. From this point of view, when formulating standards for LED lamps using electrolytic capacitors, the country should not only not restrict the power factor, but also encourage and reward it.
Anyway, because LED bulbs are mainly used to replace incandescent lamps. The most commonly used incandescent lamps are 40W and 60W. According to the current luminous efficiency of LEDs, a 5W LED bulb can replace a 40W incandescent lamp. In less than 1-2 years, a 5W bulb can also replace a 60W incandescent lamp, so for LED bulbs, the power factor is not a problem at all. Moreover, even if electrolytic capacitors are used, it is easy to increase the power factor to above 0.7 as long as the charging current is limited.
It can be seen that whether it is life span or power factor, the use of electrolytic capacitors is not a problem.
So what are the problems and disadvantages of removing electrolytic capacitors like the previous methods? Some are:
1. The solution without electrolytic capacitors will cause flickering of light. We know that LED will only emit light when current flows through it, and from the current waveform in Figure 3, we can see that its light emission is intermittent at one times the power supply frequency (bridge rectification). In China, it is 100Hz, and in the United States, it is 120Hz. The highest flicker frequency that humans can feel is 70Hz. Although this flicker is not felt by the human eye, it does not mean that it is harmless to humans.
The main disturbances reported are dizziness and eye strain, while migraines can also increase the risk of stroke.
In addition, this flickering will also bring about a flash effect, which will result in multiple images of moving objects when shooting, which may cause important images to be lost in security cameras. Domestic customers who use them have reported such problems.
2. Since the LED is not continuously turned on, especially the third string is only turned on for a very short time, and the current when it is turned on exceeds the rated value by more than 54%. This kind of operation will bring two problems. One is that the utilization rate of the LED is not high, which will reduce the luminous efficiency of the whole lamp. The author has personally tested LEDs with the same luminous efficiency and the same number. One uses the above-mentioned constant current source without electrolytic capacitors, and the other uses a linear constant current source with electrolytic capacitors. As a result, the luminous efficiency of the former is more than 15% lower than that of the latter (both were tested with an integrating sphere without a lampshade). Another problem is that its maximum current exceeds the rated current by 54%. Although it is a short time, it may reduce the life of the LED if it works like this for a long time. Because the maximum current specified by the LED can only be 16%-25% higher than the rated current.
3. Due to the use of switching operation, the characteristic of no electromagnetic interference of the linear constant current source is completely lost. Even an electromagnetic interference filter must be added. The actual electromagnetic interference test results of EXC100 are shown in Figure 8. The blue line in the figure is the standard of the US FCC Class B, although its test results can meet the standard. However, as a linear constant current source, there should be no interference at all, and there is no need to do any testing. Now we have to do testing to see if it can meet the standard. This cannot be regarded as an advantage in any way.
In addition, due to the serious waveform distortion, its harmonic distortion is also relatively serious. For example, the harmonic distortion of BP5108 is as high as 25.6%.
Finally, we have to mention the last "advantage" of this type of driver power supply. It can be connected to a thyristor dimmer. Because the thyristor dimmer requires a pure resistive load, and now this type of driver power supply has adopted so many measures that the power factor is close to 1, so of course it can be connected to a thyristor dimmer. So is this an "advantage"? You must know that after using a thyristor dimmer, the power factor and efficiency of the entire system will become very poor. Then, wouldn't it be a waste of effort to improve the power factor and efficiency of the driver power supply before? If dimming is really necessary, LEDs can be dimmed using DC or pulse width modulation (PWM), which can truly achieve efficient and energy-saving dimming. There is no need to use the thyristor technology of decades ago.
V. Conclusion
In fact, LED is a DC device, and it is best to use DC power supply. Electrolytic capacitors are the best means to use their energy storage effect to convert half a sine wave into a near DC. As long as electrolytic capacitors are used, the above problems will not exist. As for the power factor, it is not a problem at all. The fluorescent lamps that have been widely used in our country and the energy-saving lamps that have been vigorously promoted recently have never mentioned the power factor requirements. What's more, the capacitive power factor is the best compensation for a large number of inductive power factors. If the power factor is really required to meet a certain value, it can be achieved by adding a few more components when using electrolytic capacitors.
Previous article:Calculation method of transformer parameters for half-bridge switching power supply
Next article:Design of EMI filter for DC power supply
Recommended ReadingLatest update time:2024-11-16 16:31
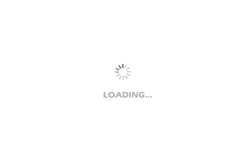
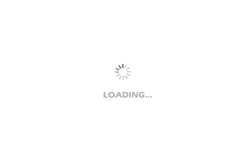
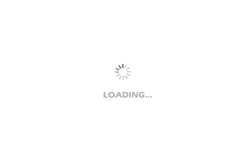
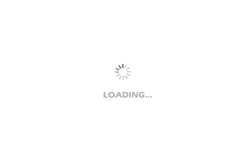
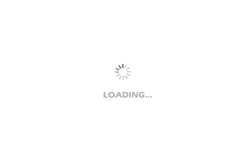
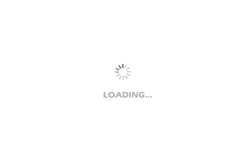
- MathWorks and NXP Collaborate to Launch Model-Based Design Toolbox for Battery Management Systems
- STMicroelectronics' advanced galvanically isolated gate driver STGAP3S provides flexible protection for IGBTs and SiC MOSFETs
- New diaphragm-free solid-state lithium battery technology is launched: the distance between the positive and negative electrodes is less than 0.000001 meters
- [“Source” Observe the Autumn Series] Application and testing of the next generation of semiconductor gallium oxide device photodetectors
- 采用自主设计封装,绝缘电阻显著提高!ROHM开发出更高电压xEV系统的SiC肖特基势垒二极管
- Will GaN replace SiC? PI's disruptive 1700V InnoMux2 is here to demonstrate
- From Isolation to the Third and a Half Generation: Understanding Naxinwei's Gate Driver IC in One Article
- The appeal of 48 V technology: importance, benefits and key factors in system-level applications
- Important breakthrough in recycling of used lithium-ion batteries
- Innolux's intelligent steer-by-wire solution makes cars smarter and safer
- 8051 MCU - Parity Check
- How to efficiently balance the sensitivity of tactile sensing interfaces
- What should I do if the servo motor shakes? What causes the servo motor to shake quickly?
- 【Brushless Motor】Analysis of three-phase BLDC motor and sharing of two popular development boards
- Midea Industrial Technology's subsidiaries Clou Electronics and Hekang New Energy jointly appeared at the Munich Battery Energy Storage Exhibition and Solar Energy Exhibition
- Guoxin Sichen | Application of ferroelectric memory PB85RS2MC in power battery management, with a capacity of 2M
- Analysis of common faults of frequency converter
- In a head-on competition with Qualcomm, what kind of cockpit products has Intel come up with?
- Dalian Rongke's all-vanadium liquid flow battery energy storage equipment industrialization project has entered the sprint stage before production
- Allegro MicroSystems Introduces Advanced Magnetic and Inductive Position Sensing Solutions at Electronica 2024
- Car key in the left hand, liveness detection radar in the right hand, UWB is imperative for cars!
- After a decade of rapid development, domestic CIS has entered the market
- Aegis Dagger Battery + Thor EM-i Super Hybrid, Geely New Energy has thrown out two "king bombs"
- A brief discussion on functional safety - fault, error, and failure
- In the smart car 2.0 cycle, these core industry chains are facing major opportunities!
- The United States and Japan are developing new batteries. CATL faces challenges? How should China's new energy battery industry respond?
- Murata launches high-precision 6-axis inertial sensor for automobiles
- Ford patents pre-charge alarm to help save costs and respond to emergencies
- New real-time microcontroller system from Texas Instruments enables smarter processing in automotive and industrial applications
- Characteristics, functions and precautions of chopper
- Copper plating under the DC conversion power inductor
- Regarding FPGA development, compared with several major companies' EDA design tools, Xilinx's Vivado is still the best
- How to simulate I2C communication using GPIO on C2000
- Evaluation board quick test - based on TI Sitara Cortex-A9
- Never forget the teacher's kindness, teachers, happy holidays~~
- PCB short circuit
- Design of full-speed USB interface for CC2531 chip
- 【Recruitment】Shenzhen-Two-hour work-Basic MSP430 knowledge
- EEWORLD University Hall ---- Principles of Automatic Control Xie Hongwei National University of Defense Technology