1 Introduction
With the widespread application of power electronic devices, a large number of low power factor diode uncontrolled rectifiers and thyristor phase-controlled rectifiers can only realize unidirectional energy transmission, which seriously pollutes the harmonics of the power grid. The reversible PWM rectifier not only has the characteristics of bidirectional energy transmission, sinusoidal grid-side current and unity power factor, but also solves many problems existing in traditional rectifier devices. In recent years, it has attracted more and more attention and has broad application prospects [1] . In medium-high voltage and high-power applications, three-level PWM rectifiers are widely used. Its power factor reaches 1. Compared with two-level PWM rectifiers, it has the following advantages: (1) The voltage peak value on each main power switch tube is only 1/2 of that of the two-level PWM rectifier; (2) The three-level PWM rectifier has 27 working states, so that the input side current waveform can maintain a certain sinusoidal degree even when the switching frequency is low; (3) Under the same switching frequency and control conditions, the harmonics of the input current of the three-level PWM rectifier are much smaller than those of the two-level rectifier, which is more suitable for high voltage and high power applications. At present, three-level PWM rectifiers usually adopt a dual closed-loop PI control algorithm in a synchronous rotating dq coordinate system. However, since the PWM rectifier is a nonlinear, time-varying and uncertain system [2] [3] , it is difficult to achieve the ideal control effect using conventional PI control, and the dynamic performance is poor.
Sliding mode variable structure control (SMC) is a type of discontinuous control whose control characteristics can force the system to make small, high-frequency up and down movements along a specified state trajectory under certain conditions, namely "sliding mode" motion. Due to its inherent advantages such as fast response, insensitivity to parameter changes, strong anti-interference ability, and simple implementation, SMC has been increasingly used in nonlinear systems [4] [5] .
In this paper, a dual closed-loop control system based on a three-level PWM rectifier is designed. In order to improve the system robustness and dynamic response of the output voltage, a voltage outer loop is designed using a sliding mode controller, which forms a dual closed-loop control system with the current inner loop of a conventional PI controller. The simulation results show that under high power and large load changes, the DC bus voltage fluctuation of the three-level PWM rectifier using a sliding mode controller is significantly reduced compared to the conventional PI controller, and the dynamic response of the DC link is effectively improved, which provides the possibility of further reducing the DC bus capacitance.
2 Mathematical model of rectifier
The topology of the diode clamped three-level PWM rectifier is shown in Figure 1. Ls and Rs are the equivalent inductance and equivalent internal resistance of the AC side reactor, respectively. Cd1 and Cd2 are the upper and lower bus capacitors on the DC side. R L is the load resistance on the DC side. e a , e b , e c are the grid phase voltages, i a , i b , i c are the grid phase currents, V dc1 , V dc2 are the voltages of the bus capacitors Cd1 and Cd2 , respectively , and I L is the load current. Assume that the grid voltage ( e a , e b , e c ) is a pure sinusoidal, symmetrical three-phase voltage. The switching functions S ip , S io , S in ( i = a, b, c ) of the three-phase bridge arms of the three-level rectifier bridge are introduced , and their meanings are:
(1) S 1i , S 2i are turned on, S 3i , S 4i are turned off, then S ip =1, S io =0, S in =0;
(2) S 2i , S 3i are turned on, S 1i , S 4i are turned off, then S ip = 0, S io = 1, S in = 0;
(3) S 3i , S 4i are turned on, S 1i , S 2i are turned off, then S ip =0, S io =0, S in =1.
Figure 1 Three-level PWM rectifier main circuit topology
Omitting the formula derivation, the mathematical model of the system in the abc coordinate system is:
Where:
in,
[page] The mathematical model based on the abc coordinate system has a clear physical meaning, but the variables on the AC side of the model are all time-varying AC quantities, which is not conducive to the design of the control system. In the synchronous rotating dq coordinate system, each AC quantity in the three-phase symmetrical system can be equivalent to a DC quantity. Therefore, the coordinate transformation is introduced to obtain the mathematical model in the dq coordinate system.
Where:
Assuming vd and vq are the d - axis and q-axis components of the grid-side voltage in the rotating dq coordinate system, we have :
Where is the differential operator.
Ignoring the error between the upper and lower capacitors of the busbar, assuming that C d1 = C d2 = C d , we have:
According to the above model, the equivalent circuit of the three-level PWM rectifier in the dq coordinate system is shown in Figure 2. For the DC side, the three-level rectifier bridge is equivalent to two current sources, and for the AC side, the three-level rectifier bridge is equivalent to two voltage sources.
Figure 2 Equivalent circuit of three-level rectifier in dq coordinate system
3 Design of voltage outer loop sliding mode controller
The three-level PWM rectifier has two external control variables: V dc and i q , where V dc is controlled by s d to maintain the stability of the DC bus voltage; i q is controlled by s q to control the system reactive current (unity power factor, leading, lagging). Taking V dc and i q as controllable outputs, the state space standard form is obtained as
Substituting the error between the reference value and the actual variable into equation (5) we get
In the formula, e ig = i qref –i q ; e Vdc = V dcref –V dc ; e Φ = Φ ref –Φ ; Φ is the disturbance;
According to equation (6) and the known two control degrees of freedom, the following sliding surface can be selected to ensure the robustness of the closed-loop system.
Where is a parameter related to the first-order response of DC voltage.
Formula (3) and (4) will become
In the dq rotating coordinate system, , e q = 0, under the ideal sliding mode state, s q is calculated by equation (5) , and the result is simplified to:
Similarly, on the ideal sliding surface, the output voltage accurately tracks the reference value, V dc = V dcref , and according to the power balance, we can get:
Substituting equation (10) and equation (11) into equation (9), we get:
Then sd and sq have little to do with the choice of sliding surface, which simplifies the design of sliding mode controller. The sliding surface is:
The voltage outer loop controller control equation is obtained from equations (12) and (14):
[page] Therefore, the following control strategy is adopted to realize the sliding mode variable structure control of the three-level PWM rectifier: set i qref and use PI controller to control the current loop; the voltage outer loop control adopts the sliding mode variable structure control algorithm, with the actual output voltage V dc and the given voltage V dcref as the controller input, and the controller output is used as the reference current i dref of the current loop PI regulator , realizing the effective combination of sliding mode variable structure control and voltage oriented vector control. Its control structure block diagram is shown in Figure 3.
Figure 3 Schematic diagram of sliding mode control of three-level rectifier
4 Simulation Results
According to the mathematical model and control strategy described above, the effectiveness of the control method proposed in this paper is simulated. The simulation parameters are as follows: input inductance 20mH, DC bus upper and lower capacitors 4000/2μF, input phase voltage 220V, DC bus voltage 600V, grid frequency 50Hz, switching frequency 2kHz, output power 5kW, sudden loading at 0.135s, and at 0.25s, the system starts to work in energy feedback grid mode. Figure 4 shows the bus voltage waveform of the three-level PWM rectifier. Among them, Figure 4 (a) shows the simulated waveforms of the phase voltage ( e a ) and current ( ia ) on the grid side of phase a . It can be seen that the voltage and current are in phase, and the power factor is above 0.99 after calculation; Figure 4 (b) shows the grid-side current waveform and its spectrum under full load, and the harmonic distortion rate is 2.00%; Figure 4 (c) shows the AC side line voltage waveform; Figures 4 (d) and (e) respectively show the DC bus voltage ( V dc ) waveforms using conventional PI control and sliding mode control. It can be seen that under sudden load conditions, the DC bus voltage drops under both control strategies, but the DC bus voltage changes less under sliding mode control and quickly reaches a steady state.
Figure 4. Simulation results of sliding mode control of three-level rectifier: (a) grid-side phase voltage and current; (b) grid-side current and its spectrum; (c) grid-side line voltage; (d) DC bus voltage waveform under conventional PI control conditions; (e) DC bus voltage waveform under sliding mode control conditions
The simulation results show that the sliding mode control strategy can achieve unity power factor control of the three-level PWM rectifier, and the system has good steady-state performance. From the DC bus voltage waveform, it can be seen that the dynamic response of the DC link is relatively fast, and the sudden change of load loading causes the bus voltage to drop by nearly 18V.
[page]5 Conclusion
This paper establishes a mathematical model of a three-level PWM rectifier and designs a circuit control strategy based on the sliding mode control principle. From the simulation results, it can be seen that the control strategy can achieve a stable output voltage, a sinusoidal input current, a unity power factor, and has good dynamic and steady-state response.
References
[1] Zhang Hao, Xie Yunxiang, et al. Three-phase high power factor rectifier based on sliding mode control. Electrical Applications, Vol. 27, No. 10, 2008.
[2] Zhang Yingchao. Research on control technology of neutral-point clamped three-level dual PWM inverter. Doctoral dissertation in engineering, Tsinghua University, 2008, 47-49.
[3] Zhang Haitao. Research on control system of three-level inverter based on IGCT. Doctoral dissertation in engineering, Tsinghua University, 2006, 47-49.
[4] Jin Hongyuan. Research on three-level PWM rectifier. PhD dissertation of Huazhong University of Science and Technology, 2006, 51.
[5] Hu Qing, Yu Haiyan, Xia Guiwen. Application of sliding mode variable structure control in three-phase rectifier. Journal of Shenyang University of Technology, 2002, 24(3): 139-142.
Previous article:Technical Analysis of Several Linear Regulators
Next article:Design of high-power LED constant current drive based on DC/DC regulator
Recommended ReadingLatest update time:2024-11-17 07:46
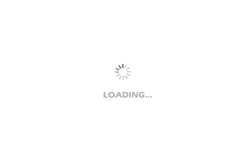
- Popular Resources
- Popular amplifiers
-
Power Electronics System Modeling and Control, edited by Xu Dehong, a teaching book for postgraduates published by the Machinery Industry Press
-
Design, production and debugging of flyback switching power supply (by Chen Yongzhen and Chen Zhibo)
-
开关电源设计与制作基础 (蔡宣三,倪本来编著)
-
Comparison of Control Output Characteristics of Current-Source Bidirectional PWM Rectifiers SPWM and SVPWM
- MathWorks and NXP Collaborate to Launch Model-Based Design Toolbox for Battery Management Systems
- STMicroelectronics' advanced galvanically isolated gate driver STGAP3S provides flexible protection for IGBTs and SiC MOSFETs
- New diaphragm-free solid-state lithium battery technology is launched: the distance between the positive and negative electrodes is less than 0.000001 meters
- [“Source” Observe the Autumn Series] Application and testing of the next generation of semiconductor gallium oxide device photodetectors
- 采用自主设计封装,绝缘电阻显著提高!ROHM开发出更高电压xEV系统的SiC肖特基势垒二极管
- Will GaN replace SiC? PI's disruptive 1700V InnoMux2 is here to demonstrate
- From Isolation to the Third and a Half Generation: Understanding Naxinwei's Gate Driver IC in One Article
- The appeal of 48 V technology: importance, benefits and key factors in system-level applications
- Important breakthrough in recycling of used lithium-ion batteries
- Innolux's intelligent steer-by-wire solution makes cars smarter and safer
- 8051 MCU - Parity Check
- How to efficiently balance the sensitivity of tactile sensing interfaces
- What should I do if the servo motor shakes? What causes the servo motor to shake quickly?
- 【Brushless Motor】Analysis of three-phase BLDC motor and sharing of two popular development boards
- Midea Industrial Technology's subsidiaries Clou Electronics and Hekang New Energy jointly appeared at the Munich Battery Energy Storage Exhibition and Solar Energy Exhibition
- Guoxin Sichen | Application of ferroelectric memory PB85RS2MC in power battery management, with a capacity of 2M
- Analysis of common faults of frequency converter
- In a head-on competition with Qualcomm, what kind of cockpit products has Intel come up with?
- Dalian Rongke's all-vanadium liquid flow battery energy storage equipment industrialization project has entered the sprint stage before production
- Allegro MicroSystems Introduces Advanced Magnetic and Inductive Position Sensing Solutions at Electronica 2024
- Car key in the left hand, liveness detection radar in the right hand, UWB is imperative for cars!
- After a decade of rapid development, domestic CIS has entered the market
- Aegis Dagger Battery + Thor EM-i Super Hybrid, Geely New Energy has thrown out two "king bombs"
- A brief discussion on functional safety - fault, error, and failure
- In the smart car 2.0 cycle, these core industry chains are facing major opportunities!
- Rambus Launches Industry's First HBM 4 Controller IP: What Are the Technical Details Behind It?
- The United States and Japan are developing new batteries. CATL faces challenges? How should China's new energy battery industry respond?
- Murata launches high-precision 6-axis inertial sensor for automobiles
- Ford patents pre-charge alarm to help save costs and respond to emergencies
- Playing with Zynq Serial 49——[ex68] Image FFT Filtering Processing of MT9V034 Camera
- Pingtouge RVB2601 Review: ADC Polling Single Channel and DMA Multi-Channel Acquisition
- Motor open loop response time
- TI C2000 applied to power system
- What is the principle of this circuit?
- Active filter
- BQ34Z100-G1 Topic Selected Questions and Answers
- [Raspberry Pi Pico Review] 3. Pico outputs PWM signals to control four-wire fans
- Please help me see how to clear the data of TS1102A
- I want to know if this method is correct to predict the change in capacitance of chip capacitors due to temperature drift?