LEDs have become the standard solution for movie lighting and camera flash in mobile phones. The demand for higher picture quality and higher resolution requires brighter flash LED solutions. The challenge is how to squeeze the best light flux from the battery by achieving the most efficient solution. As a result, operation that draws high current from the battery requires many power-saving operation features and a robust system design. This article will introduce a system-level flash LED driver design and some features that ensure safe system operation and integration.
Efficient Camera Flash LED Driver
High-resolution cameras require a high-brightness flash to take pictures in minimum light conditions. Customers are demanding a flash solution as a standard feature of mobile phones. Flash-equipped mobile phones have become an attractive selling point. This feature requires high luminous flux, which poses a challenge to the design of efficient LED driver systems.
System Design
The high forward voltage and current of the flash LED in a mobile phone and a given battery voltage make the boost converter the best solution. When driving large currents, the inductor-based boost converter shows satisfactory efficiency. The LED must be current driven because the forward voltage varies not only with temperature, but also has its own variations. This variation in forward voltage comes from its production process and has a range of ±20%, see Figure 1.
A simple approach is to connect the flash LED in series with a current sense resistor and then drive it through a boost converter. Figure 1 illustrates this approach.
Figure 2: Simple LED driving method using external current sensing resistor
The output voltage of the boost regulator is controlled to match the set LED current sensed by an external resistor. Unfortunately, this deviates from the designer's goal of squeezing the highest luminous flux from the limited power provided by the battery. The external current sense resistor has high power dissipation and is sized to provide available headroom voltage even at low currents to drive continuous movie lighting. On the other hand, if the current increases, the voltage drop across the current sense resistor increases, resulting in significant power dissipation. In addition, high-precision resistors with ideal power dissipation ratings are expensive and increase the size of the solution, requiring one resistor per LED channel.
Therefore, a better solution is an active current sink or source integrated into the LED driver, as shown in Figure 3. The internal current sense resistor can be adjusted in a way that the voltage drop and the resulting power dissipation are reduced, depending on the LED current. For low LED currents, the voltage drop can be maintained high enough to obtain an accurate sense signal.
Figure 3 Improved LED driving scheme using adaptive current sink and detection
The current sink not only senses the LED current, it can also regulate it by dynamically adjusting the resistor. The resulting current sink voltage drop serves as the information needed to dynamically adjust the boost converter output voltage, aiming to keep power dissipation to an acceptable minimum at any current level.
Figure 4 Comparison of active current sensing and resistive current sensing
Figure 4 shows a comparison between using a 1Ω resistor to sense current and using an active current sensing method regulated to a 400mV drop. The active current sensing method significantly contributes to higher system efficiency due to the lower power consumption.
Squeezing light flux from the battery
In the past, the RF PA drew the highest pulse current from the mobile phone battery. With the development of multi-functional mobile phones in the past 5 years, the processor power supply and the flash LED power supply, which is the focus of this article, have drawn the highest current. For example, if you want to drive an LED current of 1.5A, the current drawn from the battery can be as high as 3A due to the voltage ratio of the boost converter. Such high currents can cause the battery voltage to drop sharply. The undervoltage threshold detection mechanism prevents the system from failing in this situation. The phone will completely shut down due to low battery voltage when the flash is turned on, which is a very bad user experience. The common solution is to let the camera software turn off the flash in the low battery voltage state, which is not too bad compared to the user experience of not using the flash. The slow battery voltage information refresh rate provided by the PMIC, battery temperature and aging effects, and more serious inaccuracies relax the safety margin.
If the flash driver itself can prevent the battery voltage from dropping too much, then a smaller safety margin can be maintained. This can be achieved by using a controlled slew rate to ramp up the LED current and continuously monitoring the battery voltage during the ramp-up period.
TI has a flash driver technology that monitors the battery voltage. To obtain a stable LED current waveform and avoid excessive battery voltage drop, the flash driver actively controls the LED current rise/fall sequence. During the rising phase (rising slope of 25mA/12µs), the input voltage is monitored. If the input voltage drops below a set threshold, the device immediately stops the LED current from rising further to the set threshold and keeps the flash current at the actual level, see Figure 5.
Figure 5 Battery voltage drop monitoring
Therefore, it is guaranteed that the safety margin is very small and the phone does not shut down. Irreversible battery voltage drops during battery cycles are avoided and the overall battery operating time is increased.
Security system integration
The spotlight is designed for safe and trouble-free operation when driving high pulse currents. Mobile phone manufacturers are pressing for a seamless system integration solution. This requires a feature set that goes beyond the standard safety operation features such as inductor current limiting, undervoltage protection, etc. The TPS61310 flash LED driver has this feature set for this demanding operation.
LED Fault Detection
LED short circuits must be detected not only during production, but also during device operation to avoid dangerous conditions. One way to detect this condition is to force a current of a few mA to flow in the forward direction. This current can test the LED in the sub-illumination range, so the end user will not notice the brightness. However, this method has some disadvantages: LED manufacturers usually do not test the sub-illumination range. Due to process differences in production, there are huge inaccuracies not only between LED types but also within a single LED type. This may result in missed detection of a short-circuited LED or false false detection. The TPS61310 is different. If one or more LEDs are in a short-circuit condition during operation, the low-side current sinks LED1, LED2, LED3 limit the maximum output current and increase their input resistance to prevent excessive current absorption according to the settings of the video illumination mode or flash mode. In addition, this process is monitored and the short-circuit LED condition is reported to the test equipment during production or to the camera engine during operation through the I2C interface. Using a similar method, the open circuit condition can also be detected.
Over temperature detection
An attractive mobile phone product design may not meet the requirements of optimal thermal design in some cases. High-power flash LEDs have limited permissible pulse handling capabilities. If the phone is exposed to high temperatures, and/or the LED temperature rises due to the preceding flash operation, the capacitive thermistor may not be able to handle the LED power loss, resulting in an irreversible drop in luminous efficacy above 85°C, shortened lifetime, or even extinction. To bridge the gap between thermal design and functional/attractive design imperatives, the TPS61310 allows one or more LED temperatures to be measured using an NTC sense resistor. If the critical temperature is exceeded, the LED on/off time pulse ratio is reduced by software, allowing the LED to cool down between flash operations. This feature can also be used as a finger burn protection feature.
The TPS61310 chip temperature is also monitored. In addition to the standard thermal shutdown function, the TPS61310 can also provide an early warning function to the camera engine to avoid the thermal shutdown function being accidentally triggered, thus providing space for the device to cool down.
TPS61310 Movie Lighting/Flash Driver
The TPS61310 is capable of driving a 1.5A single, dual or triple flash LED application. Proprietary features such as battery voltage monitoring, power-saving operation, and reliable LED short-circuit detection make it a simple integrated solution for flash driving and movie lighting. After being programmable through a high-speed I2C I/F, the device has the highest cross-platform design flexibility. As an option, dedicated logic inputs can be used for zero-delay triggering. The 2x2mm2 chip-scale package and the lack of external components to program the current or flash on-time result in an extremely small solution size.
Previous article:Design of high-efficiency LED backlight driver power supply solution
Next article:Using DC/DC chip to make LED constant current drive circuit solution
Recommended ReadingLatest update time:2024-11-16 20:32
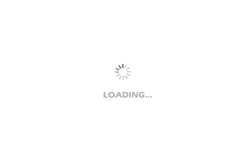
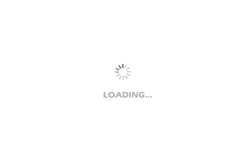
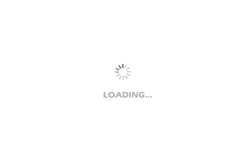
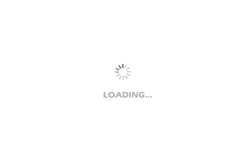
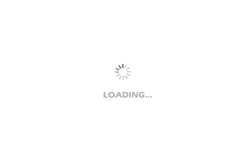
- Popular Resources
- Popular amplifiers
- MathWorks and NXP Collaborate to Launch Model-Based Design Toolbox for Battery Management Systems
- STMicroelectronics' advanced galvanically isolated gate driver STGAP3S provides flexible protection for IGBTs and SiC MOSFETs
- New diaphragm-free solid-state lithium battery technology is launched: the distance between the positive and negative electrodes is less than 0.000001 meters
- [“Source” Observe the Autumn Series] Application and testing of the next generation of semiconductor gallium oxide device photodetectors
- 采用自主设计封装,绝缘电阻显著提高!ROHM开发出更高电压xEV系统的SiC肖特基势垒二极管
- Will GaN replace SiC? PI's disruptive 1700V InnoMux2 is here to demonstrate
- From Isolation to the Third and a Half Generation: Understanding Naxinwei's Gate Driver IC in One Article
- The appeal of 48 V technology: importance, benefits and key factors in system-level applications
- Important breakthrough in recycling of used lithium-ion batteries
- Innolux's intelligent steer-by-wire solution makes cars smarter and safer
- 8051 MCU - Parity Check
- How to efficiently balance the sensitivity of tactile sensing interfaces
- What should I do if the servo motor shakes? What causes the servo motor to shake quickly?
- 【Brushless Motor】Analysis of three-phase BLDC motor and sharing of two popular development boards
- Midea Industrial Technology's subsidiaries Clou Electronics and Hekang New Energy jointly appeared at the Munich Battery Energy Storage Exhibition and Solar Energy Exhibition
- Guoxin Sichen | Application of ferroelectric memory PB85RS2MC in power battery management, with a capacity of 2M
- Analysis of common faults of frequency converter
- In a head-on competition with Qualcomm, what kind of cockpit products has Intel come up with?
- Dalian Rongke's all-vanadium liquid flow battery energy storage equipment industrialization project has entered the sprint stage before production
- Allegro MicroSystems Introduces Advanced Magnetic and Inductive Position Sensing Solutions at Electronica 2024
- Car key in the left hand, liveness detection radar in the right hand, UWB is imperative for cars!
- After a decade of rapid development, domestic CIS has entered the market
- Aegis Dagger Battery + Thor EM-i Super Hybrid, Geely New Energy has thrown out two "king bombs"
- A brief discussion on functional safety - fault, error, and failure
- In the smart car 2.0 cycle, these core industry chains are facing major opportunities!
- The United States and Japan are developing new batteries. CATL faces challenges? How should China's new energy battery industry respond?
- Murata launches high-precision 6-axis inertial sensor for automobiles
- Ford patents pre-charge alarm to help save costs and respond to emergencies
- New real-time microcontroller system from Texas Instruments enables smarter processing in automotive and industrial applications
- MSP430 clock frequency configuration process
- [Mill Edge AI Computing Box FZ5 Review] Pynq Framework - Helloworld!
- pybNano development board added to uf2-stm32f
- Compound tube and complementary push-pull circuit
- [RTT & Renesas high performance CPK-RA6M4 development board review] - Serial and USB communication
- During the epidemic, how to use UWB technology to ensure the prevention and control of enterprises?
- My childhood fantasy has finally come true! OLED pen!
- 555 classic circuit diagram: 555 test circuit
- Last day! TI live broadcast with prizes, ACI motor actual control evaluation example, in-depth understanding of TI C2000
- Here is a Tai Chi Bagua diagram of the radio frequency industry