Compared with ordinary signal lights, the flashing signal light has a more obvious warning effect because of its small size, strong light emission in a short time, and good signal transmission effect. It can be widely used in special vehicles (engineering vehicles, police cars, fire trucks, etc.), road traffic, aviation instructions and other occasions, and avoids various accidents to the greatest extent. The flashing interval of the flashing signal light is 0.5 to 1 s. Since the human eye is not very sensitive to the slight change of the flashing interval time, the manufacturer allows an error of 10% to 20%, but people are very sensitive to the change of the flashing number, so the flashing number must be consistent with the set number. This signal light requires the ability to control different flashing times and stop flashing times, so it has multiple working modes, and its control mode is realized by a pulse sequence generator. The circuit is required to be simple and reliable.
Existing products are composed of two timing capacitors and two oscillators. When working, the signals output by the two oscillators are processed by logic to obtain a variety of pulse sequences. Therefore, the two timing capacitors are required to have high accuracy and temperature characteristics.
Since the flashing interval of the flashing signal light is 0.5~1s when working, a larger capacity tantalum capacitor or electrolytic capacitor is used. Since the size of the capacitor capacity is sensitive to temperature, and the internal temperature variation range of the flashing signal light can reach -30~100℃ when working. In order to work stably, it is necessary to ensure that the two capacitors have high accuracy and consistent temperature characteristics, otherwise the number of pulse sequences generated will be different from the set value. In actual mass production, it is impossible to achieve complete consistency of the characteristics of the two capacitors, which brings many problems to mass production.
Using a single capacitor timing and a special voltage successive comparison method to generate a pulse sequence can overcome the above shortcomings.
Since the pulse sequence generator proposed in this article uses a bidirectional trigger diode, it has a simple circuit, does not require a low-voltage working power supply, has strong anti-interference ability, has multiple working modes, and has low power consumption, which is particularly suitable for flashing signal lights.
1 Working principle of pulse sequence generator of voltage successive comparison method
The working principle waveform of pulse sequence generator is shown in Figure 1. A sawtooth wave is generated by a single capacitor, and then a pulse is generated by comparison method at different voltages of the sawtooth wave. Therefore, as long as the comparison voltage is stable, the number of output pulses remains unchanged. It can be seen from Figure 1 that when the capacitance becomes larger or smaller, only the pulse interval changes, while the number of pulses remains unchanged.
2 Pulse sequence generator with single capacitor timing The
pulse sequence generator block diagram is shown in Figure 2, which is mainly composed of a timing capacitor, a holding capacitor, two bidirectional trigger diodes, a constant current source, etc. The specific circuit is shown in Figure 4.
2.1 Bidirectional trigger diode working characteristics
The working characteristic curve of the bidirectional trigger diode is shown in Figure 3. After being triggered at VB0, the internal resistance decreases rapidly, and it automatically disconnects if the current is maintained <10 mA. The VB0 of the bidirectional trigger diode DB3 is 33 V, and the hysteresis voltage △V is 7 V. This characteristic can be used to form a pulse generator with automatic comparison point change.
2.2 Working principle of sawtooth wave generator
Figure 4 is the overall circuit diagram. Q2, R5, and C3 form a constant current charging type sawtooth wave generator. Therefore, C3 is a timing capacitor and requires high precision. C2, C4, and C5 are auxiliary capacitors without high precision requirements. C2 only requires low leakage and can use a small-capacity monolithic capacitor. The current of the constant current source charging C4 depends on formula (1)
R2, R3, R4 and R8 form a voltage divider network. The voltage divider ratio is changed by S1 and S2 to set different maximum values of the sawtooth voltage, thereby changing the number of pulses within the range of 2 to 4. C4, Q4, R10 and Q5 form a maximum value controller of the sawtooth voltage. If the voltage at point D reaches 33 V, Q5 is triggered to turn on, the thyristor Q4 is turned on, and the voltages of C3 and C5 are quickly discharged to re-form the sawtooth wave.
[page]2.3 Working principle of the pulse generator with automatic comparison point change
C2, D1, Q3, R7 form a pulse generator with automatic comparison point change. At the beginning, the voltage of C2 is 0 V. Therefore, when the sawtooth voltage at point A reaches 33 V (comparison point 1), Q3 is triggered to turn on, and the thyristor Q1 that controls the strobe tube is turned on to realize a strobe. At this time, since C3 and C5 are much larger than C2 (experiments show that more than 10 times is sufficient), C2 is quickly charged with the hysteresis voltage of Q3, 7 V, and then Q3 is cut off. The sawtooth voltage at point A continues to rise. When the voltage reaches 33+7=40 V (comparison point 2), Q3 triggers C2 to quickly charge 7 V. At this time, the voltage of C2 is 7+7=14 V, and so on. Therefore, the voltages of comparison points 1, 2, 3, and 4 are 33 V, 40 V, 47 V, and 54 V, respectively. When the sawtooth voltage at point A reaches the set number of control voltages, Q4 turns on C3 through D2, and C2 quickly discharges through D1, restarting the next cycle.
Changing the voltage value of the voltage regulator D2 can change the starting point of the sawtooth wave, thereby changing the time T1 when the first pulse arrives.
2.3 Experimental results
Since the timing time is in the order of seconds and the trigger pulse time is in the order of microseconds, it is difficult to observe the trigger pulse, so the waveform at both ends of the strobe tube after being triggered is used to replace the waveform of the trigger pulse.
In Figure 5, the pulse number is set twice, the timing capacitor C3 in the upper figure is 4.7μF, and C3 in the lower figure is 4.7+2.2=6.9μF. The actual measured working waveform is when the change is about 50%.
In Figure 6, the pulse number is set to 4 times, and the actual measured operating waveform is when C3 in the upper figure is 4.7μF and C3 in the lower figure is 6.9μF.
It can be seen that when the capacity of capacitor C3 changes within the range of 50%, only the trigger pulse interval changes, while the set number of times remains unchanged. Moreover, due to the constant current charging method, the pulse interval time is almost the same when the trigger number is from 2 to 4. If the voltage divider ratio is changed, the number of pulses can be controlled within 1 to 8.
3 Conclusion
A pulse sequence is formed by using a capacitor and a bidirectional trigger diode and adopting the successive voltage comparison method. Since only one capacitor is used, various problems caused by the traditional pulse sequence generator using two capacitors for timing are overcome.
Experiments have proved that the single capacitor pulse sequence generator composed of a bidirectional trigger diode DB3 does not need to provide a low-voltage working power supply, and directly uses the 300 V high voltage for strobe, and the entire circuit works in a micro-power state.
Since the hysteresis voltage of DB3 is 7 V, the voltage difference of each comparison point is large, which is conducive to anti-interference.
When this circuit is used, even if the capacity of the timing capacitor C3 changes by 50%, the generator can accurately output the set pulse, but the time interval becomes larger, and C2, as a holding capacitor, has almost no effect on the timing time when its capacity changes by 100%. The general error of the capacitors used in production is ±lO%, so it is easy to meet the requirements of this circuit.
Previous article:Current limiter using current differential transconductance amplifier and its application
Next article:Improving Reliability and Performance of Medical Designs with Smart MOSFETs
Recommended ReadingLatest update time:2024-11-16 21:42
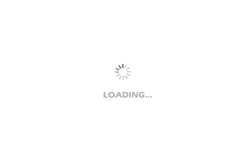
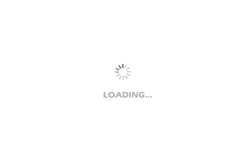
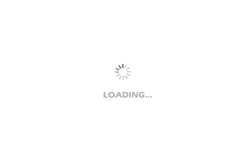
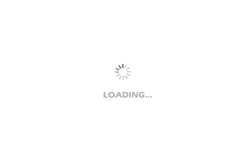
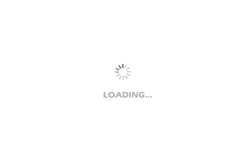
- Popular Resources
- Popular amplifiers
-
Modern Electronic Technology Training Course (Edited by Yao Youfeng)
-
Sensor Principle and Application Circuit Design (Edited by Chen Shuwang, Song Lijun, Xu Yunfeng)
-
Single-chip microcomputer C language programming and simulation
-
100 Examples of Microcontroller C Language Applications (with CD-ROM, 3rd Edition) (Wang Huiliang, Wang Dongfeng, Dong Guanqiang)
- MathWorks and NXP Collaborate to Launch Model-Based Design Toolbox for Battery Management Systems
- STMicroelectronics' advanced galvanically isolated gate driver STGAP3S provides flexible protection for IGBTs and SiC MOSFETs
- New diaphragm-free solid-state lithium battery technology is launched: the distance between the positive and negative electrodes is less than 0.000001 meters
- [“Source” Observe the Autumn Series] Application and testing of the next generation of semiconductor gallium oxide device photodetectors
- 采用自主设计封装,绝缘电阻显著提高!ROHM开发出更高电压xEV系统的SiC肖特基势垒二极管
- Will GaN replace SiC? PI's disruptive 1700V InnoMux2 is here to demonstrate
- From Isolation to the Third and a Half Generation: Understanding Naxinwei's Gate Driver IC in One Article
- The appeal of 48 V technology: importance, benefits and key factors in system-level applications
- Important breakthrough in recycling of used lithium-ion batteries
- Innolux's intelligent steer-by-wire solution makes cars smarter and safer
- 8051 MCU - Parity Check
- How to efficiently balance the sensitivity of tactile sensing interfaces
- What should I do if the servo motor shakes? What causes the servo motor to shake quickly?
- 【Brushless Motor】Analysis of three-phase BLDC motor and sharing of two popular development boards
- Midea Industrial Technology's subsidiaries Clou Electronics and Hekang New Energy jointly appeared at the Munich Battery Energy Storage Exhibition and Solar Energy Exhibition
- Guoxin Sichen | Application of ferroelectric memory PB85RS2MC in power battery management, with a capacity of 2M
- Analysis of common faults of frequency converter
- In a head-on competition with Qualcomm, what kind of cockpit products has Intel come up with?
- Dalian Rongke's all-vanadium liquid flow battery energy storage equipment industrialization project has entered the sprint stage before production
- Allegro MicroSystems Introduces Advanced Magnetic and Inductive Position Sensing Solutions at Electronica 2024
- Car key in the left hand, liveness detection radar in the right hand, UWB is imperative for cars!
- After a decade of rapid development, domestic CIS has entered the market
- Aegis Dagger Battery + Thor EM-i Super Hybrid, Geely New Energy has thrown out two "king bombs"
- A brief discussion on functional safety - fault, error, and failure
- In the smart car 2.0 cycle, these core industry chains are facing major opportunities!
- The United States and Japan are developing new batteries. CATL faces challenges? How should China's new energy battery industry respond?
- Murata launches high-precision 6-axis inertial sensor for automobiles
- Ford patents pre-charge alarm to help save costs and respond to emergencies
- New real-time microcontroller system from Texas Instruments enables smarter processing in automotive and industrial applications
- Battery Pack BMS Coulomb Counter Chip Solution
- How to distinguish between pads and vias_Differences between vias and pads
- Could you please tell me what circuit is generally used to implement the 0/4-20mA drive circuit?
- Principle and application of diaphragm pressure gauge
- [AT-START-F425 Review] No.1 Unboxing AT32F425
- Showing off your products (6) - silicon lab
- EEWORLD University - How to draw a high-end PCB ruler with Altium20
- Looking for a high-speed linear array image sensor model
- DC-DC converters are used to improve the safety and reliability of power supply.
- A very good article, those who learn Verilog can take a good look at it