Today's portable product designs have conflicting requirements for the batteries they use. For example, more features increase power consumption, and users want longer battery life. However, shrinking product size and cost constraints prevent battery capacity from increasing, so saving power becomes the most important consideration. Traditional designs usually try to minimize current consumption in order to minimize power consumption; however, the battery's storage capacity is the product of voltage, current and time. To effectively improve the power efficiency of the entire system, all three variables must be considered simultaneously. Microcontroller systems that use batteries as power sources and these batteries can be replaced by users can use microcontrollers designed to cope with these variables because these microcontrollers can solve the above problems through functions such as on-chip voltage conversion and traditional low-power operation modes.
Battery Characteristics
Most low-end and mid-range portable products use replaceable or rechargeable batteries that can also be replaced by users. As shown in Figure 1, the voltage of a single battery cell is usually between 1.2-1.6V when it is fully charged, and drops to 0.9-1.0V when the battery is exhausted. Connecting two single-cell batteries in series can provide a voltage between 1.8-3.2V.
Microcontroller power supply characteristics during normal operation
Common low-power microcontrollers are able to operate within the supply range of two batteries. For example, most 8- and 16-bit microcontrollers use 0.35-micron CMOS technology, which can operate up to 3.6V, but will not function well at 1.8V. At lower voltages, digital logic will operate more slowly, and analog switch components will have higher on-resistance. Component performance also varies with battery voltage, although battery voltage is usually irrelevant to application requirements. In addition, if the digital logic is designed to operate at the minimum battery voltage, it will consume more current at higher voltages. The dynamic power
consumption of a CMOS logic gate can be written as: P = C × V2 × f, where C is the load capacitance, which is a function of the design and process technology; V is the supply voltage; and f is the switching frequency, which is a function of the application processing requirements. Supply voltage is the primary means of controlling power consumption, so if voltage conversion can be added directly to the chip, as the C8051F9xx contains a low dropout (LDO) regulator, a stable 1.8V voltage can be provided to the digital core of the microcontroller (see Figure 2), significantly reducing dynamic power consumption.
Benefits of Voltage Conversion
The advantages of using an LDO regulator can be seen by looking at the dynamic power consumption relationship of CMOS technology:
P = C × V2 × f
= V × (C × V × f)
= V × I
where dynamic current I = C × V × fWhen
analyzing dynamic current, we often normalize the dynamic current to a frequency of 1MHz or a specific supply voltage; for example, at 1.8V, a common low-power microcontroller will have a dynamic current consumption of 220μA per MHz. Without power regulation, this increases to 220 × (3.2/1.8) = 391μA per MHz at 3.2V. But with an LDO regulator, the battery current is fixed at 220μA per MHz over the entire voltage range. Designers can also upgrade to more advanced 0.18-micron process technology, which makes digital logic faster and reduces current consumption by 20% to 30%. It is not difficult to reduce the operating voltage below 1.8V, but current flash memory technology requires at least 1.8V, and many analog peripherals also require voltages above 1.8V to meet performance and application requirements.
Figure 1 shows that no single-cell or dual-cell architecture can provide a voltage between 1.6-1.8V. If the microcontroller core voltage is in this range, then an LDO can provide the required voltage when using two batteries, and an inductor-based DC/DC boost converter can be used if one battery is used. During the entire battery life, the battery-powered circuit only needs to perform step-up or step-down conversion, without dynamically switching between the two modes. Although an integrated DC/DC boost converter (such as the converter included in the C8051F9xx) will slightly increase the circuit complexity, it allows the system to operate on a single battery, greatly reducing the cost and size of the product.
Although LDOs can significantly reduce the power consumption of dual-battery systems, DC/DC boost converters can provide higher overall power efficiency than LDOs. All else being equal, a single-cell design using an 80% efficient DC/DC boost converter will consume half the power of a conventional 0.35 micron dual-cell design without an LDO.
Sleep Mode Requirements
To provide maximum power efficiency and battery life, the microcontroller must optimize its operation during wake-up and normal mode, ensuring that components spend the majority of their time in ultra-low power sleep mode. In some applications, sleep mode current is the largest contributor to overall power consumption. To minimize sleep
mode current, the LDO and DC/DC converter must be turned off, while the power supply to the digital core must be removed. They must be able to start up quickly so that the microcontroller can quickly return to normal operating mode. Many blocks, such as power management and the real-time clock circuit (RTC), operate even in sleep mode and must be able to operate from an unregulated supply of 0.9-3.2V. Removing power to the digital core logic also prevents off-state leakage current from causing sleep mode current to increase, but even when the microcontroller enters sleep mode, the contents of RAM memory and all registers must be saved so that program execution can resume from the correct location. It also requires some form of continuous supply voltage monitoring or brownout detection to ensure that the state data is not corrupted even if the voltage drops below the minimum voltage required to retain the data.
Finally, the microcontroller should be able to leave sleep mode when triggered by an external event or when an internal timer expires, and it is best to support a quartz crystal or RC oscillator. To ensure the longest battery life, the sleep mode current of the entire chip, including the brownout detection circuit and the 32.768KHz quartz oscillator, should be less than 1μA. For example, the C8051F9xx has a typical sleep mode current of only 50nA including the brownout detection circuit, and can quickly return to normal operation mode from sleep mode (typically 2μs with 2 batteries and less than 10μs with 1 battery).
Minimize the time spent in normal operation mode
When the microcontroller switches between sleep mode and normal mode, it actually does no useful work, even though it consumes more current. Fast wake-up times save power and allow quick response to time-sensitive triggers, such as returning to normal mode due to serial port activity. Avoid using slow-starting quartz oscillators in high-speed system clock circuits. Instead, choose an accurate and fast-starting on-chip oscillator. The way the analog blocks are started up can also have a significant impact on how long the microcontroller stays in normal mode. For example, a voltage regulator or voltage reference circuit using an external decoupling capacitor may take several milliseconds to stabilize. Once in normal operation mode, the digital core should operate at maximum clock frequency so that the quiescent current is spread over more clock cycles, resulting in lower current consumption per MHz. When analyzing this performance metric, it is best to include all quiescent current sources, such as supply voltage and frequency monitoring circuits, reference voltage circuits, LDO regulators, and system clock oscillators.
Advantages of an integrated solution
Whether a traditional microcontroller is paired with an external LDO regulator or a DC/DC boost converter, its performance will not be as good as a fully integrated solution. Integrated components not only significantly reduce size and cost, but integrated voltage converters are also generally more efficient because they are designed specifically to power the microcontroller core. Finally, the external converter cannot be shut down into sleep mode, otherwise it will not be able to provide power to the microcontroller. Some external DC/DC boost converters can provide power to a dormant microcontroller in standby mode, but standby mode typically draws tens of microamperes from the battery.
Previous article:Methods of Setting Up an Electromagnetic Compatibility Laboratory
Next article:Design of portable device battery monitoring system based on BQ27210
Recommended ReadingLatest update time:2024-11-16 22:30
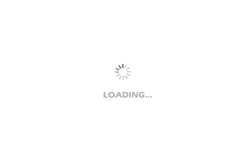
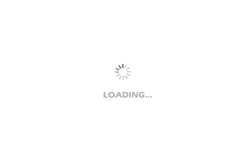
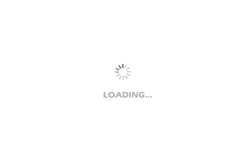
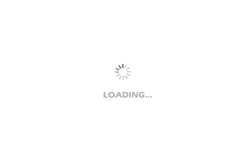
- Popular Resources
- Popular amplifiers
-
西门子S7-12001500 PLC SCL语言编程从入门到精通 (北岛李工)
-
New Energy Vehicle Detection and Diagnosis Experiment (Edited by Mao Caiyun, Zhou Xien, and Long Jiwen)
-
Virtualization Technology Practice Guide - High-efficiency and low-cost solutions for small and medium-sized enterprises (Wang Chunhai)
-
ESP32-S3 source code
- MathWorks and NXP Collaborate to Launch Model-Based Design Toolbox for Battery Management Systems
- STMicroelectronics' advanced galvanically isolated gate driver STGAP3S provides flexible protection for IGBTs and SiC MOSFETs
- New diaphragm-free solid-state lithium battery technology is launched: the distance between the positive and negative electrodes is less than 0.000001 meters
- [“Source” Observe the Autumn Series] Application and testing of the next generation of semiconductor gallium oxide device photodetectors
- 采用自主设计封装,绝缘电阻显著提高!ROHM开发出更高电压xEV系统的SiC肖特基势垒二极管
- Will GaN replace SiC? PI's disruptive 1700V InnoMux2 is here to demonstrate
- From Isolation to the Third and a Half Generation: Understanding Naxinwei's Gate Driver IC in One Article
- The appeal of 48 V technology: importance, benefits and key factors in system-level applications
- Important breakthrough in recycling of used lithium-ion batteries
- Innolux's intelligent steer-by-wire solution makes cars smarter and safer
- 8051 MCU - Parity Check
- How to efficiently balance the sensitivity of tactile sensing interfaces
- What should I do if the servo motor shakes? What causes the servo motor to shake quickly?
- 【Brushless Motor】Analysis of three-phase BLDC motor and sharing of two popular development boards
- Midea Industrial Technology's subsidiaries Clou Electronics and Hekang New Energy jointly appeared at the Munich Battery Energy Storage Exhibition and Solar Energy Exhibition
- Guoxin Sichen | Application of ferroelectric memory PB85RS2MC in power battery management, with a capacity of 2M
- Analysis of common faults of frequency converter
- In a head-on competition with Qualcomm, what kind of cockpit products has Intel come up with?
- Dalian Rongke's all-vanadium liquid flow battery energy storage equipment industrialization project has entered the sprint stage before production
- Allegro MicroSystems Introduces Advanced Magnetic and Inductive Position Sensing Solutions at Electronica 2024
- Car key in the left hand, liveness detection radar in the right hand, UWB is imperative for cars!
- After a decade of rapid development, domestic CIS has entered the market
- Aegis Dagger Battery + Thor EM-i Super Hybrid, Geely New Energy has thrown out two "king bombs"
- A brief discussion on functional safety - fault, error, and failure
- In the smart car 2.0 cycle, these core industry chains are facing major opportunities!
- The United States and Japan are developing new batteries. CATL faces challenges? How should China's new energy battery industry respond?
- Murata launches high-precision 6-axis inertial sensor for automobiles
- Ford patents pre-charge alarm to help save costs and respond to emergencies
- New real-time microcontroller system from Texas Instruments enables smarter processing in automotive and industrial applications
- The US-China patent dispute - MPEG-2 - is over, but what about MPEG-4?
- I want to ask why this motor cannot start? The voltage from B+ to B- is normal, but after starting, the voltage from B+ to M- jumps and the motor vibrates.
- Summary of equivalent circuits of common electronic components
- Comparison of several MicroPython IDEs
- Analysis of the working principles of seven triode collector DC circuits 4
- Pingtouge Xuantie VirtualZone: Security extension based on RISC-V architecture
- DSP Implementation of Square Root Operation
- Selling new LPCXpresso54608 (om13092)
- EMF detector using ATtiny24A-PU
- Introduction to the transmission distance and wall penetration capability of Zigbee communication technology