In the pursuit of higher system efficiency and performance, the input voltages of digital and mixed-signal components in data storage and communication systems are moving lower and lower. In many cases, the maximum input voltage required by most components within such systems is now only 3.3V. In this case, the traditional 5V or 12V intermediate voltage rail can be bypassed and the 24VDC or 48VDC backplane distribution voltage can be directly converted to a 3.3V dual-purpose bus and power rail. Many high-power DC/DC brick module suppliers (such as Emerson and TDK-Lambda) have recognized this trend and have easily achieved 92% efficiency indicators by significantly improving their performance in high step-down ratio operation. Using this 3.3V intermediate bus, subsequent point-of-load regulators can generate lower voltages (i.e., 2.5V, 1.2V, 1.0V, etc.) to power memory, ASIC/FPGA cores, high-speed I/O, etc.
Direct conversion from an intermediate bus provides another advantage by reducing the number of copper layers required in the printed circuit board (PCB) to route the power rails to the load. Take, for example, a PCB with a 5V rail used only as an intermediate bus, which contains two DC/DC converters to support 3.3V and 1.8V rails. The same board redesigned with a 3.3V intermediate bus and a single 3.3V to 1.2V converter will most likely have fewer copper layers (three rails now two). The resulting total solution size on the board is very attractive while eliminating the need to route the 5V potential to an integral section of the PCB. The option of minimizing the number of copper layers in the manufacturing process of the PCB has the potential to reduce cost and material, and is expected to improve yield and reliability.
In addition, the lower voltage intermediate bus rail is also suitable for system operation from a backup power source such as a supercapacitor. Compared with batteries, supercapacitors can support higher peak current, power density, wider operating temperature range and lower ESR, so they are increasingly used as short-term power supply to supplement battery backup systems. Since the maximum charging voltage of supercapacitors is only 2.3V to 2.7V, the use of high-efficiency low-input voltage buck converters can maximize system preparation time to achieve fast system recovery after the main power is reconnected.
Limitations of Traditional Solutions
With traditional DC/DC step-down solutions, the switching regulator or switching controller requires a minimum input voltage or bias voltage of approximately 5V to drive the N-channel power MOSFET. This minimum voltage is required to drive the power MOSFET into a low on-resistance region during current conduction. Any increase in on-resistance is detrimental to efforts to improve operating efficiency, especially at high currents often encountered in networking and storage systems. For systems that seek to improve operating efficiency and reduce production costs by minimizing component input supply voltages (such as 3.3V) with intermediate rail voltages, the challenge is how to best support bias supplies that typically consume only 50mA to 100mA of current - add a 5V output high voltage step-down regulator; add a step-up converter (from 3.3V); or continue to use the existing 5V intermediate bus. Each of these options requires some unpleasant trade-offs in terms of component count, design effort, PCB complexity, reliability, cost, and operating efficiency.
A Better Alternative Solution
Another alternative solution that aims to solve the low operating input voltage challenge mentioned earlier in this article is the LTM4611 step-down µModule® regulator. This device belongs to a new family of DC/DC converters that have evolved from traditional switching power management solutions and integrates nearly all components of the switching converter (including the inductor) into a compact surface mount package. The LTM4611 power module takes a single operating input voltage rail of 1.5V to 5.5V and steps it down to an output voltage as low as 0.8V and can provide up to 15A of output current. Self-generated bias supply built entirely into an LGA package allows operation from a single low voltage supply. Figure 1 shows the LTM4611 circuit schematic for a fully operational 15A step-down solution. It is obvious from the figure that the circuit requires very few external components, allowing for a compact solution and simple PCB layout.
Figure 1: Schematic of a complete voltage converter (designed to operate from a single 2.1V to 5.5V input to provide a 1.8V/15A output)
Operating Efficiency Comparison
Justifying the traditional three-stage buck architecture from an efficiency standpoint is very tricky, as each step-down stage between the distribution rail and the load must be much more efficient than a two-stage solution. Figure 2 shows the previously proposed 5V intermediate bus option and a 3.3V intermediate bus implemented using the LTM4611 µModule regulator. In both cases, the 48V step-down is simulated as a 75W Emerson (formerly Artesyn) 1/8 brick single output converter with 10A loads on its 1.8V and 3.3V rails. In the traditional three-stage buck architecture, the 5V to 3.3V and 5V to 1.8V step-down converters are simulated as another device in the µModule regulator family.
Figure 2: Schematic diagram of three-stage and two-stage buck architectures (shown are the total power losses when converting
from 48VDC to 3.3VDC and 1.8VDC at 10A output current
)
Figure 3 compares the efficiency and total power loss of a three-stage solution to a two-stage solution using the LTM4611 over a wide range of output currents (assuming the same output current on each rail). Since the brick is rated for 75W maximum, the maximum output current that the three-stage solution can provide is limited to 13A for the 3.3V and 1.8V rails, while the two-stage solution can support up to 14A each. As the curves show, the difference in total power loss between the two solutions during the step-up to the 48V distribution voltage can be quite large, and this can further drive up costs due to increased copper area in the PCB, increased actual system size, use of heat sinks, and even forced cooling airflow required to maintain reliable system operation.
Figure 3: Efficiency and power loss comparison of three-stage and two-stage conversion (from 48VDC to 3.3VDC and 1.8VDC)
For an increasing number of products, reducing power loss at light loads is just as important, if not more important, than reducing power loss at heavy loads. Subsystems are designed to operate in lower power standby or sleep states as long as possible (to save energy) and draw peak power (full load) only when needed. The LTM4611 supports pulse skipping and Burst Mode® operation, which significantly improves efficiency levels at load currents below 3A compared to continuous conduction mode.
Current Sharing of Multiple Power Supplies to Deliver 60A or More Output Current
For power rails that need to deliver up to 60A output, current sharing of up to four LTM4611 µModule regulators is supported. Current mode control makes current sharing of modules particularly reliable and easy to implement, while even ensuring current sharing between modules during startup, transient and steady-state operation.
In contrast, many voltage mode modules achieve current sharing by using a master-slave configuration or "droop-sharing" (also known as "load line sharing"). Master-slave mode is susceptible to overcurrent trips during startup and transient load conditions, while droop-sharing results in degraded load regulation and makes it almost impossible to ensure good module-to-module current matching during transient load steps. The LTM4611 typically provides better than 0.2% load regulation from no load to full load - and 0.5% (maximum) over the entire internal module temperature range of -40ºC to 125ºC.
Accurate Voltage Regulation at the Load
High current, low voltage FPGAs, ASICs, microprocessors (μPs), etc. often require
extremely accurate, tightly regulated voltages at the package terminals (e.g., VDD and DGND pins) – ±3% (or better) of nominal VOUT
.
At
such high current levels and low voltage levels, resistive distribution losses in the PCB traces can affect the voltage at the load. To meet this stringent regulation requirement for low output voltages, the LTM4611 provides a unity-gain differential amplifier for remote sensing at the load terminals when the voltage is less than or equal to 3.7V. As can be seen in Figure 1, the differential feedback signal (VOSNS
+
–
VOSNS−
) across the POL is reconstructed at DIFF_VOUT
(
with respect to the module’s local ground SGND), allowing the control loop to compensate for any voltage drops in the power delivery path between the module’s output pins and the POL device.
When the output voltage of the LTM4611 is within ±5% of the nominal VOUT
,
an internal output voltage power good (PGOOD) indicator pin provides a logic high open-drain signal; otherwise, the PGOOD pin is pulled to a logic low. When the output voltage exceeds 107.5% of the nominal value, the output overvoltage protection function circuit is triggered and turns on the internal low-side MOSFET until the output voltage overvoltage condition is cleared. Foldback current limiting protects the upstream power supply and the device itself in the event of an output short circuit.
Thermally Enhanced Package
The device’s LGA package allows heat to be dissipated from both the top and bottom, facilitating the use of a metal chassis or BGA heat sink. The package’s shape facilitates excellent heat dissipation with or without cooling airflow. Figure 4 shows an IR thermal image of the top surface of the LTM4611, showing that the power loss measured on the bench was only 3.2W when performing a 1.8V input to 1.5V/15A output conversion without cooling airflow.
As mentioned earlier, at the low 1.8V input voltage condition, a traditional power IC solution without a bias supply will struggle to drive the gate with enough amplitude to fully saturate the power MOSFET. Therefore, its thermal performance will be lower than what the LTM4611 can provide (as shown in Figure 4), which has an internal micropower bias generator.
Figure 4: Top thermal image of the LTM4611 regulator producing 1.5V/15A output from a 1.8V input.
Power loss is 3.2W. Bench testing without cooling airflow produced a 65ºC surface temperature hotspot.
Housed in a thermally enhanced LGA (land grid array) package, the LTM4611 offers impressive efficiency with a small land pattern (just 15mm x 15mm) and footprint (only 4.32mm high – occupying just 1cm3 of space
)
. In addition to
high efficiency
, the LTM4611 has a relatively flat power dissipation curve for a given input voltage, making thermal design of the LTM4611 and reuse in subsequent products simple – even as intermediate bus voltages decrease due to shrinking IC die.
A Reliable Solution
Linear Technology's µModule regulators, such as the LTM4611, are tested to the same rigorous standards as other packaged integrated circuits in the product line. Before being released to the public, products must successfully pass a series of tests such as operating life testing per JEDEC specifications, +85°C/85% temperature-humidity bias, temperature cycling, mechanical shock, vibration, etc. This principle gives engineers full confidence that these highly integrated solutions can provide reliability comparable to traditional switching converters, which require numerous associated external components that must be purchased, assembled and inspected by procurement, manufacturing and quality departments.
Conclusion
The industry's pressing need for faster performance and lower power consumption has driven digital components to operate at lower voltages. To meet this trend, DC/DC brick module suppliers are introducing new devices that can directly step down the distribution voltage rail (24V or 48V) to an output voltage below 5V with high efficiency. Generating a 5V bias voltage rail solely for the efficient operation of traditional switching converters adds undesirable cost, power, complexity, or components. The LTM4611 is built into a single LGA package (which many other integrated circuits use) and maintains high efficiency and excellent thermal performance over the entire input voltage range. The LTM4611 is a simple and highly reliable step-down regulator that can easily adapt to point-of-load applications that require high output current from input voltages as low as 1.5V and reduces the need for "extra" voltage rails.
Previous article:MicrochipdsPIC33F Offline 1000W UPS Power Supply Reference Design
Next article:Analysis of Internal Components of PC Power Supply
Recommended ReadingLatest update time:2024-11-16 21:26
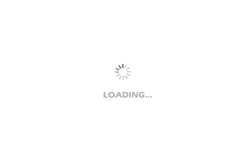
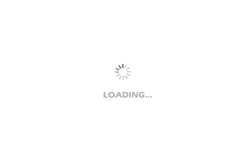
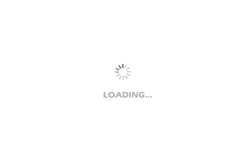
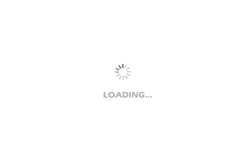
- Popular Resources
- Popular amplifiers
-
西门子S7-12001500 PLC SCL语言编程从入门到精通 (北岛李工)
-
New Energy Vehicle Detection and Diagnosis Experiment (Edited by Mao Caiyun, Zhou Xien, and Long Jiwen)
-
Virtualization Technology Practice Guide - High-efficiency and low-cost solutions for small and medium-sized enterprises (Wang Chunhai)
-
ESP32-S3 source code
- MathWorks and NXP Collaborate to Launch Model-Based Design Toolbox for Battery Management Systems
- STMicroelectronics' advanced galvanically isolated gate driver STGAP3S provides flexible protection for IGBTs and SiC MOSFETs
- New diaphragm-free solid-state lithium battery technology is launched: the distance between the positive and negative electrodes is less than 0.000001 meters
- [“Source” Observe the Autumn Series] Application and testing of the next generation of semiconductor gallium oxide device photodetectors
- 采用自主设计封装,绝缘电阻显著提高!ROHM开发出更高电压xEV系统的SiC肖特基势垒二极管
- Will GaN replace SiC? PI's disruptive 1700V InnoMux2 is here to demonstrate
- From Isolation to the Third and a Half Generation: Understanding Naxinwei's Gate Driver IC in One Article
- The appeal of 48 V technology: importance, benefits and key factors in system-level applications
- Important breakthrough in recycling of used lithium-ion batteries
- Innolux's intelligent steer-by-wire solution makes cars smarter and safer
- 8051 MCU - Parity Check
- How to efficiently balance the sensitivity of tactile sensing interfaces
- What should I do if the servo motor shakes? What causes the servo motor to shake quickly?
- 【Brushless Motor】Analysis of three-phase BLDC motor and sharing of two popular development boards
- Midea Industrial Technology's subsidiaries Clou Electronics and Hekang New Energy jointly appeared at the Munich Battery Energy Storage Exhibition and Solar Energy Exhibition
- Guoxin Sichen | Application of ferroelectric memory PB85RS2MC in power battery management, with a capacity of 2M
- Analysis of common faults of frequency converter
- In a head-on competition with Qualcomm, what kind of cockpit products has Intel come up with?
- Dalian Rongke's all-vanadium liquid flow battery energy storage equipment industrialization project has entered the sprint stage before production
- Allegro MicroSystems Introduces Advanced Magnetic and Inductive Position Sensing Solutions at Electronica 2024
- Car key in the left hand, liveness detection radar in the right hand, UWB is imperative for cars!
- After a decade of rapid development, domestic CIS has entered the market
- Aegis Dagger Battery + Thor EM-i Super Hybrid, Geely New Energy has thrown out two "king bombs"
- A brief discussion on functional safety - fault, error, and failure
- In the smart car 2.0 cycle, these core industry chains are facing major opportunities!
- The United States and Japan are developing new batteries. CATL faces challenges? How should China's new energy battery industry respond?
- Murata launches high-precision 6-axis inertial sensor for automobiles
- Ford patents pre-charge alarm to help save costs and respond to emergencies
- New real-time microcontroller system from Texas Instruments enables smarter processing in automotive and industrial applications
- EEWORLD University Hall----Using JTAG with UCD3138
- AltiumDesigner integrated library design based on Access database
- EEWORLD University Hall----Live Replay: TE explains the design trends of smart antennas and sensor application cases in the Internet of Things
- Solution to EPLAN software freeze
- PDIUSBD12 Send mode command, soft connection does not work
- Can the same timer realize two independent PWM pulses?
- Today's live broadcast: ADI inertial MEMS applications
- .DSN file is garbled when opened.
- [GD32L233C-START Review] Introduction to onboard resources
- Live Q&A Summary: ADI MEMS Sensors Open a New Era of Conditional State Monitoring