1 Introduction
The power supply system is an important equipment of the power system. It is mainly used in power plants, substations, and communication power supplies. It is an important power supply to ensure automatic control and protection, power, instrumentation, signal, communication, emergency lighting, etc. Its performance and quality are directly related to the stable operation of the power grid and the safety of equipment. In the past, the centralized monitor of power supply equipment mainly used the single-chip microcomputer as the core to realize the acquisition, control, communication, etc. of various signals. Compared with the single-chip microcomputer, the DSP chip has better processing performance, lower power consumption, higher peripheral integration, and stronger real-time control ability. This paper uses TI's DSP chip TMS320LF2407A in the development of the monitoring device of the power DC system. By using its efficient real-time processing capability (30MIPS), the operating status of the DC charging module and the battery is detected in real time, and the relevant data is recorded and processed, so that the remote function can realize the remote signaling, telemetry, remote control, and remote adjustment of the power supply equipment, which is conducive to replacing the manual control technology with the computer monitoring system, meeting the requirements of power station automation, realizing unmanned substations, and improving the comprehensive efficiency and feasibility of the power grid.
2 Overall structure of monitoring system
The overall structure of the monitoring system consists of a computer in the monitoring and dispatching center, a centralized monitor, and a charging module monitoring unit. The monitoring and dispatching center can communicate serially with the centralized monitor through the telephone network, MODEM or CAN, LONWORK bus; the centralized monitor communicates serially with the intelligent charging module through RS485 or RS232. The centralized monitor can receive and quickly respond to monitoring commands and control instructions from the upper monitoring center through serial communication at any time. On the one hand, it can realize telemetry, remote control, remote signaling, and remote adjustment of the lower monitoring unit (charging module) through serial communication. On the other hand, it sends status change or alarm information to the monitoring and dispatching center. Maintenance personnel can monitor the operation of each on-site rectifier and distribution equipment in the monitoring and dispatching center to achieve unattended operation.
3 Working principle and hardware design of centralized monitor
3.1 Working principle of centralized monitor
The structure of centralized monitor consists of data processing unit, human-machine interface (keyboard, display, clock) unit, serial communication unit, etc.
As shown in Figure 1, each monitored analog quantity is selected by the multi-way switch CD4051 to enter the AD conversion interface of 2407A, and is sampled regularly by 2407A. Since there are many monitored analog quantities, the DSP adopts the cascade mode during sampling, and performs 16 conversions at a time. The DSP compares, calculates, stores, displays, and alarms the converted data. The switch input enters the IOPB port of the DSP through the optocoupler and buffer. The DSP generates corresponding actions such as sound and light alarms and shutting down the power module through the detection and numerical processing results of the IOPB port. Through the buttons of the human-machine interface, you can flip the screen up, down, forward, and backward to view the monitoring information (charging module status, battery status, etc.) and change the system parameter settings (temperature compensation coefficient, voltage, current threshold, etc.). The DSP controls the module power supply and battery through serial communication and relay action respectively. The analog input includes AC input voltage, AC input current, system output DC voltage, system load total current, battery voltage, current, temperature, ambient temperature, etc. These analog signals are converted through sensors and transmitters, such as: DC output voltage sampling comes from the DC panel output end, after voltage reduction, buffering, filtering, it is converted to 0-3.3V voltage; current sampling comes from the distribution panel shunt, after amplification, photoelectric coupling, filtering, buffering, it is converted to 0-3.3V voltage. Digital input includes fuse blown, DC output overvoltage, undervoltage signal, main switch status, etc.
[page]3.2 Hardware Design of Centralized Monitor
The TMS320 series DSP controller integrates real-time processing capability and controller peripheral functions, providing an ideal solution for control system applications. Here we use the TMS320LF2407A fixed-point DSP controller as the processor of the data processing unit. It is a true single-chip controller. Its power supply voltage is reduced to 3.3 volts. The execution speed of 30MIPS shortens the instruction cycle to 33ns, thereby improving the real-time control capability of the controller. There are 32K words of FLASH program memory, 1.5K words of data program RAM, 544 words of dual-port RAM and 2K words of single-port RAM, two event manager modules, expandable external memory 192K words of space, watchdog timer module, controller network (CAN) 2.0B module, 10-bit A/D converter, 40 individually programmed or multiplexed IO ports, and power management can independently switch peripheral devices into low-power working mode. This can reduce external expansion devices and reduce the size of the entire monitor.
The main functions of the human-machine interface unit are to display the system status information, provide sound and light alarms, and accept key inputs. An LCD module is used to display the system status information and prompt key input parameter information, and the light-emitting diode and buzzer are used to display the alarm information. The clock uses the calendar chip PCF8583 with an I2C bus interface. Since the 2407A does not have a dedicated I2C timing pin, software is used to simulate the I2C bus timing in this design. The pins SPISIM and SPISTE of the 2407A SPI port are set to I/O mode and connected to the SCL and SDA pins of PCF8583 respectively, and a pull-up resistor is required. In order to simplify the circuit, we only use 5 buttons to complete the query setting needs.
The data communication unit includes data exchange between the DSP and the upper monitoring system and the DSP and the lower monitoring unit. Here, the upper monitoring system refers to the dispatch center computer or the local PC, and the lower monitoring unit refers to the charging module monitoring unit composed of a single chip. Asynchronous serial transceiver 16C550 and MODEM can be used to realize remote communication with the central computer; communication with the local machine can be achieved through RS232 bus. Since the power supply of 2407A chip is 3.3V and its serial communication SCI interface is CMOS level, and the microcomputer serial port uses the standard RS-232-CEIA level (-3V~-15V is 1, +3V~+15V is 0), MAXIM's low-power and high-speed level conversion chip MAX3232E is used to realize CMOS and EIA level conversion, and optical coupling isolation is used between each communication interface. The RS-232 standard bus is 25 lines, and the simplest 3-line transmission (ground line, sending line, receiving line) is used in actual applications. The communication interface chip of 2407 and the single-chip microcomputer is MAX488, and the interface circuit complies with the RS-485 standard. It can also realize external communication according to different needs of users, such as using CAN bus to connect to the outside to realize field bus control.
[page]4 Software Design of Centralized Monitor
In order to facilitate users to add or delete certain functions, the software adopts a modular structure and is programmed in a mixed manner using C language and assembly language. The main program flow is shown in Figure 2, which completes the data analysis of the AD conversion results, the processing of the IO port digital quantity, the call of the battery management program, the clock program, the LCD display program, etc. The data analysis includes the calculation of the discharge current difference of the battery group, the floating charge voltage judgment, the charging current comparison, the discharge voltage comparison, the low voltage cut-off voltage threshold adjustment, etc.; the IO digital quantity processing includes the judgment and alarm of the switch quantity; the interrupt program includes AD conversion, serial communication, keyboard processing, etc.
The battery management program automatically controls the battery for floating charge and discharge protection according to the results of data analysis. The monitor studied in this paper considers the management of two groups of batteries. The DSP calculates and analyzes the battery status based on the real-time data of the detected battery group, and automatically performs the floating charge and floating charge conversion according to the set parameter values, and provides comprehensive sound and light alarms and corresponding battery protection. For example: based on the discharge current difference of each group of batteries, it prompts possible battery failure; the charging current limit value is set at different stages of battery voltage to ensure that the battery capacity is replenished to the maximum. In the charging current limit, the maximum value of each battery charging current is compared with the current limit value to ensure that the current of each battery group does not exceed the charging current limit value. In the low-voltage circuit breaker, when the battery is discharged to the set low-voltage cut-off voltage, the battery group will be automatically cut off to prevent the battery from over-discharging. The low-voltage cut-off voltage value set here is not fixed. It is related to the actual discharge current. When the current is high, the final voltage is set to be smaller, and when the current is low, the low-voltage cut-off voltage threshold is higher. The charging module is regularly placed in the off state through software control means to discharge the battery, prevent the internal resistance of the battery from increasing, and thus increase the service life of the battery. The battery management program flow chart is shown in Figure 3.
The LCD display program framework is shown in Figure 4: Each screen can display 15*4 Chinese characters, and the display screen is divided into 16 screens. The first screen is the monitoring submenu, which includes time, AC voltage, AC current, output voltage, load current, ambient temperature, and floating charge status. Press the up key on the first screen to enter the main menu screen, which includes four submenus: monitoring, charging module, battery, and alarm record. You can arbitrarily select the submenu you want to view on the main menu screen, where the charging module content includes status query and parameter setting (normal, broadcast). The content in the battery includes status query and parameter setting. Entering the status query submenu can view the temperature, voltage, current, floating charge status, etc. of the battery pack. You can change the parameters related to the battery such as the temperature compensation coefficient through parameter setting. The fault record submenu includes the fault number, the time of occurrence, etc. The conversion of information between screens, the movement of the cursor in the screen, and the increase and decrease of parameters are realized through the combination of up, down, left, right, and confirm keys.
[page] Serial communication software, including serial communication between DSP and PC and serial communication between DSP and single-chip microcomputer. For PC, VC++6.0 is used as the development tool, and Windows ActiveX control - MSComm is used to implement the communication program. In the event processing function oncomm1, the received lower computer data is written into the database file to further realize the function of the computer monitoring software. The centralized monitor controls multiple charging modules through the communication between DSP2407 and multiple single-chip microcomputers. Data can be transmitted to each charging module in turn or sent simultaneously (broadcast mode). In the protocol of this paper, the communication between DSP and PC and single-chip microcomputer adopts CRC standard cyclic redundancy code check, baud rate 9600bps, frame format: 11 bits per frame, 1 start bit, 8 data bits, 1 check bit, and 1 stop bit. In the communication between PC and DSP, since the PC needs to control multiple DC screens, that is, it needs to communicate with multiple DSPs, the DSP communication in this paper adopts the address bit mode that is very effective in processing small data, sets the sleep bit of SCI to enter the receiving sleep mode, and interrupts when the address frame is detected, and then judges whether the received address is the same as its own address. If the same, it can read the data sent by the PC afterwards. The data message format is shown in Figure 5.
Figure 4 LCD display program flowchart
Figure 5 Data message format
Similarly, the charging module address needs to be sent when the DSP communicates with the microcontroller to establish a one-to-one channel or a one-to-many channel (broadcast mode) before sending data. When the DSP sends the address code, the check bit is 1, and when it sends the data code, the check bit is 0. The DSP serial communication adopts the interrupt method. After the DSP starts the serial port, it will no longer inquire about its status and continue to execute its own program to realize the parallel operation of the DSP and the serial port. When the serial port generates an interrupt, it first applies for an interrupt to the DSP. After the DSP responds to the interrupt, it temporarily interrupts its own program and executes the corresponding serial port interrupt service program. After execution, it returns to the main program. This method allows information to be processed in a timely manner.
6 Conclusion
The centralized monitor of the power supply system studied in this paper is based on the DSP with fast computing capability. It has the following main functions based on the real-time detection of multiple electrical quantities: 1. It can monitor the current, voltage and temperature of the battery pack in real time; the DC output voltage, current, fuse status signal input and DC output alarm in the DC panel; the working status of the charging module; AC voltage, current, etc.; 2. It can intelligently control the on/off and equalization/floating charge of the charging module according to the status of the battery, and adjust the output voltage and current limit level of the charging module; 3. It can query the status information of each charging module and battery through buttons and change system parameters; 4. It can give sound and light alarm for faults and provide fault history records; 5. It uses the serial interface DSP to exchange data with the PC and the charging module, and accepts the remote control of the monitoring and dispatching center to realize remote communication, telemetry, remote control and remote adjustment of the charger. Compared with the monitor with the single-chip microcomputer as the core, this device better meets the real-time, stability and reliability requirements of the power DC system equipment monitoring system, and is more adapted to the development of modern power supply technology.
References
1 Liu Heping et al. TMS320LF240X DSP Structure, Principle and Application. Beijing University of Aeronautics and Astronautics Press. 2002
2 Wang Jiaqing, Chief Editor. Principle, Use and Maintenance of Intelligent High-Frequency Switching Power Supply System. Posts and Telecommunications Press. 2000
3 Li Xianyong. VC++ Serial Communication Technology and Engineering Practice Posts and Telecommunications Press. 2002
Keywords:DSP
Reference address:Research on Centralized Monitor of Electric Power System Based on DSP
The power supply system is an important equipment of the power system. It is mainly used in power plants, substations, and communication power supplies. It is an important power supply to ensure automatic control and protection, power, instrumentation, signal, communication, emergency lighting, etc. Its performance and quality are directly related to the stable operation of the power grid and the safety of equipment. In the past, the centralized monitor of power supply equipment mainly used the single-chip microcomputer as the core to realize the acquisition, control, communication, etc. of various signals. Compared with the single-chip microcomputer, the DSP chip has better processing performance, lower power consumption, higher peripheral integration, and stronger real-time control ability. This paper uses TI's DSP chip TMS320LF2407A in the development of the monitoring device of the power DC system. By using its efficient real-time processing capability (30MIPS), the operating status of the DC charging module and the battery is detected in real time, and the relevant data is recorded and processed, so that the remote function can realize the remote signaling, telemetry, remote control, and remote adjustment of the power supply equipment, which is conducive to replacing the manual control technology with the computer monitoring system, meeting the requirements of power station automation, realizing unmanned substations, and improving the comprehensive efficiency and feasibility of the power grid.
2 Overall structure of monitoring system
The overall structure of the monitoring system consists of a computer in the monitoring and dispatching center, a centralized monitor, and a charging module monitoring unit. The monitoring and dispatching center can communicate serially with the centralized monitor through the telephone network, MODEM or CAN, LONWORK bus; the centralized monitor communicates serially with the intelligent charging module through RS485 or RS232. The centralized monitor can receive and quickly respond to monitoring commands and control instructions from the upper monitoring center through serial communication at any time. On the one hand, it can realize telemetry, remote control, remote signaling, and remote adjustment of the lower monitoring unit (charging module) through serial communication. On the other hand, it sends status change or alarm information to the monitoring and dispatching center. Maintenance personnel can monitor the operation of each on-site rectifier and distribution equipment in the monitoring and dispatching center to achieve unattended operation.
3 Working principle and hardware design of centralized monitor
3.1 Working principle of centralized monitor
The structure of centralized monitor consists of data processing unit, human-machine interface (keyboard, display, clock) unit, serial communication unit, etc.
As shown in Figure 1, each monitored analog quantity is selected by the multi-way switch CD4051 to enter the AD conversion interface of 2407A, and is sampled regularly by 2407A. Since there are many monitored analog quantities, the DSP adopts the cascade mode during sampling, and performs 16 conversions at a time. The DSP compares, calculates, stores, displays, and alarms the converted data. The switch input enters the IOPB port of the DSP through the optocoupler and buffer. The DSP generates corresponding actions such as sound and light alarms and shutting down the power module through the detection and numerical processing results of the IOPB port. Through the buttons of the human-machine interface, you can flip the screen up, down, forward, and backward to view the monitoring information (charging module status, battery status, etc.) and change the system parameter settings (temperature compensation coefficient, voltage, current threshold, etc.). The DSP controls the module power supply and battery through serial communication and relay action respectively. The analog input includes AC input voltage, AC input current, system output DC voltage, system load total current, battery voltage, current, temperature, ambient temperature, etc. These analog signals are converted through sensors and transmitters, such as: DC output voltage sampling comes from the DC panel output end, after voltage reduction, buffering, filtering, it is converted to 0-3.3V voltage; current sampling comes from the distribution panel shunt, after amplification, photoelectric coupling, filtering, buffering, it is converted to 0-3.3V voltage. Digital input includes fuse blown, DC output overvoltage, undervoltage signal, main switch status, etc.
[page]3.2 Hardware Design of Centralized Monitor
The TMS320 series DSP controller integrates real-time processing capability and controller peripheral functions, providing an ideal solution for control system applications. Here we use the TMS320LF2407A fixed-point DSP controller as the processor of the data processing unit. It is a true single-chip controller. Its power supply voltage is reduced to 3.3 volts. The execution speed of 30MIPS shortens the instruction cycle to 33ns, thereby improving the real-time control capability of the controller. There are 32K words of FLASH program memory, 1.5K words of data program RAM, 544 words of dual-port RAM and 2K words of single-port RAM, two event manager modules, expandable external memory 192K words of space, watchdog timer module, controller network (CAN) 2.0B module, 10-bit A/D converter, 40 individually programmed or multiplexed IO ports, and power management can independently switch peripheral devices into low-power working mode. This can reduce external expansion devices and reduce the size of the entire monitor.
The main functions of the human-machine interface unit are to display the system status information, provide sound and light alarms, and accept key inputs. An LCD module is used to display the system status information and prompt key input parameter information, and the light-emitting diode and buzzer are used to display the alarm information. The clock uses the calendar chip PCF8583 with an I2C bus interface. Since the 2407A does not have a dedicated I2C timing pin, software is used to simulate the I2C bus timing in this design. The pins SPISIM and SPISTE of the 2407A SPI port are set to I/O mode and connected to the SCL and SDA pins of PCF8583 respectively, and a pull-up resistor is required. In order to simplify the circuit, we only use 5 buttons to complete the query setting needs.
The data communication unit includes data exchange between the DSP and the upper monitoring system and the DSP and the lower monitoring unit. Here, the upper monitoring system refers to the dispatch center computer or the local PC, and the lower monitoring unit refers to the charging module monitoring unit composed of a single chip. Asynchronous serial transceiver 16C550 and MODEM can be used to realize remote communication with the central computer; communication with the local machine can be achieved through RS232 bus. Since the power supply of 2407A chip is 3.3V and its serial communication SCI interface is CMOS level, and the microcomputer serial port uses the standard RS-232-CEIA level (-3V~-15V is 1, +3V~+15V is 0), MAXIM's low-power and high-speed level conversion chip MAX3232E is used to realize CMOS and EIA level conversion, and optical coupling isolation is used between each communication interface. The RS-232 standard bus is 25 lines, and the simplest 3-line transmission (ground line, sending line, receiving line) is used in actual applications. The communication interface chip of 2407 and the single-chip microcomputer is MAX488, and the interface circuit complies with the RS-485 standard. It can also realize external communication according to different needs of users, such as using CAN bus to connect to the outside to realize field bus control.
[page]4 Software Design of Centralized Monitor
In order to facilitate users to add or delete certain functions, the software adopts a modular structure and is programmed in a mixed manner using C language and assembly language. The main program flow is shown in Figure 2, which completes the data analysis of the AD conversion results, the processing of the IO port digital quantity, the call of the battery management program, the clock program, the LCD display program, etc. The data analysis includes the calculation of the discharge current difference of the battery group, the floating charge voltage judgment, the charging current comparison, the discharge voltage comparison, the low voltage cut-off voltage threshold adjustment, etc.; the IO digital quantity processing includes the judgment and alarm of the switch quantity; the interrupt program includes AD conversion, serial communication, keyboard processing, etc.
The battery management program automatically controls the battery for floating charge and discharge protection according to the results of data analysis. The monitor studied in this paper considers the management of two groups of batteries. The DSP calculates and analyzes the battery status based on the real-time data of the detected battery group, and automatically performs the floating charge and floating charge conversion according to the set parameter values, and provides comprehensive sound and light alarms and corresponding battery protection. For example: based on the discharge current difference of each group of batteries, it prompts possible battery failure; the charging current limit value is set at different stages of battery voltage to ensure that the battery capacity is replenished to the maximum. In the charging current limit, the maximum value of each battery charging current is compared with the current limit value to ensure that the current of each battery group does not exceed the charging current limit value. In the low-voltage circuit breaker, when the battery is discharged to the set low-voltage cut-off voltage, the battery group will be automatically cut off to prevent the battery from over-discharging. The low-voltage cut-off voltage value set here is not fixed. It is related to the actual discharge current. When the current is high, the final voltage is set to be smaller, and when the current is low, the low-voltage cut-off voltage threshold is higher. The charging module is regularly placed in the off state through software control means to discharge the battery, prevent the internal resistance of the battery from increasing, and thus increase the service life of the battery. The battery management program flow chart is shown in Figure 3.
The LCD display program framework is shown in Figure 4: Each screen can display 15*4 Chinese characters, and the display screen is divided into 16 screens. The first screen is the monitoring submenu, which includes time, AC voltage, AC current, output voltage, load current, ambient temperature, and floating charge status. Press the up key on the first screen to enter the main menu screen, which includes four submenus: monitoring, charging module, battery, and alarm record. You can arbitrarily select the submenu you want to view on the main menu screen, where the charging module content includes status query and parameter setting (normal, broadcast). The content in the battery includes status query and parameter setting. Entering the status query submenu can view the temperature, voltage, current, floating charge status, etc. of the battery pack. You can change the parameters related to the battery such as the temperature compensation coefficient through parameter setting. The fault record submenu includes the fault number, the time of occurrence, etc. The conversion of information between screens, the movement of the cursor in the screen, and the increase and decrease of parameters are realized through the combination of up, down, left, right, and confirm keys.
[page] Serial communication software, including serial communication between DSP and PC and serial communication between DSP and single-chip microcomputer. For PC, VC++6.0 is used as the development tool, and Windows ActiveX control - MSComm is used to implement the communication program. In the event processing function oncomm1, the received lower computer data is written into the database file to further realize the function of the computer monitoring software. The centralized monitor controls multiple charging modules through the communication between DSP2407 and multiple single-chip microcomputers. Data can be transmitted to each charging module in turn or sent simultaneously (broadcast mode). In the protocol of this paper, the communication between DSP and PC and single-chip microcomputer adopts CRC standard cyclic redundancy code check, baud rate 9600bps, frame format: 11 bits per frame, 1 start bit, 8 data bits, 1 check bit, and 1 stop bit. In the communication between PC and DSP, since the PC needs to control multiple DC screens, that is, it needs to communicate with multiple DSPs, the DSP communication in this paper adopts the address bit mode that is very effective in processing small data, sets the sleep bit of SCI to enter the receiving sleep mode, and interrupts when the address frame is detected, and then judges whether the received address is the same as its own address. If the same, it can read the data sent by the PC afterwards. The data message format is shown in Figure 5.
Similarly, the charging module address needs to be sent when the DSP communicates with the microcontroller to establish a one-to-one channel or a one-to-many channel (broadcast mode) before sending data. When the DSP sends the address code, the check bit is 1, and when it sends the data code, the check bit is 0. The DSP serial communication adopts the interrupt method. After the DSP starts the serial port, it will no longer inquire about its status and continue to execute its own program to realize the parallel operation of the DSP and the serial port. When the serial port generates an interrupt, it first applies for an interrupt to the DSP. After the DSP responds to the interrupt, it temporarily interrupts its own program and executes the corresponding serial port interrupt service program. After execution, it returns to the main program. This method allows information to be processed in a timely manner.
6 Conclusion
The centralized monitor of the power supply system studied in this paper is based on the DSP with fast computing capability. It has the following main functions based on the real-time detection of multiple electrical quantities: 1. It can monitor the current, voltage and temperature of the battery pack in real time; the DC output voltage, current, fuse status signal input and DC output alarm in the DC panel; the working status of the charging module; AC voltage, current, etc.; 2. It can intelligently control the on/off and equalization/floating charge of the charging module according to the status of the battery, and adjust the output voltage and current limit level of the charging module; 3. It can query the status information of each charging module and battery through buttons and change system parameters; 4. It can give sound and light alarm for faults and provide fault history records; 5. It uses the serial interface DSP to exchange data with the PC and the charging module, and accepts the remote control of the monitoring and dispatching center to realize remote communication, telemetry, remote control and remote adjustment of the charger. Compared with the monitor with the single-chip microcomputer as the core, this device better meets the real-time, stability and reliability requirements of the power DC system equipment monitoring system, and is more adapted to the development of modern power supply technology.
References
1 Liu Heping et al. TMS320LF240X DSP Structure, Principle and Application. Beijing University of Aeronautics and Astronautics Press. 2002
2 Wang Jiaqing, Chief Editor. Principle, Use and Maintenance of Intelligent High-Frequency Switching Power Supply System. Posts and Telecommunications Press. 2000
3 Li Xianyong. VC++ Serial Communication Technology and Engineering Practice Posts and Telecommunications Press. 2002
Previous article:Design of a dual-color three-cycle colored light controller
Next article:High-performance current-mode PWM controller meets green power design requirements
Recommended ReadingLatest update time:2024-11-16 23:49
Multi-monitor will be the killer app for DisplayPort
DisplayPort has come a long way from being an effort to establish a new external and internal video interface to becoming the next generation PC interconnect and a viable industry standard interconnect video interface. The question of why we need another video interface in addition to the ones we have today is often
[Power Management]
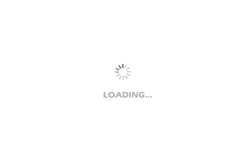
Application Examples of the MAXQ3120 Mixed-Signal Microcontroller
Designers and manufacturers of monitoring systems have been looking for microcontrollers to provide an increasing number of general functions for daily monitoring applications, including meeting the requirements of electricity metering, vehicle monitoring, data collection, and sensor adjustment. The MAXQ3120 is
[Microcontroller]
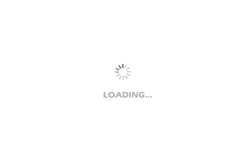
Design of image capture card based on TMS320F206DSP
Abstract: An interface design scheme is proposed that uses the video A/D chip TLC5510 and the low-end DSP chip TMS320F206 to achieve image acquisition. At the same time, the interface program is given, which provides a new application path for the low-end DSP chip.
Keywords: ADC DSP interface design vide
[Embedded]
ARM11 and DSP Collaborative Video Stream Processing Technology 3G Video Safety Helmet Design
This paper designs a 3G video helmet based on ARM11 and DSP dual-core video processing technology. After local efficient compression processing of the audio and video signals at the work site, it transmits them to the remote server in real time through the 3G network, realizing remote command and monitoring and two-
[Embedded]
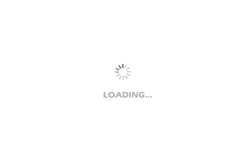
Comparison between ARM+DSP, AVR and C51
Single-chip microcomputers have been widely used in industrial automation control, automatic detection, portable intelligent instruments, military, aerospace, household appliances, intelligent toys, power electronics, mechatronics equipment and other fields, making all kinds of products greatly improved in terms of fun
[Microcontroller]
Realization of Multi-channel Measurement Signal Spread Spectrum Transmission System Using DSP
1 Introduction
In the field of measurement and control, it is usually required to transmit multiple measurement signals. The transmission process of the signal is often interfered by the complex environment around it, which will cause great distortion. For example, if a spread spectrum communication transmission s
[Test Measurement]
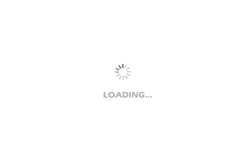
FlexEnable strategically focuses on China development, creating a new wave of low-cost flexible displays
FlexEnable, a UK company headquartered in Cambridge, is a leader in the development and industrialization of flexible organic electronics and has implemented a major corporate strategy to revolutionize the Chinese display industry by providing the lowest cost and most scalable flexible display technology for mass mark
[Power Management]
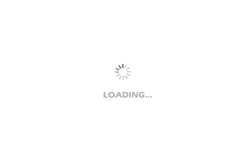
Implementing Bit- and Cycle-Accurate Floating-Point DSP Algorithms Using Xilinx FPGAs
The need for floating point operations is becoming more common due to existing FPGA and system level requirements. This video demonstrates how System Generator for DSP provides users with a powerful design flow to implement bit and cycle accurate, single/double/custom precision floating point operations.
[Embedded]
- Popular Resources
- Popular amplifiers
Recommended Content
Latest Power Management Articles
- MathWorks and NXP Collaborate to Launch Model-Based Design Toolbox for Battery Management Systems
- STMicroelectronics' advanced galvanically isolated gate driver STGAP3S provides flexible protection for IGBTs and SiC MOSFETs
- New diaphragm-free solid-state lithium battery technology is launched: the distance between the positive and negative electrodes is less than 0.000001 meters
- [“Source” Observe the Autumn Series] Application and testing of the next generation of semiconductor gallium oxide device photodetectors
- 采用自主设计封装,绝缘电阻显著提高!ROHM开发出更高电压xEV系统的SiC肖特基势垒二极管
- Will GaN replace SiC? PI's disruptive 1700V InnoMux2 is here to demonstrate
- From Isolation to the Third and a Half Generation: Understanding Naxinwei's Gate Driver IC in One Article
- The appeal of 48 V technology: importance, benefits and key factors in system-level applications
- Important breakthrough in recycling of used lithium-ion batteries
MoreSelected Circuit Diagrams
MorePopular Articles
- Innolux's intelligent steer-by-wire solution makes cars smarter and safer
- 8051 MCU - Parity Check
- How to efficiently balance the sensitivity of tactile sensing interfaces
- What should I do if the servo motor shakes? What causes the servo motor to shake quickly?
- 【Brushless Motor】Analysis of three-phase BLDC motor and sharing of two popular development boards
- Midea Industrial Technology's subsidiaries Clou Electronics and Hekang New Energy jointly appeared at the Munich Battery Energy Storage Exhibition and Solar Energy Exhibition
- Guoxin Sichen | Application of ferroelectric memory PB85RS2MC in power battery management, with a capacity of 2M
- Analysis of common faults of frequency converter
- In a head-on competition with Qualcomm, what kind of cockpit products has Intel come up with?
- Dalian Rongke's all-vanadium liquid flow battery energy storage equipment industrialization project has entered the sprint stage before production
MoreDaily News
- Allegro MicroSystems Introduces Advanced Magnetic and Inductive Position Sensing Solutions at Electronica 2024
- Car key in the left hand, liveness detection radar in the right hand, UWB is imperative for cars!
- After a decade of rapid development, domestic CIS has entered the market
- Aegis Dagger Battery + Thor EM-i Super Hybrid, Geely New Energy has thrown out two "king bombs"
- A brief discussion on functional safety - fault, error, and failure
- In the smart car 2.0 cycle, these core industry chains are facing major opportunities!
- The United States and Japan are developing new batteries. CATL faces challenges? How should China's new energy battery industry respond?
- Murata launches high-precision 6-axis inertial sensor for automobiles
- Ford patents pre-charge alarm to help save costs and respond to emergencies
- New real-time microcontroller system from Texas Instruments enables smarter processing in automotive and industrial applications
Guess you like
- Three considerations for selecting Ethernet for harsh industrial environments
- [RVB2601 Creative Application Development] User Experience 02 -- KV Storage
- 【EEWorld invites you to play disassembly
- Simplify the design of automotive body motor controllers and quickly achieve lightweighting
- Does anyone know how to calculate the input power by first boosting the voltage and then reducing it?
- Remote control aircraft, electric vehicles, motorcycle anti-theft devices, flashlights, etc. single chip computer development
- Why do I/O ports of microcontrollers need drivers?
- There is a constant current source circuit. The simulation is fine, but the actual circuit is incorrect. Can you help me take a look? Thank you!
- The boost circuit is unstable, what is the reason?
- Wireless PLC remote download 4-20ma wireless transmission 0-5v wireless transmission analog quantity wireless transmission solution