Thermal management is the most difficult, demanding, and expensive design aspect of a new LED lamp. If thermal management is not adequately performed, it can lead to catastrophic consequences such as lighting failure or fire. However, thermal management of LED lamps is the most complex, demanding, and expensive aspect of the entire design solution. This article will explore how to implement negative temperature coefficient (NTC) thermal management to maximize the safety of LED designs and significantly reduce power consumption.
In traditional incandescent bulbs, the only heat source is the filament, which is not in direct contact with anything. In LED lamps, however, the LED is the light source, and the heat dissipation of the LED is in direct contact with the LED bulb. This direct contact is due to the way the LED is connected to the driver circuit. In order to achieve heat dissipation, the heat must be removed from the LED and driver circuit or effectively managed, which is also the basic premise for the long-term operation of the LED lamp.
To understand the importance of thermal management, let's imagine an application where an LED lamp is installed in a general lighting socket such as a wall sconce or ceiling lamp, and the LED lamp is controlled by a wall switch. Since most standard lamps such as wall sconces or ceiling lamps rely mainly on heat convection or airflow to dissipate heat, the heat dissipation effect of this application is not ideal for LED lamps.
Without effective thermal management, the consequences can be disastrous, from frequent replacement of failed LED lamps to building fires. Using smart LED lamp control to monitor the temperature of the LED lamp is a simpler way to manage thermal management, and it also greatly improves safety because the LED lamp can reduce power when the temperature rises.
NTC Thermal Management
The basic principle of the NTC circuit is to improve the safety of the LED lamp and reduce the complexity of the design by monitoring the temperature of the LED lamp. When the temperature rises, the controller reduces the lumens to keep the LED within a safe level. In other words, when the temperature rises, the lumens are reduced, and when the temperature drops, the lumens are increased.
We can detect the temperature change of the LED lamp by sensing the voltage across the NTC. The sensed voltage is directly related to the temperature of the NTC, and the resistance of the NTC decreases as the temperature of the NTC and its surrounding circuits increases. There are two basic methods for determining temperature using the NTC.
Method 1: Use the NTC in a voltage divider circuit that forces a known voltage on the system and then measures the voltage at the NTC node. As the temperature of the NTC increases, the resistance decreases. The reduction in resistance will cause the voltage divider ratio to change. The voltage at the NTC node will also decrease as the temperature increases.
Method 2: Force a known current through the NTC and measure the voltage across the NTC. When the temperature of the NTC increases, the resistance decreases. According to Ohm's law, the decrease in resistance will change the voltage at the NTC node. If the resistance decreases and the current remains constant, the voltage at the NTC node will also decrease.
Both methods of monitoring the temperature of LED lamps are simple and straightforward to implement in terms of improved operation and safety. Figure 1 is a schematic diagram of the two methods using the LED as the source of the temperature increase.
Figure 1: Two basic methods of determining temperature using NTC.
Too hot or LED failure?
When the lumen output of an LED lamp drops, it is important to know whether the LED output is dropping due to excessive temperature environment or due to LED failure. We can use an indicator that shows the lumen drop to determine the cause of the drop.
The lumen drop in the system shown in Figure 2 is indicated by a low-power red LED. When the system is at maximum lumen output, the red LED is off; when the temperature of the LED lamp increases, the lumen output decreases, and when the lumen output decreases, the red LED turns on. As the lumen output continues to decrease, the intensity of the red LED increases accordingly. When the lumen output drops to its minimum intensity, the red LED will turn on completely.
Figure 2
When lumen output is at minimum intensity and the temperature of the LED lamp is still high, the red LED indicator can also serve as an alarm to warn of serious problems. In alarm mode, the red LED will flash continuously while all white LEDs are off.
The block diagram of Figure 3 shows a general LED driver and LED controller with NTC and alarm indicators. The general LED lamp contains an LED driver that is configured to provide a set current through the LED. The driver cannot reduce lumens based on temperature. The temperature monitoring function provided by the driver is only used for its own protection and completely shuts down when the temperature is extremely high.
The LED controller has all the control functions of the general LED driver and can enhance the intelligence of other functions such as temperature monitoring, communication and dimming control. The blue part of the block diagram is the basic module and components of the LED controller. The components shown in red are not required for basic operation, but are shown for the NTC and alarm functions described in this article.
The addition of NTC to the general LED can shut down the LED lamp in a controlled sequence when the temperature reaches the preset limit. The two red components on the right side of the LED controller (resistor and NTC) are configured according to method one described in the NTC operation section. The controller provides a precise voltage to the resistor element. The voltage at the NTC node is measured by the controller for conversion to the corresponding system temperature.
The alarm mechanism allows the LED light to indicate that the temperature has risen to the point where it must shut down for safety. The two red components (resistor and LED) on the left side of the LED controller are a basic indicator LED configuration. The brightness of the LED is controlled by a PWM (pulse width modulation) signal. The LED increases in brightness as the PWM duty cycle increases.
The above smart LED light displays the alarm information in the form of another LED indicator. LED alarm is just one of many communication interfaces that smart LEDs can use. Other interfaces include PLC (power line communication), DMX (digital multiplexing), and DALI (digital addressable lighting interface).
Lumen adjustment
The flowchart in Figure 4 shows a simple algorithm for monitoring the temperature of an LED light and adjusting the lumen level when the temperature reaches a certain safety limit. The "Power-on Startup - System Initialization" block at the top of the flowchart is the microcontroller initialization block. When the wall switch is turned on, the LED light is powered up and this block will configure the LED light for basic operations such as lumen output and temperature detection.
Figure 4: LED light monitoring and adjustment flowchart
The "Is the light on?" block detects whether the light is off due to excessive temperature. This simple bitwise test will determine whether the light is on. If set to the Light On position, the light is on, if not set to the Light On position, the light is not on. When power is first applied, the light is on by default and the Light On position is set.
The “Alarm” control block controls the on and off sequence after the temperature is too high and the LED light is turned off by the controller. The next “Is the light on?” block will start the test sequence again. The only way to exit the alarm condition is to remove and reapply power using the wall switch.
The next “Sense Temperature” block will sense the voltage at the NTC node. NTCs typically change non-linearly with temperature, so the sensed voltage can be compared to a lookup table for a relative temperature. This temperature is used in the next two control blocks.
The “Safe Temperature” block is used to determine if the temperature of the LED light is within a safe range. When the temperature reaches the configured maximum value, the system will turn the light off. If the temperature is below the maximum allowed, the system will continue the temperature stability test. The “
Light Off” block is used to turn the light off if the LED light temperature is within an unsafe range. Next is the “Is the light on?” block, which restarts the test sequence again.
The “Temperature Change” block is used to determine if the temperature change since the last lumen adjustment cycle requires an increase or decrease in light output. The "Temperature Increase" block is used to determine whether the temperature is rising or falling. Since the previous control block has already determined that the temperature has changed enough since the last lumen adjustment cycle, there are only two choices here.
The Max Lumens block determines if the LED light is set to maximum lumen output. If the lumen output is at the maximum, the Is Light On? block is re-entered to restart the test sequence.
When the previous control block detects that the lumen output is not at the maximum, the Lumens Increase, Indicator Dim block is triggered. This control block increases the output by one step as configured during the Initialization block, and also turns the indicator LED down by one step to match the increase in lumens with the dimming of the indicator, and then restarts the test sequence.
When the Temperature Increase block detects an increase in temperature, the Min Lumens block is triggered. If the lumens are not at the preset minimum value, the flow is directed to the Lumens Decrease, Indicator Brighten block. If the lumen output is at the preset minimum value, the Is Light On? block is re-entered to restart the test sequence. The Lumens Decrease,
Indicator Brighten block turns the output down by one step as configured during the Initialization block, and also turns the indicator LED up by one step to match the decrease in lumens with the increase in the indicator, and then restarts the test sequence.
The above flowchart shows the case where the LED light remains off during an input power cycle. With a slight change in the process, a sequence can be provided that monitors the temperature after the light is turned off and turns the LED light back on when the temperature drops to safe limits.
Keywords:LED
Reference address:Low power consumption design of heat dissipation management for LED lamps
In traditional incandescent bulbs, the only heat source is the filament, which is not in direct contact with anything. In LED lamps, however, the LED is the light source, and the heat dissipation of the LED is in direct contact with the LED bulb. This direct contact is due to the way the LED is connected to the driver circuit. In order to achieve heat dissipation, the heat must be removed from the LED and driver circuit or effectively managed, which is also the basic premise for the long-term operation of the LED lamp.
To understand the importance of thermal management, let's imagine an application where an LED lamp is installed in a general lighting socket such as a wall sconce or ceiling lamp, and the LED lamp is controlled by a wall switch. Since most standard lamps such as wall sconces or ceiling lamps rely mainly on heat convection or airflow to dissipate heat, the heat dissipation effect of this application is not ideal for LED lamps.
Without effective thermal management, the consequences can be disastrous, from frequent replacement of failed LED lamps to building fires. Using smart LED lamp control to monitor the temperature of the LED lamp is a simpler way to manage thermal management, and it also greatly improves safety because the LED lamp can reduce power when the temperature rises.
NTC Thermal Management
The basic principle of the NTC circuit is to improve the safety of the LED lamp and reduce the complexity of the design by monitoring the temperature of the LED lamp. When the temperature rises, the controller reduces the lumens to keep the LED within a safe level. In other words, when the temperature rises, the lumens are reduced, and when the temperature drops, the lumens are increased.
We can detect the temperature change of the LED lamp by sensing the voltage across the NTC. The sensed voltage is directly related to the temperature of the NTC, and the resistance of the NTC decreases as the temperature of the NTC and its surrounding circuits increases. There are two basic methods for determining temperature using the NTC.
Method 1: Use the NTC in a voltage divider circuit that forces a known voltage on the system and then measures the voltage at the NTC node. As the temperature of the NTC increases, the resistance decreases. The reduction in resistance will cause the voltage divider ratio to change. The voltage at the NTC node will also decrease as the temperature increases.
Method 2: Force a known current through the NTC and measure the voltage across the NTC. When the temperature of the NTC increases, the resistance decreases. According to Ohm's law, the decrease in resistance will change the voltage at the NTC node. If the resistance decreases and the current remains constant, the voltage at the NTC node will also decrease.
Both methods of monitoring the temperature of LED lamps are simple and straightforward to implement in terms of improved operation and safety. Figure 1 is a schematic diagram of the two methods using the LED as the source of the temperature increase.
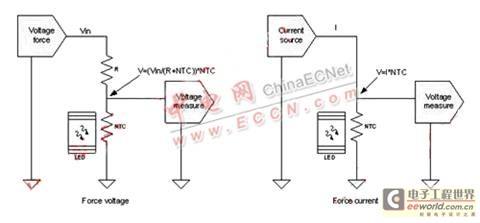
Figure 1: Two basic methods of determining temperature using NTC.
Too hot or LED failure?
When the lumen output of an LED lamp drops, it is important to know whether the LED output is dropping due to excessive temperature environment or due to LED failure. We can use an indicator that shows the lumen drop to determine the cause of the drop.
The lumen drop in the system shown in Figure 2 is indicated by a low-power red LED. When the system is at maximum lumen output, the red LED is off; when the temperature of the LED lamp increases, the lumen output decreases, and when the lumen output decreases, the red LED turns on. As the lumen output continues to decrease, the intensity of the red LED increases accordingly. When the lumen output drops to its minimum intensity, the red LED will turn on completely.
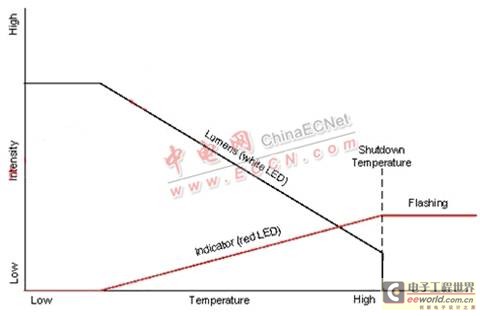
Figure 2
When lumen output is at minimum intensity and the temperature of the LED lamp is still high, the red LED indicator can also serve as an alarm to warn of serious problems. In alarm mode, the red LED will flash continuously while all white LEDs are off.
The block diagram of Figure 3 shows a general LED driver and LED controller with NTC and alarm indicators. The general LED lamp contains an LED driver that is configured to provide a set current through the LED. The driver cannot reduce lumens based on temperature. The temperature monitoring function provided by the driver is only used for its own protection and completely shuts down when the temperature is extremely high.
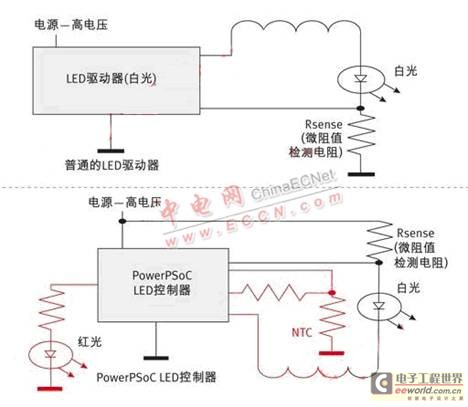
The LED controller has all the control functions of the general LED driver and can enhance the intelligence of other functions such as temperature monitoring, communication and dimming control. The blue part of the block diagram is the basic module and components of the LED controller. The components shown in red are not required for basic operation, but are shown for the NTC and alarm functions described in this article.
The addition of NTC to the general LED can shut down the LED lamp in a controlled sequence when the temperature reaches the preset limit. The two red components on the right side of the LED controller (resistor and NTC) are configured according to method one described in the NTC operation section. The controller provides a precise voltage to the resistor element. The voltage at the NTC node is measured by the controller for conversion to the corresponding system temperature.
The alarm mechanism allows the LED light to indicate that the temperature has risen to the point where it must shut down for safety. The two red components (resistor and LED) on the left side of the LED controller are a basic indicator LED configuration. The brightness of the LED is controlled by a PWM (pulse width modulation) signal. The LED increases in brightness as the PWM duty cycle increases.
The above smart LED light displays the alarm information in the form of another LED indicator. LED alarm is just one of many communication interfaces that smart LEDs can use. Other interfaces include PLC (power line communication), DMX (digital multiplexing), and DALI (digital addressable lighting interface).
Lumen adjustment
The flowchart in Figure 4 shows a simple algorithm for monitoring the temperature of an LED light and adjusting the lumen level when the temperature reaches a certain safety limit. The "Power-on Startup - System Initialization" block at the top of the flowchart is the microcontroller initialization block. When the wall switch is turned on, the LED light is powered up and this block will configure the LED light for basic operations such as lumen output and temperature detection.
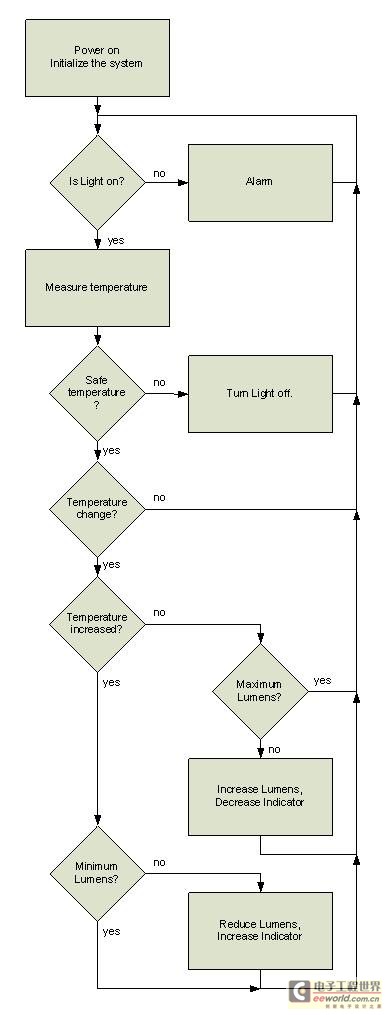
Figure 4: LED light monitoring and adjustment flowchart
The "Is the light on?" block detects whether the light is off due to excessive temperature. This simple bitwise test will determine whether the light is on. If set to the Light On position, the light is on, if not set to the Light On position, the light is not on. When power is first applied, the light is on by default and the Light On position is set.
The “Alarm” control block controls the on and off sequence after the temperature is too high and the LED light is turned off by the controller. The next “Is the light on?” block will start the test sequence again. The only way to exit the alarm condition is to remove and reapply power using the wall switch.
The next “Sense Temperature” block will sense the voltage at the NTC node. NTCs typically change non-linearly with temperature, so the sensed voltage can be compared to a lookup table for a relative temperature. This temperature is used in the next two control blocks.
The “Safe Temperature” block is used to determine if the temperature of the LED light is within a safe range. When the temperature reaches the configured maximum value, the system will turn the light off. If the temperature is below the maximum allowed, the system will continue the temperature stability test. The “
Light Off” block is used to turn the light off if the LED light temperature is within an unsafe range. Next is the “Is the light on?” block, which restarts the test sequence again.
The “Temperature Change” block is used to determine if the temperature change since the last lumen adjustment cycle requires an increase or decrease in light output. The "Temperature Increase" block is used to determine whether the temperature is rising or falling. Since the previous control block has already determined that the temperature has changed enough since the last lumen adjustment cycle, there are only two choices here.
The Max Lumens block determines if the LED light is set to maximum lumen output. If the lumen output is at the maximum, the Is Light On? block is re-entered to restart the test sequence.
When the previous control block detects that the lumen output is not at the maximum, the Lumens Increase, Indicator Dim block is triggered. This control block increases the output by one step as configured during the Initialization block, and also turns the indicator LED down by one step to match the increase in lumens with the dimming of the indicator, and then restarts the test sequence.
When the Temperature Increase block detects an increase in temperature, the Min Lumens block is triggered. If the lumens are not at the preset minimum value, the flow is directed to the Lumens Decrease, Indicator Brighten block. If the lumen output is at the preset minimum value, the Is Light On? block is re-entered to restart the test sequence. The Lumens Decrease,
Indicator Brighten block turns the output down by one step as configured during the Initialization block, and also turns the indicator LED up by one step to match the decrease in lumens with the increase in the indicator, and then restarts the test sequence.
The above flowchart shows the case where the LED light remains off during an input power cycle. With a slight change in the process, a sequence can be provided that monitors the temperature after the light is turned off and turns the LED light back on when the temperature drops to safe limits.
Previous article:Optimizing design to increase LED lamp life
Next article:Research on the brightness uniformity of LED backlight
Recommended ReadingLatest update time:2024-11-16 21:58
Design of LED dot matrix handwriting screen based on PIC16F877A single chip microcomputer
This paper uses PIC16F877A microcontroller as the main core control element to design a 32×32 LED dot matrix module writing display screen. It is mainly composed of a light pen module and a dot matrix display module. The light pen module uses the photoelectric characteristics of the photoresistor to realize the micr
[Microcontroller]
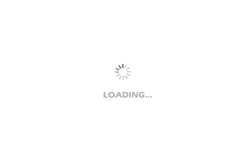
Design of Fully Automatic Washing Machine Based on 51 Single Chip Microcomputer
1. Hardware Solution The block diagram of the fully automatic washing machine is shown in Figure 1. It mainly consists of a power supply, a single-chip minimum system, a switch detection circuit, a control button input circuit, an LED indication circuit, a relay and a motor circuit. As shown in the figure: 2. Design
[Microcontroller]
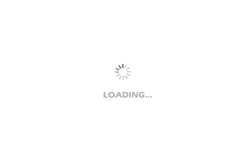
Analysis of the impact of QR code application on LED display screen
Since the emergence of mobile phone QR codes in 2002, QR codes have been used more and more widely in our lives, especially in the past two years. Because QR codes are very convenient to generate, they have become a popular medium for identity recognition and information transmission.
Scan the QR code at the
[Security Electronics]
If the five major technical difficulties of LED lamps are not overcome, MOS tubes will keep burning
1. Chip heating
This content is mainly for high-voltage driver chips with built-in power modulators. If the current consumed by the chip is 2mA, and a voltage of 300V is applied to the chip, the power consumption of the chip is 0.6W, which will of course cause the chip to heat up. The maximum current of the driv
[Power Management]
LED driver technology to improve TV backlight energy efficiency
Television, which is recognized by the world as one of the most important inventions of the 20th century, is an indispensable tool for people to exchange information. As television becomes more popular, consumers' demand for data traffic increases and application services change rapidly. Limiting the maximum power con
[Power Management]
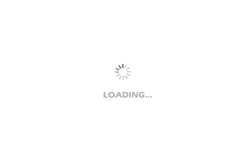
Regulating LED Current Using an Inverting Buck-Boost Topology
若需控制LED 亮度,就必须具备能够提供恒定、稳压电流的驱动器。而要达到此目标,驱动器拓朴必须能产生足够的输出电压来顺向偏置LED。那麽当输入和输出电压范围重叠时,设计人员又该如何选择呢?转换器有时可能需要逐渐降低输入电压,但有时也可能需要升高输出电压。以上情况通常出现在那些具有大范围"脏" (dirty) 输入功率来源的应用中,例如车载系统。在这种降压/升压的操作中,几种拓朴可以达到较好的效果,像是SEPIC 或四次切换升降压拓朴。这些拓朴一般需要大量的元件,设计的材料成本也因而增加。但由於它们可提供正输出电压,因此设计人员通常视其为可接受的方案。不过负输出电压转换器也是另一种不该被忽略的替代解决方案。
图1
[Power Management]
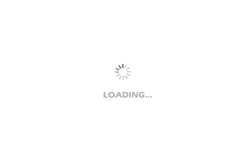
Audio level meter circuit composed of 9 LEDs
5 LED VU Meter kit is based on LB1409 IC from SANYO, which will indicates the volume level of the audio signal it senses
SUPPLY 12V DC @ 50mA
PR1 REF SET
PR2 AUDIO LEVEL SET
Schematic
.
Parts List
[Analog Electronics]
Case study of using fine-particle phosphor as diffusion powder in high-power LED packaging
Characteristics of
high-power LED
packaging
High-power LED packaging has been a research hotspot in recent years
due to its complex structure and process, and directly affects
the performance and life of
LED
. In particular, high-
power
white light LED
packaging is a hotspot among resea
[Power Management]
- Popular Resources
- Popular amplifiers
Recommended Content
Latest Power Management Articles
- MathWorks and NXP Collaborate to Launch Model-Based Design Toolbox for Battery Management Systems
- STMicroelectronics' advanced galvanically isolated gate driver STGAP3S provides flexible protection for IGBTs and SiC MOSFETs
- New diaphragm-free solid-state lithium battery technology is launched: the distance between the positive and negative electrodes is less than 0.000001 meters
- [“Source” Observe the Autumn Series] Application and testing of the next generation of semiconductor gallium oxide device photodetectors
- 采用自主设计封装,绝缘电阻显著提高!ROHM开发出更高电压xEV系统的SiC肖特基势垒二极管
- Will GaN replace SiC? PI's disruptive 1700V InnoMux2 is here to demonstrate
- From Isolation to the Third and a Half Generation: Understanding Naxinwei's Gate Driver IC in One Article
- The appeal of 48 V technology: importance, benefits and key factors in system-level applications
- Important breakthrough in recycling of used lithium-ion batteries
MoreSelected Circuit Diagrams
MorePopular Articles
- Innolux's intelligent steer-by-wire solution makes cars smarter and safer
- 8051 MCU - Parity Check
- How to efficiently balance the sensitivity of tactile sensing interfaces
- What should I do if the servo motor shakes? What causes the servo motor to shake quickly?
- 【Brushless Motor】Analysis of three-phase BLDC motor and sharing of two popular development boards
- Midea Industrial Technology's subsidiaries Clou Electronics and Hekang New Energy jointly appeared at the Munich Battery Energy Storage Exhibition and Solar Energy Exhibition
- Guoxin Sichen | Application of ferroelectric memory PB85RS2MC in power battery management, with a capacity of 2M
- Analysis of common faults of frequency converter
- In a head-on competition with Qualcomm, what kind of cockpit products has Intel come up with?
- Dalian Rongke's all-vanadium liquid flow battery energy storage equipment industrialization project has entered the sprint stage before production
MoreDaily News
- Allegro MicroSystems Introduces Advanced Magnetic and Inductive Position Sensing Solutions at Electronica 2024
- Car key in the left hand, liveness detection radar in the right hand, UWB is imperative for cars!
- After a decade of rapid development, domestic CIS has entered the market
- Aegis Dagger Battery + Thor EM-i Super Hybrid, Geely New Energy has thrown out two "king bombs"
- A brief discussion on functional safety - fault, error, and failure
- In the smart car 2.0 cycle, these core industry chains are facing major opportunities!
- The United States and Japan are developing new batteries. CATL faces challenges? How should China's new energy battery industry respond?
- Murata launches high-precision 6-axis inertial sensor for automobiles
- Ford patents pre-charge alarm to help save costs and respond to emergencies
- New real-time microcontroller system from Texas Instruments enables smarter processing in automotive and industrial applications
Guess you like
- Solution to CCS8.1.0 not finding .h files
- Analysis of the characteristics, advantages and potential applications of 60GHz wireless technology
- Looking for the design of station signal simulation control system
- EEWorld invites you to attend the 2019 STM32 Summit and Fan Carnival!
- Partial code implementation of stm32 MCU bare metal calling Baidu speech recognition interface and synthesis interface
- Switching Power Supply Interest Group 16th Task
- A brief introduction to the internal structure of photoelectric sensors
- Geek Black Technology, Shopping Carnival | Here are the deals you can’t miss!
- I need help from an expert. "When designing a microcontroller hardware circuit using STC89C51, should I design the EEPROM circuit part?"
- Claiming that software is open source when it is not is false advertising