Lighting designers are promoting light-emitting diode (LED) lighting because of the potential benefits that incandescent, halogen, fluorescent and gas/arc lamps lack. Although the business opportunities for LED lighting systems are huge, what really makes lighting designers excited is the basic design of solid-state lighting.
To be successful in LED lighting design, you must pay close attention to three factors: electronic drive, thermal management, and optical efficiency. Only by successfully balancing these three factors can you enjoy the advantages of solid-state lighting, such as long life, high electronic efficiency, high brightness, and pure color (or strictly controlled color temperature for white LEDs). This article will provide designers with a valuable reference on how to select high-power LEDs (1 watt and above) and design circuit drivers.
LED series configuration can achieve ideal lighting standards
LED dies used for solid-state lighting are generally made of semiconductor materials. Red, orange, and amber LEDs are almost all made of InAlGaP, green and blue LEDs are mostly made of InGaN, and white LEDs use blue LEDs with conversion phosphors, which are the same as blue LEDs from the perspective of electronic driving. Like standard PN junction diodes, LEDs begin to conduct current when they are forward biased, but unlike standard PN junction diodes, LEDs in forward bias emit light. The two characteristics of LEDs, driven by current (LEDs) and extremely low DC forward voltage through LEDs, make LEDs different from other light sources. The typical forward voltage VF of InAlGaP LEDs is 2 to 3 volts, while the forward voltage of InGaN LEDs is 3 to 4 volts, but the luminous flux of LEDs is proportional to the forward current IF. The first problem in electronic driver design is to fix the drive current, and the second problem is to determine the voltage range for each LED. A careful look at the manufacturer's product data sheet will find the recommended drive current and the standard, minimum and maximum values of VF, dominant wavelength and luminous flux under the corresponding current conditions. Note that the current is an independent quantity in the typical VF vs. IF comparison chart (Figure 1), indicating that current control is the key to the LED driver.
Figure 1 Comparison of VF and IF of red InAlGap LED and white InGaN LED
Although high-power LEDs have made significant progress in recent years, a single device is still not enough to meet general lighting needs. The flagship product produced by the industry, a 1-watt white LED (standard color temperature 6,500K), can produce a luminous flux of 100 lumens. However, compared with a typical 60-watt incandescent bulb, the LED lighting angle is relatively narrow. The typical luminous efficacy of an incandescent bulb is 15lm/W, which can produce 900 lumens of light, which is almost evenly distributed in all directions. If the goal is to illuminate a space that was previously equipped with incandescent bulbs, multiple LEDs are required. Connecting LEDs in series ensures that the current flowing through each device is equal and ensures that each component emits uniform light. In short, connect as many LEDs in series as possible, and then further add series circuits until the total light output reaches the desired standard. The number of LEDs that can be configured in series depends on several factors, but is mainly determined by the input voltage, electronic specifications and safety standards, and the LED driver. Figures 2, 3, and 4 show three methods of driving a lighting system composed of nine 1-watt LEDs.
The advantage of the LED configuration is that a single LED driver can be used (Figure 2) and the current flowing through each LED is guaranteed to be equal. The disadvantage is that it will result in the highest output voltage, which requires larger and more expensive circuit components and safety requirements. In addition, if any of the LEDs has an "open circuit" problem, all LEDs will not emit light.
Figure 2 Nine LEDs in a single serial circuit
The LED configuration shown in Figure 3 has the advantages of lower output voltage and reduced risk of electric shock. If one LED fails, the other two branches will continue to operate, which has both advantages and disadvantages. On the one hand, the failure of one LED will not cause the entire lamp to turn off. On the other hand, the LED driver, as a current source, must now apply more current (1.5×IF) to the other branches. This will cause the LED to overheat and shorten its service life. The second disadvantage of the series-parallel array is that the LEDs will not share the drive current equally unless their VFs match. This requires LED manufacturers to batch their products, thereby increasing costs. Even if VF batching is performed, the negative temperature coefficient of VF in the LED will cause current imbalance between branches if equal heat dissipation is not provided for each LED during design.
Figure 3 Nine LEDs in a 3x3 series-parallel array
Figure 4 illustrates a conservative approach that provides maximum system stability, but this approach is the most expensive and takes up the most space. Using separate drivers keeps the output voltage low, eliminating the need for VF binning, and the lamp can maintain some light output even if two LEDs in two different branches fail. If the LED drivers were switching regulators, the cost and space occupied by three drivers (and the surrounding passive components) would be too high.
Figure 4 Nine LEDs driven by three drivers
Current control is the key to LED drivers
Under no circumstances should a single LED be connected directly to 110 or 220 volt alternating current (AC); this would only provide a momentary brilliance and be dangerous. DC power comes in many forms, including batteries, solar cells, and fuel cells, but for general lighting, AC line voltage is the most common input voltage. The circuitry of an LED lighting system must be able to input a higher AC voltage and output a lower voltage DC current. In different countries, electronic regulations vary for wet, dry, enclosed, or open environments. In general, there are few applications that allow output voltages above 60 volts DC. Research into using LEDs for general lighting is just beginning, and standards and regulations are still vague and subject to change, but a safe option is to generate an intermediate DC bus voltage from an existing offline power supply that has electrical isolation and power factor correction and meets appropriate safety regulations. Output voltages are generally 12 volts, 24 volts, and 48 volts. In the past three or four years, various DC-DC converter ICs have been introduced to the market that can feed a universal DC voltage and output a constant current to the LEDs in series.
DC-DC converters can accurately drive LEDs
Some manufacturers offer complete AC input, DC current output driver modules that meet the insulation and power factor correction (PFC) requirements, but are limited in the number and type of LEDs they can drive. DC-DC converters can accurately drive LEDs because their output current is constant, meeting the needs of the LEDs. To achieve the flexibility required for different LED configurations, solid-state lighting designers must know which DC-DC converter ICs can be used and how to choose the component that best suits the application.
First, the IC must be able to handle the selected input voltage and output the required current over a wide range of output voltages. For a system consisting of n LEDs in series, the total output voltage required is: VO = nx VF + VSNS. In this sequence, "VSNS" represents the voltage drop across a series current sensing component (usually a resistor).
For systems where VIN-MIN is greater than VO-MAX, a buck regulator can be used. Buck regulators are the preferred choice for switching converter-based LED drivers because of their simple structure, low component count, suitability for constant current output, and wide selection of control ICs. For systems where VO-MIN is greater than VIN-MAX, a boost regulator should be used. Although boost regulators are less suitable for LED driving, they use a separate sensor and two power switches. Like buck regulators, they are highly efficient and are a good second choice to buck regulators in terms of the choice of control IC.
Finally, if the ranges of VIN and VO overlap, a buck-boost regulator is needed. This type of regulator should be the last resort for electronic driver designs, but the input voltage range and tolerance combined with the VF tolerance of the LEDs due to process and temperature often forces lighting designers to make this difficult choice. Buck-boost regulators tend to use more components, are not as efficient, and are more difficult to design than either buck or boost regulators.
In addition, buck regulators and boost regulators each use a basic topology, while buck-boost regulators use single inductor inverting topology, SEPIC topology, Cuk topology, and flyback topology (coupled inductor). Examples of topology selection are as follows:
‧ Using a buck regulator Take
a small LED lamp using six white (InGaN) LEDs as an example. The drive current is 1 amp ± 10%, which is the standard current for 3 watt LEDs. All six LEDs will be configured in series, and after checking the LED data sheet, the following forward voltage data is obtained: VF-MIN=3.0V, VF-TYP=3.7V, VF-MAX= 5.0V.
The LEDs can be batched to reduce the range of VF, but this will increase the cost, especially if the LEDs used are already batched according to luminous flux and/or color temperature. If the entire VF range is used, the output voltage can range from 18 to 30 volts. Such lamps can be sold worldwide and must operate within the universal AC input voltage range of 85 to 265 volts AC. If a standard isolated line power supply is purchased, it will provide an intermediate bus voltage (Intermediate Bus Voltage) VBUS. What is needed here is an offline power supply with a standard output voltage because it has the widest range of products to choose from and the lowest cost. Therefore, the optional VBUS is 12 volts, 24 volts or 48 volts, and each voltage has a ±5% error. 48 volts is the most ideal choice because it will provide the most efficient but lowest price LED drive topology - buck driver.
In addition, offline conversion will be more efficient than 12 volts or 24 volts, because when the AC voltage is stepped down to 48 volts, the output current will be lower and the conversion rate will be slower. Figure 5 shows an example of a buck LED driver.
Figure 5 Buck LED driver
‧ Using a boost regulator
Boost regulators are more common in portable applications, battery input applications. Both inductive boost regulators and switched capacitor boost regulators have achieved great success in driving small LED backlight displays, but this application is a portable lighting lamp for applications such as bicycle lighting or military/police flashlights. It is emitted by only three 1-watt white LEDs, which are driven by 350 mA ± 10%. As in the example above, the product datasheet specifies the following forward voltage limits: VF-MIN = 3.0V, VF-TYP = 3.7V, VF-MAX = 5.0V. The
input voltage of this lamp is three 1.5-volt AA batteries, each of which operates at 1.5 volts when fully charged, and the operating voltage drops to 0.9 volts when fully discharged. All three batteries can be configured in parallel, but this will result in a very limited voltage available for the driver IC to operate; therefore, the three batteries need to be changed to a series configuration here. The VIN range is 2.7 to 4.5 volts, and VO-MIN is 9 volts, making the inductive boost regulator very suitable. The following is an example circuit (Figure 6).
Figure 6 Boost LED driver
‧ Use Buck-Boost Regulators
Automotive electronics present special challenges for LED driver electronics due to their wide voltage range, yet automobiles were one of the earliest applications to adopt high-power LEDs due to the reliability, lifespan, and luminous efficiency of LEDs. Taillights, turn signals, and interior lighting systems were early converts to solid-state lighting systems, but headlights (low beam, high beam, fog lights, etc.) proved difficult to use LED lighting due to the number of LEDs required to obtain luminous flux. This problem is caused by the fact that all LEDs lose light output as the temperature of the die increases. In order to solve the problem of obtaining extremely high luminous flux (over 1,000 lumens) from a very small area, in addition to LED manufacturers, several companies purchased bare die and specialized in packaging to produce multi-die LED modules. This product combines eighteen dies in six series-connected and three parallel strings of LEDs. The total drive current is 1 amp, and the VF ranges from 18 to 24 volts. The standard automotive battery and alternator system operates from 9 to 16 volts, but often includes a “double battery” test that requires the system electronics to operate (or at least maintain) 28 volts for two minutes or more. “Load dump” surges (caused by disconnecting the battery while the alternator is running) can exceed 100 volts, but are usually fixed at about 40 volts. This wide input voltage range forces the driver to both step down and step up. A single inductor buck-boost driver (Figure 7) requires fewer components than a SEPIC, Cuk, or four-switch buck-boost driver. However, its disadvantage is that the output current is controlled based on VIN, requiring a floating, differential current sense to complete the control loop. The above current sensing requirements can be achieved with the low-cost dual PNP transistors in Figure 7, but higher accuracy and performance can be achieved by using an IC current sense amplifier instead.
Figure 7 Buck-boost driver
Driver characteristics are key to controlling/sensing output current
Almost any DC-DC converter IC with an adjustable output voltage can be turned into a current regulator for driving LEDs, but this solution is not ideal. A dedicated high-power LED driver should have some features that other DC-DC converters do not have, the main key being whether the output current can be accurately and effectively sensed and controlled. Whether the resistor is internal or external to the IC, the current sense voltage VSNS must be low to minimize the power dissipation in the current sense resistor. However, VSNS cannot be so low that the signal-to-noise ratio (SNR) is affected; its special advantage is that such IC design allows the user to adjust VSNS to be proportional to the control voltage, giving the user the flexibility to compromise between efficiency and SNR and still operate like a linear current regulator.
The brightness of LEDs is adjusted by pulse width modulation (PWM) to maintain a stable and consistent light source or a stable color temperature. When the pulse exceeds a certain frequency (usually 200Hz), the human eye cannot distinguish individual pulses. By keeping the LED current at a certain level and adjusting the pulse width at the same time, the average intensity of the perceived light will change relatively. The LED driver IC should accept a logic-level PWM signal and be able to act like a high-fidelity bi-level amplifier, applying pulses to the LED with a control current that matches the logic signal. In order to maintain the correctness of the output current to the PWM signal, the propagation delay must be minimized, and the conversion rate of the LED current rise and fall must be maximized. There is no need to use the enable/shutdown pins of most standard power control ICs, which usually cause a large delay to minimize the shutdown current and intentionally limit the conversion rate for tracking, slow start and sequencing.
LED drivers based on buck converters should be able to operate without output capacitors, because this transforms the output voltages into high impedances and makes them most closely matched to ideal current sources with infinite impedance. Without output capacitors, the output voltages can switch quickly, which is necessary for fast PWM dimming. Buck converters without output capacitors can be connected to a parallel dimming field-effect transistor (FET) (Figure 8). This dimming method reduces propagation delays and switching speeds by at least one order, because maintaining continuous inductor current eliminates the largest system delays. The disadvantage is that some power is consumed when the LEDs are off, but the output voltage can drop to a level equal to VSNS, minimizing the power loss; importantly, the buck regulator is the only switching regulator topology with a parallel dimming FET.
Figure 8 Buck LED driver with parallel FET dimming
LED drivers are often exposed to extreme ambient temperatures, which are even extreme for power ICs. The high cost of heat sinks and the cramped space of LEDs translate into severe heat dissipation problems. Therefore, it is necessary to set the operating temperature rating to at least 125°C and use high-power packages. High-power LEDs are usually mounted on metal core printed circuit boards (MCPCBs), which consist of an aluminum substrate with dielectric and copper conductors for electronic connections. The best (lowest) thermal resistance is achieved when the driver in a thermal gain package is also mounted on the MCPCB. Examples of thermal gain packages include lead-free lead frame packages (with a heat sink in the center) and footprint-compatible versions of pin-type packages (such as SOIC-8 and TSSOP-14) with a heat sink on the bottom. Due to the extremely high cost of aluminum substrates, driver electronics are usually not mounted on MCPCBs. In most applications, LED drivers must overcome the problems of high temperature environments and reduced heat dissipation performance of standard FR4 PCBs.
When LEDs are driven directly from a switching regulator, the most concerning fault is an open output. Some LED drivers often have current limiting, but when the output current is controlled in a regulated state, the biggest concern is the situation where one of the LEDs opens. This is the most common fault of LEDs, which causes the feedback path to be disconnected, and the result is a large increase in output voltage regardless of the control type. Buck regulators also have a safety issue in that VO can only rise as high as VIN. Because their output voltage will rise, boost and buck-boost LED drivers must take precautions until one or more circuit components fail. Just as regulators reset, hibernate, or latch-off when they encounter an output short, LED drivers, especially boost or buck-boost types, should provide automatic protection when an output opens. As shown in Figure 7, a Zener diode can be used to keep the output voltage within a certain range. The Zener breakdown voltage value should be set above the maximum VO of the regulator, and the reverse current should be set to 1 mA to minimize power dissipation in the event of a prolonged fault condition.
Previous article:PI's flicker-free dimming LED driver IC solution
Next article:Decomposition of the installation method of LED advertising display
Recommended ReadingLatest update time:2024-11-16 16:40
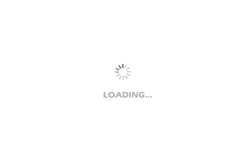
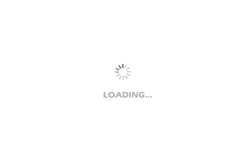
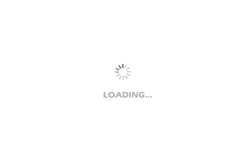
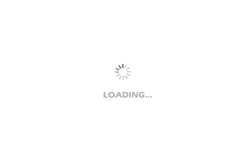
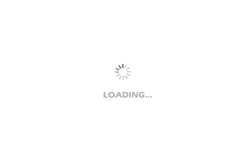
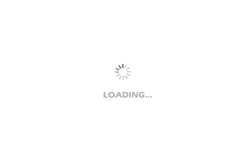
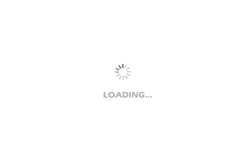
- Popular Resources
- Popular amplifiers
-
MCU C language programming and Proteus simulation technology (Xu Aijun)
-
100 Examples of Microcontroller C Language Applications (with CD-ROM, 3rd Edition) (Wang Huiliang, Wang Dongfeng, Dong Guanqiang)
-
Research on three-phase all-solid-state high-efficiency LED tunnel lighting system based on chip drive_Li Jian
-
Follow me Season 2 Episode 1 All Code + Library
- MathWorks and NXP Collaborate to Launch Model-Based Design Toolbox for Battery Management Systems
- STMicroelectronics' advanced galvanically isolated gate driver STGAP3S provides flexible protection for IGBTs and SiC MOSFETs
- New diaphragm-free solid-state lithium battery technology is launched: the distance between the positive and negative electrodes is less than 0.000001 meters
- [“Source” Observe the Autumn Series] Application and testing of the next generation of semiconductor gallium oxide device photodetectors
- 采用自主设计封装,绝缘电阻显著提高!ROHM开发出更高电压xEV系统的SiC肖特基势垒二极管
- Will GaN replace SiC? PI's disruptive 1700V InnoMux2 is here to demonstrate
- From Isolation to the Third and a Half Generation: Understanding Naxinwei's Gate Driver IC in One Article
- The appeal of 48 V technology: importance, benefits and key factors in system-level applications
- Important breakthrough in recycling of used lithium-ion batteries
- Innolux's intelligent steer-by-wire solution makes cars smarter and safer
- 8051 MCU - Parity Check
- How to efficiently balance the sensitivity of tactile sensing interfaces
- What should I do if the servo motor shakes? What causes the servo motor to shake quickly?
- 【Brushless Motor】Analysis of three-phase BLDC motor and sharing of two popular development boards
- Midea Industrial Technology's subsidiaries Clou Electronics and Hekang New Energy jointly appeared at the Munich Battery Energy Storage Exhibition and Solar Energy Exhibition
- Guoxin Sichen | Application of ferroelectric memory PB85RS2MC in power battery management, with a capacity of 2M
- Analysis of common faults of frequency converter
- In a head-on competition with Qualcomm, what kind of cockpit products has Intel come up with?
- Dalian Rongke's all-vanadium liquid flow battery energy storage equipment industrialization project has entered the sprint stage before production
- Allegro MicroSystems Introduces Advanced Magnetic and Inductive Position Sensing Solutions at Electronica 2024
- Car key in the left hand, liveness detection radar in the right hand, UWB is imperative for cars!
- After a decade of rapid development, domestic CIS has entered the market
- Aegis Dagger Battery + Thor EM-i Super Hybrid, Geely New Energy has thrown out two "king bombs"
- A brief discussion on functional safety - fault, error, and failure
- In the smart car 2.0 cycle, these core industry chains are facing major opportunities!
- The United States and Japan are developing new batteries. CATL faces challenges? How should China's new energy battery industry respond?
- Murata launches high-precision 6-axis inertial sensor for automobiles
- Ford patents pre-charge alarm to help save costs and respond to emergencies
- New real-time microcontroller system from Texas Instruments enables smarter processing in automotive and industrial applications
- What should I do if MP1584EN often burns the chip?
- Ultrasonic water and gas meter design challenges and solutions
- Increase the frequency range of the RC voltage-controlled oscillator
- How do you guys choose whether to use a 4-layer board or a 2-layer board?
- Thank you for being there + thank you for your wife's protection
- The electrical engineer blew up the company because of a resignation dispute...
- Free sharing of analog high-definition AHD and TVI and CVI to HDMI and VGA and CVBS solution schematics
- Sharing joy with others is worse than enjoying it alone——TI training’s “recommended courses” function is now available for public testing. We invite you to make suggestions and participate in the competition!
- [Anxinke NB-IoT Development Board EC-01F-Kit] 1. Unboxing and Hardware Appreciation
- Seeking advice from hardware experts: PWM control transistor buck-boost output waveform