The rapid rise of LED lighting
applications is expected to expand the demand for high-
power
LED
products. To ensure that high-power LEDs can meet market requirements, packaging companies are trying to achieve high cost-effectiveness and extended service life by improving packaging materials, die configuration, etc.
High-power light-emitting diode (LED) light sources often published by the industry are mostly
LED packaging
technologies with tens of watts or even hundreds of watts. From the perspective of optical system applications, it is not very meaningful. Instead, how to eliminate tens to hundreds of watts of heat is the key. To achieve this goal, it is necessary to effectively reduce the thermal resistance (Rjc) of a single LED package.
The power
driven
by the LED package
is limited by the thermal resistance of the package body and the matching heat dissipation module (Rca), which determine the system thermal resistance of the LED and the maximum power value that can be tolerated in a steady state. In order to reduce the thermal resistance of the package, the industry has tried to increase the distribution distance of the LED die in the package body, but the distribution area of the LED die should not be too large. Too large a light-emitting area will make subsequent
optical
processing difficult and limit the application of the product. It is not possible to simply package more LED chips in a single body to achieve high-power packaging, because there are still many factors to be considered, especially for the application.
Multi-chip
packaging materials continue to develop
As the power of LED packaging increases, multi-chip packaging has become a trend. Traditional high-power LED packaging mostly uses a pre-mold lead frame (Pre-mold Lead Frame) of plastic injection (Figure 1a). The packaging carrier (Carrier), also known as the die pad, is a continuous metal block that can no longer meet the electrical requirements of multi-chip series connection. The electrical series-parallel connection method directly affects the precision of the LED chip electrical measurement bin, the reliability life, and the drive circuit design required for the package body when it is used. Therefore, many LED packaging types have been proposed one after another. Figure 2 gives several representative examples of high-power LED packaging.
Figure 1 Schematic diagram of common high-power LED packaging structure
Figure 2 Typical high-power LED package
The main differences of the high-power LED packaging structures widely used in the industry can be roughly distinguished by the material selection of the packaging carrier. The implementation methods are nothing more than using a high thermal conductivity ceramic substrate or directly planting the die on a metal substrate (Figure 1b), which becomes a chip on board (COB) packaging form. However, because the price of high thermal conductivity ceramic substrates remains high, there is another economical option, which is to use low thermal conductivity laminated ceramics with a thermal via design (Figure 1c), and add sintered metal (such as silver) into the thermal via as a heat conduction path; in addition, there is another advanced method, which is to use semiconductor process silicon materials as carriers (Figure 1d) to achieve thermal and electrical separation, while having high power density and low thermal resistance (<0.5℃/W) characteristics, which is expected to usher in another revolution in high-power LED packaging. With the upgrade of LED power and power density, LED will gradually replace traditional light sources in various application fields.
Primary Optical
Lens
The selection of packaging materials is crucial
High temperature resistant and stable encapsulation has been widely used. The choice between different silicone substrates, in addition to processability, mainly depends on the consideration of refractive index, which will affect the optical properties of the package, including beam distribution and
light output efficiency
. In order to maintain stable and consistent optical quality, it is necessary to give the primary optical lens (Primary Lens). A good lens design can provide better light output quality, such as more uniform light intensity, color coordinate distribution, etc., which has an absolute impact on the effective light output of LEDs. The design of
primary optical lenses is different for each company. Generally, a large light output angle (≧120o) is used in the first-order light output, and then the required light shape is adjusted through subsequent second-order optical processing. Another benefit of a large light output angle is that it is conducive to extracting light and presenting a better luminous efficiency value.
The selection of primary optical materials is a key point. In the past, due to the bottleneck of optical molding materials, most of them were mainly optical polycarbonate (PC) or optical acrylic (PMMA) materials (low-end products even use epoxy resin). At this stage, due to the breakthroughs in the properties of silicone materials, they are gradually used in primary optical lenses. However, because the silicone material is a viscoelastic and non-hard structure, the optical accuracy will be affected by the difference in the degree of shrinkage of the cross-linking reaction. At the same time, because silicone easily absorbs moisture, in a high humidity environment, silicone lenses may expand due to moisture absorption, causing the originally designed light distribution to change. Silicone materials are used in high-power LED packaging and are in the promotion stage. As for the selection of optical lens materials, there is another feasible way. For those who need more refined optical quality and high reliability, stable glass lenses can be selected to meet the strict test of long life and allow harsh use environments.
The primary issue is to effectively reduce the thermal resistance value. When
LED packaging is pushed to high power, the first challenge is heat. Thermal effect has always been a major accelerating factor for the degradation of various material properties. How to control the junction temperature has become the main factor determining the power value of LED packaging. At present,
the mainstream mechanism for generating white light
in solid-state lighting
is still visible
blue light
(450-470 nanometers) through phosphor (Phosphor) to stimulate the yellow spectrum to mix and produce white light in human vision.
The blue light chip technology available on the market has reached a certain level. The chip itself has a high tolerance to thermal shock (the luminous efficiency declines by less than 1% for every 10℃ increase in temperature). However, the effect of heat on all types of fluorescent materials is relatively sensitive. The light conversion efficiency of fluorescent materials decreases with the increase in temperature (Figure 3), and it also affects the life of fluorescent materials. In particular, when the temperature of fluorescent materials exceeds 70℃, they will decline rapidly. This means that the junction temperature (Tj) of the LED must be effectively controlled below 70℃ to effectively ensure the usable life of the LED (generally, the life is calculated by L70, the time it takes for the LED to decline to 70% of its original
brightness
). This is used as the basis for judging the life, and this requirement is generally more than 20,000 hours. Therefore, when discussing the maximum power and efficiency of LEDs, it is meaningful to consider the results when they reach thermal stability under normal operating conditions. The thermal resistance of the LED package itself determines the maximum power that the package can withstand. How to effectively reduce the Rjc value is a major challenge that high-power LED packages must face.
Figure 3: Changes in light conversion efficiency of fluorescent materials with temperature
Cost, electrical properties, and reliability are the three major evaluation criteria for package die configuration.
The operating current density of LED die has an upper limit (taking a 40×40 mil chip area as an example, depending on the chip level, the drive current ranges from 350 to 1,000 mA. However, the most direct way to increase LED power is to increase the total die area in the LED package. The methods are nothing more than increasing the die size or increasing the number of die (using multi-crystal packaging). Each has its own advantages and disadvantages. It can be evaluated from the perspectives of die cost, electrical properties, and reliability life:
‧ Cost considerations
Taking a large-size 80-mil die as an example, its area is equivalent to four 40-mil die. However, in terms of die price, the cost of an 80-mil die must be higher than the cost of four 40-mil die due to yield factors.
‧ Electrical connection
method From an electrical point of view, an 80-mil die is equivalent to connecting four 40-mil dies in parallel (Figure 4a). If four 40-mil dies are used, they can be connected in series through wire bonding (Figure 4b). The difference between series and parallel connection can be reflected in performance. It is understood that the forward voltage (Forward Voltage, Vf) of each LED die
is
different. In other words, the internal resistance value of each die unit is different. When four dies are driven in parallel, there will be a problem of uneven current distribution. The die with a larger current distribution has a higher light conversion efficiency and also accelerates the aging of the die. The die with insufficient current distribution cannot release enough light energy, resulting in the overall luminous efficiency being lower than expected.
Figure 4 Schematic diagram of electrical connections corresponding to different die sizes under the same die area condition
‧ Reliability life
Due to the uneven current distribution of large grains, the area with high current density accelerates aging. The result of LED aging is a decrease in resistance, which leads to an increasing current density in the area, forming a so-called hot spot. The vicious cycle will accelerate the LED decay. Therefore, under the same current density operation, the reliability life of large grains is shorter than that of small grains.
In general, it is more advantageous to use series connection, but large-sized grains have other advantages. In terms of optical processing, large-sized grains are closer to point light sources than multiple small-sized grains, and are easier to handle. The trade-off between large and small grain sizes depends on the application field. In actual operation, the feasibility of the packaging process and
the compatibility of
the LED driver circuit
components must still be considered.
Integration of common platforms helps reduce development costs
Looking back to 2001, Lumiled Luxeon first launched a 1-watt high-power LED, which was very popular. The package at that time was a classic design. Many peripheral manufacturers launched peripheral parts that matched Luxeon, including secondary optics, heat dissipation substrates, thermal modules, drive circuits, etc. Luxeon packaging does not need to worry about optical modules, and various drive circuits are available, which greatly shortens the product development schedule. In contrast, at this stage, each manufacturer has its own unique specifications for high-power LED packaging, and there are no common parts that can be used interchangeably. Even Lumiled (now merged into
Philips
), which was very popular at the time, broke the traditional design tradition, making the original peripheral component manufacturers at a loss. Without the development of an integrated common platform, the expected result is that each manufacturer develops its own high-power LED package specifications, making it more difficult for downstream system application manufacturers to use it. Unless a single LED supply source is locked, if two or three supply sources are desired at the same time, multiple development costs must be invested in the same product. The inability to realize a universal platform can be expected to end in a situation where the strong prey on the weak, rather than sharing the sweet fruits.
The challenges
of color rendering
, color uniformity, and price are getting bigger and bigger.
White light LEDs
have made great
progress in recent years. The energy-saving benefits of high-power LEDs replacing traditional light sources have been proven. In early 2008, the white light LED packages that can be mass-produced have exceeded the 70
lumens
per watt
level, surpassing the most popular energy-saving bulbs (tubes) for traditional general lighting. It can be predicted that in the next year, commercial white light LEDs with more than 100 lumens per watt will be available. While blindly pursuing high luminous efficiency, the LED industry is also expected to improve optical quality, including:
‧ Pursuit of color rendering For
light sources used in indoor lighting, people emphasize the color rendering of the light source, with the aim of making the illuminated object present a more natural color. How to improve color rendering (CRI>80) depends on the cooperation of chip manufacturers and fluorescent material manufacturers to make the excitation spectrum wider and closer to natural light sources.
‧ Improve light color uniformity
The color uniformity of light projected by many LEDs is not ideal, and the problem of yellow ring on the periphery is often seen (
the color temperature
of light near the outer ring
is lower than that of the central area). Even internationally renowned LED packaging manufacturers have difficulty solving this problem. This requires parallel processing from the aspects of packaging structure, optical design and phosphor coating process technology.
‧ Price popularization
The largest market for high-power LED packaging is general lighting. When LED can be widely used in the future, the only question left is price. It is estimated that the price of LED packaging products will be lower than the price-performance ratio of $1.5 at 100 lumens. At the same time, the LED efficiency must still be maintained at a level of more than 70 lumens per watt. When the price of AC-DC drive circuit is lower than $0.3 per watt, it will be the time when high-power LED is officially launched in solid-state lighting.
LED performance has a huge impact on product life
. In terms of LED characteristics, the packaging industry only presents the initial characteristics of the component (Initial Characteristic
,
ie, Tj=25℃). However, in actual applications, users want to know the data of the product in the steady state of continuous operation. How can terminal system integrators effectively control LED characteristics when designing products with high-power LED packaging? Customers must be faithfully provided with information about the relationship between the thermal resistance of the LED package, the LED
luminous flux
, and the change of the junction temperature (Tj), as well as the impact of the junction temperature on the LED life.
For system users, the LED package is equivalent to an electronic component, just like other electronic components. Only by providing sufficient component characteristics (especially in terms of thermal performance) can the product life be reasonably estimated and consumer confidence maintained in component use.
Previous article:Silicon Valley semiconductor industry regains its former prosperity: LED lighting
Next article:Design of LED display screen based on ARM S3C44B0X
Recommended ReadingLatest update time:2024-11-16 21:42
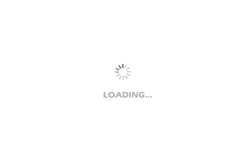
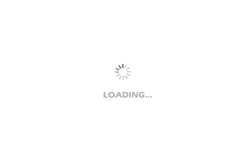
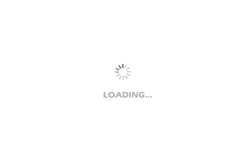
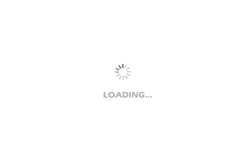
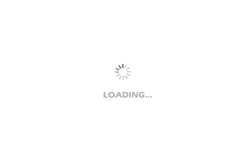
- Popular Resources
- Popular amplifiers
- MathWorks and NXP Collaborate to Launch Model-Based Design Toolbox for Battery Management Systems
- STMicroelectronics' advanced galvanically isolated gate driver STGAP3S provides flexible protection for IGBTs and SiC MOSFETs
- New diaphragm-free solid-state lithium battery technology is launched: the distance between the positive and negative electrodes is less than 0.000001 meters
- [“Source” Observe the Autumn Series] Application and testing of the next generation of semiconductor gallium oxide device photodetectors
- 采用自主设计封装,绝缘电阻显著提高!ROHM开发出更高电压xEV系统的SiC肖特基势垒二极管
- Will GaN replace SiC? PI's disruptive 1700V InnoMux2 is here to demonstrate
- From Isolation to the Third and a Half Generation: Understanding Naxinwei's Gate Driver IC in One Article
- The appeal of 48 V technology: importance, benefits and key factors in system-level applications
- Important breakthrough in recycling of used lithium-ion batteries
- Innolux's intelligent steer-by-wire solution makes cars smarter and safer
- 8051 MCU - Parity Check
- How to efficiently balance the sensitivity of tactile sensing interfaces
- What should I do if the servo motor shakes? What causes the servo motor to shake quickly?
- 【Brushless Motor】Analysis of three-phase BLDC motor and sharing of two popular development boards
- Midea Industrial Technology's subsidiaries Clou Electronics and Hekang New Energy jointly appeared at the Munich Battery Energy Storage Exhibition and Solar Energy Exhibition
- Guoxin Sichen | Application of ferroelectric memory PB85RS2MC in power battery management, with a capacity of 2M
- Analysis of common faults of frequency converter
- In a head-on competition with Qualcomm, what kind of cockpit products has Intel come up with?
- Dalian Rongke's all-vanadium liquid flow battery energy storage equipment industrialization project has entered the sprint stage before production
- Allegro MicroSystems Introduces Advanced Magnetic and Inductive Position Sensing Solutions at Electronica 2024
- Car key in the left hand, liveness detection radar in the right hand, UWB is imperative for cars!
- After a decade of rapid development, domestic CIS has entered the market
- Aegis Dagger Battery + Thor EM-i Super Hybrid, Geely New Energy has thrown out two "king bombs"
- A brief discussion on functional safety - fault, error, and failure
- In the smart car 2.0 cycle, these core industry chains are facing major opportunities!
- The United States and Japan are developing new batteries. CATL faces challenges? How should China's new energy battery industry respond?
- Murata launches high-precision 6-axis inertial sensor for automobiles
- Ford patents pre-charge alarm to help save costs and respond to emergencies
- New real-time microcontroller system from Texas Instruments enables smarter processing in automotive and industrial applications
- Commodore 64 emulator for STM32F429 Discovery
- I would like to know the name of this plug, thank you!
- [Project source code] FPGA-based snake transplantation
- 【Perf-V Review】Summary
- MOJO V3 ISE Engineering
- FPGA design pin allocation points.pdf
- Learn to Wind High Frequency Transformers
- Help: D11, D13 selection, thank you
- I see this device is always used in the circuit drive part such as motor controller
- How to solve the problem that the number of pins of CD4019B chip does not match the datasheet