Introduction
A few months ago I was looking for some LED suppliers and found out there were UV LEDs. My heart went straight to upgrading my not so big setup so I started looking for information on the internet. Turns out some other people have done it and this instructable confirmed that it is really possible. An LED UV box has a definite advantage over many tubes: it can be made at any scale you need. I bought 25 LEDs and started experimenting. That way I could find a match with LED density (pitch), distance between LEDs and board and cost.
LED
The LEDs are OSSV53E1A from OptoSupply and they have a 140 degree angle. This means that a uniform LED density can be obtained at a shorter distance between the LEDs, which means a smaller board height for a given spacing. Their peak wavelength is 405nm. The results show that they emit enough reactive spectrum to resist UV light to allow a perfect exposure. I wanted to use a common voltage and thus connected the LEDs to 12V with a 391Ω resistor in series to ensure a 20mA current.
The final setup will contain a regulator because I don't plan to use my variable regulated power supply LM317 all the time. There is another reason, due to the non linear nature of the LEDs, variations of +/-5% of 12V create a greater impact on the time required for current changes. Putting a regulator on the box just gives more flexibility in choosing the power supply. On the bottom plate I added red LEDs. These LEDs help me adjust the top and bottom of the film. I have used low brightness, cheap, frosted LEDs. The connections are similar, with a 3220Ω resistor in series with the LEDs, except the last row contains 2 LEDs and a 330Ω resistor. These are not really needed, the adjustments to the film can be done in dim ambient light. For safety reasons I added an extra function switch to turn off the UV light when opening the box, turning on the red light and stopping the timer. This makes the box more high tech and gives it a professional behavior.
LED Spacing
I used nuts on the inner wall of the box to glue down the bottom 4mm thick plexiglass. The choice was simple with something easily available. For nuts do not use ordinary glass, as it blocks UV rays. There is no top panel mounted, as it is part of the alignment process: I put the first film on the bottom, then, the second sheet of board is glued on a smaller piece of plexiglass. Alignment is done by aligning the small piece of plexiglass so that both layers overlap perfectly. Having the film attached to it is easier. Extra markings on the outer board help with this (ghost holes). The second part should contain a detailed tutorial on making double-sided boards. The final assembly allows a board area of about 10x15 cm, with temporary internal dimensions of 18 cm long, 5.5 cm wide, 11 cm deep for each of the two halves. The external dimensions will depend on the thickness of the material used. Each board contains 7 x 12 UV LEDs with 3 and 4 holes between them respectively (the actual spacing between the centers of the LEDs is the same). The distance between the top of the LEDs and the board is 3.5cm, including the 4mm of the plexiglass panel. Look at the details below to see a normal 0.1" or 1.27" spacing of the board LED arrangement:
exposure
Exposure results: I tested with small panels from 2 minutes to 8 minutes. Starting for more than 2 minutes did not prove to be the best idea, but my old regime of long exposure times made me choose this value.
You can see in the picture above that from 2 to 7 minutes if perfectly exposed. At 7 minutes some overexposure starts to show up, only in the large copper areas, due to the fact that the film was printed with a laser printer. This result is very different from what I obtain using fluorescent tubes: below 12 minutes it is clearly underexposed and above 14 it is clearly overexposed, leaving only a small interval where it is correct. So far I have used 4 plates with 2 minute exposures and they came out perfect. When the free time will provide anything, I will investigate the results of exposures of less than 2 minutes. Since any time between 2 and 7 minutes seems to work, there is no urgent need for a timer. Nevertheless, a second part should contain this basic circuit.
gallery
Finished board:
Box:
Panel Mount:
Install a nut on the bottom of the plexiglass panel:
Safety switch:
Red light on:
UV pair (switch not used):
In order to build it yourself you must first decide what size you need. With my setup, boards up to 10 x 15 cm may be exposed. For this you will need the following materials:
- 168 UV LEDs, OSSV53E1A;
- 56 91 ohm resistor 0.25W 1% (5% is also OK);
- 66 red diffused LEDs;
- 18 220 ohm resistors for the red LED;
- 6 330 ohm resistors for the red LEDs;
- 2 prototyping boards, 13 x 25 is the smallest size I found to fit;
- 1 cover for 1.5A minimum switch;
- 2 hinges;
- 1 box;
- Others: screws, nuts, glue, etc.
The box may be made of the material of your choice. I have built it from two identical halves, with internal dimensions of 18 x 11 x 5.5 cm each. The material is 8mm thick OSB so you will need the following parts:
- 4 11 x 5.5 cm pieces;
- 4 pieces 19.6 x 5.5 cm;
- 2 19.6 x 12.6 cm pieces.
Timer
Continuing with the development of my UV exposure box I have designed and built the Countdown.
There are several out there for the same purpose, but I wanted to add a few more features to get things done.
As I mentioned in my previous post, safety is a big issue for me, so I added a switch that should prevent the UV LEDs from rotating when the cover is opened. Of course, this is not enough, so the switch works with the timer to make sure everything goes well.
Key Features:
- Accurate time display
- Adjustable time, 10 seconds resolution
- Start/Pause function
- Automatically pauses and UV LED turns off when lid is opened
- Some predefined values available for convenience.
Implementing the safety measure is easy because the switch on the box can make the connection to either the red or UV LED. The timer needs to control the UV LED, so I used a MOS transistor. It also needs to know the state of the box lid. I built a circuit that can achieve all this. The conceptual schematic can be seen below:
The diagram shows, symbolically, that the red and UV LEDs are repeated in arrays across the panel via the base unit: three series LEDs and a resistor. As you can see, there is no way to turn the UV lamp on when the lid is open, even if such a command would come from the microcontroller. The microcontroller can turn the UV lamp on via a MOS transistor only when the lid is closed. This is controlled via software too. To detect if the lid is open or not, the microcontroller monitors the state of the cathodes of the red LED array. When the lid is open, this is shorted to ground and the micro sees a low logic level. When the lid is open the red LED will conduct current, forcing the microcontroller to see a high. This current, although small, is limited by the 10K resistor and therefore the LED does not come on. I could have chosen to leave the red LED on all the time, as this does not affect the functionality of the exposure box, but it adds extra consumption and more heat needs to be dissipated by the lower panel.
Although it doesn't totally make sense, I decided to go through the effort and make a display for this timer. There are probably many ways to do this starting from a simple 555 circuit. I wanted the circuit to be a challenge in its own right so that as small SMD parts as possible were used.
The display is a KW4-361ASB from Luckylight. It is small, 9mm character height and has 4 multiplexed digits. There were two basic criteria for choosing this particular part, firstly I wanted it to be small and efficient so that a small current is enough to brighten the display and secondly I wanted it to be multiplexed as this simplifies the board layout.
I chose the ATTINY2313 microcontroller because it has all the features needed to perform all the tasks: enough pin drivers, timers, enough pins and memory. It has an internal oscillator too, but I missed that the tolerance was within 10%, which I thought was too high for this project. I later added the crystal on board, but adjusted the value of the timer at the start for my particular circuit to compensate for the internal oscillator deviation. This was easy because I knew that the refresh frequency for the display is 50Hz, so the frequency meter is all I need. I believe that this should have no fluctuations and no future compensation will be needed to maintain a smaller value error, maybe less than 2-3%. I recommend using a quartz crystal, but it is not mandatory, you can use my method or simply accept a maximum 10% tolerance.
To turn on the UV LEDs I used a TSM2302 MOS transistor which has a 3.6A capability, more than enough for both boards. Other transistors can be used, such as the IRLML0060TRPBF.
Besides that, there are 4 buttons on the board, a 7805 voltage regulator and connectors. The 4 buttons have the following functions from left to right: Start/Stop timer, UP? adds 10 more seconds, DOWN? subtracts 10 seconds, MEM? recalls some preset value from memory.
Since the software can be flexible in the connections displayed, I chose to make the PCB layout for the connections as convenient as possible, that's why the schematic is not very simple.
The connections for the switch and LED array are as follows:
Because of the function of the box, I decided to make its PCB a challenge: small display, small SMD components. The finished PCB is as follows, the board is very compact and measures less than 6 x 3.5 cm:
The LM317 regulator and heat sink are also mounted in the box:
I used 2 nuts on every mounting screw between the heatsink and the box to ensure good air circulation:
And, of course, 3A protection diodes, just in case:
When installing the timer:
Final result:
You might be wondering why there is no programming interface. There are two reasons: I wanted to make it as compact as possible and the fact that it is the type of circuit that requires a single programmer (for the end user). Since all the required programming pins are connected to the display it is easy to wire up a few programmers, as you can see in the picture below what I did:
Previous article:SEPIC coupled inductor loop current
Next article:Application of frequency converter in air conditioning system
Recommended ReadingLatest update time:2024-11-17 01:59
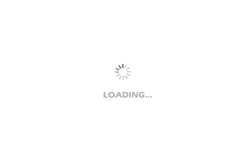
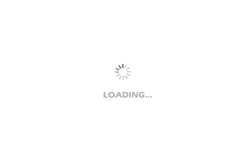
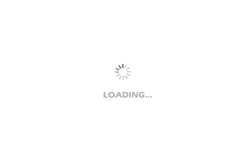
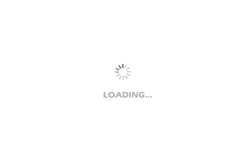
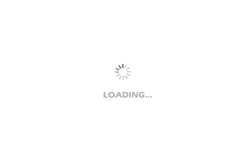
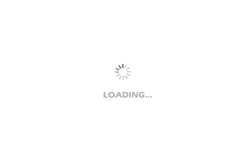
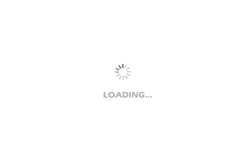
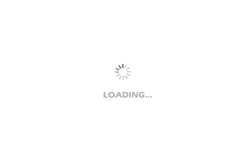
- MathWorks and NXP Collaborate to Launch Model-Based Design Toolbox for Battery Management Systems
- STMicroelectronics' advanced galvanically isolated gate driver STGAP3S provides flexible protection for IGBTs and SiC MOSFETs
- New diaphragm-free solid-state lithium battery technology is launched: the distance between the positive and negative electrodes is less than 0.000001 meters
- [“Source” Observe the Autumn Series] Application and testing of the next generation of semiconductor gallium oxide device photodetectors
- 采用自主设计封装,绝缘电阻显著提高!ROHM开发出更高电压xEV系统的SiC肖特基势垒二极管
- Will GaN replace SiC? PI's disruptive 1700V InnoMux2 is here to demonstrate
- From Isolation to the Third and a Half Generation: Understanding Naxinwei's Gate Driver IC in One Article
- The appeal of 48 V technology: importance, benefits and key factors in system-level applications
- Important breakthrough in recycling of used lithium-ion batteries
- Innolux's intelligent steer-by-wire solution makes cars smarter and safer
- 8051 MCU - Parity Check
- How to efficiently balance the sensitivity of tactile sensing interfaces
- What should I do if the servo motor shakes? What causes the servo motor to shake quickly?
- 【Brushless Motor】Analysis of three-phase BLDC motor and sharing of two popular development boards
- Midea Industrial Technology's subsidiaries Clou Electronics and Hekang New Energy jointly appeared at the Munich Battery Energy Storage Exhibition and Solar Energy Exhibition
- Guoxin Sichen | Application of ferroelectric memory PB85RS2MC in power battery management, with a capacity of 2M
- Analysis of common faults of frequency converter
- In a head-on competition with Qualcomm, what kind of cockpit products has Intel come up with?
- Dalian Rongke's all-vanadium liquid flow battery energy storage equipment industrialization project has entered the sprint stage before production
- Allegro MicroSystems Introduces Advanced Magnetic and Inductive Position Sensing Solutions at Electronica 2024
- Car key in the left hand, liveness detection radar in the right hand, UWB is imperative for cars!
- After a decade of rapid development, domestic CIS has entered the market
- Aegis Dagger Battery + Thor EM-i Super Hybrid, Geely New Energy has thrown out two "king bombs"
- A brief discussion on functional safety - fault, error, and failure
- In the smart car 2.0 cycle, these core industry chains are facing major opportunities!
- Rambus Launches Industry's First HBM 4 Controller IP: What Are the Technical Details Behind It?
- The United States and Japan are developing new batteries. CATL faces challenges? How should China's new energy battery industry respond?
- Murata launches high-precision 6-axis inertial sensor for automobiles
- Ford patents pre-charge alarm to help save costs and respond to emergencies
- MM32F103 Development Board Initial Impressions
- With the configuration parameter table, can AT commands be customized?
- Sincerely recruiting embedded software and hardware engineers
- Characteristics, functions and precautions of chopper
- Copper plating under the DC conversion power inductor
- Regarding FPGA development, compared with several major companies' EDA design tools, Xilinx's Vivado is still the best
- How to simulate I2C communication using GPIO on C2000
- Never forget the teacher's kindness, teachers, happy holidays~~
- ★★ If you don’t read this before you start to learn embedded systems, you will definitely regret it.
- PCB short circuit