When confirming the use and installation environment, capacitors used within the rated performance range specified in the product sample design instructions should avoid use in the following situations:
a. High temperature (temperature exceeds the maximum operating temperature);
b. Overcurrent (current exceeds the rated ripple current). When the ripple current exceeds the rated value, the capacitor body will overheat, the capacity will decrease, and the life will be shortened;
c. Overvoltage (voltage exceeds rated voltage). When the voltage applied to the capacitor is higher than the rated working voltage, the leakage current of the capacitor will increase, and its electrical and oxygen properties will deteriorate in a short period of time until it is damaged;
d. Apply reverse voltage or AC voltage. When a DC aluminum electrolytic capacitor is connected to the circuit with reverse polarity, the capacitor will cause the electronic circuit to short-circuit, and the resulting current will damage the capacitor. If it is possible to apply a positive voltage to the negative lead in the circuit, use a non-polar capacitor;
e. When used in circuits that are repeatedly and rapidly charged and discharged, such as for fast charging, its service life may be shortened due to capacity reduction, rapid temperature rise, etc.;
f. It is prohibited to use capacitors in harsh environments where they are in direct contact with water, salt water, oil or where there is condensation, in environments filled with harmful gases (sulfide, ammonia, etc.), in environments exposed to direct sunlight, ozone, ultraviolet rays, and radioactive substances, or in environments where vibration and impact conditions exceed the range specified in the sample and instructions;
g. When installing the capacitor, leave space above the explosion-proof valve of the capacitor, avoid wiring and installing other components above the explosion valve, and avoid installing heating components around the capacitor and on the circuit board.
Notes on capacitor installation
a. Used capacitors cannot be used again, but they can be removed for periodic inspection to test electrical performance;
b. If the capacitor has been charged, it should be discharged with a resistor of about 1kΩ before use;
c. If the capacitor is stored at a temperature above 35°C and a humidity greater than 70%, its leakage current may increase. Before use, it can be treated by applying a rated voltage through a resistor of about 1kΩ;
d. Before installation, confirm the rated capacity, voltage and polarity of the capacitor;
e. Do not use capacitors that have fallen on the ground;
f. Do not use deformed capacitors;
g. The spacing between the positive and negative leads of the capacitor should match the position of the solder holes on the PCB. If the capacitor is forcibly inserted into a circuit board with incompatible hole spacing, stress will act on the lead wires, causing the capacitor to short-circuit or increase leakage current;
h. During installation, insert the capacitor pins or soldering pins into the PCB until the bottom of the capacitor is attached to the surface of the PCB;
i. Do not apply mechanical pressure exceeding the specified value. When tension is applied to the capacitor lead wire, the tension will act on the inside of the capacitor, causing a short circuit, open circuit or increased leakage current. Do not shake the capacitor strongly before soldering it to the circuit board.
Mechanism of capacitor failure due to low voltage
In circuit design, there is a common perception that "when the margin design of the device is uncertain, the larger the margin, the more reliable it will be". In fact, this view is wrong. For safety capacitors, if the withstand voltage margin is too large, it will also lead to a kind of failure, which is called "low voltage failure".
The mechanism of low voltage failure is the existence of dielectric leakage current. Under high humidity conditions, moisture will penetrate into the capacitor due to its poor sealing. When voltage is applied to the two poles of the capacitor, the infiltrated moisture will form leakage current due to its conductivity. Excessive leakage current will greatly reduce the energy storage characteristics of the capacitor, resulting in the loss of the capacitor's characteristics. This phenomenon is most likely to occur when the capacitor is powered on after the humidity storage test.
However, after a period of high-temperature storage (not less than 2 hours), the performance of the capacitor can be restored when the power is turned on again.
Alternatively, remove the capacitor and apply a higher voltage to both ends (not less than 0.7 times the rated voltage, such as a 50V capacitor, add a voltage of not less than 35V and not more than 50V), apply the voltage for a short period of time, and then solder the capacitor to the circuit board. After turning on the power, the failure phenomenon will disappear.
The mechanism of the above phenomenon is shown in the figure. When moisture penetrates into the filling medium, a leakage current path as shown in the figure will be formed, on which leakage current will be generated. There is resistance in the conduction path, so heat I2R will be generated. When the rated withstand voltage of the capacitor is large, and the actual applied voltage is very small (such as applying 10% of the rated withstand voltage), the heat is very small and is not enough to evaporate the moisture, so it manifests as capacitor failure. However, when the applied voltage is large, the same resistance value can generate a large amount of heat, which will cause moisture to evaporate quickly and the capacitor characteristics will recover quickly. Therefore, the withstand voltage of the capacitor is reduced too much, which is easy to cause low voltage failure. Generally, it is advisable to reduce the rated value to 70% of the rated value.
After the high-temperature storage test, moisture evaporates quickly at high temperatures and the capacitance characteristics can be restored.
The mechanism and solution of capacitor pin fracture failure
Environmental stress screening test (ESS test) is a common method to evaluate the quality of the whole product. In the ESS test, the stress of random vibration is intended to evaluate the defects of the product in terms of structure, assembly, stress, etc. Large capacitors are prone to pin breakage during vibration tests if no separate treatment measures are applied after welding. This experiment simulates the stress conditions of transportation vibration, operation vibration, impact, collision and fall.
The fracture mechanism is stress concentration, which generally occurs at the capacitor lead pins or pad connection points, as shown in the figure. When in a vibrating environment, the capacitor lead pins and pad connection points will be subjected to the impact force in the lateral shear and longitudinal tensile directions of the entire capacitor, especially when the capacitor is large, such as a large electrolytic capacitor.
The mechanism of this phenomenon is simple and the solution is not complicated. The general experience is to apply a circle of silicone rubber GD414 on the bottom of the capacitor to fix it with adhesive, but this treatment method does not work.
Silicone rubber has a tensile strength of 4-5MPa, an elongation of 100%-200%, weak intermolecular forces, poor adhesion, and low bonding strength. When used to bond capacitors, it appears to be fixed, but in fact, when the impact stress is large, the silicone rubber is stretched to a large extent, and the capacitor itself is still subject to large tensile stress and shear stress. Therefore, the recommended material for fixing is E-4X epoxy resin glue, which has a tensile strength greater than 83MPa, an elongation less than 9%, good adhesion, high bonding strength, low shrinkage, and stable dimensions. It can be clearly seen from the performance that E-4X epoxy resin glue can play a real fixing role.
The glue coating process must also be refined, requiring that the height of the epoxy glue fixing capacitor reach 1/3 of the capacitor body and form a ridge-like support on both ribs, so that the capacitor and the E-4X glue become one, no longer vibrate during vibration, and the pins are protected.
In addition, in addition to gluing and fixing, the circuit board assembly production process will also be introduced. The capacitor is assembled first, and then other components are assembled. In this way, the vertical capacitor is the highest point, and it is easy to be bumped or forced to tilt during turnover or placement. The process is changed to assemble other components and bond the columns first, and then assemble the high capacitor. In this way, during turnover or placement, the columns slightly higher than the capacitor are subjected to force to protect the capacitor.
Before the improvement process, the circuit board is first vacuum coated (forming a 15μm thick Paeilene film material on the ceramic surface of the capacitor), and then coated with silicone rubber for fixation. After the improvement, epoxy glue is first applied to the capacitor, and then the entire circuit board is vacuum coated, so that the Paeilene film is formed on the outer surface of the capacitor and the glue. Since the surface roughness of the Paeilene film is smaller than that of the ceramic surface, the contact angle of the glue on the Paeilene film surface is greater than that of the ceramic surface (the smaller the contact angle, the better the wetting effect), and the fixing effect is better after the improvement.
There are three conclusions to summarize the above problems and solutions: 1. The nature of the capacitor pin fracture is fatigue fracture; 2. The unreasonable design of the assembly method, insufficient bonding strength of the fixing glue and imperfect process are the reasons for the pin fracture; 3. Use epoxy resin glue and adjust the production process to solve this problem from an engineering perspective.
Previous article:Design of solar charger based on supercapacitor-lead-acid battery hybrid energy storage
Next article:Design of industrial control monitoring system based on FPGA
Recommended ReadingLatest update time:2024-11-17 02:40
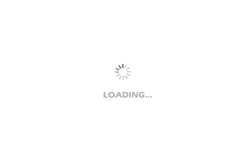
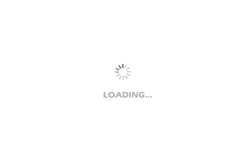
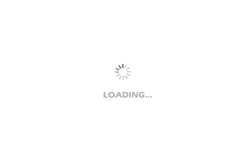
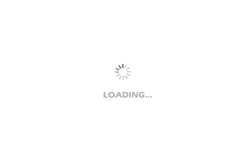
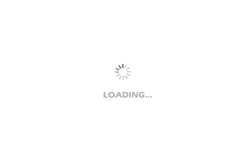
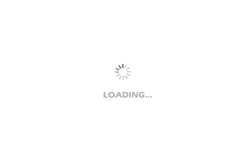
- MathWorks and NXP Collaborate to Launch Model-Based Design Toolbox for Battery Management Systems
- STMicroelectronics' advanced galvanically isolated gate driver STGAP3S provides flexible protection for IGBTs and SiC MOSFETs
- New diaphragm-free solid-state lithium battery technology is launched: the distance between the positive and negative electrodes is less than 0.000001 meters
- [“Source” Observe the Autumn Series] Application and testing of the next generation of semiconductor gallium oxide device photodetectors
- 采用自主设计封装,绝缘电阻显著提高!ROHM开发出更高电压xEV系统的SiC肖特基势垒二极管
- Will GaN replace SiC? PI's disruptive 1700V InnoMux2 is here to demonstrate
- From Isolation to the Third and a Half Generation: Understanding Naxinwei's Gate Driver IC in One Article
- The appeal of 48 V technology: importance, benefits and key factors in system-level applications
- Important breakthrough in recycling of used lithium-ion batteries
- Innolux's intelligent steer-by-wire solution makes cars smarter and safer
- 8051 MCU - Parity Check
- How to efficiently balance the sensitivity of tactile sensing interfaces
- What should I do if the servo motor shakes? What causes the servo motor to shake quickly?
- 【Brushless Motor】Analysis of three-phase BLDC motor and sharing of two popular development boards
- Midea Industrial Technology's subsidiaries Clou Electronics and Hekang New Energy jointly appeared at the Munich Battery Energy Storage Exhibition and Solar Energy Exhibition
- Guoxin Sichen | Application of ferroelectric memory PB85RS2MC in power battery management, with a capacity of 2M
- Analysis of common faults of frequency converter
- In a head-on competition with Qualcomm, what kind of cockpit products has Intel come up with?
- Dalian Rongke's all-vanadium liquid flow battery energy storage equipment industrialization project has entered the sprint stage before production
- Allegro MicroSystems Introduces Advanced Magnetic and Inductive Position Sensing Solutions at Electronica 2024
- Car key in the left hand, liveness detection radar in the right hand, UWB is imperative for cars!
- After a decade of rapid development, domestic CIS has entered the market
- Aegis Dagger Battery + Thor EM-i Super Hybrid, Geely New Energy has thrown out two "king bombs"
- A brief discussion on functional safety - fault, error, and failure
- In the smart car 2.0 cycle, these core industry chains are facing major opportunities!
- Rambus Launches Industry's First HBM 4 Controller IP: What Are the Technical Details Behind It?
- The United States and Japan are developing new batteries. CATL faces challenges? How should China's new energy battery industry respond?
- Murata launches high-precision 6-axis inertial sensor for automobiles
- Ford patents pre-charge alarm to help save costs and respond to emergencies
- The college entrance examination is over, but we are still in the "high-school" mode
- 【Arduino】168 Sensor Series Experiments (211) --- WS2812B Ring 93 Light Module
- The dry goods in the jar are worth the quick surfing ANT series
- Matching of vivado version and modelsim version
- I have some questions about project handover (software) at work. I hope experienced seniors can give me some guidance.
- Learn about RF MEMS switches in one article
- CC2541 Bluetooth Learning-Clock Setting
- Dismantle ABC and CCB U-Shield
- How to view MSP430 technical data
- How to view the status of GPIO ports during CCS5.5 debugging