LED light sources have many environmental advantages, but early products still have some technical bottlenecks in heat dissipation and high brightness design that cannot be broken through. However, with the continuous improvement of LED chip manufacturing process, the brightness output lumens of existing lighting LEDs are closer to daily lighting needs. In addition , the IC solid-state component design allows LED light source design to add more application flexibility and advantages.
In particular, LED light sources have the advantages of being not easily damaged and having a long lifespan. If the cost of each unit is not taken into account, compared to traditional high-energy-consuming tungsten filament lamps (incandescent lamps)/halogen lamps/high-pressure sodium lamps, and CCFL fluorescent lamps with mercury pollution concerns, LED is a new alternative light source with excellent performance.
However, in order to cope with different daily lighting applications, it is also necessary to continuously improve LED product design in terms of luminous efficiency , light shape, heat dissipation design and overall cost of use, so that LED lighting has more practical value and is no longer just a decoration that demonstrates environmental protection.
80W high brightness LED can have 6,400~8,000 lumens brightness, the lamp can reach 100lm-W, and the component life exceeds 50,000 hours.
LED lighting sources have different material properties and different light-emitting principles from traditional lighting equipment. If the light shape is not processed and the lighting quality is not improved, there are still many limitations to directly replacing the light sources used in daily life with LEDs, especially the key issues such as color rendering , lighting shape, lighting color, power conversion efficiency, etc., which need to be improved through chip process improvement or optical and physical design enhancement of lamps to further meet the needs of general lighting.
LED solid-state lighting still has the problem of high cost
In the actual lighting application market, LED solid-state lighting itself is still subject to high unit prices and high costs. If the relevant industry wants to accelerate the popularization of LED lighting applications in a short period of time, it is still necessary to improve cost efficiency one by one in key projects such as component costs, manufacturing technology, and verification standards.
In terms of production technology, the final product must be enhanced in terms of color temperature, color rendering, and photoelectric conversion efficiency. At the same time, it is necessary to improve related technologies such as AC-DC power conversion, high-power drive control, light source heat dissipation, and light shape processing. These are all important keys to the rapid popularization of LED lighting technology.
High-brightness LEDs have a longer service life than traditional high-brightness halogen lamps and sodium lamps. They can be made into outdoor lamps, saving maintenance costs.
As mentioned earlier, the design of LED lighting sources must first improve the heat dissipation design of the lighting module. The integration of heat dissipation mechanisms is the key to whether LED lighting products can maintain long life and low light decay. For example, using COB LED
polycrystalline
lamp boards, the LED chips are fixed on the printed circuit board. The LED chips can directly contact
the PCB
to increase the heat conduction efficiency, thereby improving the common heat dissipation problems in LED lighting applications.
LED substrate design can improve component heat dissipation efficiency
In order to cope with high-power, high-brightness lighting application designs, the original PCB substrate will be replaced with a metal core PCB material to increase the heat dissipation efficiency of LED components, because the heat generated during the driving process can be reduced by the metal core of the PCB to reduce thermal impedance, thereby enhancing the heat dissipation performance.
Metal core PCBs often use MCPCB (Metal Core Printed Circuit Board) to reduce the thermal resistance of the substrate design. In order to reduce costs, MCPCB often uses aluminum as the core of the substrate, which has low cost, good heat dissipation capacity and better corrosion resistance.
If LED is to gain the advantage of being widely used as a daily light source, it must further develop the core technology of the chip. The key factors affecting the luminous characteristics and efficiency of LED components are the differences in the substrate material and crystal growth technology. In addition to the traditional sapphire substrate, LED substrate materials such as silicon, silicon carbide, zinc oxide, gallium nitride, etc. are currently the focus of LED applications. Thin-film chip technology is the key technology for developing high-brightness LED chips.
Thin film focuses on reducing the lateral light loss of the crystal grains. With the bottom reflective surface integration, 97% of the chip's light output generated by electricity can be directly output from the front of the LED to avoid light loss, which naturally improves the unit luminous efficiency of the LED. In addition to improving the photoelectric efficiency of the LED chip, it can also be improved by changing the chip structure, such as the roughening design of the chip surface, and through multiple electro-optical efficiency improvement process methods to improve the product.
Comprehensively enhance the lighting performance of LED components using packaging technology
In terms of high-power LED packaging technology, it can be divided into single chip packaging, multi-chip integrated packaging, chip board packaging, etc. By improving the packaging technology, the LED luminous efficiency, heat dissipation, and product reliability can be comprehensively improved.
In terms of single chip packaging applications, packaging can be used to improve luminous efficiency, heat dissipation thermal resistance, or develop SMT mass-produced components. In addition, during the packaging stage, fluorescent powder can be mixed into the package to improve the output color temperature of the LED, or control the LED lighting color and improve the lighting quality.
High brightness LED lamp module, can be driven by a single high power LED to reach 30W~120W
In addition to improving the process of the die itself or using packaging design, the design of LED lamps or the combination of optical lenses can all use optical physical properties to improve product quality. For example, LEDs with optical silicone encapsulation can give the components a larger lighting beam angle, and the components that have been packaged can also be used with secondary optical lenses to strengthen the design of the bottom reflector cup, greatly enhancing the optical properties of LED components.
Among the many LED design solutions for high-brightness lighting , there are also solutions that use a large number of LED components in a flat arrangement to increase the light output of the lamp by quantity. The same is true for LED component packaging. Packaging multiple LED chips at once on the carrier plane is also a common design solution for LED lighting applications.
Previous article:Design of full-color LED display system based on STM32
Next article:Detailed explanation of various LED cooling technologies and insight into LED lighting cooling strategies
Recommended ReadingLatest update time:2024-11-16 17:52
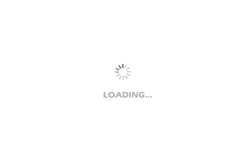
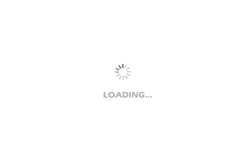
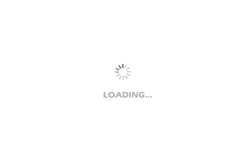
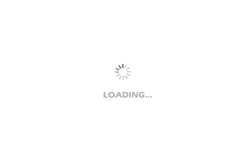
- Popular Resources
- Popular amplifiers
- MathWorks and NXP Collaborate to Launch Model-Based Design Toolbox for Battery Management Systems
- STMicroelectronics' advanced galvanically isolated gate driver STGAP3S provides flexible protection for IGBTs and SiC MOSFETs
- New diaphragm-free solid-state lithium battery technology is launched: the distance between the positive and negative electrodes is less than 0.000001 meters
- [“Source” Observe the Autumn Series] Application and testing of the next generation of semiconductor gallium oxide device photodetectors
- 采用自主设计封装,绝缘电阻显著提高!ROHM开发出更高电压xEV系统的SiC肖特基势垒二极管
- Will GaN replace SiC? PI's disruptive 1700V InnoMux2 is here to demonstrate
- From Isolation to the Third and a Half Generation: Understanding Naxinwei's Gate Driver IC in One Article
- The appeal of 48 V technology: importance, benefits and key factors in system-level applications
- Important breakthrough in recycling of used lithium-ion batteries
- Innolux's intelligent steer-by-wire solution makes cars smarter and safer
- 8051 MCU - Parity Check
- How to efficiently balance the sensitivity of tactile sensing interfaces
- What should I do if the servo motor shakes? What causes the servo motor to shake quickly?
- 【Brushless Motor】Analysis of three-phase BLDC motor and sharing of two popular development boards
- Midea Industrial Technology's subsidiaries Clou Electronics and Hekang New Energy jointly appeared at the Munich Battery Energy Storage Exhibition and Solar Energy Exhibition
- Guoxin Sichen | Application of ferroelectric memory PB85RS2MC in power battery management, with a capacity of 2M
- Analysis of common faults of frequency converter
- In a head-on competition with Qualcomm, what kind of cockpit products has Intel come up with?
- Dalian Rongke's all-vanadium liquid flow battery energy storage equipment industrialization project has entered the sprint stage before production
- Allegro MicroSystems Introduces Advanced Magnetic and Inductive Position Sensing Solutions at Electronica 2024
- Car key in the left hand, liveness detection radar in the right hand, UWB is imperative for cars!
- After a decade of rapid development, domestic CIS has entered the market
- Aegis Dagger Battery + Thor EM-i Super Hybrid, Geely New Energy has thrown out two "king bombs"
- A brief discussion on functional safety - fault, error, and failure
- In the smart car 2.0 cycle, these core industry chains are facing major opportunities!
- The United States and Japan are developing new batteries. CATL faces challenges? How should China's new energy battery industry respond?
- Murata launches high-precision 6-axis inertial sensor for automobiles
- Ford patents pre-charge alarm to help save costs and respond to emergencies
- New real-time microcontroller system from Texas Instruments enables smarter processing in automotive and industrial applications
- MSP430G2755 Main Memory Bootloader UART Porting Guide
- A simple temperature control circuit to help you understand the circuit diagram
- 【CH579M-R1】3. ADC internal temperature measurement, external channel and touch button test
- How to migrate from GCC Linker to SEGGER Linker in Embedded Studio?
- Based on PSOC6 development board simulation I2C solution X-NUCLEO-IKS01A3 LPS22HH
- 【CH579M-R1】+OTA first experience
- Xunwei i.MX6ULL Terminator to view the real-time value of variables
- Simple 6LoWPAN Mesh Data Collector
- I created a project with stm32cubemx and then used the module generated by keil RTE, but the code generated by RTE is repeated. How can I disable the duplication?
- 【ESP32-C3-DevKitM-1】LED PWM for ESP32-C3