Low voltage AC lighting systems are becoming more and more popular in the market, from indoor accent lighting to general track lighting and even outdoor lighting systems. Retailers and home improvement stores such as IKEA and Home Depot have quickly and widely communicated these technologies to customers, making power systems incorporate specific low voltage usage rules so that users can install them themselves without going through contractors. The rise
of low voltage AC LED lighting applications
All low voltage AC lighting systems use a stand-alone main power supply. This main power supply provides an offline AC conversion solution to low voltage. Under any load, even if the circuit is open circuit, its output will not exceed 30 volts effective value (VRMS). Secondly, the circuit must have a 25 ampere (A) current limit under all conditions. These two conditions will determine the maximum power of low voltage AC lighting applications. The typical output voltage is 12 or 24 volts AC (VAC), but the maximum current value of 25 amps remains unchanged, whether it is a 12 volt, 300 watt (W) system or a 24 volt, 600 watt system.
For these reasons, low voltage AC lighting is becoming increasingly popular in light emitting diode (LED) lighting applications, and the technology can even be used in 300 watts of LED lighting power, equivalent to the output of three to four street lamps. This allows designers great flexibility in design, allowing for relatively large single components or multi-configuration lamp designs powered by a single power source, or designs in between. What is certain is that through flexible LED lighting application design, lighting systems will take a big step forward from traditional incandescent lamps.
In low voltage AC systems, three different lighting fixtures can be considered, first a large/high output design that is only installed in one or two individual systems; second a medium output design that can support ten to twenty small lamps installed in the system; and finally a small output design that allows fifty to one hundred lamps in a single system.
Large array designs create high light source output applications
For large array designs, the benefits of LED unique design are immediately apparent in two different areas, especially in the more unique example of large lighting sources, where large arrays can be used to create high light source output applications. Typically, a 100W LED source is used in street lighting applications (using a high voltage offline solution). Although it is not recommended to use a low voltage AC system (which would bring a whole new set of rules and standards), designers have the opportunity to achieve the same effect with a low voltage AC budget, starting with a standard LED with a forward voltage of 3.5V and using 350mA current, roughly based on 1.2W each or about eighty LEDs.
In order to achieve the expected output power, it is very attractive to use a single driver and multiple series/parallel combinations of LED solutions, but the industry generally does not encourage this design rule because if individual control of each LED line is supported, the first problem encountered is that the LED and temperature have a feedforward relationship. When the temperature rises, the forward voltage drop must be strictly controlled to avoid more current flowing and further increase the temperature of the LED. The biggest impact is that when different lines share the same current, improper matching problems will soon occur. If the current is not individually arranged to pass through the entire line, it is likely to become the source of system failure.
Finding the Right LED Driver Using Online Design Tools
As mentioned above, there are a variety of drivers available on the market that can meet the needs. National Semiconductor (NS) has several LED drivers that can achieve the required maximum input range while also having the features and performance of easy design. Let's start with the 24VAC system, which is the most notable special large-scale lamp. The drivers mentioned so far are DC-DC converters, so there will be some rectification of the AC signal provided by the main power supply. Based on this situation, the input conditions for the converter must be changed to:
24VRMS=67.88VPP and the maximum input voltage range of the driver after adjustment is 34 volts.
For the conditions that are known, at this stage of the design, the designer may have a specific LED specification in mind, and all the designs discussed in this article can be developed using an online design tool such as National Semiconductor's WEBEBCH LED Designer, where the input voltage (34 volts DC), LED type/value and the desired output configuration can be entered. In addition, under the conditions of 350 mA and Vf = 3.5 volts, a 24VAC light string composed of nine LEDs can be driven, which is 34 volts direct current (VDC) after rectification. Through the parameter search tool in the online tool, it seems that there are many applicable input ranges, but due to the limitation of the working cycle, there are actually not a large number of supported lines. In this case, only two LED drivers, LM3401 and LM3409 from National Semiconductor, can be supported. If the number of LEDs is reduced from nine to eight, the choice of drivers will increase.
It is worth noting that when the number of LEDs in the light string increases, it needs to be supported by voltage boosting. The main converter topology of most low-voltage AC applications today is the buck converter (the output drive voltage to the LED is lower than the input voltage to the converter), which is the main point of view for fewer LED lines.
Understand the role of the driver and prescribe the right medicine for the situation
Generally speaking, it is most cost-effective to use a single driver to drive multiple LEDs. However, it is not advisable to use parallel lines in a single driver, but it is hoped that the series lines can be extended as much as possible; the advantage is that even if the lines are strictly regulated and protected, the current passing through the LEDs can be ensured to be the same. In this way, a larger input voltage can simply drive a large number of LED lines, but after rectification, the line usually loses half of the AC voltage value, so its advantage is greatly reduced; to solve this problem, a boost solution can be adopted (when the output voltage is larger than the input voltage) to reduce the burden of driving a large number of LED lines.
Another point of view is that if the light string can maintain less than 20 LEDs (Vf = 3.5V and 350mA LED drive current), it can maintain the boost output under the low voltage limit (70VDC under the low voltage limit of 84.85VPP), which can be achieved through any LM342X driver from National Semiconductor, which provides overvoltage/undervoltage protection mechanism, current limit, and overheat protection function as required.
In addition, understanding the characteristics of the driver device plays an important role in circuit design, such as whether it is necessary to support pulse width modulation (PWM) dimming, analog dimming, etc., or whether some optical elements and overheat protection need to be added to change the light source output. The above considerations are all factors in choosing which driver to use.
In response to the above needs, the LM3421/23 driver has the characteristics of preventing and detecting additional error warnings, which is a suitable component for applications that want to achieve high-level protection and provide microcontroller (MCU) response. The built-in overheat protection function of the LM3424 is beneficial for optical or overheat protection applications (reducing the output current related to LED temperature); furthermore, although the LM3429 is the most basic driver in this series, it still has overvoltage protection and current limiting in boost applications to assist boost detection.
Figure 1 shows a circuit diagram for driving twenty LEDs, each with an average current of 350 mA and a forward voltage of 3.5 volts. In addition, the circuit may be changed due to the need for analog dimming (when the input is reduced, the output of the light source will decrease) to meet the requirements of a simple and fully protected line driver. If you want to seek more stringent color accuracy, PWM dimming can be used.
Figure 1 Large array designs use the LM3429 in a boost configuration to drive twenty LEDs at 350 mA from a 24VAC system.
Large capacitor solution reduces ripple and extends electrolytic capacitor life
There is a simple concept of applying a boost solution to recover the voltage lost when driving a large number of LED strings with AC rectification and still keep it in the low voltage limit. This is about 27 watts consumed by the front end (24.5 watts LED at 92% efficiency), so it is obvious how the system can be expanded to a high specification design with each line fully protected under a single accessory.
If four such circuits are further adopted, each line can achieve the 100-watt design goal of complete protection and control. To achieve this architecture, a general rectifier may be used in the front end (only a bridge diode with a current rate of ×4 and a capacitor of ×4 of C1/C2 are required). In addition, if the LED lighting design has 300 to 600 watts of available power in a low-voltage system, the total current of 25 amps has many options for designers. For example, the maximum voltage and current margin (Headroom) from D1 to D4 needs to be regulated. The output capacitance can be expressed by the following equation:
C=0.7(I)/ΔE(f)
Where I represents the input current to the downstream circuit (DC to DC conversion area), ΔE is the allowable ripple voltage, and f is the AC frequency. Since this design has 92% efficiency, given the LED power of 24.5W, this means that the front-end DC-DC area will have 26.6W of power; and after rectification (34VDC), from the 24VAC source, 26.6W is used and an average input current of about 782mA is generated. In this way, the diode rectifier can be appropriately sized.
On the other hand, the acceptable ripple also affects the capacitor requirements. For example, to implement an input current of 800mA and allow a ripple of 1V on the 120Hz line (2×60Hz due to the bridge rectifier) requires a large capacitor of 9,300μF; if the ripple is 3V, only 1,500μF is needed. Since reducing the ripple provides better protection for the life of the electrolytic capacitor, the large capacitor will be the possible choice in this case.
Small Array Design Challenges Lowering Capacitor Temperatures Is Imperative
At the other extreme of the spectrum is a small array design, which could be a single LED component or three components in a single package, making 1W a 3W solution for modern LED lighting efficiency, popular in ambient and park lighting.
Keeping 105°C rated capacitors cool at 65°C and below is the weakest link in the design; however, since electrolytic capacitors double their life for every 10°C below rated temperature, if a designer can maintain 65°C or better, a 105°C rated capacitor will have its rated life extended sixteen times, at this ratio, a 5,000 hour rated capacitor can be extended to 80,000 hours, making small array designs a great challenge but imperative.
As can be seen, good thermal design plays a key role in LED applications, and using an efficient driver such as the LM3429 makes the design challenge easier to solve. The hottest device in this design is the unijunction field effect transistor (FET) M1 switch, which can reach a temperature of about 65°C. Although this does not have much impact, the designer must ensure that it and other important heat sources are kept away from the electrolytic capacitors and that all components on the board are kept below 50°C. It can be seen that the heat dissipated from the LED is always the biggest challenge, not the electronics.
Small Array Designs Win in Cabinet/Display Lighting
Cabinet and display lighting are another popular application for small array designs in low voltage AC systems. Consider a 3V forward voltage, 350mA, 1W LED. With a simple 12VAC system, the buck converter architecture provides ample margin and can efficiently drive the LED. As shown in Figure 2, the LM3407 offers a 350mA output limit, a small package, and very few external components to drive this type of LED. Due to the low power consumption design (slightly over 1.5W at the input), up to two hundred modules can be supported on a single low voltage 12VAC circuit, and more than two hundred and fifty if operated using a 24VAC system (most low voltage systems are current limited to 25 amps maximum).
Figure 2 The LM3407, which is suitable for small array design, uses a 12VAC system to drive a 3Vf single LED with a
current of 350 mA. In contrast, the conversion of AC to DC is handled by a large array design. Based on the input current in the DC to DC conversion region, appropriate values can be selected for the input rectifier diode and the holding capacitor. In this design, an input current of less than 100 mA and a ripple of 2 volts are required, so 330 μF will easily meet such requirements.
An additional consideration is for designing for smaller loads. The primary transformer may require a minimum load to operate. This is especially true in very small and low power systems. For a 60W low voltage AC transformer, a 10W load may be required to operate properly. The efficiency of the LED device can handle this problem depending on the supply range of the main power supply.
For example, in the RD-148 reference design from National Semiconductor, the LM3405A is used to demonstrate a single LED solution driving a 3.6Vf, 600mA system in a 12VAC system. The LM3405A and LM3407 based on the reference design architecture are suitable for use in smaller light modules because of their small package size (LM3405A uses SOT23 package) and very few external components. Through the example of RD-148, a complete solution with a size of 14mm x 21.5mm can be easily implemented, and even smaller solutions are possible.
Thermal management is critical for mid-size array systems
Recent advances in mid-size designs (mid-size arrays, but many individual systems) have resulted in higher lighting output with better efficiency and thermal management techniques using larger multi-component arrays in a single package. To accomplish this, consider a 10.5 volt Vf warm white array, and a typical current of 640 mA. It is important to note that maintaining the array at typical currents or proper thermal management can extend product life, even in high temperature environments, and while this is a difficult challenge for many IC drivers, market demand has led to a large number of products that meet this requirement. However, after several design cycles, the industry has found that many drivers that integrate FETs have difficulty dealing with thermal design.
Continuing with the above argument, many integrated FET products operate at an ambient temperature of 30°C, and their IC junction temperature exceeds 90°C. This means that the component has only a 35°C margin under the recommended operating temperature of the external environment (it will enter thermal shutdown when it reaches 150-160°C, but the maximum recommended operating temperature is 125°C). This is difficult to handle for thermal mechanical design, so it is necessary to ensure that this situation does not occur in LED applications.
Thermal Challenges Solved with Highly Integrated Controllers
In summary, the thermal cycle with a 60°C temperature difference (from the LED cap to the soldering point, all the way to the driver board) is not perfect in design. When it comes to the life and reliability of LEDs, thermal energy is always a problem that must be solved, and the LM3409 controller shown in Figure 3 is an excellent choice. It allows designers to dissipate heat through various external components. For example, a low-cost P-Channel metal oxide semiconductor field effect transistor (PFET) external component can be used to significantly reduce the system temperature by using the LM3409, and the hottest component should be the PFET at 53°C.
Figure 3 The LM3409, suitable for medium-sized array designs, uses a 12VAC system to drive 640 mA of current and 10.4 volts into the LED array package.
Since the junction temperature of LM3409 is 43℃ and all tests are conducted at 30℃ ambient temperature, it means that it has sufficient thermal margin, which makes it easier for designers to achieve thermal design goals. In addition, LM3409 is a highly integrated controller, especially for fixed current LED drive applications, so only a few external components are needed to solve size problems and reduce production costs.
LM3409 also has the advantage of easy dimming control. Whether it is PWM dimming (on the EN pin) or analog dimming, the analog dimming function can be obtained by separating the main input rail through a voltage divider. In this way, when the input voltage is directly reduced, the LED current is also reduced to achieve design flexibility. Secondly, if absolute color accuracy or other special dimming functions are required, a PWM signal (provided by an external microcontroller or similar device) or an analog IADJ pin can be used to meet this requirement.
On the other hand, LM3409 has two effective monitoring current loops, one is set at the high-end current sensing resistor RSNS, and the other is directly at ISENS. Designers have three ways to achieve analog dimming via ISENS. The first is to open ISENS to allow RSNS to control the LM3409. The second is to provide an external voltage from 0 to 1.24 volts to the pin (1.2 volts is the maximum output when set by RSNS). Or a voltage divider can be connected from the pin to ground to vary the current (always setting RSNS to maximum).
Through the above three methods, after the AC power is converted into DC power, it can be easily connected to the main input rail through the voltage divider; however, if the voltage divider is selected at 1.24 volts, the maximum input voltage can be obtained (16.97V for 12VAC system and 33.94V for 24VAC system). Therefore, when the input voltage is lower, a lower light output will naturally be generated.
What is worth discussing is the difference between this situation and the driver without a typical dimming device, or how the LM3409 will perform without this connection.
Since the above cases are for DC-to-DC regulators, there will be a natural change from input to output, and in view of this, the idea of controlling a fixed voltage or current comes into being. For example, if no dimming signal is provided, the circuit will try to maintain the current specification until the input voltage is close to the output voltage (LED driving voltage), and the output level will not change until the input enters the circuit signal loss region (usually when driving current in buck regulator operation, the input voltage is higher than the required output). When the input voltage begins to drop, the output voltage also decreases rapidly.
In contrast, under the regulation of the PFET controller, the LM3409 has only a small range of changes and can maintain very low losses throughout the entire duty cycle. Its use of analog dimming can linearly reduce the LED current, making the LED design dimmable and reaching the undervoltage lockout setting before the switch is turned off (or the LED can be driven with a very small output voltage). The dimming function is achieved by changing the voltage, which can effectively control the input line. However, at the front end of the AC to DC converter, additional capacitors are required to minimize the input ripple caused by the light source output.
Additionally, by directly linking the dimming function to the input voltage, the LED driver stability is not a concern. Unless adequately filtered, any transient state of the input line will show up on the output. Therefore, this connection is less favored unless the dimming function is required, leaving IADJ open.
On the other hand, low voltage TRIAC dimming devices can also present design challenges. Low voltage dimming systems that use a voltage regulator transformer or reduce the peak of the AC low voltage waveform can work well if similar circuits are used, but TRIAC dimming systems require additional circuitry to properly decode the chopped waveform. Low
voltage AC systems combined with LED lighting solutions are all-inclusive
In summary, low voltage AC systems combined with LED lighting performance can provide designers with the ability to create a wide range of lighting solutions from small to large. National Semiconductor has a wide range of products for 24VAC and 12VAC systems to help realize their designs. With a wide range of product lineups, the decision of which solution to use depends on the features of the components and the required solution size.
It is particularly important to note that the overall system design must be based on some of the characteristics and progress of today's drivers in order to make the right decisions and make the design simpler, more robust and cost-effective. Having complete solution knowledge will further enable fast and cost-effective solutions, and give designers many options available.
Not only that, low-voltage AC LEDs also provide stable circuit analysis in terms of simplified design. These advantages can save design time and money, while also improving product reliability.
Previous article:Comparative Analysis: A60 LED Bulb Market Analysis
Next article:LED constant current drive precise control
Recommended ReadingLatest update time:2024-11-16 15:27
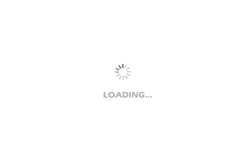
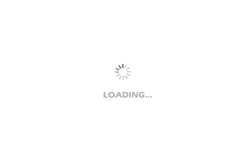
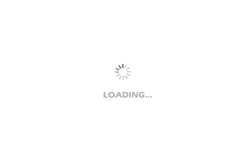
- Popular Resources
- Popular amplifiers
- MathWorks and NXP Collaborate to Launch Model-Based Design Toolbox for Battery Management Systems
- STMicroelectronics' advanced galvanically isolated gate driver STGAP3S provides flexible protection for IGBTs and SiC MOSFETs
- New diaphragm-free solid-state lithium battery technology is launched: the distance between the positive and negative electrodes is less than 0.000001 meters
- [“Source” Observe the Autumn Series] Application and testing of the next generation of semiconductor gallium oxide device photodetectors
- 采用自主设计封装,绝缘电阻显著提高!ROHM开发出更高电压xEV系统的SiC肖特基势垒二极管
- Will GaN replace SiC? PI's disruptive 1700V InnoMux2 is here to demonstrate
- From Isolation to the Third and a Half Generation: Understanding Naxinwei's Gate Driver IC in One Article
- The appeal of 48 V technology: importance, benefits and key factors in system-level applications
- Important breakthrough in recycling of used lithium-ion batteries
- Innolux's intelligent steer-by-wire solution makes cars smarter and safer
- 8051 MCU - Parity Check
- How to efficiently balance the sensitivity of tactile sensing interfaces
- What should I do if the servo motor shakes? What causes the servo motor to shake quickly?
- 【Brushless Motor】Analysis of three-phase BLDC motor and sharing of two popular development boards
- Midea Industrial Technology's subsidiaries Clou Electronics and Hekang New Energy jointly appeared at the Munich Battery Energy Storage Exhibition and Solar Energy Exhibition
- Guoxin Sichen | Application of ferroelectric memory PB85RS2MC in power battery management, with a capacity of 2M
- Analysis of common faults of frequency converter
- In a head-on competition with Qualcomm, what kind of cockpit products has Intel come up with?
- Dalian Rongke's all-vanadium liquid flow battery energy storage equipment industrialization project has entered the sprint stage before production
- Allegro MicroSystems Introduces Advanced Magnetic and Inductive Position Sensing Solutions at Electronica 2024
- Car key in the left hand, liveness detection radar in the right hand, UWB is imperative for cars!
- After a decade of rapid development, domestic CIS has entered the market
- Aegis Dagger Battery + Thor EM-i Super Hybrid, Geely New Energy has thrown out two "king bombs"
- A brief discussion on functional safety - fault, error, and failure
- In the smart car 2.0 cycle, these core industry chains are facing major opportunities!
- The United States and Japan are developing new batteries. CATL faces challenges? How should China's new energy battery industry respond?
- Murata launches high-precision 6-axis inertial sensor for automobiles
- Ford patents pre-charge alarm to help save costs and respond to emergencies
- New real-time microcontroller system from Texas Instruments enables smarter processing in automotive and industrial applications
- C5517 FFT hardware accelerator performs calculations sometimes well and sometimes poorly
- Antenna Aperture Tuning eBook
- Burn dtb file separately
- Talk about the future applications of drones and get points for speaking up
- How is the 0-10V/4-20mA input and output circuit of the inverter usually implemented?
- The editor you've been complaining about for a long time has been updated~
- MSP FRAM MCUs Reduce Volatility for the IoT
- MSP430 FAQ: Instruction System
- Repair a Bull socket
- CC1310 Two-wire Serial Bootloader Solution