Solar energy is an inexhaustible clean energy. With global environmental pollution and energy crisis becoming increasingly serious, research on solar energy utilization is of great significance to alleviate the energy crisis, protect the ecological environment and ensure the sustainable development of the economy. At present, my country's photovoltaic technology is still far behind that of advanced countries in the world, and the operating cost of building a large independent photovoltaic power station is high. Therefore, it is urgent to develop a household photovoltaic grid-connected system. In addition, among household energy consumption, air conditioning consumes a lot of electricity in summer, and the load is peaked during the day, and the law of load change is very consistent with the output of solar cells. It plays a peak-leveling role for the city power supply system. Therefore, based on this feature of the air conditioner, this paper proposes a design idea of combining household photovoltaic power generation system with air conditioning. Its working principle is to convert solar energy into electrical energy and send it to the air conditioner, which in turn powers the air conditioner. When the air conditioner is turned off, the electrical energy of the solar cell can also be fed back to the power grid, so that solar energy can be fully utilized. In the process of solar energy transfer, this paper introduces the maximum power point tracking method to keep the photovoltaic array at the maximum output power. This method is analyzed in detail in the article. There is not much research on solar air conditioning systems in China, but based on foreign market information, I believe that there will be broad application prospects in China in the future.
Working principle of photovoltaic power generation system
System composition
The main circuit of the system is shown in Figure 1.
|
For the entire system, the power consumption of the air conditioner can be supplied by both the photovoltaic array and the grid. The grid-connected inverter converts the DC power generated by the photovoltaic array into AC power with the same frequency and phase as the grid voltage to supply power to the air conditioner. During the day, when the AC power generated by the photovoltaic system exceeds the power required by the air conditioner, the excess is fed to the grid; at other times, when the AC power generated by the air conditioner is greater than the AC power generated by the photovoltaic system, the grid automatically provides supplementary power to the load.
Figure 1 is the main circuit diagram of the photovoltaic power generation system, which mainly consists of two parts. The first part is the Buck-Boost converter working in discontinuous mode, and the second part is the inversion process. In the photovoltaic power generation circuit, the Buck-Boost converter consists of S1, S2, Lp and D1. Its function is to shape the output current io in combination with maximum power point tracking. Li and Ci act as input filters to smooth the input current. The inverter output current iac serves as the input current to the air conditioner power supply circuit. Maximum power point tracking is completed based on the switching frequency modulation of S1.
In the Buck-Boost circuit, when S1 is turned on, S2 and D1 are turned off, and Lp stores energy. When S1 is turned off, D1 and S2 are turned on, and the energy stored in Lp and Cdc will be transferred to the output. During the switching period Ts, the switching of S2 is controlled by comparing the relationship between io and the given current i'ac,reg.
Lp acts as a buffer for temporary energy storage. If the output power of the photovoltaic array is higher than the power absorbed by the air conditioner, the energy stored in Lp will be transferred to Cdc through LS and D2 after S2 is turned off. The average voltage of Cdc is equivalent to half of the peak voltage of Vac. Cdc is used to correct i'ac,reg and i0. Therefore, the connection between Lp and Cdc plays a role in current shaping and reducing the voltage stress on Cdc in the process of transmitting energy to the charging circuit. In the inverter process, the inverter is composed of SA, SB, SC and SD. SA and SB are turned on in the positive half cycle of the AC voltage, and SC and SD are turned on in the negative half cycle of the AC voltage. When S2 and D1 are turned on, the current difference between L2 and is absorbed by C1, and L4 is used to filter out the high-frequency current components transmitted to the air conditioner to achieve a smooth sine wave output by the inverter.
Output characteristics of photovoltaic cells
In the photovoltaic power generation system, solar cells directly convert solar energy into electrical energy. The output of solar cells is determined by many factors, such as sunshine conditions, temperature, etc. In different environments, the output curve of solar cells is different, and the corresponding maximum power point is also different. The stronger the sunshine, the greater the power that the solar cell can output. The temperature is just the opposite. The higher the temperature of the solar cell itself, the smaller the power that the solar cell can output. Its output has nonlinear characteristics. Figure 2 shows the output characteristic curve of the solar cell. Figure 2 (a) is the curve of U, I and sunshine (S) of the solar cell when the solar cell temperature is 25℃. It can be seen from the figure that the power at any point on the curve is P=UI. Its value is related to U and I as well as sunshine (S), solar cell temperature, etc. It can be further known from Figure 2 (b) that since the working efficiency of the solar cell is equal to the ratio of the output power to the power projected on the solar cell area, in order to improve the working efficiency of this system, the solar cell must be operated at the maximum power point as much as possible, so that the maximum power output can be obtained with the solar cell with the smallest power possible. In Figure 2, points A, B, C, D, and E correspond to the maximum power points at different sunshine times.
|
Maximum power point tracking of solar cells
The maximum power point tracking of solar cells is to make full use of solar energy so that the solar cells always output the maximum power. The MPP tracking of solar cells is based on the modulation of the switching frequency S1. The PWM signal of switch S1 is modulated by a low-frequency signal. The model of the solar cell can be equivalent to the circuit in Figure 3.
|
Vg is the power source, rg is the internal resistance of the battery, both Vg and rg are affected by the intensity of sunlight and temperature, and the input voltage and input resistance of the converter are represented by Vin and rin. Assume 100% conversion efficiency.
2.4 Hardware Implementation of the System The controller here uses TI's DSP chip TMSLF2407. This DSP chip is a high-speed dedicated microprocessor that maintains the characteristics of a general microprocessor system and has a better computing ability for digital signal processing than a general microprocessor. It uses an improved Harvard structure, multiple bus technology to achieve a parallel operation mechanism, a special multiplier-accumulator structure, and provides a very flexible instruction system, all of which greatly increase the computing speed and improve the flexibility of the system. To this end, his tasks mainly include the following aspects:
(1) Collect analog quantities such as DC, AC voltage and battery voltage for monitoring and control;
(3) Conduct real-time interactive communication with the human-machine interface to receive and send system status parameters that need to be displayed; (4) Receive over-current and over-voltage protection signals provided by power devices to realize automatic protection function. The hardware block diagram of the system is shown in Figure 4:
3 Simulation Results Based on the theoretical research of maximum power point tracking mentioned above, in order to verify the correctness of the scheme, Matlab software is used to simulate and analyze the photovoltaic power generation circuit. ode23tb simulation with variable step size is used. The simulation starts from 0 s and the simulation time is set to 0.1 s. The sampling period of the maximum power point tracking module is 0.001. The input sunshine of the solar photovoltaic array is 100 W/m2, and the battery temperature is 25℃. After setting the simulation parameters of each module, simulation can be performed. Figure 5 shows the voltage and current waveforms of the photovoltaic power generation system with MPPT after it is converted into AC power through the inverter and then output through the isolation transformer. The voltage is 120 V/div and the current is 0.5 A/div. It can be seen from the figure that the AC voltage and current have good sinusoidal waveforms and the power factor is close to 1.
4 Conclusion The design of the maximum power tracking function, especially in situations where the temperature difference changes greatly, can effectively increase the output power of solar cells and make full use of energy. The simulation results also show that the design of the photovoltaic power generation circuit has good stability, thus verifying the correctness of the scheme. And because of the use of TMS320F2407 control, the controllability of the entire system is improved, and the control relationship between the front and rear levels can be better coordinated. |
Previous article:The time has come for 100% efficient power supplies
Next article:Application of large screen LCD in torque limiter
Recommended ReadingLatest update time:2024-11-17 02:56
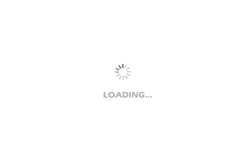
- MathWorks and NXP Collaborate to Launch Model-Based Design Toolbox for Battery Management Systems
- STMicroelectronics' advanced galvanically isolated gate driver STGAP3S provides flexible protection for IGBTs and SiC MOSFETs
- New diaphragm-free solid-state lithium battery technology is launched: the distance between the positive and negative electrodes is less than 0.000001 meters
- [“Source” Observe the Autumn Series] Application and testing of the next generation of semiconductor gallium oxide device photodetectors
- 采用自主设计封装,绝缘电阻显著提高!ROHM开发出更高电压xEV系统的SiC肖特基势垒二极管
- Will GaN replace SiC? PI's disruptive 1700V InnoMux2 is here to demonstrate
- From Isolation to the Third and a Half Generation: Understanding Naxinwei's Gate Driver IC in One Article
- The appeal of 48 V technology: importance, benefits and key factors in system-level applications
- Important breakthrough in recycling of used lithium-ion batteries
- Innolux's intelligent steer-by-wire solution makes cars smarter and safer
- 8051 MCU - Parity Check
- How to efficiently balance the sensitivity of tactile sensing interfaces
- What should I do if the servo motor shakes? What causes the servo motor to shake quickly?
- 【Brushless Motor】Analysis of three-phase BLDC motor and sharing of two popular development boards
- Midea Industrial Technology's subsidiaries Clou Electronics and Hekang New Energy jointly appeared at the Munich Battery Energy Storage Exhibition and Solar Energy Exhibition
- Guoxin Sichen | Application of ferroelectric memory PB85RS2MC in power battery management, with a capacity of 2M
- Analysis of common faults of frequency converter
- In a head-on competition with Qualcomm, what kind of cockpit products has Intel come up with?
- Dalian Rongke's all-vanadium liquid flow battery energy storage equipment industrialization project has entered the sprint stage before production
- Allegro MicroSystems Introduces Advanced Magnetic and Inductive Position Sensing Solutions at Electronica 2024
- Car key in the left hand, liveness detection radar in the right hand, UWB is imperative for cars!
- After a decade of rapid development, domestic CIS has entered the market
- Aegis Dagger Battery + Thor EM-i Super Hybrid, Geely New Energy has thrown out two "king bombs"
- A brief discussion on functional safety - fault, error, and failure
- In the smart car 2.0 cycle, these core industry chains are facing major opportunities!
- Rambus Launches Industry's First HBM 4 Controller IP: What Are the Technical Details Behind It?
- The United States and Japan are developing new batteries. CATL faces challenges? How should China's new energy battery industry respond?
- Murata launches high-precision 6-axis inertial sensor for automobiles
- Ford patents pre-charge alarm to help save costs and respond to emergencies
- PLDFPGA structure and principle introduction.pdf
- [Xingkong Board Python Programming Learning Main Control Board] Electronic photo album based on Xingkong Board
- GND copper pour settings are set to pour over all same net objects, but there are still a few GND net pads that cannot be poured.
- 28 "Wanli" Raspberry Pi car - car assembly
- [Xingkong Board Python Programming Learning Main Control Board] 1. Unboxing Hardware Appreciation and Mind+ Environment Construction
- EEWORLD University ---- Micro-Nano Processing (Semiconductor Manufacturing Technology) Swiss Federal Institute of Technology
- FPGA Design Code Cleanliness 2
- Overview of multi-string battery protection chip manufacturers
- Implementation of PID Control Algorithm Based on DSP
- Confused about measuring tantalum capacitors with a digital multimeter?