As for the new version of the solid-state lighting standard of the "Energy Star", an important feature of this standard is that it requires a minimum power factor of 0.7 for a variety of residential lighting products, some of which are typical products such as portable table lamps, cabinet lights and outdoor corridor lights. The power of this type of LED lighting application is generally between 1 and 12W, which is a low-power application. The most suitable power supply topology for this type of low-power application is the isolated flyback topology. Unfortunately, the standard design techniques used to design these power supplies typically result in a power factor (PF) in the range of 0.5 to 0.6. This article will analyze the reasons why the existing designs have low power factors, explore the techniques and solutions to improve the power factor, introduce the relevant design process and share some test data to show how this reference design can easily meet the power factor requirements of the "Energy Star" solid-state lighting specification for residential LED lighting applications.
Design Background
A typical offline flyback power converter uses a full-wave bridge rectifier and a large capacitor in front of the switching regulator. This configuration is chosen because the line power decreases to zero every 2 line cycles and then rises to the next peak. The large capacitor acts as an energy storage element to fill the corresponding missing power and provide a more constant input to the switching regulator to maintain power flow to the load. This configuration has a low power utilization or power factor of the input line waveform. The line current is consumed in large and narrow pulses close to the peak of the voltage waveform, introducing interfering high-frequency harmonics.
There are many passive power factor correction (PFC) solutions in the industry, which usually use more additional components. One of the solutions is the valley-fill rectifier, in which the combination of electrolytic capacitors and diodes increases the line frequency conduction angle, thereby improving the power factor. In fact, this process uses high line voltage to charge the series capacitors with low current, and then discharges the capacitors to the switching regulator with a larger current at a lower voltage. Typical applications use 2 capacitors and 3 diodes, while to further enhance the power factor performance, 3 capacitors and 6 diodes are used.
Figure 1: Typical valley-fill circuit.
Although the valley-fill rectifier improves the utilization of the line current, it does not provide a constant input to the switching regulator. The power delivered to the load will have a large ripple, up to twice the line frequency. It should be noted that four diodes are still required to rectify the line power, bringing the number of diodes used in this solution to seven or ten. These diodes and multiple electrolytic capacitors increase the solution cost, reduce reliability, and occupy considerable board area.
Another solution is to use an active PFC stage before the flyback converter, such as the NCP1607B. This solution provides excellent power factor with typical performance of better than 0.98, but increases component count, reduces efficiency and increases complexity, and is best used at power levels much higher than the power level of this application.
Solution
High power factor usually requires a sinusoidal line current with a very small phase difference between the line current and voltage. The first step in modifying the design is to obtain very low capacitance before the switching stage, resulting in a more sinusoidal input current. This allows the rectified voltage to follow the line voltage, resulting in a more ideal sinusoidal input current. Thus, the input voltage to the flyback converter follows the rectified sinusoidal voltage waveform at twice the line frequency. If the input current is maintained at the same waveform, the power factor is high. The energy delivered to the load is the product of the voltage and current, a sine-squared waveform. Due to this sine-squared energy transfer, the load will see a ripple at twice the line frequency, similar in nature to the ripple seen in valley-fill circuits.
As mentioned above, the input current must be maintained at a nearly sinusoidal waveform to achieve a high power factor. The key to a high power factor is to not allow the control loop to correct for output ripple by maintaining the feedback input at a constant level related to the line frequency. One option is to significantly increase the output capacitance, thereby reducing the amount of 120Hz ripple, which may be required for some applications. LEDs for general lighting applications are more tolerant of ripple if the frequency is above the range of visible light perception. A more compact and inexpensive solution is to filter the feedback signal back to the PWM converter to establish a nearly constant level. This level fixes the maximum current in the power switch. The current of the power switch is determined by the applied transient input voltage divided by the transformer primary inductance multiplied by the length of the power switch on time.
ON Semiconductor's NCP1014LEDGTGEVB evaluation board is optimized to drive 1 to 8 high-power, high-brightness LEDs, such as CreeRebel, SeoulSemiconductorZ-Power®, or OSRAMGoldenXR-E/XP-E, Luxeon™XLAMP®Dragon™. The design is based on the NCP1014, a compact fixed-frequency pulse-width modulation (PWM) converter that integrates a high-voltage power switch with internal current limiting. Because the NCP1014 operates at a fixed frequency, the current cannot rise above a certain point; this point is determined by the input voltage and the primary inductance before the end of the switching cycle or on-time. Due to the on-time limitation, the input current will follow the waveform of the input voltage, providing a higher power factor. The relevant circuit diagram is shown in Figure 2.
Figure 2: NCP1014LEDGTGEVB circuit diagram
Previous article:High-efficiency 28V, 3.3A LED driver design for LED street lighting applications
Next article:13W Off-line High Power Factor TRIAC Dimmable LED Downlight Design Example
Recommended ReadingLatest update time:2024-11-16 21:03
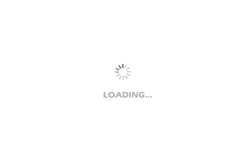
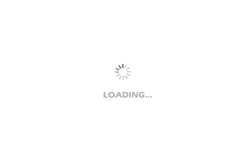
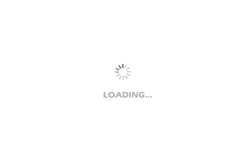
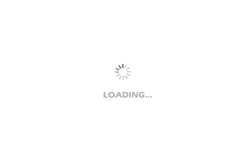
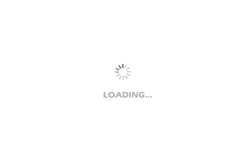
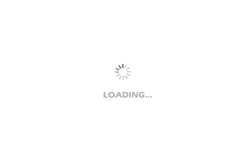
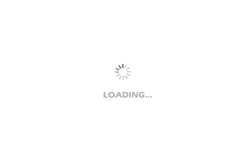
- Popular Resources
- Popular amplifiers
-
MCU C language programming and Proteus simulation technology (Xu Aijun)
-
100 Examples of Microcontroller C Language Applications (with CD-ROM, 3rd Edition) (Wang Huiliang, Wang Dongfeng, Dong Guanqiang)
-
Research on three-phase all-solid-state high-efficiency LED tunnel lighting system based on chip drive_Li Jian
-
Follow me Season 2 Episode 1 All Code + Library
- MathWorks and NXP Collaborate to Launch Model-Based Design Toolbox for Battery Management Systems
- STMicroelectronics' advanced galvanically isolated gate driver STGAP3S provides flexible protection for IGBTs and SiC MOSFETs
- New diaphragm-free solid-state lithium battery technology is launched: the distance between the positive and negative electrodes is less than 0.000001 meters
- [“Source” Observe the Autumn Series] Application and testing of the next generation of semiconductor gallium oxide device photodetectors
- 采用自主设计封装,绝缘电阻显著提高!ROHM开发出更高电压xEV系统的SiC肖特基势垒二极管
- Will GaN replace SiC? PI's disruptive 1700V InnoMux2 is here to demonstrate
- From Isolation to the Third and a Half Generation: Understanding Naxinwei's Gate Driver IC in One Article
- The appeal of 48 V technology: importance, benefits and key factors in system-level applications
- Important breakthrough in recycling of used lithium-ion batteries
- Innolux's intelligent steer-by-wire solution makes cars smarter and safer
- 8051 MCU - Parity Check
- How to efficiently balance the sensitivity of tactile sensing interfaces
- What should I do if the servo motor shakes? What causes the servo motor to shake quickly?
- 【Brushless Motor】Analysis of three-phase BLDC motor and sharing of two popular development boards
- Midea Industrial Technology's subsidiaries Clou Electronics and Hekang New Energy jointly appeared at the Munich Battery Energy Storage Exhibition and Solar Energy Exhibition
- Guoxin Sichen | Application of ferroelectric memory PB85RS2MC in power battery management, with a capacity of 2M
- Analysis of common faults of frequency converter
- In a head-on competition with Qualcomm, what kind of cockpit products has Intel come up with?
- Dalian Rongke's all-vanadium liquid flow battery energy storage equipment industrialization project has entered the sprint stage before production
- Allegro MicroSystems Introduces Advanced Magnetic and Inductive Position Sensing Solutions at Electronica 2024
- Car key in the left hand, liveness detection radar in the right hand, UWB is imperative for cars!
- After a decade of rapid development, domestic CIS has entered the market
- Aegis Dagger Battery + Thor EM-i Super Hybrid, Geely New Energy has thrown out two "king bombs"
- A brief discussion on functional safety - fault, error, and failure
- In the smart car 2.0 cycle, these core industry chains are facing major opportunities!
- The United States and Japan are developing new batteries. CATL faces challenges? How should China's new energy battery industry respond?
- Murata launches high-precision 6-axis inertial sensor for automobiles
- Ford patents pre-charge alarm to help save costs and respond to emergencies
- New real-time microcontroller system from Texas Instruments enables smarter processing in automotive and industrial applications
- Discrete components to build a transistor amplifier circuit, emitter follower circuit with suitable static operating point and wide input voltage range
- 【AT-START-F403A Review】3. Porting RTX operating system
- Problem with itoa function in embedded C language?
- HFSS simulation software field strength pattern and 3D diagram
- Contract issues
- Industrial 4-20mA Circuit
- c# System.Object class and safe transformation of data
- Please reinstate the invitation of 8 people, please, I beg you, I thought I would never give any suggestions again, I beg the maintenance staff on behalf of my boss
- Embedded software squeezes out the lowest power mode
- Sharing of experience in single board circuit design (2) -- Power socket selection