Key factors for automotive LEDs are their relative resistance to vibration, long life, high energy efficiency and the ability to finely control the light source. LEDs are less sensitive to mechanical shock than incandescent bulbs, but require a drive circuit. Typically, the automotive electrical supply system is powered by a lead-acid battery that is charged by the engine through an alternator/regulator that is mechanically driven. Such a system works well for old incandescent bulbs, but not for LEDs. To achieve optimal performance from LEDs, a precise, constant current source is required. To
properly drive an LED, the current must be controlled regardless of the voltage. Light output is primarily determined by current, not voltage. In theory, every electron is converted to a photon , and a fixed fraction of the photons that escape the LED become the light we see.
If the voltage is constant, a low-quality solution can be achieved with just one resistor. It should be noted that the LED itself is somewhat self-regulating when simply connected in series with a resistor. If the temperature rises, the LED's efficiency and brightness decrease, and the forward voltage drop also decreases. The reduced forward voltage drop in turn results in an increase in current,
which somewhat compensates for the decrease in brightness due to the temperature rise. As long as the battery voltage is constant, the series resistor solution is sufficient for computer and instrumentation applications. However, the automotive industry mandates that the device can cope with battery variations between 8V and 18V, and also tolerate 80V peaks. In addition, high-brightness LEDs generate a lot of heat in the resistor. This makes thermal design more difficult.
A better, but not optimal, alternative is to use a dc-dc voltage converter to generate a suitable regulated voltage and then combine this with a resistor. This solution is feasible if you already have a dc-dc converter to power a computer or other electronic device, and this method is probably the most common way to drive an LED. However, it is better to drive the LED with a constant current device that operates independently of the voltage. Energy dissipation and energy conversion are two basic types of current regulators.
A linear buck current regulator is an example of an energy dissipation type of current regulator. For a given current, the energy represented by the voltage drop across the current regulator is consumed. On the other hand, an energy conversion current regulator attempts to store the difference in energy between different levels. The
equation used to describe this energy conversion is one of the basic laws of thermodynamics:
· Input Power = Output Power
· Substitute W = V·I given (given) for W:
· Vin·Iin = Vout·Iout + (100-X% efficiency)W heat (heat)
If the forward voltage of the LED is taken as Vout and the required current as Iout, the general equation describing the LED driver is obtained.
Energy dissipation LED driver It is relatively simple to build a linear current regulator with discrete components. Figure 1 shows a current regulator built with discrete components. D1 should be a Zener diode or a voltage reference. The current is determined by the equation ILED = VD1/RSET. D2 provides simple temperature compensation for the transistor base diode.
Although the circuit is simple, like all power-consuming LED drivers, there are problems with energy consumption and heating caused by the resistors. As the brightness of the LED increases, the heating becomes more and more serious. The brighter the LED is, the more energy is wasted.
This type of current regulation can be used when the current is small and the sum of the forward voltages of the LEDs in series is slightly lower than the supply voltage. Several LED driver
IC
manufacturers use this constant current method. However
, this method is not recommended when
driving
high-brightness LEDs
.
Energy-saving LED drivers
In many cases,
a switching
constant current device can provide a better electronic solution. The switching constant current device controls the on/off of a series load, which is why it is named. During one cycle, the RLC (tank circuit) circuit is charged. In the next cycle, the stored energy is used to drive the load or to increase the voltage level of the energy center that drives the load. This energy arrangement generally achieves efficiencies above 80%, and in most cases it can reach more than 90%. Therefore, the switching constant current device can be used to increase the voltage, decrease the voltage or even reverse the voltage. Linear constant current devices do not have these capabilities.
Working description: The voltage difference between the input voltage and the LED voltage charges the coil L. When energy is accumulated in the coil, the voltage above it will drop and the current will increase. When the current reaches a specified value, the control circuit will turn off the transistors in sequence. Then, during a certain off time, part of the energy in the coil will power the LED. This results in an overlapping current flowing through the LED. The switching current regulator circuit controls the peak value of the current. This value can be set by programming the current regulator IC or by external components. The current also depends on the choice of the sense resistor at the drain end of the NFET switch.
In the buck current regulator application, the current flowing through the LED is continuous but overlapping. The energy consumption of the entire circuit is discontinuous (Figure 2). It can cause problems on the power supply input side and easily induce noise through the power supply line.
Boost regulator
If the supply voltage is lower than the sum of the forward voltages of all series-connected LEDs, a boost current regulator is used. This type of current regulator is more complex because it has to control the boosted voltage in addition to the current.
This boost current regulator cannot handle the situation where the supply voltage is higher than the sum of the forward voltages of all series-connected LEDs. When this happens, the current increases sharply and uncontrollably, as shown in Figure 3.
This LED driver will also generate a pulsating current through the LED. Since the current through the LED is relatively large, it is difficult to filter out. In principle, a simple boost current regulator will generate more noise on the current output to the LED. Therefore, when
routing
the PCB
, keep the connection between the driver and the LED as short as possible.
SEPIC Current Regulator
The SEPIC current regulator is a single-ended primary
inductor
converter. This current regulator can be used as both a boost and a buck. However, the capacitive reactance between the coils is a drawback. The capacitor must handle all the energy converted into current and voltage for the LED.
This type of current regulator comes in handy when you basically need a buck current regulator and there may be overvoltage on the power supply line.
Boost/Buck Current Regulator
The most reliable and safest solution for a good boost LED driver is to combine a boost current regulator and a buck current regulator in cascade. This architecture minimizes the work required for optimization. A boost current regulator is more suitable for providing power to several buck current regulators in parallel. Lighting Engineer Community
对降低噪声来说,这种作法还是种成效显著的解决之道。它集升压恒流器优异的电压输出与降压恒流器同样优异的电流输出双美于一身。
由高压驱动LED
当电源电压很高,而LED的前向压降(Vf)与之相比要低10到20倍时,会出现由对与LED串接在一起的线圈极短的充电时间引发的问题。快速充电(和放电)将导致低效率。
充放电周期如图4所示,可容易地看出:上升时间(频率)比恒流的基本频率高10到20倍。
One of the most effective ways to achieve high efficiency and reduce radiated noise is to choose a switching frequency so that the rise time is comparable to the rated frequency of the coil. When the voltage difference is 10 to 20 times, the switching frequency should be chosen 10 to 20 times lower than the most efficient frequency of the coil.
However, an optimal solution is obtained when the supply voltage is twice the forward voltage of the series LED.
The regulated current is shown in Figure 5, where the waveform is quite symmetrical.
With the advantage of its independence from the supply voltage and the high isolation between the supply voltage and the LED current, the coil can also be used as a transformer. It can replace step-up and step-down solutions, but the efficiency is not high. The strong magnetic coupling between the primary and secondary windings of the inductor will improve the efficiency. It has the following advantages: any wire connected to the LED can be shorted to ground or the supply without any dangerous current.
Electrical noise generated by switching current regulators
All switching current regulators generate noise. Common dc-dc voltage regulators that rely on controlling the voltage level can obtain a well-filtered power supply. This is achieved by adding a large capacitor at the output and increasing the switching frequency to improve efficiency. LED current regulators should use constant current rather than voltage regulation.
The buck regulator mentioned earlier is a simple and cost-effective regulator, but will generate significant electrical noise in LED applications if the physical implementation is not well arranged. The PCB layout and the selected cables are critical to controlling the noise level.
General rules for reducing noise:
1. Reduce the switching frequency.
2. Keep the wires to the LED short and the current loop small.
3. If long wires are required to connect the LED, add noise filters.
4. Use high-speed feedback diodes.
5. Place the switching transistor in the center of the PCB.
6. Carefully select the cables used for the power supply lines and add noise filters.
In addition to these general rules, Melexis also takes steps to help control the noise of the driver IC. In the MLX10801 and MLX10803 drivers, a pseudo-random number generator is used for the switching frequency to minimize electrical noise.
In
the
automotive electronics
environment, there are several
tests
and test procedures to evaluate the relative noise performance of electronic modules. A commonly used standard and test procedure is
defined by the International Electrotechnical Commission (IEC) branch International Committee on Radio Interference (CISPR).
Figure
6 is a simple schematic for a low-noise application that meets CISPR25 Class 5 requirements. The shape and size of coil L1 must be determined based on the switching frequency and LED current. To do this, we can use a software program and Excel spreadsheet that can be downloaded from www.melexis.com. The switching frequency should be lower than 150kHz to avoid the lowest frequency band required by CISPR25. The program also provides ROSC, RSET, and RSENSE values. L2 is part of a noise filter that is required when passing the highest level of noise reduction requirements. For CISPR25 Classes 1 to 3, coil L2 can be omitted.
When using the circuit in Figure 6, it is a good idea to choose L1 and L2 to be 100μH for typical LED currents of 0.5 to 1A. Because the noise spectrum is very wide, the capacitor should be able to handle both high and low frequencies. This is why we place two sets of capacitors on both ends of the filter coil L2. The feedback diode D1 is the main source of high frequency noise. This diode should be carefully selected and tested repeatedly in the application. For input voltages below 100V, a Schottky diode is the best choice.
More information and help on how to optimize the design can be found in the Melexis website forum "Knowledge Base".
Temperature compensation of LEDs
Red and yellow gallium arsenide (GaAs) and gallium arsenide phosphide (GaAsP) LEDs have a large change in light output depending on the junction temperature. Typically, an LED with 100% light output at 25°C will only have 40% light output at 80°C. This change in light output can be easily compensated. The improved low noise design only requires the addition of a PTC and NTC resistor (Figure 7).
As shown in Figure 8, using temperature compensated PTC and NTC resistors, the relative light output is maximized at 80°C. If, for whatever reason, the junction temperature drops below 80°C, the PTC resistor will become a relatively low value and proportionally reduce the current. Thus, a balance needs to be struck between the PTC coefficient and the LED light output.
For protection, an NTC resistor at the other reference input of the MLX10803 reduces the current in the same way when the temperature is above 80°C.
LED Applications for Brake, Turn and Tail Lights
Today, almost all cars use red GaAs LED taillights. However, most LED taillights are too bright on cold nights and too dim in hot and bright places. Many years ago, the legal standards governing automotive lighting were based on incandescent lamps. Incandescent lamps operate under conditions where the filament heats up to several thousand degrees to emit light. Therefore, the difference in light output is basically unnoticeable even if the ambient temperature varies by 60°C (between 20 and 80°C). At present, the difference in brightness between LED taillights and incandescent taillights is obvious on cold days. It is questionable whether LEDs are too bright on cold days. The temperature compensation method described previously will give the car a more professional and sophisticated lighting appearance, and will look even better when used in combination with incandescent lamps. This situation may become an issue to be addressed by standards organizations, which need to establish reference specifications for lamps operating at different temperatures.
In applications that combine the brake and taillight functions, pulse width modulation (
PWM
) is used to produce two levels of lighting: one for the taillight and the other for the brakelight. This is because LED manufacturers generally test and classify their LEDs at only one current value (the driving current value used to produce the brake light effect). In the past, there was no testing and classification for the low light output of taillights. Fortunately, this situation is changing, and LUMILEDs now test LEDs at two current levels.
This is important because if the LED can match two current levels, the driver can alternate between driving two specific current levels without the need for PWM, and then PWM is no longer needed. LED taillights driven by PWM methods, when the PWM ratio is from 1:10 to 1:20 and the frequency is from 80Hz to 100Hz, the light they produce looks uncomfortable compared to traditional incandescent lamps. This is because the human eye is sensitive to red light and these frequencies. This is more severe in cold environments and when current compensation is not in place due to cold environments.
Summary of this article
Several ICs and application circuits based on specific occasions have been developed
to achieve more sophisticated automotive
LED lighting
applications. In the previous examples, how to deal with these challenges was discussed. In order to successfully develop a lighting module that is completely used for a specific application, more fine-tuning than the measures mentioned here is required. The above general discussion should help to better understand the various constraints in the realization of lighting projects, and with this understanding,
more reliable and more pleasant lighting solutions
can
be designed with current high-brightness LEDs
.
Previous article:LED wafer (epitaxial) growth process
Next article:LED production process and packaging steps
Recommended ReadingLatest update time:2024-11-16 23:51
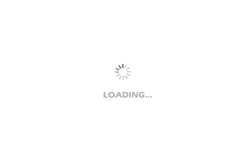
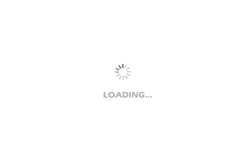
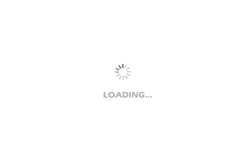
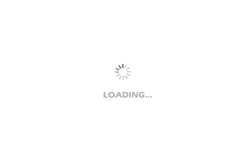
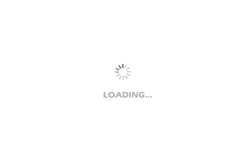
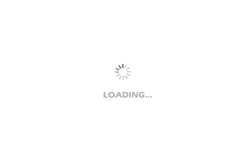
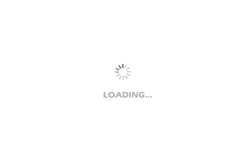
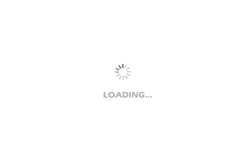
- Popular Resources
- Popular amplifiers
- MathWorks and NXP Collaborate to Launch Model-Based Design Toolbox for Battery Management Systems
- STMicroelectronics' advanced galvanically isolated gate driver STGAP3S provides flexible protection for IGBTs and SiC MOSFETs
- New diaphragm-free solid-state lithium battery technology is launched: the distance between the positive and negative electrodes is less than 0.000001 meters
- [“Source” Observe the Autumn Series] Application and testing of the next generation of semiconductor gallium oxide device photodetectors
- 采用自主设计封装,绝缘电阻显著提高!ROHM开发出更高电压xEV系统的SiC肖特基势垒二极管
- Will GaN replace SiC? PI's disruptive 1700V InnoMux2 is here to demonstrate
- From Isolation to the Third and a Half Generation: Understanding Naxinwei's Gate Driver IC in One Article
- The appeal of 48 V technology: importance, benefits and key factors in system-level applications
- Important breakthrough in recycling of used lithium-ion batteries
- Innolux's intelligent steer-by-wire solution makes cars smarter and safer
- 8051 MCU - Parity Check
- How to efficiently balance the sensitivity of tactile sensing interfaces
- What should I do if the servo motor shakes? What causes the servo motor to shake quickly?
- 【Brushless Motor】Analysis of three-phase BLDC motor and sharing of two popular development boards
- Midea Industrial Technology's subsidiaries Clou Electronics and Hekang New Energy jointly appeared at the Munich Battery Energy Storage Exhibition and Solar Energy Exhibition
- Guoxin Sichen | Application of ferroelectric memory PB85RS2MC in power battery management, with a capacity of 2M
- Analysis of common faults of frequency converter
- In a head-on competition with Qualcomm, what kind of cockpit products has Intel come up with?
- Dalian Rongke's all-vanadium liquid flow battery energy storage equipment industrialization project has entered the sprint stage before production
- Allegro MicroSystems Introduces Advanced Magnetic and Inductive Position Sensing Solutions at Electronica 2024
- Car key in the left hand, liveness detection radar in the right hand, UWB is imperative for cars!
- After a decade of rapid development, domestic CIS has entered the market
- Aegis Dagger Battery + Thor EM-i Super Hybrid, Geely New Energy has thrown out two "king bombs"
- A brief discussion on functional safety - fault, error, and failure
- In the smart car 2.0 cycle, these core industry chains are facing major opportunities!
- The United States and Japan are developing new batteries. CATL faces challenges? How should China's new energy battery industry respond?
- Murata launches high-precision 6-axis inertial sensor for automobiles
- Ford patents pre-charge alarm to help save costs and respond to emergencies
- New real-time microcontroller system from Texas Instruments enables smarter processing in automotive and industrial applications
- [ESP32-Audio-Kit Audio Development Board] - 2: Installing "esp-idf-v3.3.5" on Windows 10
- CC2640 Software Architecture
- Recruiting senior analysts in the electronics industry
- Qorvo's 5G Small Base Station
- Sensor Basics and Common Terms
- Introduction to the basic knowledge of lithium batteries (PPT)
- EEWORLD University - Understanding PID Control (English subtitles)
- Live broadcast registration with prizes [Microchip Embedded Security Solutions | Automotive Network Security]
- sensor
- Canaan-K510 kit version network usage and current difficulties