introduction
The tablet market is expected to grow from more than 50 million units this year to more than 200 million units in 2016. Despite this, there is still no standard tablet architecture. For example, some tablets are powered by a single lithium-ion battery, while others use two. Regardless of the number of batteries used, all tablet manufacturers want to maximize battery life. The display backlight is one of the most power-hungry systems in a tablet. Display sizes range from 7 inches to 10 inches. The number of backlight LEDs in recently released tablets ranges from 20 to 36. This article will guide readers on how to select the best WLED driver and LED string configuration to meet tablet application requirements without sacrificing efficiency and battery life.
Tablet backlight requirements
Like laptops or netbooks, tablet backlight driver applications are also based on DC/DC converters and grounded resistor paths for LEDs. This application generally has the following requirements:
1. Low EMI in RF range
2. No visible flicker during high brightness
3. Ceramic output capacitors have minimal audible noise caused by piezoelectric hum
4. Consistent display brightness
5. High dimming ratio
6. Highest efficiency, maximum battery life
Meeting the first requirement, low EMI in the RF range, is relatively easy. Power designers have been working to implement this goal for years, trying many methods, such as setting the switching frequency and subsequent harmonics outside the RF range, using shielded inductors, designing PCBs with minimal length but wider traces where appropriate, and so on. Some driver ICs have integrated MOSFET gate drive circuits with hierarchical rise times to reduce noise in the RF range.
The type of dimming greatly affects the next four requirements. When using pulse width modulation (PWM) dimming, the LED current is pulsed on and off at its maximum current level during the dimming process to produce an average DC LED current. In this case, backlight flicker is not as noticeable as long as the PWM dimming frequency is well above 60 Hz. If analog dimming is used, flicker is not a problem because the LED DC current level drops below its maximum value during dimming.
The third requirement, minimal audible noise from ceramic capacitors, is related to the driver topology. Figure 1 shows a simple driver with a current sense resistor as a path to ground for the LED current. The converter regulates the voltage across the current sense resistor, thereby controlling the LED current.
Figure 1: Simple LED driver
Figure 2 shows a driver for the integrated current sinks. The driver samples the voltage of each current sink and ensures that the converter can deliver just enough power to keep the current sinks operating properly.
As with blinking, this is not a problem when using analog dimming, because there is only a small change in the output capacitor voltage to accommodate small changes in LED current. However, if PWM dimming is used, the way the driver prevents the output capacitor from discharging becomes important. The simplest drivers also have a resistor from the driver feedback (FB) pin to ground, and the output capacitor begins to discharge sharply at low dimming duty cycles when the driver's converter is effectively turned off. More complex drivers integrate current sinks (as shown in Figure 2), which can replace the current sense resistor. They simply turn on the sink and the DC/DC converter that powers the LEDs, removing the discharge and recharge path for the output capacitor.
Figure 2: LED driver with integrated current sink
The fourth requirement, uniform display brightness, can be perfectly achieved by precisely matching the LED currents of all strings. The key feature of an integrated current sink driver is very precise matching between strings. For some drivers without an integrated current sink, ballast resistors are placed in series with the LEDs to improve the matching between strings.
The fifth requirement, high dimming ratio (e.g., 0.1%, or 1000:1), is difficult to achieve with a simple driver, whether using analog dimming or PWM dimming. When using analog dimming at low duty cycles, the analog control voltage becomes so low that the IC's leakage current and compensation voltage can significantly reduce accuracy. PWM dimming with a simple driver is the most common implementation, which is achieved by completely switching the converter. This dimming creates a converter soft-start time, forcing the PWM dimming frequency to be very low, close to the flicker range. The duty cycle causes the output capacitor to discharge and hum during the recharge period. Therefore, high dimming ratios are perfectly achieved with an integrated current sink because it can be switched very quickly.
The sixth and final requirement, high efficiency, is not only relevant to the driver, but also to the LED configuration. The power MOSFET, inductor, and rectifier diode of the driver DC/DC converter together determine the efficiency of the converter. The ground path of a simple driver is the current sense resistor. The lower the FB voltage of the converter, the higher the overall driver efficiency. Similarly, for a driver with an integrated current sink, the lower the minimum operating voltage of these sinks, the higher the efficiency of the driver. A simple driver will almost always be more efficient than a driver with a current sink, assuming that they have exactly the same internal components, because the current sink generally requires a higher bias voltage than the current sense resistor. However, to meet the other performance requirements of the tablet, the driver with an integrated current sink is generally the best choice.
Optimal LED Configuration
Minimizing power consumption and maximizing battery life by selecting the optimal number of strings and the optimal number of LEDs per string is a challenging task. Using fewer strings requires more LEDs per string and results in a higher output voltage for the boost converter. The greater the difference between the input and output voltages of the boost converter, the lower its efficiency. In addition, more strings result in higher total output current and higher losses in the inductor and boost rectifier diode. Figure 3 shows the simulated boost power stage efficiency for three different LED configurations for different series (S) and parallel (P) combinations. Using more strings allows for fewer LEDs per string and provides a lower output voltage, but it requires more current sinks that have to dissipate more power, reducing the overall efficiency of the driver.
Figure 3: Boost power stage efficiency (click to view original image)
Figure 4 shows the total driver efficiency, which includes the power level and current sink efficiency for the same LED configuration shown in Figure 3. From this graph, we can clearly see that the best simulated efficiency occurs when the 20 LEDs are configured with 5 LEDs in series and 4 strings in parallel (5S4P), the 24 LEDs are configured with 6S4P, and the 36 LEDs are configured with 6S6P. Based on these results, the rule of thumb for maximizing the efficiency of the tablet backlight driver is to choose the number of S and P to be equal or as close to each other as possible, but the number of P should be smaller when there are only two options.
Figure 4: Total driver efficiency (click to view original image)
Example Backlight Configuration
Based on the previous analysis, backlight drivers with integrated current sinks, such as the Texas Instruments TPS61181A laptop backlight driver, can be optimized for tablet backlighting (see Figure 5). For tablets that use two Li-ion batteries, both the driver and boost power stage can be powered directly from the batteries. For tablets that use only a single Li-ion battery, the driver bias rail can be powered by the panel's AVDD rail or another power supply (4.5V or higher) in the system. Because the TPS61181A can provide slightly more power than most tablets require (that is, the power FETs are slightly oversized, so the RDS(on) is very low), this converter consumes less power than converters designed for this output power, further maximizing efficiency. Figure 6 shows the measured efficiency results for the 6S6P configuration TPS61161A.
Figure 5: TPS61181A powering tablet backlight (click to view original image)
Figure 6: TPS61181A efficiency when powered by a single lithium-ion battery (click to view original image)
in conclusion
Choosing the best backlight driver for a tablet requires considering all application requirements. Drivers with integrated current sinks are the best choice in meeting all requirements except efficiency. However, careful selection of a driver with a slightly oversized converter, external components with minimal power drop, and an optimal LED string configuration can result in a tablet backlight that maximizes battery life while meeting all design requirements.
Previous article:TIUCC28950600W high performance power system solution
Next article:Don't use an outdated UPS to protect your current network
Recommended ReadingLatest update time:2024-11-16 15:26
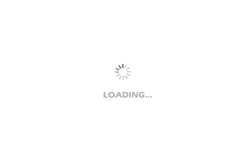
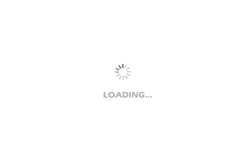
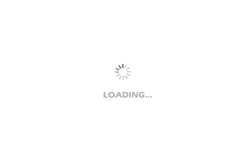
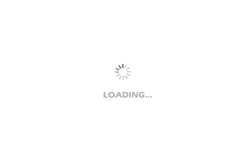
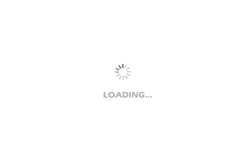
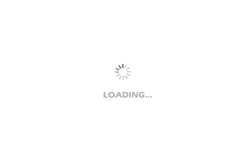
- Popular Resources
- Popular amplifiers
-
Siemens Motion Control Technology and Engineering Applications (Tongxue, edited by Wu Xiaojun)
-
Modern Product Design Guide
-
Modern arc welding power supply and its control
-
Small AC Servo Motor Control Circuit Design (by Masaru Ishijima; translated by Xue Liang and Zhu Jianjun, by Masaru Ishijima, Xue Liang, and Zhu Jianjun)
- MathWorks and NXP Collaborate to Launch Model-Based Design Toolbox for Battery Management Systems
- STMicroelectronics' advanced galvanically isolated gate driver STGAP3S provides flexible protection for IGBTs and SiC MOSFETs
- New diaphragm-free solid-state lithium battery technology is launched: the distance between the positive and negative electrodes is less than 0.000001 meters
- [“Source” Observe the Autumn Series] Application and testing of the next generation of semiconductor gallium oxide device photodetectors
- 采用自主设计封装,绝缘电阻显著提高!ROHM开发出更高电压xEV系统的SiC肖特基势垒二极管
- Will GaN replace SiC? PI's disruptive 1700V InnoMux2 is here to demonstrate
- From Isolation to the Third and a Half Generation: Understanding Naxinwei's Gate Driver IC in One Article
- The appeal of 48 V technology: importance, benefits and key factors in system-level applications
- Important breakthrough in recycling of used lithium-ion batteries
- Innolux's intelligent steer-by-wire solution makes cars smarter and safer
- 8051 MCU - Parity Check
- How to efficiently balance the sensitivity of tactile sensing interfaces
- What should I do if the servo motor shakes? What causes the servo motor to shake quickly?
- 【Brushless Motor】Analysis of three-phase BLDC motor and sharing of two popular development boards
- Midea Industrial Technology's subsidiaries Clou Electronics and Hekang New Energy jointly appeared at the Munich Battery Energy Storage Exhibition and Solar Energy Exhibition
- Guoxin Sichen | Application of ferroelectric memory PB85RS2MC in power battery management, with a capacity of 2M
- Analysis of common faults of frequency converter
- In a head-on competition with Qualcomm, what kind of cockpit products has Intel come up with?
- Dalian Rongke's all-vanadium liquid flow battery energy storage equipment industrialization project has entered the sprint stage before production
- Allegro MicroSystems Introduces Advanced Magnetic and Inductive Position Sensing Solutions at Electronica 2024
- Car key in the left hand, liveness detection radar in the right hand, UWB is imperative for cars!
- After a decade of rapid development, domestic CIS has entered the market
- Aegis Dagger Battery + Thor EM-i Super Hybrid, Geely New Energy has thrown out two "king bombs"
- A brief discussion on functional safety - fault, error, and failure
- In the smart car 2.0 cycle, these core industry chains are facing major opportunities!
- The United States and Japan are developing new batteries. CATL faces challenges? How should China's new energy battery industry respond?
- Murata launches high-precision 6-axis inertial sensor for automobiles
- Ford patents pre-charge alarm to help save costs and respond to emergencies
- New real-time microcontroller system from Texas Instruments enables smarter processing in automotive and industrial applications
- How to set the GND pin of a separate component as a flower pad in PADS?
- EEWORLD University Hall----Keithley 4200A-SCS parameter analyzer accelerates semiconductor equipment, materials and process development
- EEWORLD University Hall ---- Advanced C Language Programming for Embedded Systems (Ling Ming, Southeast University)
- Two-phase brushless DC motor speed control system based on DSP and CPLD
- The main structure of the DM642 image processing program
- Multi-way switch, battery inspection instrument
- EEWORLD University ---- Wildfire FPGA Video Tutorial
- 【Node.js for Embedded Systems】Electronic version
- 24V to 16V circuit problem
- The problem of the propagation speed of electric pulses in wires