LED packaging technology is currently developing in four directions: high light efficiency , high reliability, high heat dissipation and thinness. The main highlights are silicon-based LEDs and high-voltage LEDs. Silicon-based LEDs have attracted more and more attention in the industry because they have stronger heat dissipation capabilities than traditional sapphire-based LEDs, so the power can be made larger. Cree focuses on the development of silicon-based LEDs. The main problem it currently has is that the yield is still low, resulting in high costs.
High-voltage LEDs are another highlight. They can significantly reduce the input-output voltage difference of the DC-DC buck circuit, further improving the efficiency of the LED driver power supply , which can effectively reduce the requirements of the LED lamp for the heat dissipation shell, thereby reducing the overall cost of the LED lamp. Currently, Cree, Osram and Everlight are all developing high-voltage LED processes. Lin Zhimin, director of the second research and development department of Everlight Electronics (Everlight), said: "In the future, Everlight will expand the research and development of products using high-voltage LEDs and integrate more components to create small light engines that are easy to use, in order to reduce the cost of lamps and contribute to the popularization of solid-state lighting ."
LED packaging principle
LED packaging mainly provides a platform for LED chips , allowing LED chips to have better light, electricity and heat performance. Good packaging can make LEDs have better luminous efficiency and a good heat dissipation environment, which in turn increases the service life of LEDs. LED packaging technology is mainly built on five major considerations, namely, optical extraction efficiency, thermal resistance, power dissipation, reliability and cost performance (Lm/$).
Each of the above factors is a very important link in packaging. For example, light extraction efficiency is related to cost performance; thermal resistance is related to reliability and product life; power dissipation is related to customer applications. Overall, the best packaging technology must take all of these into account, but the most important thing is to think from the customer's perspective. A good package is one that can meet and exceed customer needs.
Regarding the composition of LED packaging materials, Lin Zhimin explained in detail that LED packaging is mainly composed of substrate, chip, die-bonding glue, phosphor, packaging glue, etc. We first use the die-bonding glue to stick the chip to the substrate, use gold wire to electrically connect the chip and the substrate, and then mix the phosphor with the packaging glue. Different colors can be obtained by matching different phosphor ratios and appropriate chip wavelengths. Finally, the mixture of phosphor and packaging glue is poured into the substrate. After heating and baking to solidify the glue, the most basic LED packaging is completed.
Four major development trends of LED packaging
He also pointed out that LED packaging technology is mainly developing towards high luminous efficiency, high reliability, high heat dissipation capacity and thinness. From the perspective of chips, the most common ones are horizontal chips, while high-end manufacturers are developing vertical chips and flip-chip chips. The original horizontal LED used a sapphire substrate, which had poor heat dissipation capacity, and under high current drive , the light extraction efficiency also dropped significantly. Therefore, in order to reduce the cost of LEDs, the design of high current density chips has become the main research direction to obtain more light output. Under such considerations, the use of vertical packaged chips has become the next topic. Such chips use high heat dissipation substrates such as silicon, which have better heat dissipation efficiency under high current operation, so they also have higher light output. However, due to the complex production process and low process yield, it is impossible to achieve the ideal high cost performance. Therefore, in high-wattage packaging, the price factor caused by process yield is also a major consideration.
TSMC 's subsidiary, Vision Optoelectronics, specializes in wafer-level high-power LED silicon-based packaging technology. The company entered the Chinese street lamp market in 2010, and in 2011 it focused on indoor lighting bulb products. Li Yuhua, director of LED technology research and development at Vision Optoelectronics, said that based on 8-inch epitaxial wafers, Vision Optoelectronics' current packaging capacity is 2,000 pieces per month, equivalent to 4 million pieces. Last year, its products successfully entered the Chinese street lamp market, and when the volume was high, the monthly shipments even reached 700,000 to 800,000 pieces.
Unlike the alumina (sapphire) substrate technology used by general Taiwanese LED packaging manufacturers, Caiyu uses wafer-level LED silicon-based packaging technology. Caiyu's Li Yuhua said that silicon-based packaged LEDs are better than sapphire substrates in terms of heat dissipation, but the current selling price is also higher than sapphire substrate products. However, Li Yuhua believes that within this year, the prices of Caiyu's silicon-based packaging and sapphire substrate products will converge. Caiyu has even set a goal to reduce costs by 30% each year.
The yield of silicon substrates is still low
The biggest demand for silicon substrates is better thermal conductivity. Li Yuhua further pointed out that the most important requirement for next-generation lighting LED packaging is heat dissipation. It is estimated that the heat problem will be difficult to solve within 5 years. The second is the need for a strong structure and stable and reliable materials. In addition, the performance of light is also very important, such as uniformity, light source intensity, whether the light output efficiency is better, and the performance of light type. Finally, it is the management of mass production and cost.
The biggest feature of the evolution of LED packaging in the past 30 years is that the size is getting smaller and smaller, so the thermal effect problem becomes prominent when the input drive current is high. In other words, the demand for high-power LEDs is increasing. When small LEDs are placed and power is supplied, heat will be generated. In order to reduce the heat, the brightness of the light will decrease. At this time, in order to increase the brightness, a higher current must be introduced, and high current will generate more heat. This becomes a cycle, and the heat continues to increase. The junction temperature is too high, and the result is that the LED efficiency will decrease by 5% for every 20°C increase (or 0.25% for every 1°C increase).
90% of the heat generated by LEDs goes downward, so heat dissipation is very important in packaging technology. In general, the available high-power LED sub-mount materials are ceramics (aluminum oxide, aluminum nitride) and silicon. Among them, aluminum substrates have warping problems, and in terms of thermal conductivity and heat diffusion, silicon is the best choice.
硅基LED封装工艺流程为:绝缘及金属层、芯片/金属线键结及荧光材料涂布、 透镜 组装,再进行切割与 测试 。使用硅晶圆方法可以藉以控制穿孔型式(单一或多重),因而增加光萃取率,这是陶瓷基板所做不到的。李豫华并特别指出采钰独家的 IC 制造兼容晶圆级荧光粉涂布技术,可以在LED芯片最上层造就薄而高效能的荧光粉出光层,可改善黄晕现象,且此技术可控制 色温 的一致性。
另外,半球形 镜头 为以光学设计方式增加出光率的方法之一,也是采钰独家设计的晶圆级产品,镜头设计符合各种出光形式的需求。此外,利用不同材料的折射率不同,由内而外愈来愈小,亦可控制出光路径使其出光率增加,此结构模式可改善出光率逾7%。再者,藉由荧光粉补偿过程可以达到紧密的色温控制,因而良率可获得提升,使原本低于70%的良率,经由补偿可以提升超过95%。目前采钰的LED硅基封装成品已经在多处导入,包括大陆秦皇岛、大陆京沈高速公路匝道的 LED路灯 及新竹清华大学校园等。
However, LED silicon-based packaging still faces many technical challenges that need to be overcome. For example, in terms of materials, silicon has the disadvantage of being easy to break, and structural strength is also a problem. Phosphors need to consider their electronic brightness and thermal and wet impedance. In addition, the refractive index, thermal stability, and adhesion of the lens are also considerations. In terms of structure, the insulating layer and metal layer have their own challenges.
Caiyu specializes in LED lighting and currently has no plans to enter the field of large-size LED backlights. As Taiwan, Japan, the United States, and Canada will begin to ban incandescent light bulbs in 2012, Caiyu believes that the sales volume of LED warm white bulbs will explode in the third quarter of 2011, and the company has also included bulb products in its development focus this year.
Flip-Chip LED Chip Packaging
In addition to the vertical chips mentioned above, flip-chip chips are also the target of the industry's efforts. The production of flip-chip chips is much simpler than that of three-dimensional chips, and it can avoid complex processes, which greatly improves the feasibility of mass production. In addition, with the mature support of the back-end chip process gold finger and via technology, the previous method of solid crystal that required planting multiple gold balls has been transformed into a large-area P and N electrodes directly adhering to the bracket, combined with the eutectic solid crystal method, which greatly simplifies the technical threshold of flip-chip chip packaging. Furthermore, the shortened packaging heat dissipation path has better heat dissipation capacity than horizontal chips, and the driving voltage can also be reduced. Lin Zhimin emphasized that in the future, driven by energy conservation and carbon reduction, flip-chip chip packaging will be a good solution.
Based on the above packaging considerations, Everlight currently uses phosphor coating and transfer technology as the main packaging technology. Phosphor coating is a technology developed by Everlight, which mainly covers a thin phosphor layer on the chip, which can greatly improve the luminous efficiency of the component. Currently, Everlight has used this product in high-power devices.
The transfer process technology was originally used in small surface mount products. Lin Zhimin said that Everlight has achieved great success in this product and has further applied this technology to high-power models, overcoming technical problems such as silicon molding and mold sticking. Currently, due to the increase in power and reliability requirements of backlight components such as TVs, traditional PPA reflective cover substrates are organic materials and cannot provide better heat and light resistance like silicon or resin. In order to effectively improve reliability, Everlight also plans to use this transfer process technology in backlight component products.
Regarding the package size, the smallest high-power package size that Everlight Electronics can achieve in its current experiments is 3.0 × 3.0mm, and even the sample preparation is below 2.0 × 2.0mm. However, the most common specification currently on the market is still 3.5 × 3.5mm products. This product has a very wide range of applications. Therefore, Everlight's Lin Zhimin said that as a pioneer in the era of solid-state lighting, Everlight Electronics will continue to apply small-size high-power technology to this product, using low-cost aluminum nitride ceramic substrates with high-reflectivity reflectors to manufacture the package bracket required for this product. In addition, the eutectic die bonding process technology will be applied to quickly guide heat from the center of the LED to the highly thermally conductive aluminum nitride ceramic through metal, in order to reduce the operating temperature of the LED component and achieve high efficiency (150lm/w), high power (3-5W operation), long life (60,000hrs), and low energy consumption LED product performance.
Furthermore, the choice of chip is also very important. Lin Zhimin said that Everlight will work with high-quality partners around the world to improve the quality and reduce the cost of existing chips, as well as the rapid development of new chip structures, in order to use the silicone molding process technology with the lowest cost for mass production to reduce the packaging cost of existing LED chip processes, and use the fast-response optical structure design to meet the light-collecting effect of the newly designed chip structure, in order to achieve the design goal of the lowest mass production cost and the highest efficiency.
LED package above 20W
In terms of LED packaging, COB packaging technology is another major focus. In response to this, ProLight Technology General Manager Chen-Lun Xing believes that LEDs below 10W are not suitable for COB packaging technology. The mainstream in this field still uses single high-power packaging; LEDs above 20W are more suitable for COB packaging technology. ProLight Technology focuses on the research and development of high-power LED packaging technology, and Epistar is its original shareholder. ProLight's current business in the Chinese mainland market is mainly focused on miner lamps and architectural lighting. Chen-Lun Xing pointed out that the miner lamp market is relatively stable. Although the growth rate has not been high in recent years, ProLight has maintained a high market share in this field.
The rapid expansion of Japan's LED bulb market in 2010 has become a typical example of global LED lighting. At present, Japan's LED bulb market is mainly based on COB polycrystalline packaging, while traditional high-power chips and modules are mostly used for directional LED light sources such as MR16.
Xing Chenzhenlun pointed out that the most commonly used substrates for COB packaging are aluminum substrates, copper substrates and ceramic substrates. The thermal conductivity of each material is different, resulting in differences in thermal conductivity. For example, the thermal conductivity of diamond is 1000, followed by silver and copper at around 400, and then aluminum at more than 100, while the thermal conductivity of ceramics is between 8-22. Among insulating materials, the thermal conductivity of ceramics is already quite good, and coupled with its low price, many packages choose to use ceramic substrates.
Dayi Technology is one of the companies that is actively involved in the R&D and design of LED ceramic heat sink substrates. The company uses sophisticated thick film and thin film yellow light processes and patented electroforming technology to engage in the R&D and production of LED heat sink ceramic substrates. Its current product line includes ceramic heat sink substrates for high-power LED packaging.
High Voltage LED Packaging
In addition to high-power LEDs, high-voltage LED packaging is also a major focus. Everlight's Lin Zhimin said that the company has developed a series of high-voltage LED packaging products, spanning the 1W, 2W and 4W product markets. The advent of high-voltage products is to solve the problem of excess energy loss caused by the existence of step-down circuits in solid-state lighting with a new mindset, and thus help end consumers reduce purchase costs.
Lin Zhimin emphasized that the key point of high-voltage LED product packaging technology is to continue the above advantages, and in addition, it should provide consumers with more convenience, so that different regions can be quickly and conveniently applied under different voltage operating conditions. For example, the 4W product launched by Everlight Electronics can directly use the circuit board's line series and parallel design to meet the different voltage source requirements of 110V and 220V around the world. And because the voltage span of a single component package can reach 110V or even 220V, when developing high-voltage LED packages, Everlight Electronics insists on using an insulated ceramic substrate package to reduce the risk of spark discharge between positive and negative electrodes of small sizes.
At the same time, since the high-voltage LED chip itself has a sapphire substrate, the lateral light is stronger than that of ordinary chips. Therefore, a phosphor design with uniform coverage at all angles should be used during packaging to ensure that the temperature of the package is consistent across the entire viewing angle, thereby improving the quality of light.
Previous article:Detailed explanation of LED packaging technology: ceramic COB technology
Next article:Interpretation of four major key technologies of LED fluorescent lamps
Recommended ReadingLatest update time:2024-11-16 22:24
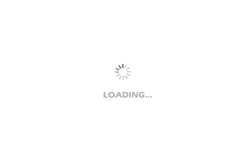
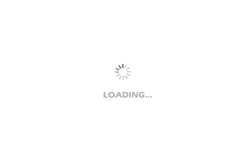
![[DIY tutorial] Environmentally friendly and practical LED reading light](https://6.eewimg.cn/news/statics/images/loading.gif)
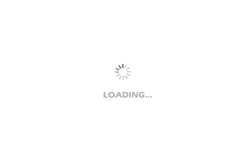
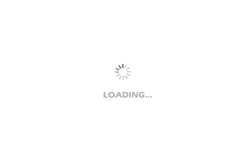
- Popular Resources
- Popular amplifiers
- MathWorks and NXP Collaborate to Launch Model-Based Design Toolbox for Battery Management Systems
- STMicroelectronics' advanced galvanically isolated gate driver STGAP3S provides flexible protection for IGBTs and SiC MOSFETs
- New diaphragm-free solid-state lithium battery technology is launched: the distance between the positive and negative electrodes is less than 0.000001 meters
- [“Source” Observe the Autumn Series] Application and testing of the next generation of semiconductor gallium oxide device photodetectors
- 采用自主设计封装,绝缘电阻显著提高!ROHM开发出更高电压xEV系统的SiC肖特基势垒二极管
- Will GaN replace SiC? PI's disruptive 1700V InnoMux2 is here to demonstrate
- From Isolation to the Third and a Half Generation: Understanding Naxinwei's Gate Driver IC in One Article
- The appeal of 48 V technology: importance, benefits and key factors in system-level applications
- Important breakthrough in recycling of used lithium-ion batteries
- Innolux's intelligent steer-by-wire solution makes cars smarter and safer
- 8051 MCU - Parity Check
- How to efficiently balance the sensitivity of tactile sensing interfaces
- What should I do if the servo motor shakes? What causes the servo motor to shake quickly?
- 【Brushless Motor】Analysis of three-phase BLDC motor and sharing of two popular development boards
- Midea Industrial Technology's subsidiaries Clou Electronics and Hekang New Energy jointly appeared at the Munich Battery Energy Storage Exhibition and Solar Energy Exhibition
- Guoxin Sichen | Application of ferroelectric memory PB85RS2MC in power battery management, with a capacity of 2M
- Analysis of common faults of frequency converter
- In a head-on competition with Qualcomm, what kind of cockpit products has Intel come up with?
- Dalian Rongke's all-vanadium liquid flow battery energy storage equipment industrialization project has entered the sprint stage before production
- Allegro MicroSystems Introduces Advanced Magnetic and Inductive Position Sensing Solutions at Electronica 2024
- Car key in the left hand, liveness detection radar in the right hand, UWB is imperative for cars!
- After a decade of rapid development, domestic CIS has entered the market
- Aegis Dagger Battery + Thor EM-i Super Hybrid, Geely New Energy has thrown out two "king bombs"
- A brief discussion on functional safety - fault, error, and failure
- In the smart car 2.0 cycle, these core industry chains are facing major opportunities!
- The United States and Japan are developing new batteries. CATL faces challenges? How should China's new energy battery industry respond?
- Murata launches high-precision 6-axis inertial sensor for automobiles
- Ford patents pre-charge alarm to help save costs and respond to emergencies
- New real-time microcontroller system from Texas Instruments enables smarter processing in automotive and industrial applications
- Wireless Earbud Battery Ultra-Low Standby Power Consumption Reference Design
- Fake news and exaggerated hype are hurting China's IC industry. Silence is not the solution (Reprinted)
- TA0CCR0 interrupt of msp430
- What are the 9 most important applications of the Internet of Things (IoT)?
- MOS tube burnt out
- About CS1256 Analog Chip
- At the same frequency, the impedance of a large capacitor is smaller than that of a small capacitor, and it has better filtering performance for high frequencies. Why do we need to connect a small capacitor in parallel?
- [GD32E503 Review] Part 5: FreeRTOS Project Creation
- I heard that ST has released a LoRa development board, NUCLEO-WL55JC2. Why can't I find any information about it anywhere in the world?
- MT7603EN Supply