1 Basic principles of frequency standard generation circuit based on feedback control principle and GPS frequency discipline technology
The key to high-precision broadband frequency measurement technology based on GPS frequency calibration is to control the oscillator through the GPS timing signal to generate a standard frequency signal with high stability and high accuracy. Figure 1 is a standard frequency generation circuit based on feedback control principle and GPS taming frequency calibration technology.
It is a closed-loop feedback control system, mainly composed of five parts: GPS receiver, time interval measurement link, data control and processing link, error control voltage generation link, voltage controlled oscillator (VCO), and frequency divider. The GPS receiver receives the 1 pps signal generated by the satellite signal, uses the signal to adopt high-precision time interval measurement technology, compares it with the frequency division signal of the local frequency standard, calculates the relative frequency difference according to the rate of change of the phase difference, forms an error control voltage, and feeds it back to the local voltage controlled oscillator. The oscillator output signal frequency is adjusted until the frequency division output frequency is equal to the GPS second pulse frequency, the error control voltage is close to zero, and the system is finally in a balanced state, thereby achieving tracking and locking of the input signal (GPS). The accuracy of the local frequency standard is locked to the accuracy of the GPS standard, thereby achieving the taming and adjustment of the high-stability crystal oscillation frequency, and improving the accuracy and stability of the frequency standard oscillator.
2 Characteristics Analysis of Voltage Controlled Oscillator
The accuracy and stability of the frequency standard generation circuit based on the feedback control principle and GPS discipline frequency calibration technology mainly depends on the voltage controlled oscillator in the loop. The voltage controlled oscillator (VCO) is a voltage-frequency conversion circuit. As a controlled oscillator in the loop, its output frequency should change linearly with the control voltage. The relationship between the output frequency and input frequency of an ideal voltage controlled oscillator is:
Where: KVCO is the gain of the voltage controlled oscillator. In practical applications, the linear range of the voltage controlled oscillator is limited. Beyond this range, the parameters of the loop will change greatly, which is not conducive to loop design. The following indicators are usually used to evaluate the quality of VCO:
(1) Low jitter or low phase noise: Due to the influence of factors such as circuit structure, power supply noise and ground noise, the output signal of the VCO is not an ideal square wave or sine wave. Its output signal has a certain jitter. After conversion into the frequency domain, it can be seen that there is also a large energy distribution near the center frequency of the signal, which is the so-called phase noise. The jitter of the VCO output signal directly affects the design of other circuits. It is usually hoped that the jitter of the VCO is as small as possible.
(2) Wide frequency modulation range: The adjustment range of the VCO directly affects the frequency adjustment range of the entire system. Usually, as the process deviation, temperature and power supply voltage change, the locking range of the VCO will also change. Therefore, the VCO is required to have a wide enough adjustment range to ensure that the output frequency of the VCO can meet the design requirements.
(3) Stable gain: The voltage-frequency nonlinearity of the VCO is one of the main reasons for noise generation. At the same time, this nonlinearity will also bring uncertainty to the circuit design. The changing VCO gain will affect the loop parameters and thus the stability of the loop. Therefore, it is hoped that the VCO gain change is as small as possible.
Common voltage-controlled oscillators include inverter-type VCO, differential pair-type VCO and LC-type VCO.
The core of the inverter type VCO is composed of an odd number of inverters, and the oscillation frequency is determined by the delay of each inverter and the number of inverters. The delay time of each unit is related to the current, voltage, and process flowing through the inverter. The advantages of this structure of VCO are simple circuit design and the oscillation frequency can be designed to be very high, but it is more sensitive to power supply or ground noise and has larger phase jitter.
The differential pair VCO is mainly composed of a differential pair delay, and its loop structure is shown in Figure 2. The differential delay unit is composed of a voltage-controlled current source, a resistive load, and an NMOS tube. The oscillation frequency is controlled by controlling the current of the voltage-controlled current source. The advantage of the differential pair VCO is that the differential signal can suppress ground noise or power supply noise, and the phase jitter is small. The disadvantage is that the bandwidth is limited and it is not suitable for high-frequency applications.
The characteristics of LC type VCO are: due to the high Q value of LC resonant cavity, the phase noise of this type of VCO is very low, so it is often used in frequency synthesizers with very low frequency jitter requirements. And the operating frequency of this structure is only related to the inductance L and the capacitance C. By reducing the inductance or capacitance and reducing the parasitic capacitance of the circuit, the circuit can work at a very high operating frequency.
Figure 3 is a common negative transconductance LC type VCO structure. The signal fed back from the drain end of the MOS tube is fed back to the source end of the MOS tube through another MOS tube. Assuming that the transconductance of the MOS tube is gm, the impedance looking up from the dotted end of Figure 3 (a) is -2/gm, which is a negative resistance, which is generated by the positive feedback of two cross MOS tubes. Usually, if the oscillator is to oscillate, this negative resistance should be less than or equal to the equivalent parallel internal resistance of the LC resonant cavity, that is, the larger the transconductance of the MOS tube, the smaller the negative resistance, and the easier the circuit is to oscillate. In the case of oscillation, the oscillation frequency of the circuit is related to L and C, that is, the capacitor C is a voltage-controlled capacitor. By adjusting the voltage Vcont, the size of the capacitor can be adjusted, thereby changing the oscillation frequency of the circuit. The structures of Figure 3(b) and (c) are similar to Figure 3(a). The structure of Figure 3(a) has a stronger ability to suppress power supply noise, and the structure of Figure 3(b) has a stronger ability to suppress ground noise. Figure 3(c) has the advantages of the first two structures and only requires one inductor, which can reduce the problem of reduced common-mode suppression caused by the asymmetric inductance of the first two structures. Compared with the previous two circuits, this circuit also has a disadvantage, that is, the circuit has two current sources, so the power supply noise is relatively large.
FIG4 is a differential structure LC type VCO. Assuming that NMOS and PMOS have equal transconductance gm, the negative resistance of this structure is ~1/gm, which is 1/2 less than the negative resistance of the structure in FIG3. Since, if the structures in FIG4 and FIG3 are to have the same negative resistance, the current required by the structure in FIG4 is only 1/4 of that in FIG3, the structure in FIG4 is more suitable for low power design.
The voltage-controlled capacitor can be realized by the junction capacitance of the diode in CMOS. Since the junction capacitance is related to the voltage across the diode, the size of the junction capacitance can be controlled by controlling this voltage. The frequency adjustment range of the LC-type VCO is related to the voltage-controlled capacitor. Usually due to process limitations, the junction capacitance of the diode changes within 50%, and the corresponding frequency adjustment range of the VCO is only about 10%. Therefore, the frequency adjustment range of the loop using this structure is limited, and other auxiliary methods are needed to expand the frequency adjustment range. The frequency locking range will also affect the gain of the VCO. The larger the locking range, the greater the gain of the VCO, and the higher the VCO gain, the greater the input noise of the oscillator. This is because a small noise interference on the control voltage will cause a large VCO frequency change, so the adjustment range of the VCO and the phase noise must be compromised.
3 Design of Low Noise and Low Power Voltage Controlled Oscillator
FIG5 is a fully differential LC voltage-controlled oscillator of the structure shown in FIG4, which has a higher power supply noise and substrate noise suppression capability and requires less current. The subcircuit vco_var_cap is a voltage-controlled capacitor array, and the number of voltage-controlled capacitors turned on can be controlled by controlling GAIN<3:0>, thereby selecting a suitable VCO gain and operating frequency.
Figure 6 is the control voltage scanning curve of this LC type voltage controlled oscillator, where Figure 6(a) is the relationship curve between the output frequency and the control voltage. It can be seen from the figure that when the control voltage changes from 0 V to 2 V, the output frequency changes from 2.06 GHz to 1.98 GHz. Figure 6(b) is the relationship curve between the gain of the voltage controlled oscillator and the change of the control voltage. When the control voltage is between 0 and 2 V, the maximum gain of the voltage controlled oscillator is 2π×50 MHz/V, and the minimum gain is 2π×20 MHz/V. The designed frequency is stable within the range of the gain change of this voltage controlled oscillator, so it can be considered that the working range of the voltage controlled oscillator is 1.98~2.06 GHz.
Figure 7 is the transient simulation waveform of the voltage-controlled oscillator. It can be seen from the figure that the oscillator goes from non-oscillation to oscillation in about 100 ns. The oscillation stabilization time is related to the negative resistance of the oscillator. The smaller the negative resistance, the stronger the positive feedback capability of the loop and the shorter the time to reach stability.
4 Conclusion
In order to make the output standard signal have high stability and high sensitivity, the design of VCO plays a decisive role. The advantage of differential pair VCO is that the differential signal can suppress ground noise or power supply noise, and the phase jitter is small. The disadvantage is that the bandwidth is limited and it is not suitable for high-frequency applications. The Q value of the LC resonant cavity is very high, so the phase noise of the LC type VCO is very low, so it is often used in occasions with very low frequency jitter requirements, and the operating frequency of this structure is only related to the inductor L and the capacitor C. By reducing the inductor or capacitor and reducing the parasitic capacitance of the circuit, the circuit can work at a very high operating frequency. Based on the analysis and comparison of the advantages and disadvantages of the three types of voltage-controlled oscillators, namely the inverting VCO, the differential pair VCO, and the LC VCO, this paper adopts a fully differential LC type voltage-controlled oscillator to obtain a voltage-controlled oscillator with the dual advantages of differential structure and LC structure.
Previous article:Current Matching Problems in Parallel Connection of Multiple Devices
Next article:Design of voltage isolation correction circuit in superconducting magnet quench detection
Recommended ReadingLatest update time:2024-11-16 15:31
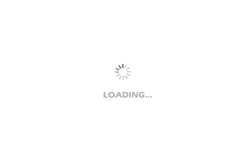
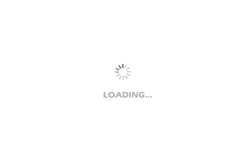
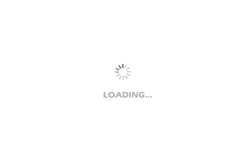
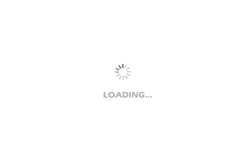
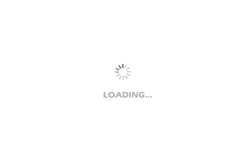
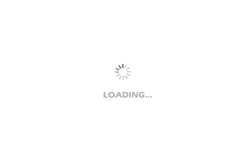
- Popular Resources
- Popular amplifiers
- MathWorks and NXP Collaborate to Launch Model-Based Design Toolbox for Battery Management Systems
- STMicroelectronics' advanced galvanically isolated gate driver STGAP3S provides flexible protection for IGBTs and SiC MOSFETs
- New diaphragm-free solid-state lithium battery technology is launched: the distance between the positive and negative electrodes is less than 0.000001 meters
- [“Source” Observe the Autumn Series] Application and testing of the next generation of semiconductor gallium oxide device photodetectors
- 采用自主设计封装,绝缘电阻显著提高!ROHM开发出更高电压xEV系统的SiC肖特基势垒二极管
- Will GaN replace SiC? PI's disruptive 1700V InnoMux2 is here to demonstrate
- From Isolation to the Third and a Half Generation: Understanding Naxinwei's Gate Driver IC in One Article
- The appeal of 48 V technology: importance, benefits and key factors in system-level applications
- Important breakthrough in recycling of used lithium-ion batteries
- Innolux's intelligent steer-by-wire solution makes cars smarter and safer
- 8051 MCU - Parity Check
- How to efficiently balance the sensitivity of tactile sensing interfaces
- What should I do if the servo motor shakes? What causes the servo motor to shake quickly?
- 【Brushless Motor】Analysis of three-phase BLDC motor and sharing of two popular development boards
- Midea Industrial Technology's subsidiaries Clou Electronics and Hekang New Energy jointly appeared at the Munich Battery Energy Storage Exhibition and Solar Energy Exhibition
- Guoxin Sichen | Application of ferroelectric memory PB85RS2MC in power battery management, with a capacity of 2M
- Analysis of common faults of frequency converter
- In a head-on competition with Qualcomm, what kind of cockpit products has Intel come up with?
- Dalian Rongke's all-vanadium liquid flow battery energy storage equipment industrialization project has entered the sprint stage before production
- Allegro MicroSystems Introduces Advanced Magnetic and Inductive Position Sensing Solutions at Electronica 2024
- Car key in the left hand, liveness detection radar in the right hand, UWB is imperative for cars!
- After a decade of rapid development, domestic CIS has entered the market
- Aegis Dagger Battery + Thor EM-i Super Hybrid, Geely New Energy has thrown out two "king bombs"
- A brief discussion on functional safety - fault, error, and failure
- In the smart car 2.0 cycle, these core industry chains are facing major opportunities!
- The United States and Japan are developing new batteries. CATL faces challenges? How should China's new energy battery industry respond?
- Murata launches high-precision 6-axis inertial sensor for automobiles
- Ford patents pre-charge alarm to help save costs and respond to emergencies
- New real-time microcontroller system from Texas Instruments enables smarter processing in automotive and industrial applications
- 【NXP Rapid IoT Review】Environmental Quality Test
- [ATmega4809 Curiosity Nano Review] Installing MCC
- GD32E231C-START Unboxing
- X-NUCLEO-IKS01A3 sensor test based on STM32F401RE development board 5L
- Simulation failed with no results
- Principle of Dialogue Communication
- Voltage jump problem
- 【McQueen Trial】Main functions corresponding to driver pins
- ti dsp (tms320VC5502) + isp1581 usb2.0 high speed data acquisition solution
- Tesla's electric motor