1 Introduction
Compared with the traditional centralized power supply system, the modular distributed power supply has the characteristics of high reliability, high efficiency, small size and easy use, but it needs to be equipped with reliable current sharing measures to ensure the uniform distribution of electrical and thermal stresses between modules. This paper proposes a modular high-power DC power supply. The single power module is based on DSP and adopts high-frequency switching power conversion technology to achieve voltage stabilization and current sharing of multiple modules in parallel operation.
2 Overall design of power supply
The basic module is a power supply with a voltage adjustment range of 22 V to 30 V DC and a power of 4 kW. The PWM control method is used to control the output by changing the PWM duty cycle. The main circuit of the basic module adopts a half-bridge topology; the control circuit is based on TMS320LF2407A to achieve voltage regulation, current limiting, and current balancing functions, and the protection circuit includes input voltage detection, output overcurrent detection, output overvoltage detection, and whole machine overheating detection.
3 Hardware Design of Basic Modules
The circuit principle of the power module is shown in Figure 1. Since the voltage stress of the primary switch tube in the half-bridge structure is the smallest, for offline switching power supplies, L1 in the circuit is the main filter inductor with a large inductance; L2 is the auxiliary inductor with a small inductance, which is mainly used to further reduce the output switching noise.
The rated power of a single power module is 4 kW, and the rated output voltage is 28 V. Considering the overload problem, the actual maximum output current is 150 A. According to the equal power of the primary and secondary sides of the transformer, the current flowing through the power module is estimated. Considering that the three-phase AC power supply voltage fluctuates within the range of ±15%, the voltage of the primary winding of the half-bridge converter transformer is 230 V, and the maximum current flowing through the primary winding of the transformer, that is, the power module, is 18.3 A. The reverse pressure on the power module is the three-phase rectifier voltage; the voltage calculated based on the maximum value of the three-phase AC voltage is 618 V. In order to ensure the reliable operation of the device, the rated current of the power module is more than twice the operating current. Therefore, the IGBT module CM100DY-24NF of Mitsubishi Corporation is selected, which has a rated current of 100 A, a withstand voltage of 1,200 V, and a two-unit half-bridge structure.
The control circuit is mainly composed of TMS320LF2407A subsystem, A/D input, voltage regulation, power-on protection and other circuits. Among them, the TMS320-LF2407A subsystem mainly includes clock, reset, JTAG simulation interface and power supply system.
4 Software Design of TMS320LF2407A
TMS320LF2407A DSP is the control core of the power module. It realizes voltage regulation, current sharing and other functions by changing the duty cycle of the output PWM. The main program is in the waiting interrupt state after completing system initialization, A/D initialization and timer start. Each functional module is realized through the interrupt service program.
4.1 Software Design of Voltage Stabilization Function
The sensor outputs a voltage signal, which is filtered and sampled, and then compared with a given voltage signal. The deviation is sent to the PID regulator to change the PWM duty cycle to keep the output voltage constant. The PID regulator uses an incremental PID control algorithm that discretizes and improves the analog PID control law. The control is simple and the parameters are easy to set. The control increment of the duty cycle can be obtained by measuring the deviation three times.
4.2 Software Design of Current Sharing Function
There are many ways to achieve the current sharing function for a power system with several power modules connected in parallel, such as output impedance method, master-slave current sharing method, automatic current sharing method, democratic current sharing method, etc. This power system module adopts the automatic current sharing method (also known as the external current sharing controller method). This method requires a communication line with a narrow bandwidth (called the current sharing bus) to connect each module. The voltage of the current sharing bus is proportional to the average value of the current of each module. This power system module uses TMS320LF2407A as a controller for voltage regulation and current sharing at the same time, and improves the average automatic current sharing method. The average current is calculated and the current sharing threshold is set through the sampling data of the circulating current error and the load current. Each power module decides whether to participate in the current sharing according to the specific values of its load current and circulating current. In this way, current sharing can be achieved accurately, and the automatic current sharing method is also avoided. Failures and instability problems are easy to occur. Figure 2 shows the flow chart of the current sharing subroutine.
5 Conclusion
In addition to the above designs, in order to ensure the reliable and efficient operation of the power supply, this modular power supply system also designs surge current suppression circuits, generalized soft switches - absorption circuits, protection circuits, and anti-electromagnetic interference designs for the main circuit and control circuit. Finally, four series of DC power supplies were developed. The input voltage is three-phase three-wire AC 380 V. The output voltage is DC 28 V, and the rated capacities are 4 kW, 8 kW (current sharing error <2%), 16 kW (current sharing error <3%), and 24 kW (current sharing error <5%).
Now, with TMS320LF2407A DSP as the control core, the design of a high-power digital DC switching power supply with multi-module parallel operation has been realized. After experimental testing and actual use, the power supply works stably, and the voltage stabilization and current sharing effects are good, meeting the expected requirements.
Previous article:Capacitor Application in Power Supply Design
Next article:Hard disk MP3 power supply design based on new ASSP LTC3455
Recommended ReadingLatest update time:2024-11-16 18:06
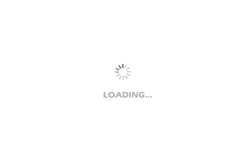
- MathWorks and NXP Collaborate to Launch Model-Based Design Toolbox for Battery Management Systems
- STMicroelectronics' advanced galvanically isolated gate driver STGAP3S provides flexible protection for IGBTs and SiC MOSFETs
- New diaphragm-free solid-state lithium battery technology is launched: the distance between the positive and negative electrodes is less than 0.000001 meters
- [“Source” Observe the Autumn Series] Application and testing of the next generation of semiconductor gallium oxide device photodetectors
- 采用自主设计封装,绝缘电阻显著提高!ROHM开发出更高电压xEV系统的SiC肖特基势垒二极管
- Will GaN replace SiC? PI's disruptive 1700V InnoMux2 is here to demonstrate
- From Isolation to the Third and a Half Generation: Understanding Naxinwei's Gate Driver IC in One Article
- The appeal of 48 V technology: importance, benefits and key factors in system-level applications
- Important breakthrough in recycling of used lithium-ion batteries
- Innolux's intelligent steer-by-wire solution makes cars smarter and safer
- 8051 MCU - Parity Check
- How to efficiently balance the sensitivity of tactile sensing interfaces
- What should I do if the servo motor shakes? What causes the servo motor to shake quickly?
- 【Brushless Motor】Analysis of three-phase BLDC motor and sharing of two popular development boards
- Midea Industrial Technology's subsidiaries Clou Electronics and Hekang New Energy jointly appeared at the Munich Battery Energy Storage Exhibition and Solar Energy Exhibition
- Guoxin Sichen | Application of ferroelectric memory PB85RS2MC in power battery management, with a capacity of 2M
- Analysis of common faults of frequency converter
- In a head-on competition with Qualcomm, what kind of cockpit products has Intel come up with?
- Dalian Rongke's all-vanadium liquid flow battery energy storage equipment industrialization project has entered the sprint stage before production
- Allegro MicroSystems Introduces Advanced Magnetic and Inductive Position Sensing Solutions at Electronica 2024
- Car key in the left hand, liveness detection radar in the right hand, UWB is imperative for cars!
- After a decade of rapid development, domestic CIS has entered the market
- Aegis Dagger Battery + Thor EM-i Super Hybrid, Geely New Energy has thrown out two "king bombs"
- A brief discussion on functional safety - fault, error, and failure
- In the smart car 2.0 cycle, these core industry chains are facing major opportunities!
- The United States and Japan are developing new batteries. CATL faces challenges? How should China's new energy battery industry respond?
- Murata launches high-precision 6-axis inertial sensor for automobiles
- Ford patents pre-charge alarm to help save costs and respond to emergencies
- New real-time microcontroller system from Texas Instruments enables smarter processing in automotive and industrial applications
- How does condensation water in dry sealed spaces occur?
- Several tips for drawing schematics
- How to protect your IP when connecting to cloud services? Microchip offers tips
- 【AT-START-F425 Review】 2. Development Environment Construction and Demo Examples
- Is anyone familiar with lithium battery protection IC? If I want to verify these parameters, is there a special instrument? It shouldn't be...
- Electronic engineers, how can we better embrace GaN? Participate in the survey to get a gift!
- EEWORLD University----UCD3138 Digital PWM (DPWM) Module
- A joke only programmers can understand
- Battery voltage detection simulation + program based on MSP430
- Help: STM32 macro definition compilation fails, please correct me