There are still many unsolved problems in
LED
technology, one of which is how to produce high-quality white light.
White light LEDs
are composed of
blue LEDs
and a phosphor that shifts the light output to other parts of the spectrum. Many white light LEDs do not produce a high
Color
Rendering Index (CRI), which is a parameter used to measure the ability of a light source to reproduce colors faithfully.
Higher quality white light systems can be obtained by mixing two or more colors of LED light. In these multi-color systems, the light output of each color source will drift over time and temperature.
Light sensors
and small microcontrollers (
MCUs
) can be used to maintain specific colors and related
color
temperatures
(CCT).
There are many small and affordable light sensors on the market that can provide information to the MCU for processing. Typically,
the sensor
has some optional color filters to
measure
red, green,
blue
, or white light (no filter). The light sensor output
can
be connected to the MCU through a variety of methods. Light-to-voltage sensors are connected to analog-to-digital converters (ADCs) through the output voltage. Light-to-frequency sensors provide a variable frequency output that is proportional to the amount of light. The pulsed outputs of these sensors can be accumulated in an MCU timer to determine light levels. Light-to-digital sensors typically have a serial digital interface, such as I2C. Each type of sensor interface has unique benefits and requires different MCU resources. The system block diagram in Figure 1 shows a variety of MCU
peripherals
that
are useful in
color-tunable
LED lighting
designs.
Figure 1 MCU peripherals that can be used in LED color control systems
In a complete closed-loop color control system, the MCU must read the color content from the light sensor, calibrate the light sensor output, and adjust the output of each
LED driver
to achieve the desired color. The LEDs require a constant current
driver
to maintain consistent light output. This can be achieved using a variety of driver technologies, including linear and
switch
mode solutions. The final choice depends on factors such as efficiency requirements, input voltage range, and number of LEDs used.
The driver output can be controlled using different methods. First, the MCU can
generate an analog reference voltage
through a digital-to-analog converter (
DAC
) or a digital potentiometer. The reference voltage can vary the driver output between zero and maximum current. The MCU can also provide a
PWM
signal that modulates the driver output. The PWM signal can be used to enable/disable the driver itself or to control a switch that disconnects the LED from the driver output. If PWM control is used, the PWM frequency should be selected to be high enough so that the human eye cannot detect any flicker.
The designer must determine what control resolution the color control system requires in order to select an MCU with the appropriate peripherals. For light-to-voltage sensors, the measurement resolution of the ADC on the MCU is important. Light-to-frequency sensors require an MCU time base that is incremented by an external
clock
. Light-to-digital sensors require the appropriate serial
communication
interface peripherals.
MCUs with multiple PWM peripherals can be used to control individual LED drivers. In high-resolution color control systems, PWM peripherals with 16-bit or higher control resolution are preferred. Serial communication peripherals such as UART, SPI, I2C, LIN, and
USB
support input/output control and
display
functions.
MCU devices such as the
PIC24FJ16GA002
are excellent choices
for color control systems
. The PIC24 device has a small 28-pin package, a program memory range of 16 to 64 KB, and provides a serial communication interface, a 10-bit ADC, and 5 PWM channels in a single device. The 16-bit MCU core can easily handle the arithmetic operations related to sensor calibration and color control.
The sensor data output must be calibrated to a reference voltage to provide consistent results. The calibration process uses a colorimeter to mathematically relate the output of different color LEDs to the spectral response and sensitivity of the light sensor in a standard chromaticity coordinate system. The calibration process generates a coefficient matrix that must be stored in nonvolatile memory with the lighting system and used to determine the difference between the correlation and the desired output at each control of the control system.
Once the calibration is completed, the MCU can compare the sensor data with the ideal CIE (International Commission on Illumination) chromaticity diagram coordinates and adjust the output channels until the ideal CCT is achieved. The PID control
algorithm
for each output channel
adjusts the sensor data using the calibration value, finds the difference from the target set point, and then adjusts the output channel. The PID is run continuously to reduce the error until the output CCT matches the set point CCT. The PID coefficients can be fine-tuned to maximize the system response, but how quickly the PID algorithm converges to the target CCT is also a function of the efficiency of the MCU processing arithmetic operations. Some color control systems may require faster processing speed and response than others. For example, general lighting systems have
lower requirements than local dimming systems for
HDTV
panels
. Systems with dimmable light sources or high CRI have a range of user control requirements.
Medical devices
with
graphic
LCD
displays
may have dimmable
LED backlights
(which require the MCU to communicate with the LCD via SPI) and a touch screen interface for adjusting CCT and
brightness
. General lighting for commercial display equipment may require control from a central panel or
computer
to automatically adjust brightness, CCT, and on/off according to the time of day. Communication between these devices may be achieved using hardwired serial
bus
protocols such as DALI or DMX512, while some other devices may require custom interfaces implemented over USB or
Ethernet
. In completed buildings, installing a hardwired infrastructure may not be feasible and control may need to be done via
wireless
communications and protocols such as ZigBee. For such lighting applications, MCUs with flexible peripherals are ideal for implementing communications and user interfaces.
Previous article:Basic Electronics Knowledge: LED Advantages and Industry Classification
Next article:Main dimming technologies and future development of LED lamps
Recommended ReadingLatest update time:2024-11-16 17:44
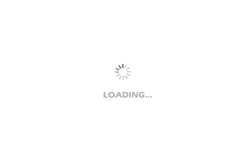
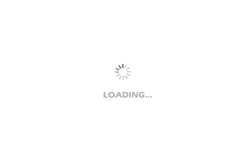
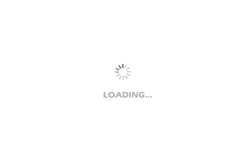
- Popular Resources
- Popular amplifiers
-
Wireless Sensor Network Technology and Applications (Edited by Mou Si, Yin Hong, and Su Xing)
-
Modern Electronic Technology Training Course (Edited by Yao Youfeng)
-
Modern arc welding power supply and its control
-
Small AC Servo Motor Control Circuit Design (by Masaru Ishijima; translated by Xue Liang and Zhu Jianjun, by Masaru Ishijima, Xue Liang, and Zhu Jianjun)
- MathWorks and NXP Collaborate to Launch Model-Based Design Toolbox for Battery Management Systems
- STMicroelectronics' advanced galvanically isolated gate driver STGAP3S provides flexible protection for IGBTs and SiC MOSFETs
- New diaphragm-free solid-state lithium battery technology is launched: the distance between the positive and negative electrodes is less than 0.000001 meters
- [“Source” Observe the Autumn Series] Application and testing of the next generation of semiconductor gallium oxide device photodetectors
- 采用自主设计封装,绝缘电阻显著提高!ROHM开发出更高电压xEV系统的SiC肖特基势垒二极管
- Will GaN replace SiC? PI's disruptive 1700V InnoMux2 is here to demonstrate
- From Isolation to the Third and a Half Generation: Understanding Naxinwei's Gate Driver IC in One Article
- The appeal of 48 V technology: importance, benefits and key factors in system-level applications
- Important breakthrough in recycling of used lithium-ion batteries
- Innolux's intelligent steer-by-wire solution makes cars smarter and safer
- 8051 MCU - Parity Check
- How to efficiently balance the sensitivity of tactile sensing interfaces
- What should I do if the servo motor shakes? What causes the servo motor to shake quickly?
- 【Brushless Motor】Analysis of three-phase BLDC motor and sharing of two popular development boards
- Midea Industrial Technology's subsidiaries Clou Electronics and Hekang New Energy jointly appeared at the Munich Battery Energy Storage Exhibition and Solar Energy Exhibition
- Guoxin Sichen | Application of ferroelectric memory PB85RS2MC in power battery management, with a capacity of 2M
- Analysis of common faults of frequency converter
- In a head-on competition with Qualcomm, what kind of cockpit products has Intel come up with?
- Dalian Rongke's all-vanadium liquid flow battery energy storage equipment industrialization project has entered the sprint stage before production
- Allegro MicroSystems Introduces Advanced Magnetic and Inductive Position Sensing Solutions at Electronica 2024
- Car key in the left hand, liveness detection radar in the right hand, UWB is imperative for cars!
- After a decade of rapid development, domestic CIS has entered the market
- Aegis Dagger Battery + Thor EM-i Super Hybrid, Geely New Energy has thrown out two "king bombs"
- A brief discussion on functional safety - fault, error, and failure
- In the smart car 2.0 cycle, these core industry chains are facing major opportunities!
- The United States and Japan are developing new batteries. CATL faces challenges? How should China's new energy battery industry respond?
- Murata launches high-precision 6-axis inertial sensor for automobiles
- Ford patents pre-charge alarm to help save costs and respond to emergencies
- New real-time microcontroller system from Texas Instruments enables smarter processing in automotive and industrial applications
- Temperature transmitter hardware framework and schematic diagram
- Testing solutions for redundant link networks
- Key wireless technologies for 5G systems
- [NXP Rapid IoT Review] + Rapid IoT App Running Error
- How to Design an RF Power Amplifier: The Basics
- What is the principle of touch switch?
- What is jitter and phase noise?
- [Shanghai Hangxin ACM32F070 development board + touch function evaluation board evaluation] + OLED screen display driver
- Tailing Micro B91 Development Kit Burning Pitfalls Record
- Antai Testing - Sharing of Maintenance Experience of Tektronix AFG3021 Arbitrary Signal Generator