The types of LED product packaging structures are also classified according to the characteristics of luminous color, chip material, luminous brightness, size, etc. A single tube core generally constitutes a point light source, and multiple tube cores assembled generally constitute a surface light source and a line light source for information, status indication and display. The light-emitting display also uses multiple tube cores, which are combined with appropriate connections (including series and parallel connections) of the tube cores and suitable optical structures to form the light-emitting segments and light-emitting points of the light-emitting display. Surface mount LEDs can gradually replace pin-type LEDs, and the application design is more flexible. They have occupied a certain share in the LED display market and have an accelerating development trend. Some solid lighting sources have been launched on the market, becoming the medium- and long-term development direction of LEDs in the future.
Leaded package
LED foot-type package uses lead frame as pins of various package shapes. It is the first package structure successfully developed and put on the market. There are many varieties and the technology is mature. The structure and reflective layer of the package are still being improved. Standard LED is considered by most customers to be the most convenient and economical solution in the display industry. The typical traditional LED is placed in a package that can withstand 0.1W input power. 90% of its heat is dissipated from the negative lead frame to the PCB board and then to the air. How to reduce the temperature rise of the pn junction during operation is a must for packaging and application. The encapsulation material is mostly high-temperature curing epoxy resin, which has excellent optical properties, good process adaptability, and high product reliability. It can be made into colored transparent or colorless transparent and colored scattering or colorless scattering lens packages. Different lens shapes constitute a variety of shapes and sizes. For example, the circle is divided into several types according to the diameter, such as Φ2mm, Φ3mm, Φ4.4mm, Φ5mm, Φ7mm, etc. Different components of epoxy resin can produce different luminous effects.
There are many different packaging structures for colorful point light sources: ceramic base epoxy resin packaging has good operating temperature performance, the pins can be bent into the required shape, and the volume is small; metal base plastic reflective cover packaging is an energy-saving indicator light, suitable for power indication; the flashing type combines the CMOS oscillation circuit chip with the LED tube core, which can generate flashing light with strong visual impact; the two-color type is composed of two tube cores with different luminous colors, which are packaged in the same epoxy resin lens. In addition to the two colors, a third mixed color can be obtained. It is widely used in large-screen display systems and can be packaged to form a two-color display device; the voltage type combines the constant current source chip with the LED tube core, which can directly replace various voltage indicator lights of 5-24V. The surface light source is formed by bonding multiple LED tube cores to the specified position of the micro PCB board, using a plastic reflective frame cover and potting epoxy resin. The different designs of the PCB board determine the arrangement and connection of the external leads, and there are structural forms such as dual-row in-line and single-row in-line. Hundreds of package shapes and sizes have been developed for point and surface light sources for market and customer application.
LED light-emitting displays can be composed of various multi-digit products such as digital tubes or M-shaped tubes, symbol tubes, and matrix tubes, and can be designed into various shapes and structures according to actual needs. Taking digital tubes as an example, there are three packaging structures: reflective cover type, monolithic integrated type, and single seven-segment type. There are two connection methods: common anode and common cathode. One digit is usually called a digital tube, and more than two digits are generally called displays. The reflective cover type has the characteristics of large fonts, low material consumption, and flexible assembly. It is generally made of white plastic into a seven-segment shell with a reflective cavity. A single LED tube core is bonded to a PCB board that is aligned with the seven reflective cavities of the reflective cover. The center position of the bottom of each reflective cavity is the light-emitting area formed by the tube core. The leads are bonded by pressure welding, and epoxy resin is dripped into the reflective cover. It is aligned and bonded with the PCB board with the tube core, and then cured. The reflective cover type is divided into two types: empty seal and solid seal. The former uses epoxy resin with scattering agent and dye, and is mostly used for single-bit and double-bit devices; the latter is covered with color filter and uniform light film, and transparent insulating glue is applied on the tube core and the bottom plate to improve the light output efficiency. It is generally used for digital display with more than four digits. The monolithic integrated type is to make a large number of seven-segment digital display graphic tube cores on the luminous material wafer, and then cut them into single-chip graphic tube cores, bond, press weld, and package the shell with lens (commonly known as fisheye lens). The single-strip seven-segment type cuts the already made large-area LED chip into light strips containing one or more tube cores, so that the same seven strips are bonded to the digital font frame, and then pressed and epoxy resin packaged. The characteristics of the monolithic type and the single-strip type are miniaturization, and dual-in-line packaging can be used. Most of them are special products. The LED light column display is placed on a circuit board with a length of 106mm, with 101 tube cores (up to 201 tube cores). It is a high-density package that uses the principle of optical refraction to make a point light source form an image through 13-15 gratings of a transparent cover to complete the display of each tube core from point to line. The packaging technology is relatively complex.
The electroluminescent mechanism of semiconductor pn junction determines that LED cannot produce white light with continuous spectrum, and a single LED cannot produce more than two high-brightness monochromatic lights. It can only use fluorescent materials during packaging, and apply fluorescent powder on the blue or ultraviolet LED tube core to indirectly produce broadband spectrum and synthesize white light; or use several (two or three or more) tube cores that emit different colors to be packaged in a component shell, and form white light LED by mixing the colors. Both methods have been put into practical use. In 2000, Japan produced 100 million white light LEDs, which developed into a type of product that emits white light stably, and designed and assembled multiple white light LEDs into electric light sources that do not require high luminous flux, mainly for local decorative purposes, and pursue new trends.
Surface Mount Package
In 2002, surface mount LEDs (SMD LEDs) were gradually accepted by the market and gained a certain market share. The shift from pin-type packaging to SMD was in line with the general development trend of the entire electronics industry, and many manufacturers launched such products.
Most of the early SMD LEDs used the improved SOT-23 with a transparent plastic body, with an outer size of 3.04×1.11mm and reel-type container taping packaging. Based on SOT-23, the SLM-125 series and SLM-245 series LEDs with high brightness SMD lenses were developed. The former is single-color light, and the latter is two-color or three-color light. In recent years, SMD LED has become a hot spot for development, which has well solved the problems of brightness, viewing angle, flatness, reliability, consistency, etc., using lighter PCB boards and reflective layer materials, requiring less epoxy resin to be filled in the display reflective layer, and removing the heavier carbon steel material pins. By reducing the size and weight, the weight of the product can be easily reduced by half, which ultimately makes the application more perfect, especially suitable for indoor and semi-outdoor full-color display applications.
The soldering pad is an important channel for heat dissipation. The data of SMD LED provided by manufacturers are based on 4.0×4.0mm soldering pads. Reflow soldering can be used to design the soldering pads to be equal to the pins. Ultra-high brightness LED products can use PLCC (plastic package with lead chip carrier)-2 package, with an outer size of 3.0×2.8mm. The high-brightness tube core is assembled by a unique method. The product thermal resistance is 400K/W. It can be welded in CECC mode. Its luminous intensity reaches 1250mcd under a driving current of 50mA. The character height of the seven-segment one-, two-, three- and four-digit digital SMD LED display devices is 5.08-12.7mm, and the display size selection range is wide. PLCC packaging avoids the manual insertion and pin alignment process required for the pin seven-segment digital display, meets the production requirements of automatic pick-and-place equipment, has flexible application design space, and displays bright and clear. The multi-color PLCC package has an external reflector and can be easily combined with a light-emitting tube or light guide to replace the current transmissive optical design with a reflective type to provide uniform lighting for a large area. A power SMD LED package that works under 3.5V, 1A driving conditions has been developed.
Power Packaging
LED chips and packages are developing towards high power. Under high current, the light flux is 10-20 times greater than that of Φ5mmLED. Effective heat dissipation and non-degrading packaging materials must be used to solve the light decay problem. Therefore, tube shell and packaging are also key technologies. LED packages that can withstand several W power have appeared. The 5W series of white, green, blue-green and blue power LEDs have been supplied since the beginning of 2003. The light output of white LEDs reaches 1871m, and the light efficiency is 44.31m/W. In order to solve the green light decay problem, LEDs that can withstand 10W power have been developed. The large-area tube size is 2.5×2.5mm, which can work under 5A current and the light output reaches 2001m. As a solid lighting source, there is great room for development.
Luxeon series power LED is a flip chip soldering of A1GalnN power flip chip die on a silicon carrier with solder bumps, and then the flip chip soldered silicon carrier is loaded into the heat sink and tube shell, and the bonding leads are packaged. This package is the best design for light extraction efficiency, heat dissipation performance, and increased working current density. Its main features are: low thermal resistance, generally only 14℃/W, only 1/10 of conventional LEDs; high reliability, the package is filled with stable flexible gel, in the range of -40-120℃, the internal stress caused by sudden temperature changes will not cause the gold wire to disconnect from the lead frame, and the epoxy resin lens will not turn yellow, and the lead frame will not be stained by oxidation; the optimal design of the reflector cup and lens makes the radiation pattern controllable and the optical efficiency the highest. In addition, its output light power, external quantum efficiency and other performance are excellent, which has brought the development of LED solid light sources to a new level.
The types of LED product packaging structures are also classified according to the characteristics of luminous color, chip material, luminous brightness, size, etc. A single tube core generally constitutes a point light source , and multiple tube cores can generally constitute a surface light source and a line light source for information, status indication and display. The light-emitting display is also composed of multiple tube cores, which are properly connected (including series and parallel) with a suitable optical structure to form the light-emitting segments and light-emitting points of the light-emitting display. Surface mount LEDs can gradually replace pin-type LEDs, and the application design is more flexible. They have occupied a certain share in the LED display market and have an accelerating development trend. Some solid lighting sources have been launched on the market, becoming the medium- and long-term development direction of LED in the future.
Leaded package
LED foot-type package uses lead frame as pins of various package shapes. It is the first package structure successfully developed and put on the market. There are many varieties and the technology is mature. The structure and reflective layer of the package are still being improved. Standard LED is considered by most customers to be the most convenient and economical solution in the display industry. The typical traditional LED is placed in a package that can withstand 0.1W input power. 90% of its heat is dissipated from the negative lead frame to the PCB board and then to the air. How to reduce the temperature rise of the pn junction during operation is a must for packaging and application. The encapsulation material is mostly high-temperature curing epoxy resin, which has excellent optical properties, good process adaptability, and high product reliability. It can be made into colored transparent or colorless transparent and colored scattering or colorless scattering
lens
package. Different lens shapes constitute a variety of shapes and sizes. For example, the circle is divided into several types according to the diameter, such as Φ2mm, Φ3mm, Φ4.4mm, Φ5mm, Φ7mm, etc. Different components of epoxy resin can produce different luminous effects.
There are many different packaging structures for colorful point light sources: ceramic base epoxy resin packaging has good operating temperature performance, the pins can be bent into the required shape, and the volume is small; metal base plastic reflective cover packaging is an energy-saving indicator light, suitable for power indication; the flashing type combines the CMOS oscillation circuit chip with the LED tube core, which can generate flashing light with strong visual impact; the two-color type is composed of two tube cores with different luminous colors, which are packaged in the same epoxy resin lens. In addition to the two colors, a third mixed color can be obtained. It is widely used in large-screen display systems and can be packaged to form a two-color display device; the voltage type combines the constant current source chip with the LED tube core, which can directly replace various voltage indicator lights of 5-24V. The surface light source is formed by bonding multiple LED tube cores to the specified position of the micro PCB board, using a plastic reflective frame cover and potting epoxy resin. The different designs of the PCB board determine the arrangement and connection of the external leads, and there are structural forms such as dual-row in-line and single-row in-line. Hundreds of package shapes and sizes have been developed for point and surface light sources for market and customer application.
LED light-emitting displays can be composed of various multi-digit products such as digital tubes or M-shaped tubes, symbol tubes, and matrix tubes, and can be designed into various shapes and structures according to actual needs. Taking digital tubes as an example, there are three packaging structures: reflective cover type, monolithic integrated type, and single seven-segment type. There are two connection methods: common anode and common cathode. One digit is usually called a digital tube, and more than two digits are generally called displays. The reflective cover type has the characteristics of large fonts, low material consumption, and flexible assembly. It is generally made of white plastic into a seven-segment shell with a reflective cavity. A single LED tube core is bonded to a PCB board that is aligned with the seven reflective cavities of the reflective cover. The center position of the bottom of each reflective cavity is the light-emitting area formed by the tube core. The leads are bonded by pressure welding, and epoxy resin is dripped into the reflective cover. It is aligned and bonded with the PCB board with the tube core, and then cured. The reflective cover type is divided into two types: empty seal and solid seal. The former uses epoxy resin with scattering agent and dye, and is mostly used for single-bit and double-bit devices; the latter is covered with color filter and uniform light film, and transparent insulating glue is applied on the tube core and the bottom plate to improve the light output efficiency. It is generally used for digital display with more than four digits. The monolithic integrated type is to make a large number of seven-segment digital display graphic tube cores on the luminous material wafer, and then cut them into single-chip graphic tube cores, bond, press weld, and package the shell with lens (commonly known as fisheye lens). The single-strip seven-segment type cuts the already made large-area LED chip into light strips containing one or more tube cores, so that the same seven strips are bonded to the digital font frame, and then pressed and epoxy resin packaged. The characteristics of the monolithic type and the single-strip type are miniaturization, and dual-in-line packaging can be used. Most of them are special products. The LED light column display is placed on a circuit board with a length of 106mm, with 101 tube cores (up to 201 tube cores). It is a high-density package that uses the principle of optical refraction to make a point light source form an image through 13-15 gratings of a transparent cover to complete the display of each tube core from point to line. The packaging technology is relatively complex.
The electroluminescence mechanism of semiconductor pn junction determines that LED cannot produce white light with continuous spectrum, and a single LED cannot produce more than two high-brightness monochromatic lights. It can only use fluorescent materials during packaging, and apply fluorescent powder on the blue or ultraviolet LED tube core to indirectly produce broadband spectrum and synthesize white light; or use several (two or three or more) tube cores that emit different colors to be packaged in a component shell, and form white light LED by mixing the colors . Both methods have been put into practical use. In 2000, Japan produced 100 million white light LEDs, which developed into a type of product that emits white light stably, and designed and assembled multiple white light LEDs into electric light sources that do not require high luminous flux, mainly for local decorative purposes, and pursue new trends.
Surface Mount Package
In 2002, surface mount LEDs (SMD LEDs) were gradually accepted by the market and gained a certain market share. The shift from pin-type packaging to SMD was in line with the general development trend of the entire electronics industry, and many manufacturers launched such products.
Most of the early SMD LEDs used the improved SOT-23 with a transparent plastic body, with an outer size of 3.04×1.11mm and reel-type container taping packaging. Based on SOT-23, the SLM-125 series and SLM-245 series LEDs with high brightness SMD lenses were developed. The former is single-color light, and the latter is two-color or three-color light. In recent years, SMD LED has become a hot spot for development, which has well solved the problems of brightness, viewing angle, flatness, reliability, consistency, etc., using lighter PCB boards and reflective layer materials, requiring less epoxy resin to be filled in the display reflective layer, and removing the heavier carbon steel material pins. By reducing the size and weight, the weight of the product can be easily reduced by half, which ultimately makes the application more perfect, especially suitable for indoor and semi-outdoor full-color display applications.
The soldering pad is an important channel for heat dissipation. The data of SMD LED provided by manufacturers are based on 4.0×4.0mm soldering pads. Reflow soldering can be used to design the soldering pads to be equal to the pins. Ultra-high brightness LED products can be packaged in PLCC (plastic packaged lead chip carrier)-2, with an outer size of 3.0×2.8mm. The high-brightness tube core is assembled by a unique method. The product thermal resistance is 400K/W. It can be welded in CECC mode. Its luminous intensity reaches 1250mcd at a driving current of 50mA. The character height of the seven-segment one-, two-, three- and four-digit SMD LED display devices is 5.08-12.7mm, and the display size selection range is wide. PLCC packaging avoids the manual insertion and pin alignment process required for the pin seven-segment digital display, meets the production requirements of automatic pick-and-place equipment, has flexible application design space, and displays bright and clear. The multi-color PLCC package has an external reflector and can be easily combined with a light-emitting tube or light guide to replace the current transmissive optical design with a reflective type to provide uniform lighting for a large area. A power SMD LED package that works under 3.5V, 1A driving conditions has been developed.
Power Packaging
LED chips and packages are developing towards high power. Under high current, the light flux is 10-20 times greater than that of Φ5mmLED. Effective heat dissipation and non-degrading packaging materials must be used to solve the light decay problem. Therefore, tube shell and packaging are also key technologies. LED packages that can withstand several W power have appeared. The 5W series of white, green, blue-green and blue power LEDs have been supplied since the beginning of 2003. The light output of white LEDs reaches 1871m, and the light efficiency is 44.31m/W. In order to solve the green light decay problem, LEDs that can withstand 10W power have been developed. The large-area tube size is 2.5×2.5mm, which can work under 5A current and the light output reaches 2001m. As a solid lighting source, there is great room for development.
Luxeon series power LED is a flip chip soldering of A1GalnN power flip chip die on a silicon carrier with solder bumps, and then the flip chip soldered silicon carrier is loaded into the heat sink and tube shell, and the bonding leads are packaged. This package is the best design for light extraction efficiency, heat dissipation performance, and increased working current density. Its main features are: low thermal resistance, generally only 14℃/W, only 1/10 of conventional LEDs; high reliability, the package is filled with stable flexible gel, in the range of -40-120℃, the internal stress caused by sudden temperature changes will not cause the gold wire to disconnect from the lead frame, and the epoxy resin lens will not turn yellow, and the lead frame will not be stained by oxidation; the optimal design of the reflector cup and lens makes the radiation pattern controllable and the optical efficiency the highest. In addition, its output light power, external quantum efficiency and other performance are excellent, which has brought the development of LED solid light sources to a new level.
The packaging structure of the Norlux series power LED is a multi-chip combination with a hexagonal aluminum plate as the base (making it non-conductive). The base has a diameter of 31.75mm, and the light-emitting area is located in the center of the base. The diameter is about (0.375×25.4)mm, which can accommodate 40 LED tube cores. The aluminum plate also serves as a heat sink. The bonding wires of the tube core are connected to the positive and negative electrodes through two contact points made on the base. The number of tube cores arranged on the base is determined according to the required output light power. The ultra-high brightness AlGaInN and AlGaInP tube cores that can be packaged can be combined. The emitted light is monochrome, color or synthetic white, and finally encapsulated with high refractive index materials according to the optical design shape. This package uses a conventional tube core high-density combination package, with high light extraction efficiency, low thermal resistance, better protection of the tube core and bonding wires, and high light output power under high current. It is also a promising LED solid light source.
In application, the packaged products can be assembled on a metal core PCB with an aluminum interlayer to form a power density LED. The PCB is used as the wiring for connecting the device electrodes, and the aluminum core interlayer can be used as a heat sink to obtain a higher luminous flux and photoelectric conversion efficiency. In addition, the packaged SMD LED is very small and can be flexibly combined to form a variety of lighting sources such as module type, light guide plate type, focusing type, and reflective type.
The packaging structure of the Norlux series power LED is a multi-chip combination with a hexagonal aluminum plate as the base (making it non-conductive). The base has a diameter of 31.75mm, and the light-emitting area is located in the center of the base. The diameter is about (0.375×25.4)mm, which can accommodate 40 LED tube cores. The aluminum plate also serves as a heat sink. The bonding wires of the tube core are connected to the positive and negative electrodes through two contact points made on the base. The number of tube cores arranged on the base is determined according to the required output light power. The ultra-high brightness AlGaInN and AlGaInP tube cores that can be packaged can be combined. The emitted light is monochrome, color or synthetic white, and finally encapsulated with high refractive index materials according to the optical design shape. This package uses a conventional tube core high-density combination package, with high light extraction efficiency, low thermal resistance, better protection of the tube core and bonding wires, and high light output power under high current. It is also a promising LED solid light source.
In application, the packaged products can be assembled on a metal core PCB with an aluminum interlayer to form a power density LED. The PCB is used as the wiring for connecting the device electrodes, and the aluminum core interlayer can be used as a heat sink to obtain a higher luminous flux and photoelectric conversion efficiency. In addition, the packaged SMD LED is very small and can be flexibly combined to form a variety of lighting sources such as module type, light guide plate type, focusing type, and reflective type.
Previous article:Technical requirements for solar LED lamps
Next article:The reasons for the long life of LED
Recommended ReadingLatest update time:2024-11-16 15:54
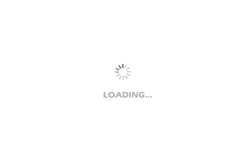
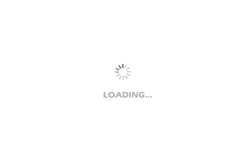
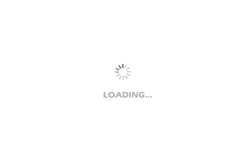
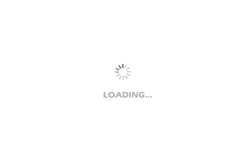
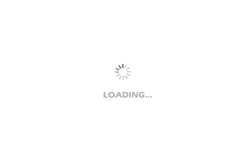
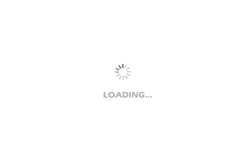
- Popular Resources
- Popular amplifiers
- MathWorks and NXP Collaborate to Launch Model-Based Design Toolbox for Battery Management Systems
- STMicroelectronics' advanced galvanically isolated gate driver STGAP3S provides flexible protection for IGBTs and SiC MOSFETs
- New diaphragm-free solid-state lithium battery technology is launched: the distance between the positive and negative electrodes is less than 0.000001 meters
- [“Source” Observe the Autumn Series] Application and testing of the next generation of semiconductor gallium oxide device photodetectors
- 采用自主设计封装,绝缘电阻显著提高!ROHM开发出更高电压xEV系统的SiC肖特基势垒二极管
- Will GaN replace SiC? PI's disruptive 1700V InnoMux2 is here to demonstrate
- From Isolation to the Third and a Half Generation: Understanding Naxinwei's Gate Driver IC in One Article
- The appeal of 48 V technology: importance, benefits and key factors in system-level applications
- Important breakthrough in recycling of used lithium-ion batteries
- Innolux's intelligent steer-by-wire solution makes cars smarter and safer
- 8051 MCU - Parity Check
- How to efficiently balance the sensitivity of tactile sensing interfaces
- What should I do if the servo motor shakes? What causes the servo motor to shake quickly?
- 【Brushless Motor】Analysis of three-phase BLDC motor and sharing of two popular development boards
- Midea Industrial Technology's subsidiaries Clou Electronics and Hekang New Energy jointly appeared at the Munich Battery Energy Storage Exhibition and Solar Energy Exhibition
- Guoxin Sichen | Application of ferroelectric memory PB85RS2MC in power battery management, with a capacity of 2M
- Analysis of common faults of frequency converter
- In a head-on competition with Qualcomm, what kind of cockpit products has Intel come up with?
- Dalian Rongke's all-vanadium liquid flow battery energy storage equipment industrialization project has entered the sprint stage before production
- Allegro MicroSystems Introduces Advanced Magnetic and Inductive Position Sensing Solutions at Electronica 2024
- Car key in the left hand, liveness detection radar in the right hand, UWB is imperative for cars!
- After a decade of rapid development, domestic CIS has entered the market
- Aegis Dagger Battery + Thor EM-i Super Hybrid, Geely New Energy has thrown out two "king bombs"
- A brief discussion on functional safety - fault, error, and failure
- In the smart car 2.0 cycle, these core industry chains are facing major opportunities!
- The United States and Japan are developing new batteries. CATL faces challenges? How should China's new energy battery industry respond?
- Murata launches high-precision 6-axis inertial sensor for automobiles
- Ford patents pre-charge alarm to help save costs and respond to emergencies
- New real-time microcontroller system from Texas Instruments enables smarter processing in automotive and industrial applications
- 【MM32 eMiniBoard Review】2a. Found that the virtual serial port may have problems, and the serial port routines cannot receive
- Help! Does anyone know what sensor this is?
- Do you usually read e-books or paper books now?
- ADC12 single channel multiple conversion routine (MSP430F5529)
- Motor startup interferes with the microcontroller problem
- Chapter 3 Interrupts, Clocks, and Low Power Consumption
- The difference between C64x+ and C64x CACHE in the C6000 series
- Realization of voltage to current conversion in Multisim12
- 【Smart Network Desk Lamp】7. Get real-time weather information and analyze it
- [RISC-V MCU CH32V103 Review] +01 Try the use of GPIO to light up the first LED