When designing a battery-powered product, it is obvious that one would like the battery life to be as long as possible. As a rapidly growing category of devices, applications that grow from a single battery are not just about the specifications: they revolve around the entire product concept. Energy-sensitive product applications can be broadly divided into energy metering systems, home and building automation, security, and medical systems (Figure 1). These products are usually centered around a microcontroller (MCU) and must operate for a long time from a single primary battery. In some applications, it is difficult or even impossible to replace the battery: in others, the end user is unwilling to pay the cost of replacing the battery.
In applications like these, very active microprocessors with very low duty cycles may spend 99% of their time in a "deep sleep" state - even higher, 99.9% is not uncommon. Microprocessors "wake up" in a cycle or in response to some stimulus, perform an operation, and return to sleep. Since they spend so much time asleep, it is obvious that the key parameter to get the longest battery life is the current consumption in the powered-down state. However, the difference between a three or four-year life on the same battery and more than 10 years, extending to 20 years, or even longer, lies in paying close attention to every aspect of how the task uses the MCU's resources, and how the MCU itself is designed to reduce energy consumption in various ways.
A single battery lasts 20 years
The CR2032 coin cell is widely used in small MCUs such as remote environmental sensors. It is a lithium/manganese dioxide 3V primary cell. Typical suppliers - for example, Kodak (reference 1) - rate 230 mAh to 2V end voltage capability at 5.6 k (about 0.5 mA). If that is the case, the battery life will be 400 hours, compared to 200,000 hours for energy-sensitive applications. This particular battery has a very good shelf life or self-discharge rate, with the data sheet showing 90% capacity after 10 years. Very similarly, this is equivalent to a continuous charge of about 0.25 A, and if a battery life of 10-20 years can be achieved, the general requirements of the application will be met.
With battery life coming with a finite amount of charge, designers must reduce their product’s current and time during all phases of the MCU’s operation, not just by microamps, but by microseconds of every action.
To reduce the current consumed in deep sleep modes, it has become common to use 8-bit (or 16-bit) cores in MCUs for energy-sensitive applications. The reason is that 8-bit cores—even in their latest versions—are small, have relatively few gates, and have low static or leakage currents. However, many current applications require more processing power than an 8-bit core can provide. In other MCU application areas, users often choose to upgrade from an 8-bit to a 32-bit environment. In the case of low power, it has been assumed that the current used by a 32-bit core in its power-down mode state must be unacceptably high. With the advent of a full range of low-power design techniques, today's IC designers have made it possible for a 32-bit ARM core to provide different low-power modes that are as good as or better than its 8-bit competitors, while also achieving fast wake-up times. The higher processing performance of 32-bit processors also enables the MCU to complete tasks faster, allowing it to spend more time in these low-power modes, further reducing average power consumption.
Low power peripheral functions
Optimizing MCU sleep state power consumption for the lowest power draw requires a holistic design approach. In addition to the core, other blocks in the MCU continue to draw some current in standby devices, voltage regulators, bias current generators, brownout detection comparators, and power-on reset circuits. In almost all cases, a simple swap applies; the deeper the power-down state, the more peripheral functions are completely cut off, and the longer it takes for the chip to wake up and be ready to perform processing tasks. Because applications vary greatly, it is important for MCU designers to provide a flexible expansion kit in the form of power-down states so that the product designer can make the best swap between standby power and responsiveness for his individual project.
Designing an ARM core to achieve current levels in the nanoamp region at its deepest sleep state is just one step in a low-energy strategy. The processing power available to a 32-bit core opens up new ways to control energy use. At any given time, it is the area below the MCU power graph that represents the charge being taken from the battery over time (Figure 2). As it is, the more the headline figure for current consumption in a specific configuration, the closer the designer must pay to maximize battery life. In the development kit for the EFM32 microcontroller, this measurement is made clear; a fundamental part of the kit’s functionality is its advanced energy monitor (Figure 3). This facility continuously measures the current in the current rail that populates the MCU core; an analog-to-digital converter (ADC) samples the voltage across a resistor, and the development kit software integrates its readings to accurately measure power over time.
[page]
A 32-bit core spends less time actively completing an identical task than a less capable MCU: at the same time, the core should also use as little power as possible while running. IC designers focused on low power have been given many refinements to achieve their goals. Examples include optimizing the clock gating structures of all chip synchronous logic, and organizing the bus system and memories – SRAM and flash – for minimal switching in any given process. Adopting a comprehensive low-power design approach results in an ARM Cortex-M3 core running typical code in flash using as little as 180μA/MHz. Careful use of these same techniques ensures that the numbers measured are accurate, down to the low clock rate, not just a peak performance number. The M3 core’s use of the Thumb2 instruction set also helps reduce “active time” once the MCU is awake and executing application code. With such a compact 16-bit instruction fetch capability, the Thumb2 ISA is very efficient.
MCU designers have many better strategies to deploy when it comes to reducing the current-time-multiplied-microseconds product. One is to reduce not only the time the core spends actually processing application code, but also the settling time between the wake-up stimulus - whether timed-generated or event-driven - and the time the CPU is ready to do "real work". One line of attack is to minimize the startup time and the clock signal supplied to the core. It is well known that when a crystal oscillator is started up from an off state, it takes some time for its output to stabilize before it can be used as a system clock. In contrast, an RC oscillator may not be accurate enough to serve as a time base for all the tasks that the MCU must do, but will produce a regular output almost instantly after power-up. Part of the solution is to reduce the time that the signals are supplied simultaneously; the CPU starts running at power-up, using the RC oscillator to adjust the clock, while a small control circuit waits for it to stabilize before passing the clock source to a crystal oscillator. Any lack of frequency accuracy in the RC oscillator's output is less significant because the period in which it is used is relatively short.
Simple tasks do not require an MCU core
While designers take great care to provide power with a capable processing core, and to achieve this goal in the shortest possible time, it is useful for chip designers and system designers to ask whether such a core is needed for a given task: even the most energy-efficient core will waste battery charge if it is woken up to perform simple tasks. Let's use the example of an environmental sensor application again - it may need to take measurements periodically, but only report the measurements to a central data logger at infrequent intervals. The software stack running the communication interface will certainly require waking up the MCU core, but more frequently turning on the analog-to-digital converter, directing the A/D conversion, and accumulating the results in low-power memory will consume very little power if only the peripherals are required to operate autonomously under the control of the interconnect matrix (Figure 4). Because applications vary greatly, a high degree of flexibility in choosing which functional blocks to power and how they are connected is important to fully exploiting this concept.
Adding Code to the Power Budget
It is well known that in modern CMOS semiconductor processes, the cost of adding silicon area to hardwired block ICs is relatively low. This has the slightly counterintuitive consequence that the most effective option to minimize power consumption is often to increase the number of gates. With advanced clock tree design, clock gating, and board power switches, IC designers can easily completely cut power at any time. One prominent feature of this approach is encryption. Even seemingly mundane data is now routinely secured by encryption, with the algorithm commonly known as AES. This is not a challenging task for a 32-bit MCU core, but it does take up a lot of processor cycles, extending the total microamperes times the total microseconds. Most of these cycles are spent executing the algorithm in some internal loop; adding an AES accelerator hardware module will cause the MCU to stop the AES algorithm and move to dedicated hardware, and get along well with the other processors to get the encrypted (or decrypted) results in fewer cycles.
The rapidly expanding class of energy-sensitive applications - led by a few high-end categories such as smart energy metering - is redefining what it means to be a battery-powered product: these products must provide service on a single battery and compare the shelf life of the battery itself to the same range of maximum time intervals specified by the battery manufacturer: up to, or even beyond, 20 years. Only a highly integrated single-chip microcontroller can provide a realistic solution for such designs. IC designers have paid close attention to every aspect of low-power chip design and can now provide product designers with modern, powerful 32-bit processor cores while minimizing power requirements.
Previous article:New trends in security system integration in urban rail transit
Next article:Design of high stability laser multi-channel monitoring system based on AD7888
Recommended ReadingLatest update time:2024-11-16 16:56
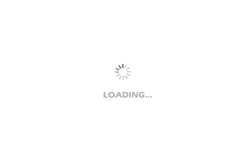
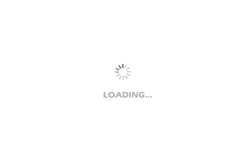
- Popular Resources
- Popular amplifiers
- Mir T527 series core board, high-performance vehicle video surveillance, departmental standard all-in-one solution
- Akamai Expands Control Over Media Platforms with New Video Workflow Capabilities
- Tsinghua Unigroup launches the world's first open architecture security chip E450R, which has obtained the National Security Level 2 Certification
- Pickering exhibits a variety of modular signal switches and simulation solutions at the Defense Electronics Show
- Parker Hannifin Launches Service Master COMPACT Measuring Device for Field Monitoring and Diagnostics
- Connection and distance: A new trend in security cameras - Wi-Fi HaLow brings longer transmission distance and lower power consumption
- Smartway made a strong appearance at the 2023 CPSE Expo with a number of blockbuster products
- Dual-wheel drive, Intellifusion launches 12TOPS edge vision SoC
- Toyota receives Japanese administrative guidance due to information leakage case involving 2.41 million pieces of user data
- Innolux's intelligent steer-by-wire solution makes cars smarter and safer
- 8051 MCU - Parity Check
- How to efficiently balance the sensitivity of tactile sensing interfaces
- What should I do if the servo motor shakes? What causes the servo motor to shake quickly?
- 【Brushless Motor】Analysis of three-phase BLDC motor and sharing of two popular development boards
- Midea Industrial Technology's subsidiaries Clou Electronics and Hekang New Energy jointly appeared at the Munich Battery Energy Storage Exhibition and Solar Energy Exhibition
- Guoxin Sichen | Application of ferroelectric memory PB85RS2MC in power battery management, with a capacity of 2M
- Analysis of common faults of frequency converter
- In a head-on competition with Qualcomm, what kind of cockpit products has Intel come up with?
- Dalian Rongke's all-vanadium liquid flow battery energy storage equipment industrialization project has entered the sprint stage before production
- Allegro MicroSystems Introduces Advanced Magnetic and Inductive Position Sensing Solutions at Electronica 2024
- Car key in the left hand, liveness detection radar in the right hand, UWB is imperative for cars!
- After a decade of rapid development, domestic CIS has entered the market
- Aegis Dagger Battery + Thor EM-i Super Hybrid, Geely New Energy has thrown out two "king bombs"
- A brief discussion on functional safety - fault, error, and failure
- In the smart car 2.0 cycle, these core industry chains are facing major opportunities!
- The United States and Japan are developing new batteries. CATL faces challenges? How should China's new energy battery industry respond?
- Murata launches high-precision 6-axis inertial sensor for automobiles
- Ford patents pre-charge alarm to help save costs and respond to emergencies
- New real-time microcontroller system from Texas Instruments enables smarter processing in automotive and industrial applications
- CH549EVT development board test - touch button plus running light test
- Why are relays still used to drive automotive motors?
- [AIoT Smart Smoke Detection System] Product Design Background
- Simulation research on high frequency antenna protection design
- Please give some advice on the working mode of the boost circuit
- i.MX6ULL Embedded Linux Development 6-System Burning to eMMC and the Pitfalls Encountered!
- Gowin GW1N development board logic analyzer speed test
- Which MSP430FR6972 development board is suitable?
- Please recommend some easy-to-understand books or web links about phase detectors and frequency detectors. Thank you.
- PS2 Interface.pdf