Test speed is very important for the production of all electronic components, and before RF testing can be performed, the DC operation of these devices must be tested. For diodes, this includes forward voltage drop, reaction breakdown voltage and junction leakage current, while for transistors, it also includes different junction breakdown voltage, junction leakage current, collector or drain characteristics, etc. This article explores ways to speed up these tests by selecting the right test instrument and setting it up appropriately.
For all manufacturers of electronic components, test speed is very important, but it is even more critical for low-priced two- and three-pin components such as diode and triode transistors. Before RF testing can be performed, these devices must be tested for DC operation. For diodes, this includes forward voltage drop, response breakdown voltage and junction leakage current. For transistors, this includes different junction breakdown voltages, junction leakage currents, collector or drain characteristics, etc. Choosing the right test instrument and using the appropriate settings can greatly speed up these testing processes.
Instrument selection
Although testing can be accomplished using a variety of digital multimeters (DMMs), voltage sources, and current sources, compared to a test system that contains all these functions in a single unit, it will take up more rack space and require multiple learning curves. The command set, system programming and maintenance are also more complex. Most importantly, triggering times become complex and triggering uncertainty increases, while coordinating the operation of discrete instruments increases bus communication traffic and reduces test efficiency.
To solve these problems, the first step is to integrate several functions into a single instrument. The source-measure unit (SMU) integrates precision voltage sources, precision current sources, voltmeters, and ammeters into one instrument, saving space and simplifying operations between devices. The second is to eliminate the communication delay between the instrument and the control computer.
Reduce communication overhead
As high-speed communication between instruments and computers becomes possible, command and control are provided for each step of the test through the GPIB (IEEE-488 bus) link, making test system automation more extensive. While this is a huge improvement over before, there are still significant speed limitations. First, GPIB requires considerable communication overhead. Another disadvantage of GPIB used for real-time testing is that control usually comes from the other end of the bus - a PC running the Windows operating system. Windows has significant delays in communication response and is unpredictable, which makes using a PC as the only option in a test environment. Synchronization of multiple instruments is almost impossible when using a controller.
![]() |
Figure 1: Measurement equipment setup for diode testing. |
The solution to this problem is to use GPIB to preconfigure the instrument and then let the instrument perform the tests on its own. Many modern instruments have source memory list programming capabilities that allow up to 100 complete test sequences to be set up and run without PC intervention. Each test can contain different instrument configurations and test conditions and can include configuration of sources, measurements, conditional jumps, math functions, and pass/fail limit testing and storage functions. Certain units can be run in DC or pulse mode with different parameters and timing, making it possible to slow down more sensitive tests or speed up others to optimize the overall test time course.
When the instrument runs essentially autonomously, the GPIB's role is to download the test program before testing and upload the results to the PC after testing, neither of which interferes with the actual testing.
Instrument trigger
To implement a simple current-voltage sweep (IV), the SMU outputs a series of voltages while measuring the corresponding current. At each voltage level, the SMU first provides a voltage. Voltage changes in the circuit will cause a transient current, so setting an appropriate delay between stimulus and measurement is critical to test integrity. The instrument will automatically adjust the delay within different ranges to produce the best results. However, attaching additional components to the test circuit, such as long cables, switch matrices, etc., will change the transient characteristics of the circuit. For high-resistance devices, longer test times are often necessary. In these cases, the user needs to define additional delays to maintain measurement integrity.
Diode testing
Our first example includes the test instrument, device handler, and PC (Figure 1), and here we need to pay attention to how to eliminate most GPIB communication through internal programming to speed up the test.
Production testing of diodes includes verification steps to determine the polarity of the diode under test and then testing forward voltage drop, reverse breakdown voltage, and leakage current.
Forward voltage drop is the voltage across a diode at some specified forward current and is obtained by passing a specified current through the diode and then measuring the voltage across it. Reverse breakdown voltage (V RM or V BR ) is the reverse voltage when the current suddenly increases infinitely, which is measured by applying a reverse current and measuring the voltage across the diode. The voltage read is compared to specific minimum limits to determine pass or fail of the test. The leakage current I R is sometimes called the reverse saturation current. I S is the current when a voltage less than the reverse breakdown voltage is applied to the diode. It is obtained by applying a specific reverse voltage and measuring the resulting current. . Write a program to set up the diode test in the memory location of the source/memory instrument, and then start execution through a trigger transmitted through the IEEE bus. The instrument performs operations according to the set programming location in the memory without computer intervention.
![]() |
Figure 2: Two SMUs are generally used in transistor testing, the first one is between the HBT base and emitter, and the second one is between the emitter and collector. |
RF power transistor test
Although many types of RF transistors exist, we use the heterojunction bipolar transistor (HBT) as an example. Similar tests can be used for other devices. Since the transistor is a three-terminal device, two SMUs are usually required. Figure 2 shows two SMUs connected to the device, the first between the base and emitter of the HBT and the second between the emitter and collector. To obtain the collector curve of the HBT, the base SMU is set to output current and measure the voltage. After setting the first base current, measure the collector current while scanning the collector voltage. The base current is then increased by one step, the collector voltage is swept again and the collector current is measured simultaneously. Repeat this process until all collector IV curves are obtained for different base current conditions.
Instrument synchronization
Since we want both instruments to be programmed (to avoid GPIB delays), we want all instruments in the test setup to be synchronized. At first, this wasn't a problem. For example, if several SMUs have the same firmware and are programmed with the same test parameters, the execution time of each step will be the same. The difficulty comes from the memory location recall and auto-ranging steps, which take an uncertain amount of time.
In situations like this it is necessary to use an external, specialized trigger controller to ensure that measurements from multiple instruments occur simultaneously. This is particularly useful when the test system uses equipment from different manufacturers, or even from the same manufacturer but with different triggering methods.
The process is as follows (the example used refers to Keithley instruments, but similar methods can be used for instruments from other manufacturers):
1. The trigger controller outputs a trigger signal to each instrument.
2. Recalls the source memory location from memory.
3.Enable source output for all instruments.
4. Each instrument executes with a user-defined delay.
5. Once the delay operation is completed, each instrument outputs a trigger signal to the controller.
6. The trigger controller waits for the trigger signal (delay output) output by each instrument.
7.The trigger controller sends a trigger signal (measurement input) to each instrument.
8. Each instrument starts measurement operations.
9. After completing the measurement, each instrument sends a trigger signal to the controller.
10. The trigger controller waits for the trigger signal (measurement output) output by each instrument.
11.Go back to step 1 to start the next test.
![]() |
Figure 3: a: Collector-emitter breakdown voltage, base open circuit; b: Collector-emitter breakdown voltage, base short circuit; c: Collector turn-off current, ICBO, and collector-base strike voltage, the emitter is open circuit. |
Specific transistor testing
HBT usually has two important breakdown voltages that need to be measured: The first is the collector-emitter breakdown voltage, which can be measured when the base is open or short-circuited. Figure 3a shows an open base (BV CEO or V (BR) The setup for measuring the collector-emitter breakdown voltage under CEO ), Figure 3b shows the setup for measuring the collector-emitter breakdown voltage under base short circuit (BV CES or V (BR)CES ). The other breakdown voltage is the collector-to-base breakdown voltage (BV CBO or V (BR)CBO ), which is typically measured with an open emitter. Figure 3c shows this test setup. In these measurements, the source-measure unit scans the voltage across the HBT while measuring the current. The current will remain very constant until the breakdown voltage is reached, after which it will suddenly increase.
Usually other parameters to be measured for RF power transistors include the collector-emitter continuous voltage, BV CEO(sus) or V CE(sus) . When reverse bias is used on the junction between the base and the emitter, the collector - The breakdown voltage of the emitter (BV CEV or BV CEX ), and the emitter-base breakdown voltage with the collector open (BV EBO ).
Junction leakage current
It is also important to describe the leakage current when the device is turned off because leakage current wastes power when the device is not operating and can shorten the operating time of battery-powered devices. The most commonly measured leakage current parameter is collector off current (I CBO ), measured between collector and base with the emitter open (Figure 3c). Base reverse-bias leakage current, also known as emitter turn-off current or emitter-base turn-off current (I EBO ), is another of the most important leakage currents. It is the leakage from the base when the device is turned off. current.
Previous article:
Next article:Design of ranging system based on ultrasonic sensor
Recommended ReadingLatest update time:2024-11-16 22:38
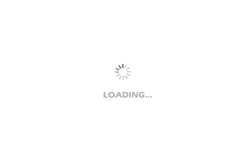
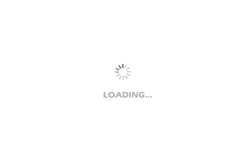
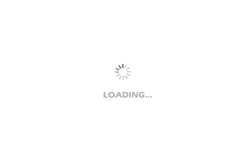
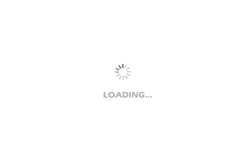
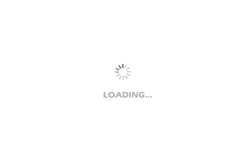
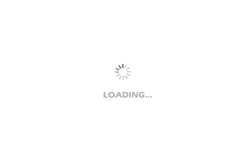
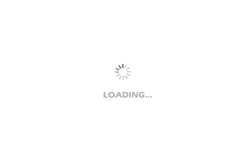
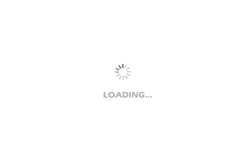
- Popular Resources
- Popular amplifiers
-
Radio Frequency Identification (RFID) System Technology and Application (Written by Ci Xinxin, Wang Subin, and Wang Shuo)
-
Modern Electronic Technology Training Course (Edited by Yao Youfeng)
-
Sensor Principle and Application Circuit Design (Edited by Chen Shuwang, Song Lijun, Xu Yunfeng)
-
Single-chip microcomputer C language programming and simulation
- Keysight Technologies Helps Samsung Electronics Successfully Validate FiRa® 2.0 Safe Distance Measurement Test Case
- From probes to power supplies, Tektronix is leading the way in comprehensive innovation in power electronics testing
- Seizing the Opportunities in the Chinese Application Market: NI's Challenges and Answers
- Tektronix Launches Breakthrough Power Measurement Tools to Accelerate Innovation as Global Electrification Accelerates
- Not all oscilloscopes are created equal: Why ADCs and low noise floor matter
- Enable TekHSI high-speed interface function to accelerate the remote transmission of waveform data
- How to measure the quality of soft start thyristor
- How to use a multimeter to judge whether a soft starter is good or bad
- What are the advantages and disadvantages of non-contact temperature sensors?
- Innolux's intelligent steer-by-wire solution makes cars smarter and safer
- 8051 MCU - Parity Check
- How to efficiently balance the sensitivity of tactile sensing interfaces
- What should I do if the servo motor shakes? What causes the servo motor to shake quickly?
- 【Brushless Motor】Analysis of three-phase BLDC motor and sharing of two popular development boards
- Midea Industrial Technology's subsidiaries Clou Electronics and Hekang New Energy jointly appeared at the Munich Battery Energy Storage Exhibition and Solar Energy Exhibition
- Guoxin Sichen | Application of ferroelectric memory PB85RS2MC in power battery management, with a capacity of 2M
- Analysis of common faults of frequency converter
- In a head-on competition with Qualcomm, what kind of cockpit products has Intel come up with?
- Dalian Rongke's all-vanadium liquid flow battery energy storage equipment industrialization project has entered the sprint stage before production
- Allegro MicroSystems Introduces Advanced Magnetic and Inductive Position Sensing Solutions at Electronica 2024
- Car key in the left hand, liveness detection radar in the right hand, UWB is imperative for cars!
- After a decade of rapid development, domestic CIS has entered the market
- Aegis Dagger Battery + Thor EM-i Super Hybrid, Geely New Energy has thrown out two "king bombs"
- A brief discussion on functional safety - fault, error, and failure
- In the smart car 2.0 cycle, these core industry chains are facing major opportunities!
- The United States and Japan are developing new batteries. CATL faces challenges? How should China's new energy battery industry respond?
- Murata launches high-precision 6-axis inertial sensor for automobiles
- Ford patents pre-charge alarm to help save costs and respond to emergencies
- New real-time microcontroller system from Texas Instruments enables smarter processing in automotive and industrial applications
- Overview of MCU bus, three-bus structure of MCU
- Most Popular Blogs of 2021: Connect, Power, and Protect
- Recruiting circuit engineers with high salary (Nantong Intelligent Perception Research Institute, Shanghai Institute of Technical Physics, Chinese Academy of Sciences)
- Does anyone have the schematic diagram of jmb366?
- If the clamp meter (multimeter) does not measure but there are still numbers, is it a malfunction?
- RK3399 open source motherboard hardware and software information released - free download
- Low Noise Amplifier LNA——ATF54143
- EEWORLD University Hall - Digital Oscilloscope Operation Digital Oscilloscope Operation_National Taiwan Normal University_Teacher Zhang Guowei
- [ESP32-Audio-Kit Audio Development Board Review] Part 1: Building esp-idf and esp-adf development environments based on vs code
- [Raspberry Pi Pico Review] Pico power supply part