If you use the shunt-thru method and use 1 MΩ inputs instead of 50 Ω, you can ignore the DC block on the T port.
Other methods for measuring high-voltage converters include the current-voltage sensing method, or a similar method using the Picotest J2111A current injector (www.picotest.com). These methods are less accurate than the shunt-through method but are better suited for high-voltage converters (up to 40 Vdc).
Figure 15. Example of configuration for shunt-through measurement method
In order to accurately measure extremely small resistances in the milliohm range, the probe contact resistance should be very small during the measurement process. The measurement terminal should be in contact with the device under test through a 2-port probe [1] [2]. In practice, we recommend that you solder the measurement terminal to the device under test. If the two measurement terminals are combined and the device under test is contacted by single-ended probing, the lead of the measurement port should be as short as possible, because its residual impedance will directly affect the measurement accuracy of the milliohm impedance.
Figure 16 is an example of using the 2-port probing method. In the figure, two homemade probes are connected to the ends of the test cable, and the probes are in contact with the output terminals of the device under test. Homemade probes can be made using SMA connectors (cut off its three ground pins, and then use the remaining ground pins and the center pin for probing) or SMA semi-rigid cables (cut the cable short, strip the middle conductor, and then solder a short pin to the outer conductor).
When performing a THRU response calibration, make sure the electrical length of the THRU component is approximately equal to the electrical length of the two probes.
Figure 16. Probing example of the shunt-through method
DC-DC Converter Output Impedance Measurement Example
Figures 17 and 18 show measurement examples of the output impedance of a 5 V to 3.3 V DC-DC converter using the shunt-through method and the E5061B gain-phase test port. The device under test is the same converter used in the loop gain measurement example in the previous chapter, and the measurement frequency range is 10 Hz to 10 MHz. The IFBW is set to Auto/Maximum 10 Hz, and the port T attenuator is set to 0 dB. During the measurement, the power of the excitation source is set to 10 dBm; when doing the through response calibration, the power of the excitation source is set to -5 dBm.
Note: When powering on or off the converter, we recommend temporarily changing the attenuation value of the T port attenuator from 0 dB to 20 dB to prevent the converter's transient output voltage from overloading the measurement receiver. If the instrument enters overload protection mode due to a transient high voltage, the method to recover is: Press the [System] button on the instrument panel, select the "Overload Recovery" and "Clear Overload Protection" buttons.
The | Z | traces are plotted using the impedance analysis function (gain-phase shunt-through method) of the E5061B-005. The left trace in Figure 17 shows the measurement results of | Z | with the converter and electronic load turned off.
As shown in the figure, the output impedance of the converter in the off state indicates the self-resonant impedance response of the converter's output capacitor. The trace on the right is the trace of | Z | measured under 0.3 A load conditions. As shown in the figure, | Z | is limited to less than 2 mΩ in the low frequency range by the feedback loop of the converter. Due to the unique receiver architecture of the gain-phase test port, the E5061B can correctly measure small impedances in the milliohm range, even at measurement frequencies below 10 Hz, and the measurement results are not affected by the ground loop of the test cable between the stimulus source and the receiver.
Figure 18 shows the traces of | Z | measured under 1 A and 2 A load conditions. As shown in the figure, in the low frequency range, the impedance of the device under test is higher than that under 0.3 A load condition. It is usually necessary to measure the output impedance under various load conditions, which allows us to know whether the output impedance of the device under test can be maintained within our desired target and whether the impedance change is small enough when the load condition changes.
Another important thing is to make sure that the trace of the output impedance does not have large forward peaks, as that will cause transient noise under all load conditions.
Figure 17. DC-DC converter output impedance measurement
At power-off state and 0.3 A load,
start frequency = 10 Hz, stop frequency = 10 MHz,
source power = 10 dBm (-5 dBm for THRU calibration)
T port: ATT = 0 dB, Zin = 50 Ω, R port: ATT = 20 dB, Zin = 50 Ω
Figure 18. DC-DC converter output impedance measurement
1 A and 2 A load conditions,
start frequency = 10 Hz, stop frequency = 10 MHz
Source power = 10 dBm (-5 dBm for thru calibration)
T port: ATT = 0 dB, Zin = 50 Ω, R port: ATT = 20 dB, Zin = 50 Ω
Previous article:Basics of Dielectric Material Measurement
Next article:Five things to consider before buying a digital multimeter
Recommended ReadingLatest update time:2024-11-16 20:50
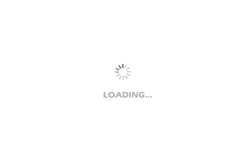
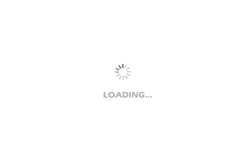
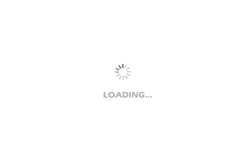
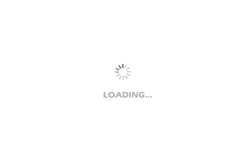
- Popular Resources
- Popular amplifiers
-
New Energy Vehicle Detection and Diagnosis Experiment (Edited by Mao Caiyun, Zhou Xien, and Long Jiwen)
-
Virtualization Technology Practice Guide - High-efficiency and low-cost solutions for small and medium-sized enterprises (Wang Chunhai)
-
Design of an adaptive constant on-time buck DC-DC converter with high efficiency and low power consumption
-
Research on design technology of high-efficiency step-up DC-DC converter with wide load range
- Keysight Technologies Helps Samsung Electronics Successfully Validate FiRa® 2.0 Safe Distance Measurement Test Case
- From probes to power supplies, Tektronix is leading the way in comprehensive innovation in power electronics testing
- Seizing the Opportunities in the Chinese Application Market: NI's Challenges and Answers
- Tektronix Launches Breakthrough Power Measurement Tools to Accelerate Innovation as Global Electrification Accelerates
- Not all oscilloscopes are created equal: Why ADCs and low noise floor matter
- Enable TekHSI high-speed interface function to accelerate the remote transmission of waveform data
- How to measure the quality of soft start thyristor
- How to use a multimeter to judge whether a soft starter is good or bad
- What are the advantages and disadvantages of non-contact temperature sensors?
- Innolux's intelligent steer-by-wire solution makes cars smarter and safer
- 8051 MCU - Parity Check
- How to efficiently balance the sensitivity of tactile sensing interfaces
- What should I do if the servo motor shakes? What causes the servo motor to shake quickly?
- 【Brushless Motor】Analysis of three-phase BLDC motor and sharing of two popular development boards
- Midea Industrial Technology's subsidiaries Clou Electronics and Hekang New Energy jointly appeared at the Munich Battery Energy Storage Exhibition and Solar Energy Exhibition
- Guoxin Sichen | Application of ferroelectric memory PB85RS2MC in power battery management, with a capacity of 2M
- Analysis of common faults of frequency converter
- In a head-on competition with Qualcomm, what kind of cockpit products has Intel come up with?
- Dalian Rongke's all-vanadium liquid flow battery energy storage equipment industrialization project has entered the sprint stage before production
- Allegro MicroSystems Introduces Advanced Magnetic and Inductive Position Sensing Solutions at Electronica 2024
- Car key in the left hand, liveness detection radar in the right hand, UWB is imperative for cars!
- After a decade of rapid development, domestic CIS has entered the market
- Aegis Dagger Battery + Thor EM-i Super Hybrid, Geely New Energy has thrown out two "king bombs"
- A brief discussion on functional safety - fault, error, and failure
- In the smart car 2.0 cycle, these core industry chains are facing major opportunities!
- The United States and Japan are developing new batteries. CATL faces challenges? How should China's new energy battery industry respond?
- Murata launches high-precision 6-axis inertial sensor for automobiles
- Ford patents pre-charge alarm to help save costs and respond to emergencies
- New real-time microcontroller system from Texas Instruments enables smarter processing in automotive and industrial applications
- Arduino's new product Nicla Vision
- The STM8S003F3P6 chip is very interesting
- Serial port cannot be recognized
- The design is too exquisite, but the repair is too painful: iFixit releases a teardown report of AirPods 2, and the repairability score is zero
- 【Wireless closed-loop feedback system for desktop robotic arms】
- 8/21-22@Wuhan! Intel/World Peace Group invites you to participate in the Artificial Intelligence Technology Introduction and Implementation Seminar
- Professor Li Xia: How basic should basic research be?
- DSP Flash API Steps
- 【i.MX6ULL】Driver Development 11——LCD Driver Practice
- Microcontroller interview question collection