Measuring the output impedance of a DC-DC converter
For the PDN that supplies power to the new LSI operating at low voltage and high current, it is very important to measure its extremely small impedance. Here, if we assume that Zpdn is the impedance between Vdd and the ground plane seen from the load device end, Delta-I is the current change caused by the operation of the load device, and a voltage drop Delta-V = Delta-i x Zpdn will be generated on the power supply layer. More strictly speaking, the voltage drop should be:
Delta-V = IFFT (FFT (delta-I) x Zpdn). [1]
For high-performance LSI applications such as MPUs, Delta-I may be several amperes or tens of amperes, and the voltage drop Delta-V is no longer a trivial issue because it can cause signal integrity and electromagnetic interference (EMI) problems. To avoid these problems, the impedance Zpdn of the power layer must be suppressed to an extremely small value in the wide frequency range from DC to GHz. In the low-frequency range, PDN is often required to have an extremely small impedance of only milliohms.
The DC-DC converter can provide this extremely small impedance in the low frequency range. Regardless of how the load changes, by adjusting the output voltage of the converter through feedback loop control, an extremely small output impedance can be obtained. The relationship between output impedance and loop gain is: Zclosed = Zopen/(1+GH), where Zopen is the open-loop output impedance, Zclosed is the closed-loop output impedance, and GH is the loop gain. In the low-frequency range where the loop gain is high, the closed-loop output impedance will be very small.
To measure the output impedance of a DC-DC converter, we can use a low-frequency network analyzer to directly measure the closed-loop output impedance Zclosed with a probe at the output terminals of the DC-DC converter. This section discusses how to use the E5061B-3L5 LF-RF network analyzer with software 005 impedance analysis to measure the output impedance of a DC-DC converter.
Figure 1. DC-DC converter output impedance in PDN
Current-voltage detection method
This method was previously used to measure the output impedance of DC-DC converters and switch-mode power supplies. Figure 2 is a simplified schematic diagram of this method. By floating the ground of the network analyzer excitation signal source with a transformer, the high-impedance receiver port of the network analyzer can be used to measure the AC voltage and current on the grounded device under test. Port T measures the AC voltage Vdut across the device under test, and port R measures the AC voltage across the 1 Ω resistor. The AC current flowing through the device under test is Idut. The ratio of the two voltage measurements is calculated, and the T/R result is directly the impedance of the device under test, because T/R=VT/VR=Vdut/(1 x Idut). In this figure, the device under test refers to the DC-DC converter and the load connected to it.
Similar to the case of measuring loop gain, we usually use an electronic load or a high-power resistor as the load of the device under test. In fact, the network analyzer measures the impedance of the DC-DC converter and the impedance of the load resistor in parallel. Since the output impedance of the DC-DC converter is much smaller than the load impedance, the measurement result mainly reflects the impedance of the device under test. The DC blocking capacitor can prevent the DC output signal of the device under test from entering the transformer and the 1 Ω resistor. Its impedance | Z |=| 1/(j * 2 * pi * f * C)| should be small enough to obtain a good signal-to-noise ratio in the low-frequency measurement range.
This measurement method is very suitable for testing DC-DC converters with relatively high output voltages, because the instrument's excitation signal source is well isolated from the DC output voltage of the device under test, and both measurement receivers are reliably connected through high impedance. In addition, since the excitation signal source is floated by the transformer, there will be no errors in the measurement results caused by the ground loop of the measurement cable. However, the measurement error caused by the residual impedance of the wiring near the 1 Ω resistor is difficult to completely eliminate, so this method is not suitable for accurately measuring very small impedances in the milliohm range.
Figure 2. Current-voltage detection method
Configuration example of current-voltage detection method
Figure 3 shows an example of a configuration using the E5061B-3L5 gain-phase test port using the current-voltage sensing method. For transformer T1, you can use the same pulse converter used in the loop gain measurement. However, we do not recommend using an off-the-shelf isolation transformer designed for use in 50 Ω or 75 Ω systems, such as North Hills' 0017C type transformer, for this measurement because it is easy to produce some unwanted residual response when the transformer is dead in this configuration.
Figure 3. Configuration example of current-voltage detection method
Figure 3. Example of configuration for current-voltage sensing method Using a DC blocking capacitor prevents DC current from flowing into the transformer windings and the 1 Ω resistor. Using a large electrolytic capacitor is sufficient to inject the excitation signal into the device under test at low-frequency measurement bands.
The 1 Ω resistor used to sense the current should be as accurate as possible. By measuring the impedance of this resistor itself, you can use simple calculations to compensate the measurement results. For example, if the impedance of the resistor is 0.98 Ω, you can multiply the measured impedance Zmeas by 0.98 to get the impedance Zdut of the device under test, because Zmeas = VT/VR = Vdut/(Idut x 0.98) = Zdut/0.98. If a lead resistor is used, the lead length should be as short as possible and soldered directly to the output terminal of the device under test. This can minimize the measurement error caused by the residual lead impedance and contact impedance between the resistor and the device under test. If you want to measure a small AC voltage at the 100V with a good signal-to-noise ratio, you should set the attenuation value in the T port to 0 dB and set the output power of the excitation signal source to the maximum level, that is, 10 dBm. To calibrate the measurement system, you can connect the test cable at the 100V and the measurement cable at the R port to the same point for a through response calibration. When performing a THRU response calibration, the power of the stimulus source should be reduced to below -5 dBm to prevent overloading the T-port of the measurement receiver.
Parallel-through measurement method
The method that can accurately measure the tiny impedance of the milliohm level is the shunt-through method. The shunt-through method has very high sensitivity in the impedance range below 50 Ω to very small impedances, and is a common method for measuring PDN impedance. Figure 4 is a simplified schematic diagram of the measurement method. The device under test is connected in parallel between the excitation signal line and the ground line, and then the transmission coefficient S21 is measured. The impedance of the device under test is then derived from S21, which represents the large attenuation caused by the very small parallel impedance. The relationship between the impedance Zdut of the device under test and S21 is: Zdut = 25 x S21/(1-S21).
Measurement Errors Caused by Test Cable Ground Loops
In the low frequency measurement range, it is difficult to measure milliohm shunt impedance using a low frequency network analyzer with a traditionally grounded receiver because the test cable ground loop between the excitation signal source and the receiver will cause measurement errors.
Now assume that the impedance Zdut of the device under test is close to 0 Ω. In the block diagram of Figure 5, the voltage Vo is almost 0, and the voltage VT measured by the instrument measurement receiver should also be close to 0. However, as shown by the dotted line, since the excitation source current will flow into the metal outer shielding layer of the measurement cable on the VT receiver side, the voltage drop generated by this current on the cable shielding resistor RC2 is VC2, so the actual measured voltage VT should be equal to VC2, which is higher than the voltage Vo we actually want to measure, which is an incorrect measurement result. Therefore, even when the impedance Zdut of the device under test is 0, the dynamic range of the measurement will decrease, and the actual measured impedance will not be smaller than RC2. Depending on the quality of the cable shielding layer and the connector swaging, the thickness of the cable shielding, the length of the cable, etc., the range is usually between 10 milliohms and tens of milliohms.
Typically, problems with measuring cable ground loop errors occur in the low-frequency measurement range below 100 kHz, which is an important frequency range for measuring the impedance of DC-DC converters and some large-capacity bypass capacitors. The same problem does not occur in the higher frequency range because the current flowing into the measurement cable shield on the VT receiver side is suppressed by the shield's own reactance (X=2 * pi * f * L), which increases with higher measurement frequencies.
Figure 4. Shunt-through measurement method
Figure 5. Measurement error caused by test cable ground loops.
Traditional solutions to reduce measurement errors - 1
There are several techniques that can minimize measurement errors using external devices. The most traditional method is to wrap the coaxial measurement cable on the excitation source side or the measurement receiver side, or both sides, around a magnetic ring with high inductance. Figures 6 and 7 show the equivalent circuit of this method. The impedance of the magnetic ring only suppresses the AC current flowing through the center conductor of the measurement cable or the outer shield of the measurement cable, but does not suppress the AC current flowing through the center conductor of the measurement cable and then returning through the outer shield of the measurement cable. When the magnetic ring is used on the cable on the VT receiver side, as shown in Figure 6, because the current flowing through the measurement cable shield resistance RC2 is suppressed by the self-inductance | Z |=2 * pi * f * L2, more current will return to the excitation source side through the shield path of the measurement cable on the excitation source side. Similarly, when a magnetic ring is applied to the cable on the excitation source side, as shown in Figure 7, more current will also return to the shield path of the measurement cable on the excitation source side. This is because more current returns to the path of the excitation source shield rather than the shield path of the cable on the VT receiver side, making the total impedance composed of RC1, RC2 and L1' (inductance caused by the magnetic field generated by the forward and reverse currents) smaller.
Previous article:Basics of Dielectric Material Measurement
Next article:Five things to consider before buying a digital multimeter
Recommended ReadingLatest update time:2024-11-16 17:56
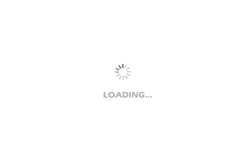
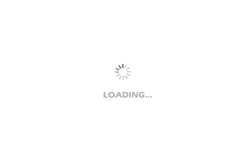
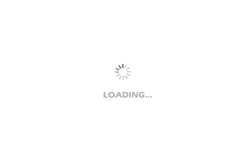
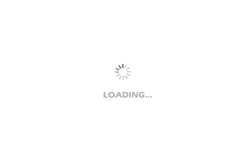
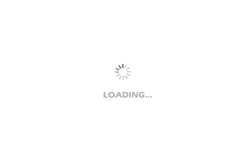
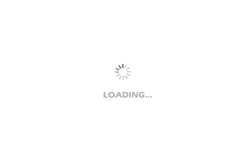
- Popular Resources
- Popular amplifiers
-
New Energy Vehicle Detection and Diagnosis Experiment (Edited by Mao Caiyun, Zhou Xien, and Long Jiwen)
-
Virtualization Technology Practice Guide - High-efficiency and low-cost solutions for small and medium-sized enterprises (Wang Chunhai)
-
Design of an adaptive constant on-time buck DC-DC converter with high efficiency and low power consumption
-
Research on design technology of high-efficiency step-up DC-DC converter with wide load range
- Keysight Technologies Helps Samsung Electronics Successfully Validate FiRa® 2.0 Safe Distance Measurement Test Case
- From probes to power supplies, Tektronix is leading the way in comprehensive innovation in power electronics testing
- Seizing the Opportunities in the Chinese Application Market: NI's Challenges and Answers
- Tektronix Launches Breakthrough Power Measurement Tools to Accelerate Innovation as Global Electrification Accelerates
- Not all oscilloscopes are created equal: Why ADCs and low noise floor matter
- Enable TekHSI high-speed interface function to accelerate the remote transmission of waveform data
- How to measure the quality of soft start thyristor
- How to use a multimeter to judge whether a soft starter is good or bad
- What are the advantages and disadvantages of non-contact temperature sensors?
- Innolux's intelligent steer-by-wire solution makes cars smarter and safer
- 8051 MCU - Parity Check
- How to efficiently balance the sensitivity of tactile sensing interfaces
- What should I do if the servo motor shakes? What causes the servo motor to shake quickly?
- 【Brushless Motor】Analysis of three-phase BLDC motor and sharing of two popular development boards
- Midea Industrial Technology's subsidiaries Clou Electronics and Hekang New Energy jointly appeared at the Munich Battery Energy Storage Exhibition and Solar Energy Exhibition
- Guoxin Sichen | Application of ferroelectric memory PB85RS2MC in power battery management, with a capacity of 2M
- Analysis of common faults of frequency converter
- In a head-on competition with Qualcomm, what kind of cockpit products has Intel come up with?
- Dalian Rongke's all-vanadium liquid flow battery energy storage equipment industrialization project has entered the sprint stage before production
- Allegro MicroSystems Introduces Advanced Magnetic and Inductive Position Sensing Solutions at Electronica 2024
- Car key in the left hand, liveness detection radar in the right hand, UWB is imperative for cars!
- After a decade of rapid development, domestic CIS has entered the market
- Aegis Dagger Battery + Thor EM-i Super Hybrid, Geely New Energy has thrown out two "king bombs"
- A brief discussion on functional safety - fault, error, and failure
- In the smart car 2.0 cycle, these core industry chains are facing major opportunities!
- The United States and Japan are developing new batteries. CATL faces challenges? How should China's new energy battery industry respond?
- Murata launches high-precision 6-axis inertial sensor for automobiles
- Ford patents pre-charge alarm to help save costs and respond to emergencies
- New real-time microcontroller system from Texas Instruments enables smarter processing in automotive and industrial applications
- How NFC and RFID technologies develop together
- Ultra-low power consumption and high precision ultrasonic flow meter based on MSP430
- Ultrasonic Flow Transmitter Reference Design
- What is the standard for package naming? Can you share it? Thank you!
- 2. Evaluation starts with lighting
- Slope compensation issues
- Controlled by "Playpad" + Siri + Shortcut Command + ESP8266
- Share the OS transplantation and application of Lingdong Micro MCU based on MM32 MCU-AMetal SPI operation
- Do you still buy electronic components offline? It’s Double 11, what goodies are in your shopping cart?
- 【TI Recommended Course】#Amplifier Protection Series#