Tektronix's 511 analog real-time oscilloscope marked the arrival of the era of commercial oscilloscopes. There were some "oscilloscope" products before 511, but because they did not have a trigger system and a calibrated time base and vertical scale, they could not provide a stable display waveform, nor could they perform quantitative tests, so they were just a qualitative observation tool. 511 was the first to add edge triggering to the "oscilloscope" test equipment to display a stable waveform, and use a calibrated time base and vertical amplifier to provide quantitative testing capabilities, greatly increasing its applicability. In this way, the commercial oscilloscope was born.
The basic structure of analog real-time oscilloscopes has not changed much since its development. The following figure is a basic structural block diagram:
The analog real-time oscilloscope has a simple structure and does not have the process of signal digitization and processing. All signal conditioning, amplification and display of ART are completed by analog devices, so from the signal entering the amplifier (or probe) to the final display on the CRT, it is almost real-time (the delay time can be almost ignored).
However, analog oscilloscopes also have dead time, and signals that appear during the dead time cannot be displayed on the screen. This dead time comes from the "trigger hold off" of the trigger system and the time to wait for the trigger. Therefore, analog oscilloscopes cannot capture signals 100%. Different models of analog real-time oscilloscopes have a maximum waveform capture probability ranging from about 30% to 70%, and the fastest scanning speed can reach 500,000 times/second. This is a very good indicator.
Let's look at the display method of analog oscilloscopes - CRT cathode ray tubes. The electron beam is deflected by the deflection plate, and then bombards the fluorescent material on the display screen to emit light to form a waveform track. When the electron beam stops bombarding, the bright spot will not disappear immediately but will retain a period of afterglow time. Afterglow time 10μs-1ms is short afterglow, 1ms-0.1s is medium afterglow, 0.1s-1s is long afterglow, and more than 1s is extremely long afterglow. General oscilloscopes are equipped with medium afterglow oscilloscope tubes, high-frequency oscilloscopes use short afterglow, and low-frequency oscilloscopes use long afterglow. Under the effect of the afterglow effect, the brightness of each point on the waveform track is proportional to the number of bombardments (frequency). Therefore, the waveform displayed by the analog real-time oscilloscope not only has information on time and amplitude, but also can represent the probability of signal occurrence in terms of brightness level, which is very conducive to observation.
But on the other hand, this characteristic of fluorescent material also brings a problem: the brightness of the trace with too few bombardments will be very low, or even impossible to observe. Therefore, analog oscilloscopes are more suitable for repetitive signals (such as continuous sine waves) or signals with repetitive characteristics (such as analog video signals). However, the observation ability of single-shot signals (such as single pulses or occasional faults) is very limited.
In summary, analog real-time oscilloscopes have the following main advantages: strong real-time performance, high waveform capture probability, and intuitive three-dimensional (time, amplitude, and signal occurrence probability) display. The main disadvantages are: inability to store data, limited analysis capabilities, insufficient ability to capture low-probability events, simple triggering, insufficient pre-trigger delay, and difficulty in bandwidth improvement (from front-end amplifier to CRT must be improved at the same time). With the rise of digitalization and the increasing demand for single-shot signal measurement, these shortcomings of analog oscilloscopes have gradually made it unable to meet test needs. Therefore, since the 1980s, mainstream oscilloscope manufacturers have gradually turned to the research and development and production of digital oscilloscopes.
Tektronix's 511 analog real-time oscilloscope marked the arrival of the era of commercial oscilloscopes. There were some "oscilloscope" products before 511, but because they did not have a trigger system and a calibrated time base and vertical scale, they could not provide a stable display waveform, nor could they perform quantitative tests, so they were just a qualitative observation tool. 511 was the first to add edge triggering to the "oscilloscope" test equipment to display a stable waveform, and use a calibrated time base and vertical amplifier to provide quantitative testing capabilities, greatly increasing its applicability. In this way, the commercial oscilloscope was born.
The basic structure of analog real-time oscilloscopes has not changed much since its development. The following figure is a basic structural block diagram:
The analog real-time oscilloscope has a simple structure and does not have the process of signal digitization and processing. All signal conditioning, amplification and display of ART are completed by analog devices, so from the signal entering the amplifier (or probe) to the final display on the CRT, it is almost real-time (the delay time can be almost ignored).
However, analog oscilloscopes also have dead time, and signals that appear during the dead time cannot be displayed on the screen. This dead time comes from the "trigger hold off" of the trigger system and the time to wait for the trigger. Therefore, analog oscilloscopes cannot capture signals 100%. Different models of analog real-time oscilloscopes have a maximum waveform capture probability ranging from about 30% to 70%, and the fastest scanning speed can reach 500,000 times/second. This is a very good indicator.
Let's look at the display method of analog oscilloscopes - CRT cathode ray tubes. The electron beam is deflected by the deflection plate, and then bombards the fluorescent material on the display screen to emit light to form a waveform track. When the electron beam stops bombarding, the bright spot will not disappear immediately but will retain a period of afterglow time. Afterglow time 10μs-1ms is short afterglow, 1ms-0.1s is medium afterglow, 0.1s-1s is long afterglow, and more than 1s is extremely long afterglow. General oscilloscopes are equipped with medium afterglow oscilloscope tubes, high-frequency oscilloscopes use short afterglow, and low-frequency oscilloscopes use long afterglow. Under the effect of the afterglow effect, the brightness of each point on the waveform track is proportional to the number of bombardments (frequency). Therefore, the waveform displayed by the analog real-time oscilloscope not only has information on time and amplitude, but also can represent the probability of signal occurrence in terms of brightness level, which is very conducive to observation.
But on the other hand, this characteristic of fluorescent material also brings a problem: the brightness of the trace with too few bombardments will be very low, or even impossible to observe. Therefore, analog oscilloscopes are more suitable for repetitive signals (such as continuous sine waves) or signals with repetitive characteristics (such as analog video signals). However, the observation ability of single-shot signals (such as single pulses or occasional faults) is very limited.
In summary, analog real-time oscilloscopes have the following main advantages: strong real-time performance, high waveform capture probability, and intuitive three-dimensional (time, amplitude, and signal occurrence probability) display. The main disadvantages are: inability to store data, limited analysis capabilities, insufficient ability to capture low-probability events, simple triggering, insufficient pre-trigger delay, and difficulty in bandwidth improvement (from front-end amplifier to CRT must be improved at the same time). With the rise of digitalization and the increasing demand for single-shot signal measurement, these shortcomings of analog oscilloscopes have gradually made it unable to meet test needs. Therefore, since the 1980s, mainstream oscilloscope manufacturers have gradually turned to the research and development and production of digital oscilloscopes.
The first generation of digital oscilloscopes are now called digital storage oscilloscopes (DSOs), which use a serial working structure. The principle block diagram is as follows:
Digital storage oscilloscopes use ADC sampling, so the measured analog waveform can be stored in data format. Of course, digitized data can also be easily used for automatic measurement, spectrum analysis, mathematical calculations or other advanced analysis. Therefore, digital oscilloscopes are particularly suitable for the acquisition and analysis of single-shot signals, which is a great breakthrough.
On the other hand, digital storage oscilloscopes are fully digital after ADC, so the bandwidth improvement is only limited by the variable gain preamplifier bandwidth and the ADC rate. With the advancement of technology, Tektronix TDS6154C is now the digital storage oscilloscope with the highest true analog bandwidth in the industry, reaching 12.5GHz (3dB). Since broadband amplifiers are the core part of the ultra-high bandwidth oscilloscope system design, the current mainstream design adopts a hardware amplifier design method that is independent of each channel, which ensures that the performance of each channel is not limited. When the design bandwidth of each channel amplifier is insufficient, some oscilloscopes use DBI technology to use the 6GHZ low-bandwidth amplifier of each channel of the oscilloscope to "splice" together in different frequency bands, and achieve a bandwidth of more than 6GHZ on a certain channel. For example, the 6GHZ frequency bands of three channels can be "spliced" to achieve a bandwidth of 18GHZ. The advantages and disadvantages of DBI technology can be clearly seen from its implementation method. The most obvious advantage is to use the low bandwidth of multiple channels to merge into a single channel with a high bandwidth of more than 10GHZ. The amplifiers and ADCs with the highest cost in oscilloscope design are designed at low speed, which is very helpful to control costs. Since DBI technology essentially distributes the signal frequency to different channels, samples it through a relatively low-speed ADC, and finally "joins" these frequencies containing different components digitally through DSP technology, it will lead to the following limitations.
1. Channel number limitation: The bandwidth is different when using different channels. When 3 or 4 channels are used, only 6 GHZ bandwidth is provided, and the ADC sampling rate is also limited.
2. Spectrum "splicing" error: From the amplitude-frequency characteristic diagram, it can be seen that each frequency "splicing" point has obvious nonlinearity. When the spectrum component of the measured signal is in this area, the waveform displayed in the oscilloscope's time domain will be distorted.
3. Low waveform capture rate: Since DBI technology requires software to process and "splice" waveforms in the digital frequency domain, the waveform processing and display speed is very low when the data volume is large.
4. Functional limitations: When DBI is turned on, although the single-channel bandwidth and ADC are improved, the bandwidth of the trigger system cannot be improved through DBI technology, and the maximum is only 800MHZ. In addition, the oscilloscope's external reference input, fine adjustment of vertical sensitivity and other functions will be limited due to the opening of DBI.
Digital storage oscilloscopes have also made great progress in the trigger system. As can be seen from the block diagram, the trigger system of a digital oscilloscope is a completely independent circuit based on analog circuits. A high-performance trigger system is like a camera shutter, which can help testers accurately locate signal behavior. In view of the characteristics of various special signals, digital storage oscilloscopes can be equipped with a variety of advanced trigger modes such as burr trigger, runt pulse trigger, transition time, communication trigger, serial trigger, window trigger, state trigger, code pattern trigger and bus trigger. Tektronix's Pinpoint? trigger system is the most advanced trigger system in the industry. It uses complete SiGe technology in edge triggering and advanced triggering, so the trigger sensitivity can reach a very high level. For example, the TDS6124C instrument can achieve 3div@9GHz sensitivity for both edge triggering and advanced triggering. This dual trigger system is supplemented by trigger delay setting and trigger reset, and the trigger mode can be set almost without restrictions.
With these characteristics, the bandwidth performance of digital storage oscilloscopes can be much higher than that of analog real-time oscilloscopes; with the cooperation of triggering and sampling, the digital storage oscilloscope has a huge improvement in the capture capability of single-shot signals (low repetition probability signals); the signal testing and analysis capabilities are also different from the past... However, after enhancing the capture and analysis capabilities of single-shot signals, it also introduces unavoidable weaknesses, which are mainly reflected in the waveform capture rate and monotonous display capabilities. Let us explain these weaknesses below:
The structure of the digital storage oscilloscope has determined that it must work in a serial mode - the signal is conditioned and enters the ADC for sampling; the ADC sampling data is sent to the acquisition memory under the control of the trigger system; after the acquisition memory is full, the waveform data is sent to the computer system; the microprocessor processes, calculates and analyzes these data according to user needs; finally, the waveform and analysis results are displayed on the display (the workflow in the rolling mode is slightly different, and it is not described in detail here). In this process: from signal conditioning, trigger monitoring to ADC sampling, it is almost real-time and will not affect work efficiency; and the data is transmitted from the acquisition memory to the computer system, the microprocessor processing, the calculation process, and the final display will affect its real-time performance due to the different architecture of the oscilloscope. The most critical part is the processing process of the microprocessor. We all know that the sampling rate of popular oscilloscopes is tens of gigabits per second (GS/s), and no general-purpose microprocessor can process such a data stream in real time, so the processing method of the oscilloscope microprocessor can only be "grab a section, process slowly, control the display", and then repeat. In this way, during the time of "slow processing", the oscilloscope will not be able to monitor the waveform, which is what we call "dead time". Events that occur during the dead time will not be displayed on the screen. In order to measure the proportion of the dead time of the digital storage oscilloscope to the total observation working time, we introduce the concept of "waveform capture rate", which is the number of waveforms that the oscilloscope can continuously capture and display per second. The "waveform" here refers to all the information collected in one trigger. Experiments have shown that the industry's highest waveform capture rate of high-performance (bandwidth above 1GHz) digital storage oscilloscopes has a waveform capture rate of about 8,000 times, and the total time it captures the waveform accounts for about 1-2% of the total observation time. In other words, more than 98% of the details of all signals are lost due to the dead time of the oscilloscope.
Every engineer believes that the instrument provides the correct information, but few engineers consider that the oscilloscope they are using can only provide so few waveform details - for example, if there is a fault in the signal you observe that occurs once per second on average, the probability of a digital storage oscilloscope finding this fault within 1 second is less than 2%, and the probability of finding it within 15 seconds is only about 26%. In fact, due to the tight development time, the average engineer will not observe a signal for more than 10 seconds - as a result, you have less than a quarter of the chance of capturing this fault and effectively debugging it.
Almost all oscilloscope manufacturers are aware of the low waveform capture rate of digital storage oscilloscopes and have developed many methods to increase the speed of oscilloscopes. However, whether using two pairs of 1.25Gbps Gigabit Ethernet links when transferring data from the acquisition memory to the microprocessor, or using acceleration technologies such as local display and point-sampling display on the display, they have failed to solve the throughput problem from the most fundamental problem - in the serial architecture, the microprocessor is the bottleneck of speed. Only by completely changing the serial structure and freeing up the microprocessor can the problem be solved.
In this regard, Tektronix has been at the forefront of the industry, starting with the transformation of serial architecture. From InstaVu? in the mid-1990s to real-time DPO in early 2006, the third generation of oscilloscopes based on parallel architecture: digital phosphor oscilloscopes, have gradually matured from their emergence. The following figure is the structure of a DPO digital phosphor oscilloscope:
From the structure, we can see that the parallel processing core of the DPO digital phosphor oscilloscope is the DPX parallel imaging processing chip. DPX completes the storage, rasterization and statistical processing of the collected data to generate a three-dimensional database. And it can directly import the rasterized waveform image information into the video memory. In this architecture, the microprocessor only performs display control and other tasks, and no longer acts as a bottleneck in the data processing process.
The parallel structure of DPO digital phosphor oscilloscope fundamentally solves the defects of low waveform capture rate and serious waveform loss of DSO digital storage oscilloscope. The waveform capture rate of DPO7000 and DPO70000 series real-time digital phosphor oscilloscopes can reach 250,000 wfm/s, and the DPO71000 and DPO72000 series ultra-high performance digital phosphor oscilloscopes can exceed 300,000 wfm/s. The proportion of captured waveforms to the total signal can reach up to 60% (provided continuously); and the new generation of DPX acquisition does not have the maximum 1.25G real-time sampling rate limit of the previous generation of "quasi-real-time phosphor oscilloscopes", but can work at any sampling rate, further enhancing the signal capture capability, and is now the best tool for discovering problems in the industry. The following figure shows the situation 15 seconds after the same level oscilloscopes from three different manufacturers simultaneously observe a clock with occasional faults (occurring about once a second). As you can see, while the first two oscilloscopes barely detected any issues, the Tektronix digital phosphor oscilloscope (right) captured multiple failures that occurred here. The difference is clear at a glance.
The three-dimensional database generated by DPX also has great advantages in display. This database recorded by the hardware buffer can save the amplitude, time and amplitude changing over time (i.e. the frequency of signal occurrence at each point) of the waveform, which far exceeds the database generated by software of other manufacturers in terms of accumulation speed and buffer depth (26 bits per point). The display waveform generated by this three-dimensional database can simultaneously inform the user of the amplitude, time and probability of signal occurrence in the form of color temperature, spectrum, brightness level, etc., which is very similar to the effect of an analog oscilloscope.
Digital phosphor oscilloscopes have waveform capture rates and display methods comparable to those of analog oscilloscopes. Their ability to capture and observe repetitive signals and signals with repetitive characteristics (such as digital signals and serial communication signals) far exceeds that of traditional digital storage oscilloscopes, and can significantly improve debugging and verification efficiency. At the same time, digital phosphor oscilloscopes also have all the analytical capabilities of digital storage oscilloscopes for single-shot capture signals. Moreover, due to the advantages of their architecture, digital phosphor oscilloscopes are fully ahead of digital storage oscilloscopes in terms of test items, test speed, and test accuracy.
Previous article:Debugging with a real-time digital phosphor oscilloscope
Next article:RF Vector Signal Analyzers: Say “No” to Poor Performance in Microwave Measurements
Recommended ReadingLatest update time:2024-11-16 22:47
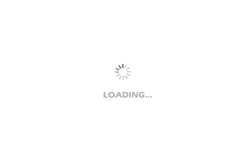
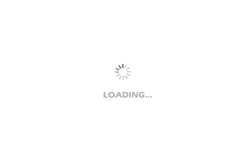
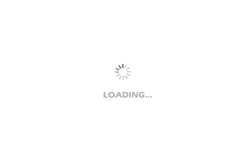
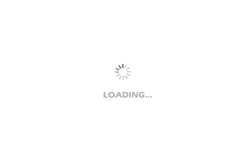
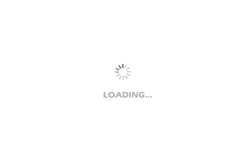
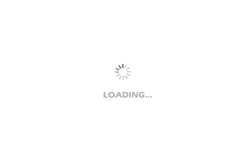
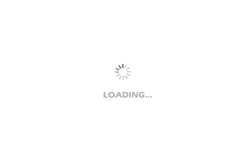
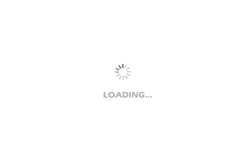
- Keysight Technologies Helps Samsung Electronics Successfully Validate FiRa® 2.0 Safe Distance Measurement Test Case
- From probes to power supplies, Tektronix is leading the way in comprehensive innovation in power electronics testing
- Seizing the Opportunities in the Chinese Application Market: NI's Challenges and Answers
- Tektronix Launches Breakthrough Power Measurement Tools to Accelerate Innovation as Global Electrification Accelerates
- Not all oscilloscopes are created equal: Why ADCs and low noise floor matter
- Enable TekHSI high-speed interface function to accelerate the remote transmission of waveform data
- How to measure the quality of soft start thyristor
- How to use a multimeter to judge whether a soft starter is good or bad
- What are the advantages and disadvantages of non-contact temperature sensors?
- Innolux's intelligent steer-by-wire solution makes cars smarter and safer
- 8051 MCU - Parity Check
- How to efficiently balance the sensitivity of tactile sensing interfaces
- What should I do if the servo motor shakes? What causes the servo motor to shake quickly?
- 【Brushless Motor】Analysis of three-phase BLDC motor and sharing of two popular development boards
- Midea Industrial Technology's subsidiaries Clou Electronics and Hekang New Energy jointly appeared at the Munich Battery Energy Storage Exhibition and Solar Energy Exhibition
- Guoxin Sichen | Application of ferroelectric memory PB85RS2MC in power battery management, with a capacity of 2M
- Analysis of common faults of frequency converter
- In a head-on competition with Qualcomm, what kind of cockpit products has Intel come up with?
- Dalian Rongke's all-vanadium liquid flow battery energy storage equipment industrialization project has entered the sprint stage before production
- Allegro MicroSystems Introduces Advanced Magnetic and Inductive Position Sensing Solutions at Electronica 2024
- Car key in the left hand, liveness detection radar in the right hand, UWB is imperative for cars!
- After a decade of rapid development, domestic CIS has entered the market
- Aegis Dagger Battery + Thor EM-i Super Hybrid, Geely New Energy has thrown out two "king bombs"
- A brief discussion on functional safety - fault, error, and failure
- In the smart car 2.0 cycle, these core industry chains are facing major opportunities!
- The United States and Japan are developing new batteries. CATL faces challenges? How should China's new energy battery industry respond?
- Murata launches high-precision 6-axis inertial sensor for automobiles
- Ford patents pre-charge alarm to help save costs and respond to emergencies
- New real-time microcontroller system from Texas Instruments enables smarter processing in automotive and industrial applications
- C6678 Multi-core DSP Software Development Difficulties and Solutions
- 150V Non-Synchronous Buck Solution with Voltage Controller
- When will the gifts redeemed from TI Mall be shipped?
- WPI Group sincerely invites you to gather in Chongqing to attend the "Ansemester and NXP - Automotive Electronics Innovation Products and Technology Seminar"
- RVB2601 Evaluation Board Trial 5: Remote Audio Acquisition System
- God, please help me find where I am wrong.
- Comparison of three basic triode amplifier circuits
- SinlinxA33 lvds screen configuration
- PCB size measurement, VX9000 optical scanning imaging measuring machine VS imager measurement
- DC Gain of Nanopower Op Amps