1 Overall design principle
The design of the suspended shaft vibration measurement sensor includes the design of the capacitance sensor, the selection of the oscillation circuit, the sampling of the photoelectric encoder, the realization of the difference frequency counting, and the intelligent control of the single-chip microcomputer. The basic principle is: first, the conductive medium capacitance sensor is used to convert the change of the vibration displacement into the change of the capacitance. Since the capacitance sensor is a capacitance element in the oscillation circuit, the change of the capacitance will cause the change of the oscillator output frequency. At the same time, another capacitance sensor is selected as a temperature compensation sensor, and a frequency signal is also obtained through the oscillator. The sampling of the vibration signal is realized by the equal-angle sampling of the photoelectric encoder. With the cooperation of the photoelectric encoder, the gate circuit and the single-chip microcomputer hardware and software, the two high-frequency signals are input into the difference frequency counter to obtain the count value within a fixed time interval, which is sent to the C8051F020 single-chip microcomputer for storage and processing, and the count difference is obtained and converted into the size of the vibration displacement. The implementation block diagram is shown in Figure 1.
2. Development of sensor
2.1 Measurement Circuit
The vibration displacement measurement circuit of the suspended shaft consists of two parts: on the one hand, a conductive medium capacitance sensor is used to convert the change of the vibration displacement of the suspended shaft into the change of capacitance; on the other hand, a reflective photoelectric encoder is used to achieve equal-angle sampling of the rotation of the suspended shaft to ensure the sampling accuracy.
2.1.1 Design of conductive medium capacitance sensor
The purpose of changing the capacitance C can be achieved by changing the area S of the capacitor plate and the distance d between the plates. A variable-pole-distance capacitance sensor is used to measure the vibration displacement of the suspended shaft. In order to enable the sensor to convert the change of vibration displacement into the corresponding change of capacitance, so that the two are in a single-valued function relationship, and to ensure that the actual motion state of the suspended shaft does not change when it rotates and is disturbed by the outside world, the conductive medium sensor uses the suspended shaft itself as the moving plate of the capacitor, and copper, which has a small effect on the material expansion coefficient due to temperature, is used as the static plate. In addition, the sensitivity, linearity and parasitic capacitance of the capacitance sensor are also fully considered during the design. Two capacitance sensors are used during the design: one for measurement and the other for temperature compensation. Moreover, each capacitance sensor is composed of two capacitors connected in series, which not only solves the connection problem of the capacitance sensor wire, but also reduces the influence of parasitic capacitance. Assume that the capacitance of the capacitance sensor used for measurement is C, and the capacitance of the capacitance sensor used for temperature compensation is C0. The specific design parameters are as follows:
The initial installation plate spacing of the two capacitors is x0=25μm; the thickness of the insulating material is d1=10μm; the coverage area of each plate is A=0.5 cm2; the measured vibration range is -25~25μm (that is, the plate spacing z range is 0~50μm); ε0=8.85×10-12 F/m, εr=2.3ε0, and the structural schematic is shown in Figure 2.
First, the relationship between the plate spacing and the vibration displacement △x is:
x-x0=△x (1)
Since each capacitive sensor is composed of two capacitors in series, considering the thickness of the insulating film on the plate surface, the capacitance C of the measuring capacitance sensor and the capacitance C0 of the temperature compensation capacitance sensor are obtained respectively.
2.1.2 Using photoelectric encoder to achieve equal rotation angle sampling
The photoelectric pulse encoder is a rotary pulse generator that converts mechanical angle into electrical pulses and can be used as a position detection and speed detection device. In the design, a reflective photoelectric encoder is used to achieve high-precision equal-angle sampling. Its output is a pulse signal, and the number of pulses is related to the rotational displacement. The rotation speed of the suspension shaft is 50 rad/s. The photoelectric encoder uses equal-angle (2°) interval sampling, so each sampling period is about t=111μs, that is, the photoelectric encoder outputs a pulse signal with a frequency of 9kHz. The vibration signal conversion process of the suspension shaft is continuous signal → discrete signal. According to the signal sampling theory: if the continuous signal f(t) is of limited bandwidth and the highest frequency of its spectrum is fm, then the signal f(t) can be uniquely represented by equally spaced sampling values, and the lowest sampling frequency fs=2fm, that is, fs≥2fm. Since the sampling frequency of the photoelectric encoder is fs=9kHz, the highest frequency of the suspension shaft vibration that the sensor can measure is fm4.5 kHz.
2.2 Signal Processing Circuit
The oscillator, difference frequency counter, control circuit and single-chip microcomputer together constitute the signal processing system. Using the functional relationship between the vibration displacement of the suspension shaft and the frequency signal, the sensor measurement results are converted into frequency signals through a specially designed oscillation circuit, and the difference frequency counter is used for control counting, and then processed by the single-chip microcomputer to finally obtain the magnitude of the vibration displacement of the suspension shaft.
2.2.1 Selection of oscillation circuit
The capacitance change output by the capacitance sensor is converted into a frequency value that is easy to measure through an oscillator. Moreover, when the capacitance is required to be in the tens of pF, the oscillator can output an oscillation frequency of up to 30 MHz. An asymmetric oscillation circuit can be used, and its structure is shown in Figure 3.
Among them, inverters G1 and G2 use 74HC04 chip (six inverters). RS is the protection resistor. After debugging the hardware circuit, RS=20.3 kΩ is obtained. Rf is the feedback resistor, which is also the delay link of the entire oscillation circuit. Its resistance directly affects the oscillation frequency. Therefore, the feedback resistor parameter Rf should be reasonably determined. Since the relationship between the plate spacing and the oscillation frequency of the capacitance sensor is: the larger the plate spacing, the higher the oscillation frequency of the oscillator, and the larger the count value of the counter. In order to ensure the accuracy of the measurement results, when the plate spacing is the largest, the count value of the counter should reach about 90% of the full scale. This design uses a serial input/12-bit parallel output difference frequency counter. Its counting range is 0~212, and the counting time △T should be slightly less than the sampling period of 100μs. The parameter determination process of Rf is as follows:
2.2.2 Implementation of difference frequency counting
The difference frequency counter uses the frequency counting method. The external crystal oscillator obtains the sampling reference signal and the counting reset signal through the gate circuit. After the rising edge of the sampling reference signal, the counter counting is enabled, and the counting module starts to count the input frequency signal. The counting time is exactly △T. The counting reset signal is used to reset the counting module at the beginning of each measurement. The sampled data result is latched at the rising edge of the counting reset signal, and the result of the last measurement is cleared. When counting, on the one hand, the temperature compensation of the capacitive sensor is taken into consideration, and the difference frequency counting method of 2 counters is adopted; on the other hand, the counter itself has a counting error of ±1 due to the asynchrony of the sampling time and the counting pulse, and the difference frequency counter is composed of 2 counters, which further increases the counting error. Therefore, the key is to eliminate the influence of this part of the error. Assume that the capacitance C and C0 of the two capacitive sensors correspond to the frequency signals output by the oscillator as f and f0, that is,
f=f(D)+f(t), (7)
f0=f(t), (8)
Where f(D) is the frequency change caused by vibration displacement; f(t) is the frequency change caused by ambient temperature.
In this way, the difference frequency output of the difference frequency counter can eliminate the influence of ambient temperature on the measurement results.
Δf=f-f0=f(D) (9)
The working principle of the difference frequency counter is to count two frequency signals separately within the counting time △T. The number of pulses measured is n and n0 respectively, so there is
n-n0=(f-f0)△T, (10)
Where n-n0 is the difference between the two counters.
Therefore, as long as a reasonable counting time △T is obtained, the counting difference of the two frequency signals can be obtained. When designing, △T is determined by using the output pulse of the single-chip microcomputer counting photoelectric encoder. Since the sampling time interval of the photoelectric encoder is about 111μs, in addition to counting, the recording and calculation time of the counting value must be reserved in a sampling cycle. Therefore, △T=100μs111μs is selected. From formula (10), it can be seen that the relationship between the counter reading difference and the frequency is
The start and stop signals of the difference frequency counter are controlled by the single chip microcomputer. When the single chip microcomputer start control signal GEP is high, the difference frequency counter starts waiting for counting. The measured frequency signal of the difference frequency counter is input by two AND gates. When each sampling cycle arrives, that is, when the single chip microcomputer receives the photoelectric encoder pulse e1 as a rising edge, the single chip microcomputer detects the output frequency signals osc11 and osc21 of the two oscillators respectively, waits for the first rising edge of the osc11 and osc21 signals, and sends control signals f1 and f2 respectively to start the AND gate, so that the difference frequency counter receives the corresponding frequency signal and counts. At the same time, the corresponding internal counter of the single chip microcomputer starts timing, and the timing time is △T. After the timing time reaches △T, the single chip microcomputer closes the gate of the corresponding input signal of the difference frequency counter, reads the count value of the difference frequency counter, and clears the counter. When both counters have completed counting, the single chip microcomputer starts digital processing of D1 and D2. The difference frequency counter adopts the synchronous locking method between the measured frequency signal and the timing control signal, and counts the two frequency signals separately, thus eliminating the counting error of ±1. The oscillator outputs a high-frequency signal. Therefore, the time interval between the first rising edge of the two frequency signals in one sampling cycle will not be large, that is, the ΔT interval counting of the two frequency signals can be completed in each sampling cycle, and the whole difference frequency counting function is realized in a cycle. The working sequence of the difference frequency counter is shown in Figure 4. In the figure, 1 is the start and stop control signal CEP of the single-chip microcomputer, 2 is the output signal e1 of the encoder, 3 is the frequency signal osc11 of the measuring sensor, 4 is the control signal f1 of AND gate 1, 5 is the frequency signal osc12 counted by counter 1, 6 is the frequency signal osc21 of the temperature compensation sensor, 7 is the control signal f2 of AND gate 2, and 8 is the frequency signal osc22 counted by counter 2.
2.2.3 Data Processing
Since the vibration displacement of the suspension shaft is in a single-valued function relationship with the count value output by the single-chip microcomputer, finally, the software program is written using the C8051F020 single-chip microcomputer to convert the count difference into the vibration displacement to realize the storage and analysis of the vibration displacement. Among them, the vibration displacement is stored in 2 bytes respectively, and the positive and negative of the vibration displacement is determined by the carry bit of the subtractor. It is stored in an independent unit, and 00H is set to indicate that the vibration is positive, and 01H indicates that the vibration displacement is negative.
Combining equations (2), (3), (6) and (11), we can deduce the relationship between the vibration displacement and the difference between the counters as shown in Table 1.
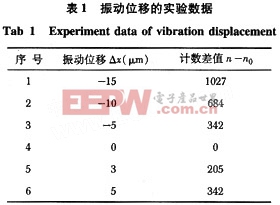
3 Conclusion
The suspended shaft vibration measurement sensor can measure the vibration displacement with a vibration frequency less than 4.5 kHz and a vibration range of -25 to 25 μm, realizing the measurement of its vibration displacement during rotation. At the same time, it avoids interference with its own motion law. Moreover, the hardware adopts angle sampling such as difference frequency measurement and photoelectric encoder control, combined with software data processing, which greatly improves the measurement accuracy, eliminates the influence of power supply fluctuations in the sensor conditioning circuit, ambient temperature changes, and distributed capacitance, and can also shield electromagnetic interference, ensuring the reliability of the measurement results. It can be used in special measurement and control environments.
Previous article:Design and implementation of telemetry demodulation and remote control injection test card based on PCI
Next article:Optical Ring Oscillator Sensors for Light Detection and Measurement
- Popular Resources
- Popular amplifiers
- From probes to power supplies, Tektronix is leading the way in comprehensive innovation in power electronics testing
- Seizing the Opportunities in the Chinese Application Market: NI's Challenges and Answers
- Tektronix Launches Breakthrough Power Measurement Tools to Accelerate Innovation as Global Electrification Accelerates
- Not all oscilloscopes are created equal: Why ADCs and low noise floor matter
- Enable TekHSI high-speed interface function to accelerate the remote transmission of waveform data
- How to measure the quality of soft start thyristor
- How to use a multimeter to judge whether a soft starter is good or bad
- What are the advantages and disadvantages of non-contact temperature sensors?
- In what situations are non-contact temperature sensors widely used?
- LED chemical incompatibility test to see which chemicals LEDs can be used with
- Application of ARM9 hardware coprocessor on WinCE embedded motherboard
- What are the key points for selecting rotor flowmeter?
- LM317 high power charger circuit
- A brief analysis of Embest's application and development of embedded medical devices
- Single-phase RC protection circuit
- stm32 PVD programmable voltage monitor
- Introduction and measurement of edge trigger and level trigger of 51 single chip microcomputer
- Improved design of Linux system software shell protection technology
- What to do if the ABB robot protection device stops
- Learn ARM development(15)
- Analysis of the application of several common contact parts in high-voltage connectors of new energy vehicles
- Wiring harness durability test and contact voltage drop test method
- From probes to power supplies, Tektronix is leading the way in comprehensive innovation in power electronics testing
- From probes to power supplies, Tektronix is leading the way in comprehensive innovation in power electronics testing
- Sn-doped CuO nanostructure-based ethanol gas sensor for real-time drunk driving detection in vehicles
- Design considerations for automotive battery wiring harness
- Do you know all the various motors commonly used in automotive electronics?
- What are the functions of the Internet of Vehicles? What are the uses and benefits of the Internet of Vehicles?
- Power Inverter - A critical safety system for electric vehicles
- Analog components and msp 432
- Useful information | 19 5V to 3.3V conversion methods commonly used by hardware engineers
- Can QT be used on LCDs without a touch screen?
- MSP430F149 Learning Road - Capture/Compare Mode
- [Mil MYC-J1028X development board trial] Build a super powerful OpenWRT soft router
- It's Friday. Let's do a little reasoning
- Why should rectifier filter capacitors use high frequency and low resistance?
- GD32E230C development board download error
- About the steps of converting .brd to .PCB
- In the LLC circuit, when the operating frequency fs is less than the resonant frequency fr, there is a problem with the secondary rectifier diode voltage waveform.