Many applications require the isolation of hazardous voltages to comply with international safety standards. To ensure the safety of equipment and operators, these standards often require isolation components (such as digital isolators or optocouplers) to withstand high voltage surges of more than 10 kV (peak). Therefore, testing isolator surge performance is an essential part of developing safe and reliable devices.
Standards published by the International Electrotechnical Commission (IEC) and VDE (Verband der Elektrotechnik) define the use of isolation technology at the system and component level in medical, industrial, consumer, and automotive systems. To ensure the safety of personnel and equipment during high voltage surges, these standards specify different surge ratings based on the isolation level required for the specific application.
There are three common isolation levels: functional isolation, basic isolation, and reinforced isolation. Functional isolation has only a few safety requirements because it is generally only used in applications where the isolation of the ground reference voltage is required to ensure the circuit can operate properly. As can be seen, safety and surge performance are not the main considerations for functional isolation.
However, safety is the main consideration for basic and reinforced isolation, so surge levels are key to determining the quality of isolation. Basic isolation protects end-equipment users from electric shock, while reinforced isolation is a separate isolation system that provides the same protection as two redundant single or basic isolation systems. Medical and industrial applications typically require reinforced isolation to protect patients and end users from lethal electric shock. The VDE reinforced isolation standard for digital isolators is VDE 0884-10, which specifies a minimum surge voltage (VIOSM) rating of 10 kV, and also specifies working voltage (VIORM) and withstand voltage (VISO). The surge voltage
rating of a digital isolator specifies the ability to withstand a surge after being subjected to continuous short-term high-voltage pulses. Figure 1 shows the timing characteristics of a surge waveform that complies with IEC 61000-4-5.
Figure 1. Surge voltage waveform
For testing, place the device on a test board and short all pins across the isolation barrier (see Figure 2). Connect a high-voltage pulse generator to one end of the isolation barrier through a 1000Ω/1000 pF network. Connect the generator loop to the other end of the isolation barrier. Connect a 100 kΩ, 2.5 W resistor across the isolation barrier to discharge the circuit after each pulse. Monitor the pulses with an oscilloscope with a 1000:1 high-voltage probe. Set the discharge gun to the lowest voltage specified in the test plan and the oscilloscope to single-shot trigger. Apply 10 pulses at this voltage level and monitor each pulse with the oscilloscope. A break in the isolation barrier can be seen by a sudden drop in pulse amplitude (to 50% in less than 50 μs). If the part can withstand 10 pulses, increase the discharge gun voltage and apply another 10 pulses. Continue until the isolation barrier fails or until the maximum test voltage is reached.
Figure 2. Surge test setup
Whether or not to pass this test depends primarily on the thickness of the insulation (also known as the distance to isolation, or DTI) and the quality of the insulation material. Applied electric fields tend to concentrate at defect points within the insulator, so lower defect densities generally result in higher breakdown ratings. Thicker materials are more resistant to breakdown because the field strength is inversely proportional to the distance between the conductors at either end of the insulator.
Optocouplers can generally pass the 10 kV surge test because the insulator is thick (typically 400 μm), which reduces the effect of insulation quality on the breakdown characteristics. Simply put, the insulation is thick, so high-quality materials are not required to pass the 10 kV test. Transformer-based isolators use a high-quality 20 μm to 32 μm polyimide layer stored in a clean room environment. Because the defect levels of this material are much lower than the injection-molded epoxy used in optocouplers, a much thinner insulation layer can still meet the 10 kV requirement. Capacitive isolators also use a high-quality insulation layer, in this case silicon dioxide (SiO2) deposited during the wafer manufacturing process. Silicon dioxide has a high dielectric strength, but generally cannot be deposited very thickly without causing mechanical stress in the film. Thicker SiO2 also reduces capacitance, which in turn results in a decrease in the coupling efficiency of the isolation barrier. For this reason, capacitive isolators generally cannot pass the 10 kV surge test and therefore cannot pass the VDE's reinforced isolation certification.
In reinforced isolation applications where protection of personnel and equipment is required, 10 kV surge protection is required. Surge testing is a critical step in determining the safety level of isolation components in such applications. Analog Devices offers a wide range of iCoupler and isoPower products that are fully capable of meeting this need.
Reference address:Surge Testing of Digital Isolators
Standards published by the International Electrotechnical Commission (IEC) and VDE (Verband der Elektrotechnik) define the use of isolation technology at the system and component level in medical, industrial, consumer, and automotive systems. To ensure the safety of personnel and equipment during high voltage surges, these standards specify different surge ratings based on the isolation level required for the specific application.
There are three common isolation levels: functional isolation, basic isolation, and reinforced isolation. Functional isolation has only a few safety requirements because it is generally only used in applications where the isolation of the ground reference voltage is required to ensure the circuit can operate properly. As can be seen, safety and surge performance are not the main considerations for functional isolation.
However, safety is the main consideration for basic and reinforced isolation, so surge levels are key to determining the quality of isolation. Basic isolation protects end-equipment users from electric shock, while reinforced isolation is a separate isolation system that provides the same protection as two redundant single or basic isolation systems. Medical and industrial applications typically require reinforced isolation to protect patients and end users from lethal electric shock. The VDE reinforced isolation standard for digital isolators is VDE 0884-10, which specifies a minimum surge voltage (VIOSM) rating of 10 kV, and also specifies working voltage (VIORM) and withstand voltage (VISO). The surge voltage
rating of a digital isolator specifies the ability to withstand a surge after being subjected to continuous short-term high-voltage pulses. Figure 1 shows the timing characteristics of a surge waveform that complies with IEC 61000-4-5.
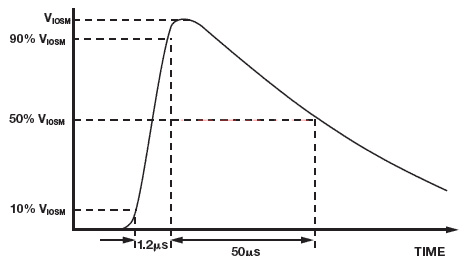
Figure 1. Surge voltage waveform
For testing, place the device on a test board and short all pins across the isolation barrier (see Figure 2). Connect a high-voltage pulse generator to one end of the isolation barrier through a 1000Ω/1000 pF network. Connect the generator loop to the other end of the isolation barrier. Connect a 100 kΩ, 2.5 W resistor across the isolation barrier to discharge the circuit after each pulse. Monitor the pulses with an oscilloscope with a 1000:1 high-voltage probe. Set the discharge gun to the lowest voltage specified in the test plan and the oscilloscope to single-shot trigger. Apply 10 pulses at this voltage level and monitor each pulse with the oscilloscope. A break in the isolation barrier can be seen by a sudden drop in pulse amplitude (to 50% in less than 50 μs). If the part can withstand 10 pulses, increase the discharge gun voltage and apply another 10 pulses. Continue until the isolation barrier fails or until the maximum test voltage is reached.
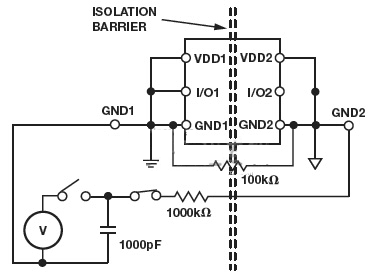
Figure 2. Surge test setup
Whether or not to pass this test depends primarily on the thickness of the insulation (also known as the distance to isolation, or DTI) and the quality of the insulation material. Applied electric fields tend to concentrate at defect points within the insulator, so lower defect densities generally result in higher breakdown ratings. Thicker materials are more resistant to breakdown because the field strength is inversely proportional to the distance between the conductors at either end of the insulator.
Optocouplers can generally pass the 10 kV surge test because the insulator is thick (typically 400 μm), which reduces the effect of insulation quality on the breakdown characteristics. Simply put, the insulation is thick, so high-quality materials are not required to pass the 10 kV test. Transformer-based isolators use a high-quality 20 μm to 32 μm polyimide layer stored in a clean room environment. Because the defect levels of this material are much lower than the injection-molded epoxy used in optocouplers, a much thinner insulation layer can still meet the 10 kV requirement. Capacitive isolators also use a high-quality insulation layer, in this case silicon dioxide (SiO2) deposited during the wafer manufacturing process. Silicon dioxide has a high dielectric strength, but generally cannot be deposited very thickly without causing mechanical stress in the film. Thicker SiO2 also reduces capacitance, which in turn results in a decrease in the coupling efficiency of the isolation barrier. For this reason, capacitive isolators generally cannot pass the 10 kV surge test and therefore cannot pass the VDE's reinforced isolation certification.
In reinforced isolation applications where protection of personnel and equipment is required, 10 kV surge protection is required. Surge testing is a critical step in determining the safety level of isolation components in such applications. Analog Devices offers a wide range of iCoupler and isoPower products that are fully capable of meeting this need.
Previous article:Bearing real-time monitoring system
Next article:Study on Photoelectric Inversion Switch and Its Reliability
- Popular Resources
- Popular amplifiers
Recommended Content
Latest Test Measurement Articles
- From probes to power supplies, Tektronix is leading the way in comprehensive innovation in power electronics testing
- Seizing the Opportunities in the Chinese Application Market: NI's Challenges and Answers
- Tektronix Launches Breakthrough Power Measurement Tools to Accelerate Innovation as Global Electrification Accelerates
- Not all oscilloscopes are created equal: Why ADCs and low noise floor matter
- Enable TekHSI high-speed interface function to accelerate the remote transmission of waveform data
- How to measure the quality of soft start thyristor
- How to use a multimeter to judge whether a soft starter is good or bad
- What are the advantages and disadvantages of non-contact temperature sensors?
- In what situations are non-contact temperature sensors widely used?
MoreSelected Circuit Diagrams
MorePopular Articles
- LED chemical incompatibility test to see which chemicals LEDs can be used with
- Application of ARM9 hardware coprocessor on WinCE embedded motherboard
- What are the key points for selecting rotor flowmeter?
- LM317 high power charger circuit
- A brief analysis of Embest's application and development of embedded medical devices
- Single-phase RC protection circuit
- stm32 PVD programmable voltage monitor
- Introduction and measurement of edge trigger and level trigger of 51 single chip microcomputer
- Improved design of Linux system software shell protection technology
- What to do if the ABB robot protection device stops
MoreDaily News
- Huawei's Strategic Department Director Gai Gang: The cumulative installed base of open source Euler operating system exceeds 10 million sets
- Download from the Internet--ARM Getting Started Notes
- Learn ARM development(22)
- Learn ARM development(21)
- Learn ARM development(20)
- Learn ARM development(19)
- Learn ARM development(14)
- Learn ARM development(15)
- Analysis of the application of several common contact parts in high-voltage connectors of new energy vehicles
- Wiring harness durability test and contact voltage drop test method
Guess you like
- How to control the harmonics of a 25W RF power amplifier to -80dBc?
- Balancing ADC Size, Power, Resolution, and Bandwidth for Precision Data Acquisition Systems
- Problems encountered after reinstalling AD14.3
- Why should we learn about transistor circuits when there are integrated circuits?
- The old version of the forum homepage has a bug
- During this extraordinary period, go out less and study more: Many TI practical courses are presented. If your body cannot be on the road, let your soul be on the road.
- Free Document Download | Littelfuse Power Control and Circuit Protection Solutions
- There are residual line segments in pads that cannot be selected. What is the reason?
- LED constant current control circuit
- January 21 Live Broadcast Review: ADI's Vital Signs Monitoring Solutions in Wearable Products