Current sense resistors are available in a variety of shapes and sizes and are used to measure current in many automotive, power control, and industrial systems. When using very low value resistors (a few mΩ or less), the resistance of the solder will become a significant percentage of the resistance of the sense element, which will significantly increase the measurement error. High-precision applications often use 4-lead resistors and Kelvin sensing techniques to reduce this error, but these specialized resistors can be expensive. In addition, when measuring large currents, the size and design of the resistor pads play a key role in determining the sensing accuracy. This article will describe an alternative approach that uses a standard, low-cost, two-pad sense resistor (4-pad layout) to achieve high-precision Kelvin sensing. Figure 1 shows the test board used to determine the errors caused by five different layouts.

Figure 1. Sense resistor layout test PCB.
Current Sense Resistor
Common current sense resistors in 2512 packages can have resistance values as low as 0.5 mΩ and can dissipate up to 3 W. To demonstrate worst-case error, these tests used a 0.5 mΩ, 3 W resistor with a 1% tolerance (Part No. ULRG3-2512-0M50-FLFSLT Manufacturer: Welwyn/TTelectronics) with dimensions and a standard 4-wire package as shown in Figure 2.

Figure 2. (a) Dimensions of the ULRG3-2512-0M50-FLFSLT resistor; (b) standard 4-pad package.
Traditional Package
For Kelvin sensing, the standard two-wire package pads must be split to provide separate paths for the system current and the sense current. Figure 3 shows an example of such a layout. The system current follows the path indicated by the red arrow. If a simple two-pad layout is used, the total resistance is:
To avoid adding resistance, the voltage sense traces need to be properly routed to the sense resistor pads. The system current will cause a significant voltage drop in the upper solder joint, but the sense current will cause a negligible voltage drop in the lower solder joint. This pad splitting scheme can eliminate the solder joint resistance from the measurement, thereby improving the overall accuracy of the system.

Figure 3. Kelvin sensing.
Optimizing Kelvin Packages
The layout shown in Figure 3 is a significant improvement over the standard two-pad approach, but the physical location of the sense point on the pad and the symmetry of the current flowing through the resistor become more significant when using very low value resistors (0.5 mΩ or less). For example, the ULRG3-2512-0M50-FLFSL is a solid metal alloy resistor, so every millimeter that the resistor extends along the pad will affect the effective resistance. Using a calibrated current, the optimal sense layout was determined by comparing the voltage drops across five custom packages. [page]
Test PCB
Figure 4 shows five layout patterns constructed on a test PCB, labeled A through E. Whenever possible, we routed the traces to test points at different locations along the sense pad, represented by the colored dots in the figure. The individual resistor packages are:

1. Standard 4-wire resistor based on the 2512 recommended footprint (see Figure 2(b)). The sense point pairs (X and Y) are located at the outer and inner edges of the pad (x-axis).
2. Similar to A, but the pad extends inward longer to better cover the pad area (see Figure 2(a)). The sense points are located at the center and ends of the pad.
3. Use both sides of the pad to provide a more symmetrical system current path. Also move the sense points to a more central location. The sense points are located at the center and ends of the pad.
4. Similar to C, except that the system current pads are joined at the innermost point. Only the outer sense points are used.
5. A hybrid of A and B. The system current flows through the wider pad and the sense current flows through the smaller pad. The sense points are located at the outer and inner edges of the pad.

Figure 4. Layout of the test PCB.
Solder was applied to the stencil and reflow soldering was performed in a reflow oven. The ULRG3-2512-0M50-FLFSLT resistor was used.
Test Steps
The test design is shown in Figure 5. A calibrated current of 20 A was passed through each resistor while the resistor was maintained at 25°C. The resulting differential voltage was measured within 1 second after the current was applied to prevent the resistor temperature from rising more than 1°C. The temperature of each resistor was also monitored to ensure that the test results were measured at 25°C. The ideal voltage drop across a 0.5 mΩ resistor is 10 mV at 20 A.
[attach]87555[/attach]
Figure 5. Test setup.
Test Results
Table 1 lists the data measured using the sense pad locations shown in Figure 4.
Table 1. Measured Voltages and Errors
Footprint |
Sense Pad |
Measured (mV) |
Error (%) |
A |
Y |
9.55 |
4.5 |
|
X |
9.68 |
3.2 |
B |
Y |
9.50 |
5 |
|
X |
9.55 |
4.5 |
C |
Y |
9.80 |
2 |
|
X |
9.90 |
1 |
D |
X |
10.06 |
0.6 |
E |
Y |
9.59 |
4.1 |
X |
9.60 |
4 |
|
|
Top pad* |
12.28 |
22.8 |
*No Kelvin sensing. The voltage across the high current main pad was measured to demonstrate the error associated with solder resistance.
Observations
1. Packages C and D have the least error due to the comparability of the results and the fact that the individual resistor variations are within tolerance. Package C is the preferred package as it is less likely to cause issues associated with component placement tolerances.
2. In each case, the sensing points at the outer ends of the resistors provide the most accurate results. This suggests that the resistors were designed by the manufacturer based on the total length of the resistors.
3. Note that the error associated with solder resistance is 22% when Kelvin sensing is not used. This equates to a solder resistance of approximately 0.144 mΩ.
4. Package E demonstrates the effects of an asymmetric pad layout. During reflow, the component passes through a large amount of solder to reach the pad. This package should be avoided.
Conclusion
Based on the results shown previously, the best package is C, which has an expected measurement error of less than 1%. The recommended dimensions for this package are shown in Figure 6.

Figure 6. Optimal package size.
The layout of the sense traces also affects the measurement accuracy. For the highest accuracy, the sense voltage should be measured at the edge of the resistor. The recommended layout shown in Figure 7 uses vias to route the outer edge of the pad to another layer, thus avoiding cutting the main power plane.

Figure 7. Recommended PCB trace routing.
The data in this article may not apply to all resistors, and results may vary depending on the resistor material and size. The resistor manufacturer should be consulted. It is the user's responsibility to ensure that the layout dimensions and construction of the package meet all SMT manufacturing requirements. ADI is not responsible for any problems that may arise from the use of this package.
Previous article:Example of integrated instrumentation for optimized switching measurements
Next article:Optimizing Isolation System Design Using Digital Isolators
Recommended ReadingLatest update time:2024-11-17 10:31
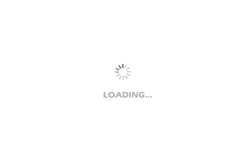
- Popular Resources
- Popular amplifiers
- Keysight Technologies Helps Samsung Electronics Successfully Validate FiRa® 2.0 Safe Distance Measurement Test Case
- From probes to power supplies, Tektronix is leading the way in comprehensive innovation in power electronics testing
- Seizing the Opportunities in the Chinese Application Market: NI's Challenges and Answers
- Tektronix Launches Breakthrough Power Measurement Tools to Accelerate Innovation as Global Electrification Accelerates
- Not all oscilloscopes are created equal: Why ADCs and low noise floor matter
- Enable TekHSI high-speed interface function to accelerate the remote transmission of waveform data
- How to measure the quality of soft start thyristor
- How to use a multimeter to judge whether a soft starter is good or bad
- What are the advantages and disadvantages of non-contact temperature sensors?
- Innolux's intelligent steer-by-wire solution makes cars smarter and safer
- 8051 MCU - Parity Check
- How to efficiently balance the sensitivity of tactile sensing interfaces
- What should I do if the servo motor shakes? What causes the servo motor to shake quickly?
- 【Brushless Motor】Analysis of three-phase BLDC motor and sharing of two popular development boards
- Midea Industrial Technology's subsidiaries Clou Electronics and Hekang New Energy jointly appeared at the Munich Battery Energy Storage Exhibition and Solar Energy Exhibition
- Guoxin Sichen | Application of ferroelectric memory PB85RS2MC in power battery management, with a capacity of 2M
- Analysis of common faults of frequency converter
- In a head-on competition with Qualcomm, what kind of cockpit products has Intel come up with?
- Dalian Rongke's all-vanadium liquid flow battery energy storage equipment industrialization project has entered the sprint stage before production
- New breakthrough! Ultra-fast memory accelerates Intel Xeon 6-core processors
- New breakthrough! Ultra-fast memory accelerates Intel Xeon 6-core processors
- Consolidating vRAN sites onto a single server helps operators reduce total cost of ownership
- Consolidating vRAN sites onto a single server helps operators reduce total cost of ownership
- Allegro MicroSystems Introduces Advanced Magnetic and Inductive Position Sensing Solutions at Electronica 2024
- Car key in the left hand, liveness detection radar in the right hand, UWB is imperative for cars!
- After a decade of rapid development, domestic CIS has entered the market
- Aegis Dagger Battery + Thor EM-i Super Hybrid, Geely New Energy has thrown out two "king bombs"
- A brief discussion on functional safety - fault, error, and failure
- In the smart car 2.0 cycle, these core industry chains are facing major opportunities!
- Compile QT5 application with qt creator
- micropython update: 2021.3
- Show off the Xiaomi mouse I received from the Ti reading activity
- [AutoChips AC7801x motor demo board review] + motor demo board unboxing report and quick new project
- About the problem of L6226 controlling brushless DC motor
- Publish a batch of paper books
- Evaluation of domestic FPGA Gaoyun GW1N-4 series development board - stepper motor control (modified)
- Camel air conditioner fan 220v series 16v capacitor, please help analyze
- QT Py Color Cuff
- Some points to note when designing 2812