Information construction is the theme of future coal mine work. At present, various mandatory laws and regulations on industrial site safety issues have been introduced one after another, and mining measurement and monitoring products have become the focus of mining products. Mining electronic belt scales are the main tools for coal mine production measurement and monitoring. The composition structure is divided into composite configuration and intrinsically safe configuration. Composite dosing means that the data acquisition and transmission parts are installed at the underground belt scale site, and the metering instruments are installed in the dispatching room above the well. This composition structure requires contacting the dispatching room by phone when the belt scale is zeroed and calibrated, and there are many links that need to be maintained on site. The intrinsically safe configuration means that the data acquisition and metering instruments are designed and installed together next to the belt scale, which is convenient for operation and maintenance.
1 Composition of mining electronic belt scale
The mining electronic belt scale consists of five parts: a scale frame (fixed frame and suspended frame), a weighing sensor , a speed sensor, a metering instrument, and a flameproof and intrinsically safe DC voltage regulator power supply. In order to facilitate the statistical measurement data, a set of upper computer software and a printer will be added to the coal mine dispatching room. The structure of the mining electronic belt scale is shown in Figure 1.
All components of the mining electronic belt scale are designed to be intrinsically safe or flameproof and intrinsically safe, and can work in dangerous environments with explosive gas or dust. The meter collects the signals of the weighing sensor and speed sensor, and sends them to the host computer through the communication module after calculation and processing. The meter supports Ethernet and RS485 communication methods, and completes human-computer interaction through LCD 显示器\'); companyAdEvent.show(this,\'companyAdDiv\',[5,18])"> display and keyboard.
2 Electrical Design
The measuring instrument uses the STM32F103VB processor as the hardware core, and has expanded Ethernet interface, RS485 communication interface, frequency acquisition, AD, switch quantity acquisition, real-time clock, LCD display, infrared remote control interface and keyboard. The RS485 communication interface uses SN75LBC184, which has strong lightning resistance. For some sites with harsh environments, it can be directly connected to the transmission line without any external protection components. In order to enhance the anti-interference ability of the instrument, TLP521 is used to isolate the processor and SN75LBC184, and DC/DC module IB0505 is used to isolate the power supply of SN75LBC184 from the main circuit power supply of the instrument. D1~D4 are voltage regulator diodes. The voltage regulator values of D1 and D3 are 12V, and the voltage regulator values of D2 and D4 are 7V, so as to ensure that the signal amplitude is limited between -7 and 12 V and improve the ability to resist overvoltage. R21 is a line matching resistor, which can reduce the reflection of the transmission signal on the line. The circuit design is shown in Figure 2.
The weight signal acquisition circuit of the measuring instrument uses a high-precision 24-bit serial A/D converter CS5532, with a 2.5 V high-precision reference voltage chip AD780, a clock frequency of 4.9152MHz, and configuration parameters of an output update rate of 12.5Hz, a system gain of 256, and an effective resolution of 16 bits. The digital power supply VCC and the analog power supply AVCC in the weight signal acquisition circuit are isolated by magnetic beads. R27, R28, C62 and C63 form two-way low-pass filters in both directions , which can eliminate high-order harmonics and most high-frequency noise signals, and reduce the frequency spectrum aliasing scene when performing harmonic analysis. D8, D9, D11 and D12 form a voltage limiting circuit. Prevent the external input line from being connected to a higher power supply to damage the chip. The circuit design is shown in Figure 3.
[page]
3 Software Design
The software is designed based on C language and uses IAR Embedded Workbench compilation environment, including main program design, communication program design, weight signal acquisition program design, infrared decoding design, LCD display program design, switch input program design, keyboard program design, etc. The metering instrument exchanges data with the host computer through Ethernet and RS485 communication. The production record and metering parameters of the metering instrument can be queried through the host computer software. Since BS485 has relatively low requirements for underground installation lines and does not require the addition of mining switches, most coal mines use RS485 communication. The RS485 data frame format uses ASCII encoding, that is, a hexadecimal number (such as: 0×3E) is divided into 2 bytes of ASCII code (0×33 and 0×45) for transmission. This encoding method can avoid the occurrence of bytes in the valid segment of the data frame that are the same as the start or end bit of the data frame. The RS485 communication program flow chart is shown in Figure 4.
CS5532 has a 20ms delay when starting up, and it is initialized after 20ms. Since CS5532 cannot be reset on power-on, the processor needs to send an initialization sequence through the ADC serial port, that is, at least 15 SYNC1 (0×FF) command bytes and 1 SYNC0 (0×FE) command byte, so that the ADC serial port enters the command mode, and then sets the RS bit of the configuration register to complete the chip reset.
The CS5532 initialization code is as follows:
The weighing sensor interface of the metering instrument adopts a parallel access design, which can enhance the anti-interference ability of the weight signal acquisition circuit. In addition, compared with the series design, the parallel access design can avoid the problem that the metering instrument cannot collect data due to damage to individual weighing sensors. The weighing sensor is powered by 5 V, with an accuracy of 2 mV/V and a full-scale output of 10mV. The range of the full-scale input signal that CS5532 can measure is determined by the gain setting and VREF+ and VPEF-. The calculation formula is: ((VREF+)-(VREF-))/(Gx4), where G is the gain amplifier coefficient, VREF+ and VREF- are the positive and negative of the reference voltage , respectively, and the value of A is determined by the reference voltage selection bit VRS. When VBS is set to 0, A=2, and when VRS is set to 1, A=1. The reference voltage of the weight signal acquisition circuit is designed to be 2.5 V, that is, VREF+ is 2.5 V, VREF- is 0 V, the CS5532 initialization program sets VBS to 1, A=1, and the gain G is set to 256, so the full-scale input range that CS5532 can measure is 2.5/256≈9.7 mV. Because there is a certain margin when the weighing sensor is selected according to the maximum flow rate of the electronic belt scale for mining, that is, the output of the weighing sensor will not exceed 9 mV when the electronic belt scale for mining is at the maximum flow rate, so the parameter configuration of CS5532 can meet the measurement accuracy requirements of the electronic belt scale for mining.
4. Security Design
The metering instrument has adopted a variety of explosion-proof measures, and the explosion-proof type is intrinsically safe. The communication circuit of the metering instrument uses a Zener safety barrier circuit to isolate the intrinsically safe end and the non-intrinsically safe end, as shown in Figure 5. R1 uses a 10Ω, 0.5W metal thick film resistor to limit the current that may flow through the intrinsically safe circuit. Four Zener diodes Z1~Z2 form a double overvoltage protection circuit for voltage limiting. Under normal operating conditions, the voltage applied between the non-intrinsically safe ends is lower than the maximum operating voltage Umax (lower than the breakdown voltage of the Zener diode). At this time, the Zener diode is in a non-conducting state. Except for a very small leakage current, it is in an "open circuit" state. When a fault occurs at the non-intrinsically safe end, such as when a high voltage is mixed in, the Zener diode breaks down in reverse and is in a "conducting" state. At this time, the Zener diode limits the mixed high voltage to the Zener voltage. As the Zener diode is turned on, its current rises sharply, and the fuse blows instantly, cutting off the high voltage flowing to the site, preventing the danger of high voltage detonating explosive materials on site, and protecting the safety of on-site equipment and personnel. To prevent the Zener diode and the wiring from short-circuiting, wiring is prohibited under the Zener diode, which ensures the safety and explosion-proof characteristics of the system on the one hand, and enhances the anti-interference ability of the system on the other hand, thereby improving the reliability of system operation.
To prevent any unit from being overhauled or replaced that affects the intrinsic safety performance, the safety barrier is completely potted with WCC-87 flame-retardant epoxy resin. The ratio of the component resin (including flame retardant) and curing agent of WCC-87 flame-retardant epoxy resin is 100:2, and the viscosity is 950±100 centipoise. The potting part should be free of dust and impurities and kept dry. The potting material level should exceed the safety barrier by 3mm. After potting, it should be left at room temperature for 4 hours, and then put into a thermostat (80℃) for curing for 4 hours. There should be no bulges, cracks or bubbles on the surface of the potting material.
5 Conclusion
Measuring instruments apply signal acquisition, data processing, remote transmission and explosion-proof technology to their design. During the production process, the circuit boards of measuring instruments must be coated with three-proof paint at least twice to effectively prevent moisture, dust and static electricity. Strict inspections must be carried out before leaving the factory, including appearance and structure inspections, main technical indicator tests, working stability tests, power supply fluctuation capacity tests, insulation resistance tests and power frequency withstand voltage tests. After testing, the zero-point temperature performance of the weight signal of the measuring instrument is: <0.5μV/℃, the full-scale temperature performance of the weight signal is: <15 ppm/℃, and the linearity error of the weight signal is: <0.02%F. S. After specific circuit analysis and test certification by the national explosion-proof inspection agency, the design intrinsic safety parameters are: Ui=5.8V, Ii=1.4A, Li=0, Ci=40μF.
Previous article:Application of cubic spline interpolation in error compensation of weighing instruments
Next article:Design of a universal photovoltaic system test platform
Recommended ReadingLatest update time:2024-11-16 15:59
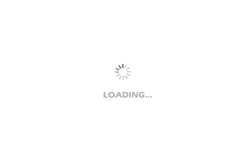
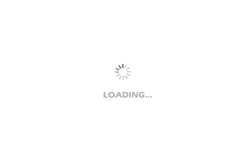
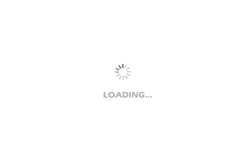
- Popular Resources
- Popular amplifiers
-
Siemens S7-1200-PLC Programming and Application Tutorial (3rd Edition) (Edited by Shi Shouyong)
-
100 Examples of Microcontroller C Language Applications (with CD-ROM, 3rd Edition) (Wang Huiliang, Wang Dongfeng, Dong Guanqiang)
-
Practical training guidance for new electrician technology (Wu Qihong, Jiang Jian, Xu Kungang, Zhang Hong)
-
Teach you to learn 51 single chip microcomputer-C language version (Second Edition) (Song Xuefeng)
- Keysight Technologies Helps Samsung Electronics Successfully Validate FiRa® 2.0 Safe Distance Measurement Test Case
- From probes to power supplies, Tektronix is leading the way in comprehensive innovation in power electronics testing
- Seizing the Opportunities in the Chinese Application Market: NI's Challenges and Answers
- Tektronix Launches Breakthrough Power Measurement Tools to Accelerate Innovation as Global Electrification Accelerates
- Not all oscilloscopes are created equal: Why ADCs and low noise floor matter
- Enable TekHSI high-speed interface function to accelerate the remote transmission of waveform data
- How to measure the quality of soft start thyristor
- How to use a multimeter to judge whether a soft starter is good or bad
- What are the advantages and disadvantages of non-contact temperature sensors?
- Innolux's intelligent steer-by-wire solution makes cars smarter and safer
- 8051 MCU - Parity Check
- How to efficiently balance the sensitivity of tactile sensing interfaces
- What should I do if the servo motor shakes? What causes the servo motor to shake quickly?
- 【Brushless Motor】Analysis of three-phase BLDC motor and sharing of two popular development boards
- Midea Industrial Technology's subsidiaries Clou Electronics and Hekang New Energy jointly appeared at the Munich Battery Energy Storage Exhibition and Solar Energy Exhibition
- Guoxin Sichen | Application of ferroelectric memory PB85RS2MC in power battery management, with a capacity of 2M
- Analysis of common faults of frequency converter
- In a head-on competition with Qualcomm, what kind of cockpit products has Intel come up with?
- Dalian Rongke's all-vanadium liquid flow battery energy storage equipment industrialization project has entered the sprint stage before production
- Allegro MicroSystems Introduces Advanced Magnetic and Inductive Position Sensing Solutions at Electronica 2024
- Car key in the left hand, liveness detection radar in the right hand, UWB is imperative for cars!
- After a decade of rapid development, domestic CIS has entered the market
- Aegis Dagger Battery + Thor EM-i Super Hybrid, Geely New Energy has thrown out two "king bombs"
- A brief discussion on functional safety - fault, error, and failure
- In the smart car 2.0 cycle, these core industry chains are facing major opportunities!
- The United States and Japan are developing new batteries. CATL faces challenges? How should China's new energy battery industry respond?
- Murata launches high-precision 6-axis inertial sensor for automobiles
- Ford patents pre-charge alarm to help save costs and respond to emergencies
- New real-time microcontroller system from Texas Instruments enables smarter processing in automotive and industrial applications
- Live Review: TI Ultrasonic Gas Flow Measurement Innovation Solution + CC13X2/CC26X2
- What a mess it is to have a 0.1uf capacitor with a problem {Complain about this here}
- PCB impedance control experience sharing
- Domestic sewage treatment online monitoring system
- Be careful when shopping on June 18: China Consumers Association warns consumers that so-called "quantum products" are "pseudo-technology"
- Getting Started with the ST SensorTile.box Sensor Kit (3) Expert Mode Experience
- Problem 2 of 7S3P battery pack
- Netizens are porting mpy to Nucleo-32
- LOTO arbitrary waveform generator SIG82 simulates the output of relay energization and disconnection signal waveforms for algorithm debugging
- For sale: 4412 development board