In the measurement and control system, the output signal of the sensor is affected by many factors and often mutates. The values of these mutation points contain important fault information. Accurately capturing and distinguishing the causes of these mutation points is the key to sensor fault diagnosis. The literature only relies on the output time series of the sensor to diagnose the fault of the sensor, and attributes the mutation of the sensor output signal to the fault of the sensor. The approach of the literature is to perform wavelet transform on the input and output signals of the control system respectively . When the wavelet function can be regarded as the first-order derivative of a smooth function, the mutation point of the signal corresponds to the modulus maximum of its wavelet transform. The mutation point is detected, and the residual sequence is generated and the sensor fault is analyzed. It is believed that the mutation of the sensor output signal is caused by the fault of the sensor or the mutation of the system input signal. In fact, there are many reasons for the mutation of the sensor output signal. In addition to the mutation of the system input and the fault of the sensor itself, there are also process disturbances, actuator faults, controller faults, controlled objects and external electromagnetic field interference. In practical applications, the above sensor fault diagnosis methods have certain limitations. Usually, in industrial process control, the time constant of the controlled object is large and cannot respond to the high-frequency components in the mutation signal . Based on the frequency band analysis technology of wavelet transform, the author discusses and analyzes the reasons that lead to sudden changes in sensor output signals, and provides a practical analysis method for fault diagnosis and performance evaluation of online sensors.
1 Generation and Characteristic Analysis of Mutation Signals
A typical control system generally consists of four parts: controller (Gc(s)), actuator (Gv(s)), controlled object (Go(g), Gd(s)) and sensor ((Gm(s)), and its block diagram is shown in Figure 1.
In the figure, X(s) is the sensor output (i.e. the measured value of the controlled parameter of the control system).
The time constant of the dynamic characteristics of most controlled objects in general industrial processes is relatively large. In order to ensure fast and undistorted detection of their output signals, the time constant of the dynamic characteristics of sensors is relatively small.
The sudden change signal of a system (sensor) refers to the sudden increase or decrease of its output amplitude and frequency at a large rate, and the two are interdependent.
1.1 Mutations caused by input R(s)
In Figure 1, let
Its logarithmic frequency characteristic curve be shown in Figure 2.
From the curve, we can get the cutoff frequency of this combination link ωc≈1 Hz.
The characteristics of the high frequency band of the curve (the section where ω>100ωc) are determined by the smaller time constants in Gc(s), Gv(s), and Go(s). Since it is far away from ωc and decays in the direction of -∞dB with a larger slope, it reflects the low-pass
filtering
characteristics of the combined link, forming the characteristic that the system cannot respond to the high-frequency components in the input signal. The characteristics of the high frequency band have little effect on the transient performance of the system, but it reflects that the time domain response cannot change in steps. Therefore, there is a delay time. The high frequency band directly reflects the system's ability to suppress the high-frequency components in the input signal. The lower the decibel value, the stronger the suppression ability.
Since the time constant To of general industrial objects is generally large, the cutoff frequency ωc is small. Therefore, when the input R(s) changes suddenly, the frequency distribution of the response sudden change signal of the object output Xo(s) and the sensor output X(s) is low and the frequency band is narrow.
1.2 Sudden changes caused by controller and actuator failures and process disturbances
Using the same analysis method, we can draw the same conclusion: the frequency distribution of the output response mutation signal caused by the fault of the controller and actuator and the mutation of the process disturbance is lower and the frequency band is narrower.
1.3 Mutations caused by strong external electromagnetic field interference
It is generally believed that sensors can resist various high-frequency electronic (radio, not considered here) interference. External strong electromagnetic field interference generally does not cause changes in the output Xo(s) of the controlled object. It often directly causes changes in the sensor output signal X(s) through circuit coupling, and it is generally a pulse signal.
1.4 Mutations caused by sensor failure
Sensor faults are divided into abrupt faults and incipient faults. The author only analyzes abrupt faults. Abrupt faults of sensors mainly include deviation faults, pulse faults, drift faults and periodic faults. Regardless of the type of abrupt fault, it will directly lead to a sudden change in the sensor output signal X(s). Since these abrupt faults are caused by sudden changes in the parameters of the internal components of the sensor, the frequency band of the output X(s) response sudden change signal is relatively wide, containing not only low-frequency components but also certain high-frequency components. This is a significant feature that is different from the sensor output X(s) response sudden change signal caused by sudden changes in the input signal, controller failure, actuator failure and process disturbance. It is the theoretical basis for distinguishing the causes of sudden changes and conducting sensor fault diagnosis in this article.
1.5 Sudden changes caused by faults in controlled objects
When a fault occurs in the controlled object, the frequency spectrum of the mutation signal is closely related to the input frequency band of the sensor. When the input frequency band of the sensor is wide, the mutation signal will contain high-frequency components. However, the input frequency band of sensors used in general industrial processes is narrow, and the mutation signal generally does not contain high-frequency components. The various mutation causes and their signal characteristics are shown in Table 1.
2 Frequency band analysis based on wavelet transform
Wavelet analysis in a narrow sense refers only to multi-resolution analysis, while wavelet analysis in a broad sense includes two parts: multi-resolution analysis and wavelet packet analysis. Their relationship is shown in Figure 3.
The thick solid line in Figure 3 is the multi-resolution decomposition process. Wavelet packet decomposition is a generalization of the multi-resolution decomposition of wavelet transform. Multi-resolution decomposition only decomposes the scale space V, that is,
Wavelet packet decomposition further decomposes the undecomposed wavelet space Wj in multi-resolution decomposition. Because the wavelet space division corresponds to the frequency band division, wavelet packet decomposition can obtain higher frequency resolution. Most common frequency band analysis is based on wavelet packet analysis, but while it improves the frequency resolution, the complexity of the algorithm is also increased. The author chose a method based on multi-resolution analysis based on the needs of practical problems, which can meet the requirements. [page]
2.1 Frequency band analysis method
Assume that the bandwidth of the signal X(t) is [0, f], and the number of decomposition layers is N. After multi-resolution decomposition, the signal frequency range corresponding to each space is used to analyze the signal in different frequency bands. Usually, the signal can be decomposed on a certain scale according to the frequency range of the signal of interest, so as to extract the information in the corresponding frequency band. If the energy of the signal in each frequency band is statistically analyzed to form a characteristic vector reflecting the signal energy, it is called the energy analysis of the frequency band.
2.2 Wavelet frequency band and energy integral
The theoretical basis of wavelet band analysis technology is the Parseval energy integral equation. For discrete orthogonal wavelet transform, the Parseval equation is:
Where: x(t) is the signal to be analyzed;
2.3 Analysis steps
According to the analysis results in Table 1, the energy band analysis based on multi-resolution analysis is implemented as follows:
① Using the prior knowledge of the system mathematical model, determine the cutoff frequency ωc of the object, and use 0~10ωc as the system bandwidth;
② Determine the appropriate sampling frequency to ensure that the electromagnetic interference signal can be collected. If the sampling frequency is f, then the analysis frequency
③ Determine the appropriate wavelet decomposition layer number N, so that 0~lOωc is just included in the low-frequency space VN, and divide the entire analysis space into relative low-frequency space and high-frequency space. Except for the low-frequency space VN where the system bandwidth is located, the remaining spaces WN, WN-1, and Wl are merged into high-frequency space;
④ Select a suitable wavelet function for multi-resolution decomposition, and use the wavelet coefficients obtained by decomposition to calculate the energy of the signal in the corresponding space (frequency band) according to formula (1), forming a two-dimensional vector e=[e1, e2] that represents the signal energy in the space, where e1 represents the energy of the low-frequency signal and e2 represents the energy of the high-frequency signal;
⑤ Normalize the two-dimensional vector e=[e1, e2] representing the spatial energy, that is
Perform feature analysis. e01 represents the ratio of the energy of the low-frequency signal to the total energy, and e02 represents the ratio of the energy of the high-frequency signal to the total energy.
3Simulation Analysis
The author conducted a simulation experiment on the typical system shown in Figure 1. In normal working state, the values of Gc(s), Gv(s), and Go(s) are the same as before.
At different moments when the system is stable, R(s) and D1(s) are changed by unit step; D2(s) changes from 0 to a pulse signal with an amplitude of 1 or a periodic signal of 0.2sin100πt; the characteristic function of the object and the sensor switches between normal value and fault value to simulate 5 reasons and 6 forms of sudden changes in the output signal, and collect data of each sudden change process. Regardless of the cause of the signal sudden change, its high-frequency signal component is generated instantly and disappears quickly. Therefore, in the total energy of the collected signal, the high-frequency component accounts for a small proportion. In order to improve the sensitivity of the detection, the collected data is processed to remove "DC", that is, the sampled data is subtracted from the average value of the 10 points before the signal sudden change. In addition, zero-mean white noise with a variance of 0.003 is added to the sampled data. The sampling frequency of the system is f = 200 Hz, the analysis frequency is fo = 100 Hz, and the db4 wavelet is used to decompose the signal into three layers. In this way, the signal frequency range of the low-frequency space is 0 ~ 12.5 Hz, and the signal frequency range of the high-frequency space is 12.5 ~ 100 Hz. The high-frequency coefficients obtained by analysis are denoised by hard threshold, and then the energy ratio statistics are performed according to formula (1). The results are shown in Table 2.
In Table 2, the proportion of low-frequency components of the mutation signal caused by external electromagnetic field interference is small, which is the result of "DC" removal; the proportion of high-frequency components of the mutation signal caused by the fault of the controlled object is very small, which is because the input frequency band of the sensor used in this simulation is only a dozen Hz. The consistency of the simulation results in Table 2 and the theoretical analysis results in Table 1 shows the effectiveness of this method.
4 Experimental studies
The experimental study was conducted on a constant pressure water supply system, as shown in Figure 4. The pressure sensor is LDG-S type. After testing, the transfer function of the generalized object G(s) = l/(0.22s+1). The setting values of the regulator parameters are: proportionality P = 142%, integral time ti = 3 s, differential time td = 2 s, from which it can be estimated that the low frequency band frequency is less than 4 Hz. At different times when the system is stable, the given value is adjusted to simulate the given input mutation signal, the zero point is adjusted to simulate the sensor constant deviation fault, the regulator proportionality is adjusted to simulate the regulator fault, and the surrounding motors are frequently started and stopped to simulate the sensor output mutation caused by the electromagnetic field, and the experimental data under various conditions are collected. The sampling frequency of the system is f = 128 Hz, the analysis frequency is fo = 64 Hz, and the db4 wavelet is used to decompose the signal into 4 layers. In this way, the signal frequency range of the low-frequency space is 0 ~ 4 Hz, and the signal frequency range of the high-frequency space is 4 ~ 64 Hz. The high-frequency coefficients obtained by analysis are subjected to hard threshold denoising, and then the energy ratio statistics are performed according to formula (1). The results are shown in Table 3. It can be seen from Table 3 that the experimental results are consistent with the simulation results in Table 2 and the theoretical analysis results in Table 1, which shows the effectiveness of this method.
5 Conclusion
The mutation signal output by the sensor contains very important fault information. The frequency composition of the mutation signal is different for different mutation causes. For controlled objects with large time constants, the mutation signal of the sensor caused by given input changes, interference changes, controller failures and actuator failures usually only has low-frequency components. The mutation signal caused by the fault of the controlled object usually only has low-frequency components. The mutation signal caused by external electromagnetic field interference is generally a pulse signal, containing low-frequency components and more high-frequency components. In addition to low-frequency components, the mutation signal caused by sensor deviation fault also contains a small amount of high-frequency components.
The wavelet frequency band analysis method based on the system mathematical model proposed in this paper does not require high accuracy of the mathematical model and can effectively diagnose sensor faults, providing a new idea for sensor fault detection and performance evaluation.
Previous article:Application of SDRAM in Arbitrary Waveform Generator
Next article:AD9959 simplifies the design of signal synchronization between multiple DDS in measurement and control communication system
Recommended ReadingLatest update time:2024-11-16 15:19
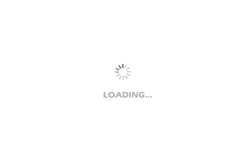
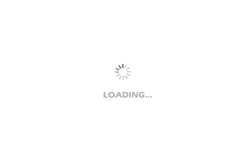
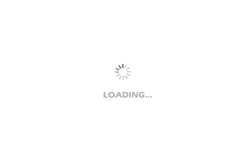
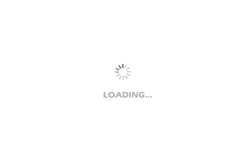
- Popular Resources
- Popular amplifiers
-
Analysis and Implementation of MAC Protocol for Wireless Sensor Networks (by Yang Zhijun, Xie Xianjie, and Ding Hongwei)
-
Introduction to Internet of Things Engineering 2nd Edition (Gongyi Wu)
-
西门子S7-12001500 PLC SCL语言编程从入门到精通 (北岛李工)
-
Modern Motor Control Technology (Wang Chengyuan, Xia Jiakuan, Sun Yibiao)
- Keysight Technologies Helps Samsung Electronics Successfully Validate FiRa® 2.0 Safe Distance Measurement Test Case
- From probes to power supplies, Tektronix is leading the way in comprehensive innovation in power electronics testing
- Seizing the Opportunities in the Chinese Application Market: NI's Challenges and Answers
- Tektronix Launches Breakthrough Power Measurement Tools to Accelerate Innovation as Global Electrification Accelerates
- Not all oscilloscopes are created equal: Why ADCs and low noise floor matter
- Enable TekHSI high-speed interface function to accelerate the remote transmission of waveform data
- How to measure the quality of soft start thyristor
- How to use a multimeter to judge whether a soft starter is good or bad
- What are the advantages and disadvantages of non-contact temperature sensors?
- Innolux's intelligent steer-by-wire solution makes cars smarter and safer
- 8051 MCU - Parity Check
- How to efficiently balance the sensitivity of tactile sensing interfaces
- What should I do if the servo motor shakes? What causes the servo motor to shake quickly?
- 【Brushless Motor】Analysis of three-phase BLDC motor and sharing of two popular development boards
- Midea Industrial Technology's subsidiaries Clou Electronics and Hekang New Energy jointly appeared at the Munich Battery Energy Storage Exhibition and Solar Energy Exhibition
- Guoxin Sichen | Application of ferroelectric memory PB85RS2MC in power battery management, with a capacity of 2M
- Analysis of common faults of frequency converter
- In a head-on competition with Qualcomm, what kind of cockpit products has Intel come up with?
- Dalian Rongke's all-vanadium liquid flow battery energy storage equipment industrialization project has entered the sprint stage before production
- Allegro MicroSystems Introduces Advanced Magnetic and Inductive Position Sensing Solutions at Electronica 2024
- Car key in the left hand, liveness detection radar in the right hand, UWB is imperative for cars!
- After a decade of rapid development, domestic CIS has entered the market
- Aegis Dagger Battery + Thor EM-i Super Hybrid, Geely New Energy has thrown out two "king bombs"
- A brief discussion on functional safety - fault, error, and failure
- In the smart car 2.0 cycle, these core industry chains are facing major opportunities!
- The United States and Japan are developing new batteries. CATL faces challenges? How should China's new energy battery industry respond?
- Murata launches high-precision 6-axis inertial sensor for automobiles
- Ford patents pre-charge alarm to help save costs and respond to emergencies
- New real-time microcontroller system from Texas Instruments enables smarter processing in automotive and industrial applications
- Agitek case sharing - Metrology and testing demonstration case of automotive electronic modules
- How to turn off MPLAB XIDE's code optimization function
- IoT Smart Parking Solutions
- EPWM1 A and B pulses are not complementary
- Find the parameters of the low-pass filter
- Bone vibration sensor and high-quality voice calls (including working principles)
- Millimeter wave sensors
- New Year's flavor competition, post photos during the New Year to win gifts~~
- C language function interrupt function
- NUCLEO_G431RB Review - First Experience