In order to meet the requirements of portability and intelligence of nuclear radiation detectors, the software and hardware implementation methods of multi-probe nuclear radiation dose rate meter with MSP430F169 single-chip microcomputer as the core are discussed. On the basis of introducing the whole system, the key issues in the instrument design are explained in detail, focusing on the principle of supplying high voltage to multiple probes through single-chip microcomputer and the implementation method of data transmission after connecting multiple probes respectively, and the schematic diagram of the single-chip microcomputer peripheral circuit is given. The experiment proves that the instrument can be fully used in the field of nuclear radiation detection, and has the advantages of miniaturization, digitization and low power consumption.
At present, domestic radiation protection instruments, whether portable or fixed monitoring instruments, all adopt the form of one probe corresponding to one host, while foreign countries already have models with multiple probes corresponding to one host. The biggest advantage of this multi-probe radiation measuring instrument is that you only need to replace different digital probes to measure the dose rates of α, β, and γ respectively without changing the host. Moreover, when measuring the same kind of rays, you can also choose different types of probes according to different situations, and use the advantages of the selected probes to expand the instrument's range. At the same time, it avoids the repeated development of similar circuit boards, and product upgrades and changes in system composition only require changing the software, which greatly reduces costs in many aspects.
1 System Overview
This system consists of two parts: the probe and the host. The detector types inside the external probe include ZnS detector for measuring α, plastic scintillator detector for measuring β, NaI crystal detector for measuring γ, dual scintillator detector for measuring α and β at the same time, and dual GM tube detector for measuring α, β and γ at the same time. The probe has a built-in MSP430F169 microcontroller to improve its digitalization; the host is a detection system with the MSP430F169 microcontroller as the core. The MSP430F169 microcontroller is an ultra-low power 16-bit mixed signal processor with higher computing performance than an 8-bit processor, far more than twice. In this design, the MSP430F169 works in low-power mode 0 most of the time, with a power consumption of 50μA/s. Only when the host sends a command to the probe will it trigger a very short operation. The current consumption during operation is about 250μA/MIPS. This system is used to query the real-time dose rate and historical data detected by the probe and to set the parameters required by the probe. When the rays enter various types of detectors, electrical signals are generated. The electrical signals are converted into standard pulse frequency signals through signal adjustment circuits. The single-chip computer system in the probe counts the pulses within the set time, and then uses the corresponding algorithm to calculate the dose rate. The dose rate is transmitted to the host through the RS 485 bus, and finally the dose rate is displayed on the LCD display interface of the host.
2 Introduction to digital probe
Figure 1 is the structure of the digital probe. Digitizing the probe can be said to be a core content of this design. The internal microcontroller communicates with the microcontroller in the host through the RS 485 bus to complete the functions of modifying parameters and transmitting data.
The digital probe is composed of a detector, an amplifier circuit, a discrimination and shaping circuit, and an MSP430 single-chip computer; while the conventional analog probe is only composed of a detector, a preamplifier circuit, and a pulse shaping circuit. It can be seen that the digital probe has a higher degree of integration, is more intelligent, and is suitable for programming control. The digital probe used in this article can modify the following parameters through programming:
Measuring time: 0 to 60 s; number of measurements: 0 to 99 times; correction factor: 0.01 to 9.99; zero point: -20 to +20; high voltage: -1 000 to +500 V.
3 Hardware Circuit Design
There are two key issues in the design process: one is the high-voltage power supply problem of multiple digital probes. The solution is to use a D/A conversion module to connect with the microcontroller, provide a variable low voltage through software control, and then connect this low voltage to the high-voltage conversion module that can linearly amplify to power the probe; the other is the identification and data transmission problem of multiple probes. The solution is to number the probes and use RS 485 serial port connection between the digital probe and the microcontroller, connecting four wires in total, namely power line, ground line, A head, and B head. When the probe receives the transmission ID instruction, it transmits its unique number to the host. The host determines which probe it is and then transfers to the corresponding software processing program. After the data is measured, the dose rate is sent to the host by the dual-machine communication method of the first MSP430 and the second MSP430 microcontroller. The dotted box in Figure 1 is the digital probe part. The A to N types of detectors and signal processing circuits here do not mean that they are connected to the host at the same time, but that they can be replaced. The remaining modules include a 128×64 LCD display with a white background and very clear display; an external memory that can store real-time data and historical data; a clock chip that displays year, month, day, and time; an alarm circuit that buzzes when the dose rate is too high; and a 2×2 keyboard that controls instrument options and page changes. The hardware connection method is shown in Figure 1.
4 Probe and host communication protocol
The host uses RS 485 serial port to connect with the intelligent probe, using half-duplex communication, the baud rate is 9600 b/s, and the format of each frame is: 1 start bit, 8 data bits, 1 stop bit. The probe is set to send state when sending data to the instrument, and the rest of the time slots are set to receive state.
Probes that measure different rays have an ID number so that the instrument can identify different probes. In order to facilitate future expansion and use, the probe ID number consists of 5 bytes with a total of 40 bits. Among them, 0 to 15 bits indicate the year of the probe's development, with 0 to 7 bits representing the year in BCD code, and 8 to 15 bits representing the century; 16 to 23 bits indicate whether the data sent is counts or radiation exposure; 24 to 32 bits indicate the measurement range; 32 to 39 bits indicate the type of radiation measured. [page]
5 Software Design
The system software design is mainly divided into two parts: the host program and the probe program. The program is developed using C language on the IAR Embedded Workbench software platform. The host software flow chart and the probe software flow chart are shown in Figure 2 and Figure 3 respectively.
After the probe is connected to the host, first, the probe sends its own ID number to the host every 1 s until the host judges, identifies and makes a correct response to the ID number; then, it determines whether the probe parameters need to be modified. If necessary, the parameters are modified through the keyboard on the host. After the modification, the parameter modification instruction is sent to the probe; finally, a data transmission instruction is sent to the probe. After receiving the instruction, the probe processes the data according to the parameters sent by the host, calculates the dose rate and transmits it to the host. If the dose rate exceeds the alarm threshold, the host will sound an alarm.
6 Conclusion
After the instrument was developed, it has been used to measure the radiation dose in the air for a period of time. The whole machine has the advantages of stable operation, high sensitivity, and low power consumption. In addition, when conducting outdoor detection, the multi-probe system is designed, which makes the instrument easy to carry and can obtain the dose rate of different types of radiation at the same time, greatly improving the detection efficiency.
Previous article:Design of a certain type of pressure sensor tester
Next article:Design of Resolution Bandwidth of Digital IF Spectrum Analyzer
Recommended ReadingLatest update time:2024-11-16 19:52
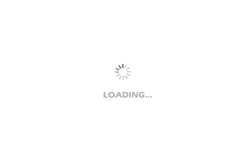
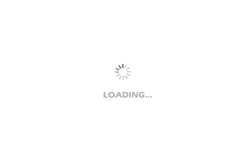
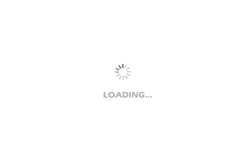
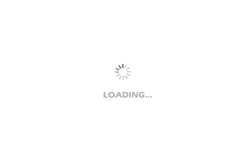
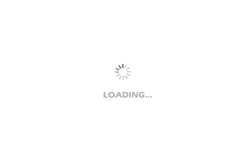
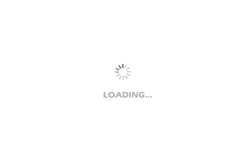
- Keysight Technologies Helps Samsung Electronics Successfully Validate FiRa® 2.0 Safe Distance Measurement Test Case
- From probes to power supplies, Tektronix is leading the way in comprehensive innovation in power electronics testing
- Seizing the Opportunities in the Chinese Application Market: NI's Challenges and Answers
- Tektronix Launches Breakthrough Power Measurement Tools to Accelerate Innovation as Global Electrification Accelerates
- Not all oscilloscopes are created equal: Why ADCs and low noise floor matter
- Enable TekHSI high-speed interface function to accelerate the remote transmission of waveform data
- How to measure the quality of soft start thyristor
- How to use a multimeter to judge whether a soft starter is good or bad
- What are the advantages and disadvantages of non-contact temperature sensors?
- Innolux's intelligent steer-by-wire solution makes cars smarter and safer
- 8051 MCU - Parity Check
- How to efficiently balance the sensitivity of tactile sensing interfaces
- What should I do if the servo motor shakes? What causes the servo motor to shake quickly?
- 【Brushless Motor】Analysis of three-phase BLDC motor and sharing of two popular development boards
- Midea Industrial Technology's subsidiaries Clou Electronics and Hekang New Energy jointly appeared at the Munich Battery Energy Storage Exhibition and Solar Energy Exhibition
- Guoxin Sichen | Application of ferroelectric memory PB85RS2MC in power battery management, with a capacity of 2M
- Analysis of common faults of frequency converter
- In a head-on competition with Qualcomm, what kind of cockpit products has Intel come up with?
- Dalian Rongke's all-vanadium liquid flow battery energy storage equipment industrialization project has entered the sprint stage before production
- Allegro MicroSystems Introduces Advanced Magnetic and Inductive Position Sensing Solutions at Electronica 2024
- Car key in the left hand, liveness detection radar in the right hand, UWB is imperative for cars!
- After a decade of rapid development, domestic CIS has entered the market
- Aegis Dagger Battery + Thor EM-i Super Hybrid, Geely New Energy has thrown out two "king bombs"
- A brief discussion on functional safety - fault, error, and failure
- In the smart car 2.0 cycle, these core industry chains are facing major opportunities!
- The United States and Japan are developing new batteries. CATL faces challenges? How should China's new energy battery industry respond?
- Murata launches high-precision 6-axis inertial sensor for automobiles
- Ford patents pre-charge alarm to help save costs and respond to emergencies
- New real-time microcontroller system from Texas Instruments enables smarter processing in automotive and industrial applications
- 【Recruitment】Shenzhen-Two-hour work-Basic MSP430 knowledge
- EEWORLD University Hall ---- Principles of Automatic Control Xie Hongwei National University of Defense Technology
- Over 200 CircuitPython Libraries
- Does anyone know a comparison table of shortwave antenna elevation height and propagation distance?
- "Goodbye 2019, Hello 2020" + a little bit more improvement
- I want an explanation of a bias circuit that is independent of power supply
- Share: Should the circuit board use grid copper or solid copper?
- Highlight Review丨What hard-core technologies did ADI showcase at IMS 2019? Come and find out~
- Google Protobuf 库
- EEWORLD University ---- Wildfire LwIP Application Development Practical Guide