Detailed explanation of the control algorithm of the electromechanical brake system (EMB) - Taking Tongyu Automobile and Feige Intelligent as examples
Latest update time:2024-11-04
Reads:
This article is about 6,000 words, it is recommended to save it for reading
Author
|
North Bay South Lane
Produced by
|
Automotive Electronics and Software
With the continuous advancement of technology, the automotive braking system is also quietly changing. The electronic mechanical braking system and its control method launched by Tongyu Automobile and Feige Intelligent Technology respectively provide reference value for solving the accuracy and reliability problems of the electronic mechanical braking system.
Tongyu Auto's electromechanical brake system is driven by an electric motor to achieve precise transmission and control of braking force, and its dual redundant design takes safety to a new level. On the other hand, Fige Intelligent Technology's brake control solution provides a deceleration method in the event of brake pedal failure, ensuring the safety of the vehicle in emergency situations. The application of these two technologies not only demonstrates the great potential of electronic brake systems in terms of accuracy, reliability and intelligence, but also heralds the continuous evolution of automotive braking technology towards a more efficient and safer direction. Next, we will analyze the core content of these technologies in detail and explore their impact on the future development of automotive braking systems.
#01
Tongyu Automobile-Electronic Mechanical Braking System and Control Method
Tongyu Automobile provides an electronic mechanical braking system (EMB) and its control method (application number 202411205388.9), which aims to solve the accuracy and reliability problems of traditional mechanical braking systems and improve the overall braking performance and safety of the vehicle. The following are the main knowledge points in the patent and a more in-depth analysis:
1.1 Technical Background
EMB uses an electric motor as the driving source of the braking force, and converts the power of the motor into braking force through a mechanical transmission mechanism to clamp the vehicle's brake disc or brake drum, thereby achieving the purpose of braking.
Compared with traditional hydraulic brake systems, EMB has higher response speed and more precise control capabilities, which can achieve more efficient energy recovery and more optimized braking performance.
With the continuous development of automobile electronics and intelligence, the electronic mechanical braking system has become a key component in advanced driver assistance systems (ADAS) and autonomous driving systems. Traditional braking systems have problems such as low accuracy in clamping force recognition and difficulty in monitoring friction lining wear. The clamping force sensors in existing EMB systems are expensive and face challenges in their placement. Completely eliminating the clamping force sensors will increase the difficulty of clamping force identification. This invention aims to solve such problems to improve the accuracy and reliability of electronic braking systems.
1.2 Purpose of the invention
The purpose of the patent invention is to design an electromechanical braking system with high-precision control, fast response and redundant safety functions, including the following goals:
-
Precise control of braking operation is achieved through modular design.
-
Monitor and identify friction lining wear conditions to extend system life.
-
Stiffness fitting and friction identification are used to achieve precise control of sensorless wheels and reduce hardware costs.
1.3 Components
The system consists of a control module and an execution module. The execution module includes a primary execution module and a secondary execution module, realizing a dual redundant design:

Electromechanical brake system control schematic diagram
-
Main execution module: including motor, force sensor and deceleration and torque increase mechanism, responsible for real-time measurement of clamping force and conversion motion.
-
Secondary execution module: responsible for calculating the estimated clamping force based on the clamping force information and algorithm of the primary execution module to provide redundant or auxiliary braking.
-
Control module: receives instructions and controls the motor rotation to achieve clamping or releasing operations.
Control Module:
Responsible for sending operating instructions to control the operation of the braking system. For example, the control module can send corresponding clamping or releasing instructions based on the driver's brake pedal signal or the vehicle's driving status information.
Controller:
It is connected to the motor position sensor, current sensor and force sensor, receives instructions from the control module, and controls the rotation of the motor according to the real-time information of these sensors.
By precisely controlling the motor's rotation angle and current, the controller is able to perform precise clamping or releasing operations.
The controller can adopt a variety of control strategies, such as PID control, fuzzy control, adaptive control, etc., to achieve the best braking performance.
Execution module:
Main execution module:
A force sensor is set up to obtain clamping force information through contact recognition. The force sensor can measure the clamping force of the brake on the brake disc or brake drum in real time and feed the information back to the controller.
It includes a motor and a deceleration and torque-increasing mechanism, a motion conversion mechanism, a motor position sensor and a current sensor.
The motor and the deceleration and torque-increasing mechanism provide the necessary clamping or releasing power, and the motion conversion mechanism converts the rotational motion into linear motion to achieve the braking operation.
Motor position sensors and current sensors provide real-time feedback, allowing the controller to precisely control the motor's rotation angle and current.
Secondary execution module:
The estimated clamping force is obtained through contact calculation to provide redundant or auxiliary braking. The secondary execution module can calculate and estimate the clamping force through a preset algorithm based on the clamping force data and/or other relevant parameters of the primary execution module.
1.4 Electromechanical Braking System Control Method
Control objectives:
Realize precise control of clamping force and effective monitoring of friction lining wear.
Avoid clamping force errors caused by friction lining wear, which affects braking performance and safety.
1.5 Specific implementation of control plan
Based on a single force sensor:
Determine whether the conditions for triggering contact calculation are met. If so, obtain vehicle parameter information, perform contact calculation and piston position calculation, then perform stiffness fitting and friction identification, and finally execute clamping/release instructions; if not, directly perform piston position calculation, stiffness fitting, friction identification and clamping/release instructions.
The method realizes effective control and monitoring of the wheel without force sensor through a single force sensor, reduces the cost and improves the reliability and safety of the braking system.
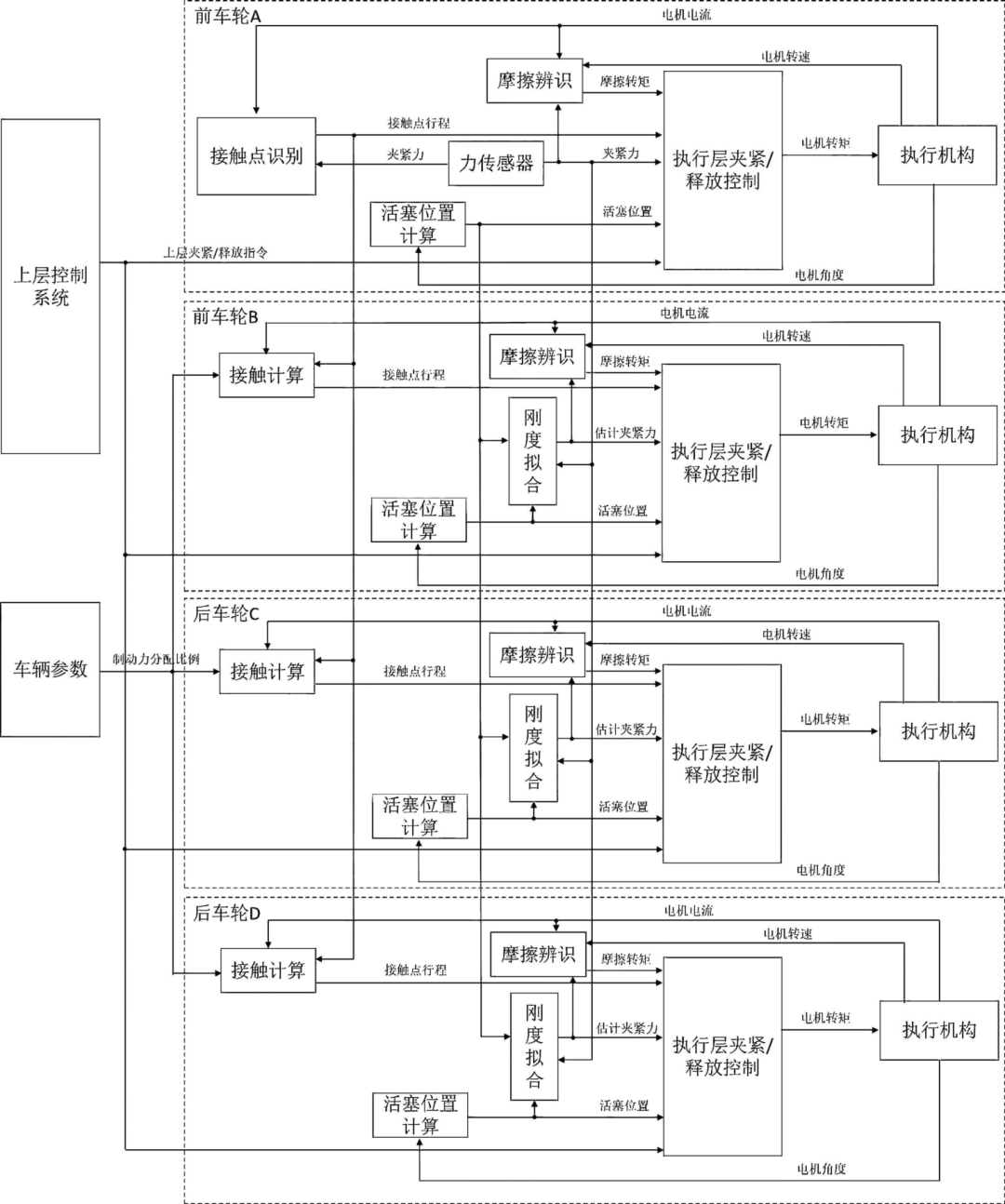
Flow chart of four-wheel overall clamping force control based on a single force sensor
This method combines vehicle parameters and motor status information to improve the accuracy of estimating the clamping force and provides strong support for the intelligent control of the vehicle braking system.
Based on two force sensors:
Similar to the single force sensor based control method, but with the addition of a force sensor that allows for a more accurate estimate of the clamping force.

Flow chart of the overall clamping force control of four wheels based on two force sensors
This method can further improve the performance and reliability of the braking system and better adapt to different vehicle parameters and driving conditions.
1.6 Key Technology Modules
-
Contact identification and contact calculation: Based on the change in motor current, the piston contact point stroke is updated to monitor the wear condition of the friction lining.
-
Stiffness fitting: The clamping force is estimated on the wheel without force sensor using the clamping force and piston position information of the wheel with force sensor.
-
Friction identification and compensation: Friction compensation is controlled by motor speed, motor current and estimated clamping force to improve system stability and accuracy.
1.7 Specific control methods
The control method of the system includes the steps of obtaining vehicle parameters, performing contact calculation, clamping force estimation and friction identification, and optimizing the braking operation through the following different control strategies:
Force sensor wheels:
The clamping force information is obtained through the force sensor, and the contact point stroke of the piston is updated to calculate the piston position.
Contact identification:
The change of clamping force and motor current obtained by the force sensor is used to update the contact point stroke of the piston, thereby determining the wear of the friction lining and achieving adaptive compensation of the friction lining.
Piston position calculation:
The motor angle is sensed in real time by the motor position sensor, and then integrated according to the actuator parameters to obtain the piston position.
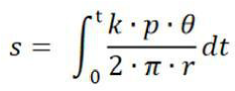
The solutions with force sensors are divided into:
-
Single force sensor control: A force sensor is installed on one wheel, and the clamping force estimation of other wheels is obtained through stiffness fitting to achieve full vehicle monitoring.
-
Dual force sensor control: Force sensors are installed on both wheels, and the control accuracy of the wheels without force sensors is further improved through stiffness fitting.

Flowchart of wheel clamping force control based on single or dual force sensors
No force sensor wheel:
Contact calculation is performed through vehicle parameters and motor current to obtain piston position information, and the clamping force is estimated through stiffness fitting.
Contact calculation:
Based on the contact point stroke obtained by the contact point identification module in the force sensor wheel, combined with the change of the motor current of the wheel actuator, the contact point stroke of the piston is updated to determine the wear condition of the friction lining and realize adaptive compensation of the friction lining.
Stiffness fitting:
The clamping force and piston position information of the wheel with a force sensor are received for stiffness fitting to obtain the functional relationship between the clamping force and the piston position. Then, based on the piston position information of the wheel without a force sensor, the estimated clamping force is calculated through the functional relationship.
Friction identification
:
Identifies friction compensation through motor current, motor speed and estimated clamping force and controls the required friction torque.
Friction compensation
:
By identifying and compensating for friction effects in real time, the deviation between the estimated clamping force and the actual clamping force can be reduced, improving braking accuracy.
Friction compensation helps eliminate brake fluctuations and judders caused by friction uncertainty, improving braking smoothness and stability.
Precise friction control and compensation reduces wear and risk of damage to brake components, thereby extending the service life of the entire brake system.

1.8 Advantages
Precise control
:
By optimizing the sensor layout and clamping force identification method, precise control of clamping force and effective monitoring of friction lining wear can be achieved.
Improve performance and reliability:
The dual design of the main execution module and the secondary execution module improves the accuracy and reliability of the braking system.
Reduce costs:
Force sensors are only set on some wheels, reducing system complexity and cost.
Enhanced safety:
Precisely controlling the clamping force of each wheel achieves a reasonable distribution of the vehicle's braking force, improving the vehicle's overall braking performance and safety.
1.9 Application Prospects
The electronic mechanical braking system and control method thereof can be applied to various vehicles, including cars, trucks, motorcycles, etc., to improve the overall braking performance and safety of the vehicles.
With the development of automobile electronics and intelligence, the EMB system will gradually become an important development direction of future automobile braking systems.
1.10 Future Development Direction
Further optimize control algorithms:
Develop more advanced control algorithms, such as those based on artificial intelligence, to further improve the performance and reliability of the braking system.
Integrate more sensors:
For example, integrate wheel speed sensors, acceleration sensors, etc. to obtain more comprehensive vehicle status information and further improve the control accuracy of the braking system.
Develop more advanced friction models:
Build more precise friction models to more accurately describe the friction characteristics between the friction lining and the brake disc, and further improve the control accuracy of the brake system.
Summarize:
Tongyu Automobile provides an advanced electro-mechanical braking system and its control method, which has the advantages of precise control, high reliability, low cost and enhanced safety, and has broad application prospects.
#02
Feige Intelligent Technology_A braking control method, device and storage medium
Fige Intelligent Technology provides a brake control solution for the electromechanical brake system (EMB) (application number 202411160648.5), which aims to solve the problem of vehicle deceleration when the brake pedal fails and improve the safety of the vehicle when the brake pedal fails. The following is a detailed analysis of the solution:
2.1 Technical Background

*Schematic diagram of the structure of the electromechanical system
-
EMB uses electric drive components as brake actuators, generates braking torque through brushless DC motors, and applies braking force to the brake disc. Each wheel is equipped with an independent braking mechanism, and the central control module is responsible for analyzing the braking requirements of each wheel and outputting corresponding control signals.
-
Components: EMB mainly includes brake actuator, motor, control module, brake housing, brake pad, pedal simulator, power supply, etc.
-
Advantages: Compared with traditional hydraulic or pneumatic brakes, EMB has the advantages of small size, fast response, reliable performance, safety and environmental protection. The brushless motor in the EMB system generates braking torque, does not require brake fluid, and avoids the "brake foot" phenomenon.
-
In order to maintain the user's operating habits of traditional brakes, a pedal simulator can be introduced to feed back pedal displacement information to the control unit.

2.2 Program Content
This method enables redundant braking mode
when the brake pedal fails
, and controls the vehicle to decelerate through the accelerator pedal to ensure safety. It specifically includes the following steps:
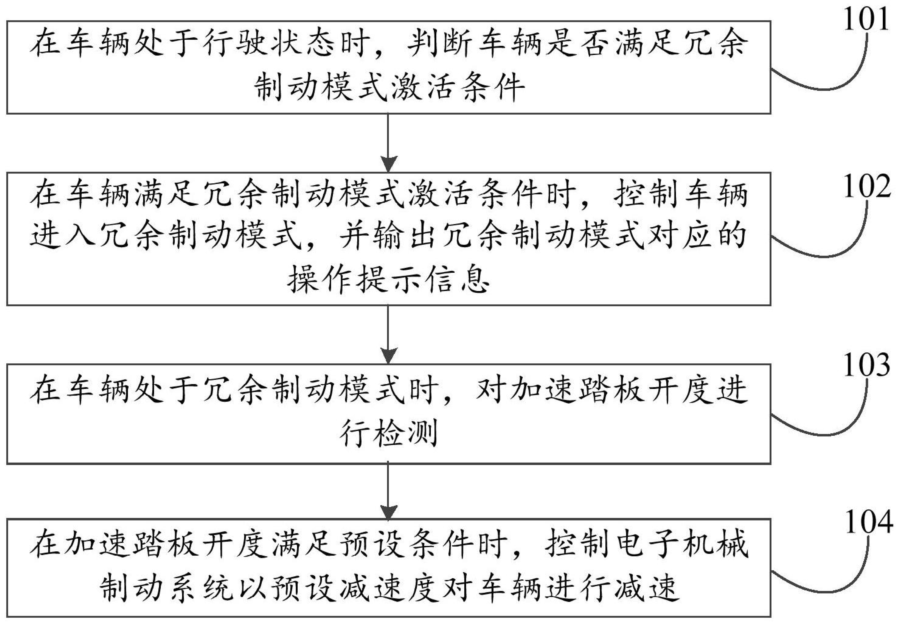
* Flowchart of the braking control method
-
Activation condition judgment: When the vehicle is in driving state and the conditions are met, the system enters redundant braking mode.
-
Operation prompt information : When entering the redundant braking mode, the corresponding prompt information is output so that the driver can understand how to operate.
-
Accelerator pedal detection : In redundant mode, the accelerator pedal opening is used to determine whether the driver needs to decelerate.
-
Electromechanical brake : When the accelerator pedal meets the preset conditions, the vehicle decelerates at the set deceleration rate.
2.3 Braking control devices and equipment
-
Braking control device: includes a judgment module, a first control module, a first detection module and a second control module, etc., which are used to implement various steps of the braking control method.
-
Electronic device and storage medium: describes the structure of an electronic device including a processor, a memory and a communication interface, and a computer-readable storage medium storing a computer program for implementing a braking control method.
Brake control device
The brake control module includes multiple control modules and detection modules, which are used to monitor the vehicle's driving status, accelerator pedal opening, brake pedal failure, etc., and perform redundant brake control when necessary.

*Schematic diagram of the brake control device
-
The judgment module is used to determine whether the vehicle meets the redundant braking mode activation conditions: detect whether the brake pedal is faulty, and determine whether to activate the redundant braking mode based on preset conditions.
-
The first control module is used to control the vehicle to enter a redundant braking mode and output operation prompt information.
-
The first detection module is used to detect the accelerator pedal opening.
-
The second control module is used to control the electronic mechanical brake system to decelerate when the accelerator pedal opening meets a preset condition.
Electronic devices and storage media
Electronic device:
The device includes a processor, a memory, etc., and stores a computer program for executing the above-mentioned braking control method.
Computer-readable storage medium:
The medium stores a computer program for executing the above-mentioned braking control method.

*Block diagram of electronic equipment
The system components include:
processor 610, communication interface 620, memory 630 and communication bus 640. These components implement data exchange and communication through communication bus 640. Processor 610 can access the instruction set in memory 630, which mainly performs the following functions:
-
When the vehicle is in motion, monitoring whether the vehicle meets the conditions for activating the redundant braking mode;
-
When the vehicle meets the conditions for activating the redundant braking mode, the vehicle enters the redundant braking mode and displays corresponding operation prompt information;
-
When the vehicle is in redundant braking mode, real-time monitoring of the accelerator pedal opening;
-
When the accelerator pedal opening reaches the preset standard, the electronic mechanical braking system is controlled to decelerate the vehicle according to the preset deceleration rate.
Optional modules
Double flash control module:
When the vehicle enters the redundant braking mode, the double flash warning lights are turned on to improve driving safety.
2.4 Redundant Braking Mode
Purpose:
As a backup braking method when the brake pedal fails, to ensure that the vehicle can be safely decelerated in an emergency.
Activation method:
It can be activated manually or automatically. Manual activation can be achieved by pressing the electronic parking brake (EPB) switch; automatic activation determines whether to enter redundant braking mode by detecting brake pedal travel and deceleration.
Operation prompts:
When the vehicle enters redundant braking mode, operation prompt information will be output through devices such as the on-board display or speakers to guide the driver to perform braking operations.
2.5 Specific Implementation Methods
-
Activate Redundant Braking Mode: When a brake pedal failure is detected, or the driver manually activates the Redundant Mode. Manual activation includes pressing the Electronic Parking Brake (EPB switch).
-
Operation prompts : After the redundant mode is activated, prompt information is provided through the vehicle-mounted equipment (such as display screen, speakers) to guide the driver to operate correctly.
-
Accelerator pedal opening detection : After entering redundant mode, the accelerator pedal opening is monitored, and the system will perform deceleration control when the conditions are met.
-
Vehicle speed and torque management : If the accelerator pedal opening does not meet the deceleration conditions, the system controls the torque output of the drive motor according to the vehicle speed. At high speeds (such as over 50 km/h ), the power output is maintained; at low speeds, the torque output is reduced.
-
Mode exit : The driver can exit the redundant mode through a physical or soft button and restore the normal control function of the vehicle.
-
When entering redundant mode, the hazard lights will automatically turn on to alert other vehicles .

* Flowchart of the brake control method
2.6 Braking control method steps
-
Judgment conditions: When the vehicle is in motion, determine whether the redundant braking mode activation conditions are met, such as brake pedal failure.
-
Entry mode: When the conditions are met, the vehicle is controlled to enter redundant braking mode and operation prompt information is output.
-
Detect pedal: In redundant braking mode, detect the accelerator pedal opening to determine whether the driver intends to decelerate.
-
Deceleration control: When the accelerator pedal opening meets the preset conditions, the electronic mechanical brake system is controlled to decelerate the vehicle at a preset deceleration.
-
Accelerator pedal control:
-
When the vehicle speed exceeds the preset speed threshold (for example, 50km/h), it means that the vehicle is in a high-speed driving state. At this time, the system will instruct the drive motor to output the first torque that matches the accelerator pedal opening to ensure the normal operation of the vehicle power system.
-
When the vehicle speed is equal to or lower than the preset speed threshold, it indicates that the vehicle speed is slow. In this case, the system will adjust the drive motor to output a lower second torque, which is less than the first torque. The purpose of this adjustment is to moderately limit the torque output of the drive motor when the vehicle speed is low, so as to remind the driver that there may be an abnormality in the vehicle braking system, while ensuring that the driver can continue to drive the vehicle smoothly.
During the implementation process, if it is detected that the opening of the accelerator pedal does not meet the preset conditions, this indicates that the driver does not intend to apply the brakes. In other words, under the current driving environment, the vehicle does not meet the deceleration requirements. For example, when the vehicle is driving on a highway or a city expressway, for the sake of driving safety, the vehicle should not be decelerated directly, but the driver should be guided to continue driving to an appropriate location before decelerating and stopping. Therefore, when the opening of the accelerator pedal does not meet the preset conditions, the system will calculate the first torque value corresponding to the current opening of the accelerator pedal and monitor the speed of the vehicle in real time.
2.7 Technical Effects
-
Improve safety: Ensure that the vehicle can still decelerate safely in the event of brake pedal failure to avoid traffic accidents.
-
Easy to operate: The driver can brake the vehicle by controlling the accelerator pedal. The operation is simple and easy to learn.
-
Cost-effective: No need to add redundant brake devices, reducing costs.
-
Improve driving experience: When the vehicle enters redundant braking mode, operation prompt information will be output to facilitate the driver's operation.
Fige Intelligent Technology provides an innovative and practical braking control solution, which effectively solves the problem of brake pedal failure in the electronic mechanical braking system, improves driving safety, and has good economic benefits. It realizes additional brake redundancy protection through vehicle signal interaction, without adding hardware, and realizes safety protection in the case of brake pedal failure. This solution provides new ideas for the application of electronic mechanical braking systems and has important research value and application prospects.
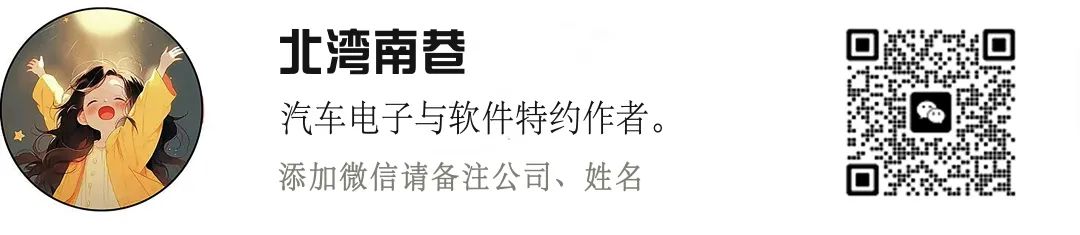
/END/