Three additional circuits for relays
Source: InternetPublisher:jikai233 Updated: 2014/04/16
Relay is a commonly used component in electronic circuits. In electronic switch drive circuits that are generally composed of transistors, relays and other components, some additional circuits are often added to change the working characteristics of the relay or provide protection. The additional circuits of relays mainly have the following three forms:
1. Relay series RC circuit: The circuit form is shown in Figure 1. This form is mainly used in circuits where the rated operating voltage of the relay is lower than the power supply voltage. When the circuit is closed, the relay coil will generate electromotive force due to the self-induction phenomenon, which hinders the increase of current in the coil, thus prolonging the pull-in time. After connecting the RC circuit in series, the pull-in time can be shortened. The principle is that at the moment the circuit is closed, the voltage across the capacitor C cannot change suddenly and can be regarded as a short circuit. In this way, a power supply voltage higher than the rated operating voltage of the relay coil is added to the coil, thereby accelerating the increase in current in the coil and making the relay Quickly absorbs. After the power supply is stable, the capacitor C has no effect, and the resistor R acts as a current limiting function. 2. Relay parallel RC circuit: The circuit form is shown in Figure 2. After the circuit is closed, the RC circuit does not work when the current is stable. When the circuit is opened, the relay coil generates an induced electromotive force due to self-induction, and is discharged through the RC circuit, causing the coil to The current decay slows down, thereby prolonging the relay armature release time and acting as a delay. 3. Relay parallel diode circuit: The circuit form is shown in Figure 3, mainly to protect driving components such as transistors. When the transistor VT in the figure changes from on to off, the current flowing through the relay coil will decrease rapidly. At this time, the coil will generate a high self-induced electromotive force which is superimposed with the power supply voltage and added between the c and e poles of VT. It will cause the transistor to break down. After connecting the diode in parallel, the self-induced electromotive force of the coil can be clamped to the forward conduction voltage of the diode. This value is about 0.7V for silicon tubes and about 0.2V for germanium tubes, thereby avoiding breakdown of driving elements such as transistors. device. When connecting diodes in parallel, be sure to note that the polarity of the diode cannot be reversed, otherwise it will easily damage drive components such as transistors.
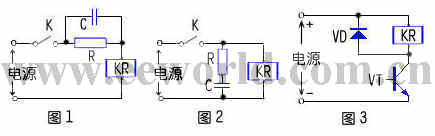
Latest Control Circuits Circuits
- Analysis of the working principle of car garage door lights
- Tutorial on making your own remote-controlled robotic arm
- How to set up a cheap beam break sensor control distance scene using a reflector
- A small improvement on the ordinary refrigerator motor starting circuit
- Star-delta step-down starting control circuit for squirrel cage asynchronous motor
- Motor control circuit for starting and running without phase loss
- IGBT modules block overcurrent by controlling the gate
- Night dog barking anti-theft reminder circuit
- Precious home appliance anti-theft alarm
- Car audio system anti-theft circuit
Popular Circuits
- Homemade disinfectant circuit
- Multi-channel patrol detection control circuit a
- Assembly line outage monitoring circuit
- Haier KFR-25GW air conditioner control circuit schematic diagram
- Galanz rice cooker control circuit
- Range hood detection control circuit
- Small power electric heater temperature detection control circuit
- Electric heater temperature detection control circuit
- Voltage servo motor and control circuit
- Wide input range non-synchronous voltage mode control circuit