introduction
With the development of power electronics technology, new permanent magnet materials and DSP (digital signal processor) with fast computing capability, the application of brushless DC motors is becoming more and more popular. Brushless DC motors have excellent speed regulation performance similar to DC motors, and overcome the shortcomings of commutation sparks and low reliability caused by the mechanical commutation device of DC motors. They have the advantages of small size, light weight, high efficiency, and flexible shape and size of the motor. Therefore, they are widely used in servo systems, CNC machine tools, electric vehicles and household appliances, and have become the main direction of modern servo technology.
Introduction to DSP
DSP (Digital Signal Processing) is digital signal processing technology, and DSP chip refers to the chip that can realize digital signal processing technology. The DSP chip adopts Harvard structure with separate program and data, has a special hardware multiplier, widely adopts pipeline operation, and provides special DSP instructions, which can be used to quickly implement various digital signal processing algorithms. In today's digital era, DSP has become a basic device in the fields of communications, computers, consumer electronics, etc.
The birth of DSP chips is a necessity of the times. Since the 1960s, with the rapid development of computers and information technology, digital signal processing technology has emerged and developed rapidly. Before the emergence of DSP chips, digital signal processing could only be completed by microprocessors. However, due to the low processing speed of microprocessors, they could not meet the high-speed real-time requirements of increasing amounts of information. Therefore, the application of faster and more efficient signal processing methods has become an increasingly urgent social need.
Application Cases
Spark Automation uses the industrial-grade high-reliability and high-performance HXS320F28027PTT chip as the main control chip, and uses a unique control algorithm to achieve a low-voltage DC brushless driver. It is suitable for low-voltage DC brushless motors with a power of less than 500W. The product has a stable speed, strong resistance to load fluctuations, high output, integrated overvoltage, undervoltage, overcurrent, stall and other protection methods, and has the characteristics of small size, low heat generation, high reliability, long life, and easy use. It is suitable for various industries such as industrial robots, lathe equipment, and medical treatment.
Zhongke Haoxin BLDC brushless DC motor solution
Advantages of brushless DC motor solution application:
Wide speed regulation range, capable of high-speed operation;
Good load regulation performance and small speed fluctuation;
The limit torque is large and can meet the requirements of heavy load applications.
About HXS320F28027PTT chip
Previous article:VPLC Series Machine Vision Motion Control All-in-One Quick Start (Part 1)
Next article:Understanding of torque motor controller
Recommended ReadingLatest update time:2024-11-21 20:11
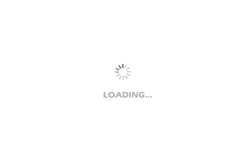
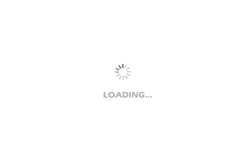
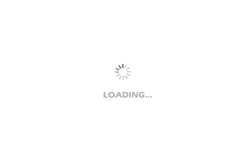
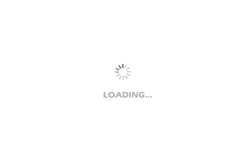
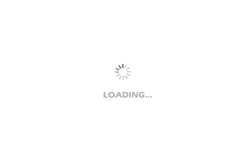
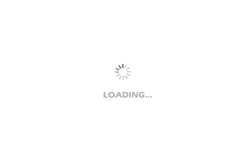
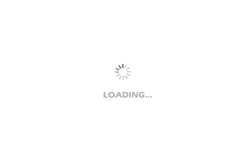
- Why is the vehicle operating system (Vehicle OS) becoming more and more important?
- Car Sensors - A detailed explanation of LiDAR
- Simple differences between automotive (ultrasonic, millimeter wave, laser) radars
- Comprehensive knowledge about automobile circuits
- Introduction of domestic automotive-grade bipolar latch Hall chip CHA44X
- Infineon Technologies and Magneti Marelli to Drive Regional Control Unit Innovation with AURIX™ TC4x MCU Family
- Power of E-band millimeter-wave radar
- Hardware design of power supply system for automobile controller
- Driving Automation Safety and Economic Engineering
Professor at Beihang University, dedicated to promoting microcontrollers and embedded systems for over 20 years.
- Intel promotes AI with multi-dimensional efforts in technology, application, and ecology
- ChinaJoy Qualcomm Snapdragon Theme Pavilion takes you to experience the new changes in digital entertainment in the 5G era
- Infineon's latest generation IGBT technology platform enables precise control of speed and position
- Two test methods for LED lighting life
- Don't Let Lightning Induced Surges Scare You
- Application of brushless motor controller ML4425/4426
- Easy identification of LED power supply quality
- World's first integrated photovoltaic solar system completed in Israel
- Sliding window mean filter for avr microcontroller AD conversion
- What does call mean in the detailed explanation of ABB robot programming instructions?
- Breaking through the intelligent competition, Changan Automobile opens the "God's perspective"
- The world's first fully digital chassis, looking forward to the debut of the U7 PHEV and EV versions
- Design of automotive LIN communication simulator based on Renesas MCU
- When will solid-state batteries become popular?
- Adding solid-state batteries, CATL wants to continue to be the "King of Ning"
- The agency predicts that my country's public electric vehicle charging piles will reach 3.6 million this year, accounting for nearly 70% of the world
- U.S. senators urge NHTSA to issue new vehicle safety rules
- Giants step up investment, accelerating the application of solid-state batteries
- Guangzhou Auto Show: End-to-end competition accelerates, autonomous driving fully impacts luxury...
- Lotus launches ultra-900V hybrid technology "Luyao" to accelerate the "Win26" plan
- We have been hit by a power outage this week.
- Monthly Original Selection July 2018 (Issue 6)
- [ESP32-S2-Kaluga-1 Review] 4. Add an interactive GUI?
- Baby growth "little partner"
- 【Practical】Eliminating EMI in Buck Converters (3)
- Looking for a DCDC chip
- Optocoupler device selection
- N32G430 lighting review
- The live broadcast entrance is now open! Award-winning live broadcast [TI C2000 signal chain real-time evaluation and usage tutorial]
- DMA serial port output