01
Space Vector SVPWM Control
Space vector SVPWM control technology is widely used in frequency converters. When driving an AC motor, the motor's magnetic flux becomes a circular rotating magnetic field, thereby allowing the motor to generate a constant electromagnetic torque.
Three-phase voltage type bridge inverter circuit
Using 180° conduction mode, there are 8 working states, namely V6, V1, V2, V1, V2, V3, V2, V3, V4, V3, V4, V5, V4, V5, V6, V5, V6, V1, and V1, V3, V5 and V2, V4, V6. "1" indicates that the upper bridge arm switch of each phase is turned on, and "0" indicates that the lower bridge arm switch is turned on. The above 8 working states can be represented as 100, 110, 010, 011, 001, 101, 111 and 000 respectively. The first 6 states have output voltage, which is an effective working state, while the last two states are all upper tubes or lower tubes, without output voltage, which is called zero working state. Therefore, this basic inverter is called a 6-beat inverter.
For a 6-beat inverter, in each working cycle, the six effective working states appear once each, and each state lasts for 60°. In one cycle, the six voltage vectors rotate 360° in total, forming a closed regular hexagon.
Voltage Space Vector Hexagon
The two "zero working states" of 111 and 000 are represented here as the zero vector at the origin, which is located at the center of the regular hexagon. By using PWM control, the magnetic flux of the AC motor can be made as close to a circle as possible. The higher the working frequency, the closer the magnetic flux is to a circle. When the required voltage vector is not the 6 basic voltage vectors, it can be achieved by a combination of two basic vectors and the zero vector.
Linear combination of space voltage vectors
The required vector is us, which is realized by a linear combination of basic vectors u1 and u2. The action time of u1 and u2 is generally less than 60° of the switching period To, and the insufficient time can be filled with a "zero vector".
Three-phase PWM modulation mode in sector I
02
Multiplexing of PWM Inverter Circuits
The purpose of multiplexing is to increase the equivalent switching frequency, reduce switching losses, and reduce the harmonic components related to the carrier. The multiplexing connection methods of PWM inverter circuits include transformer method and reactor method.
Reactor-connected dual PWM inverter circuit
The output of the circuit is drawn from the center tap of the reactor. The carrier signals of the two unit inverter circuits are staggered 180° from each other. The voltage uUN'=(uU1N'+uU2N')/2 at the output end relative to the midpoint N' of the DC power supply has become a unipolar PWM wave. The output line voltage has five levels: 0, (±1/2)Ud, and ±Ud, which is less than the harmonics when it is not multiplexed. The higher the frequency of the applied voltage, the smaller the inductance required for the reactor.
Output waveform of double PWM inverter circuit
After duplication, the angular frequency of the harmonics contained in the output voltage can still be expressed as nωc + kωr, but the harmonics when n is an odd number have been completely removed, and the lowest frequency of the harmonics is around 2ωc, which is equivalent to doubling the equivalent carrier frequency of the circuit.
03
PWM tracking control technology
**Tracking control method: **Take the desired output current or voltage waveform as the command signal, and the actual current or voltage waveform as the feedback signal. By comparing the instantaneous values of the two, the on and off of each power switch device in the inverter circuit is determined, so that the actual output tracks the changes in the command signal.
Hysteresis comparison method
This type of current tracking control is widely used.
①PWM current tracking control single-phase half-bridge inverter circuit
The deviation i -i between the command current i and the actual output current i is used as the input of a comparator with hysteresis characteristics, and its output is used to control the on and off of power devices V1 and V2.
Hysteresis comparison method command current and output current
When V1 (or VD1) is turned on, i increases; when V2 (or VD2) is turned on, i decreases. Through the control of the hysteresis comparator with a loop width of 2ΔI, i tracks the command current i* in a sawtooth shape within the range of i*+ΔI and i*-ΔI. When the loop width is too wide, the switching frequency is low and the tracking error is large; when the loop width is too narrow, the tracking error is small, but the switching frequency is too high and the switching loss increases. When L is large, the change rate of i is small and the tracking is slow; when L is small, the change rate of i is large and the switching frequency is too high.
②Three-phase current tracking PWM inverter circuit
It consists of three single-phase half-bridge circuits, and the three-phase current command signals iU, iV and i*W are 120° apart. In the positive and negative half cycles of the line voltage, there are pulses with opposite polarities output, which will increase the harmonic components in the output voltage and also increase the harmonic loss of the load.
The current tracking PWM converter circuit using hysteresis comparison has the following characteristics:
⑴The hardware circuit is simple;
⑵ Real-time control, fast current response.
⑶ No carrier is used, and the output voltage waveform does not contain harmonics of specific frequencies.
⑷ Compared with the calculation method and the modulation method, the output current contains more high-order harmonics at the same switching frequency.
⑸ It belongs to closed-loop control and is a common feature of various tracking PWM conversion circuits.
Voltage tracking control:
The command voltage u* is compared with the output voltage u, and the harmonics in the deviation signal are filtered out. The output of the filter is sent to the hysteresis comparator, and the comparator output controls the on and off of the switching device, thereby realizing voltage tracking control. The output voltage PWM waveform contains a large number of high-order harmonics, which must be filtered out with an appropriate filter.
When u*=0, the output voltage u is a high-frequency rectangular wave, which is equivalent to a self-excited oscillation circuit. When u is a DC signal, u generates a DC offset and becomes a rectangular wave with unequal positive and negative pulse widths, positive wide and negative narrow or positive narrow and negative wide. When u is an AC signal, as long as its frequency is much lower than the above self-excited oscillation frequency, after filtering out the high-order harmonics generated by the switching of the device from u, the resulting waveform is almost the same as u*, thereby realizing voltage tracking control.
Triangle wave comparison method
Triangular wave comparison method current tracking inverter circuit
Compare the command currents iU, iV and i*W with the actual output currents iU, iV, iW of the inverter circuit to obtain the deviation current, amplify it through amplifier A (amplifier A usually has proportional-integral characteristics or proportional characteristics, and its coefficient directly affects the current tracking characteristics of the inverter circuit), and then compare it with the triangle wave to generate a PWM waveform.
Features:
⑴The switching frequency is fixed and equal to the carrier frequency, making the high-frequency filter easy to design.
⑵ In order to improve the output voltage waveform, a three-phase triangular wave carrier is often used as the triangular wave carrier.
⑶ Compared with the hysteresis comparison control method, this control method contains fewer harmonics in the output current.
Timing comparison method
This method does not use a hysteresis comparator, but sets a fixed clock to sample the command signal and the controlled variable at a fixed sampling period, and controls the on and off of the switching device of the converter circuit according to the polarity of the deviation between the two, so that the controlled variable tracks the command signal.
Let's take a single-phase half-bridge inverter circuit as an example. At the sampling moment when the clock signal arrives
If
If i>i*, V1 is turned off and V2 is turned on, causing i to decrease.
The control action at each sampling moment reduces the error between the actual current and the command current. When the timing comparison method is used, the maximum switching frequency of the device is 1/2 of the clock frequency. Compared with the hysteresis comparison method, the current control error does not have a certain loop width, and the control accuracy is lower.
Previous article:Why use SVPWM to control the motor? Summary of SVPWM with Hall sensor
Next article:SVPWM-Overmodulation Introduction
Recommended ReadingLatest update time:2024-11-15 17:33
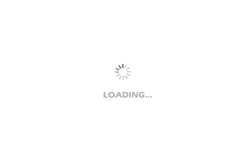
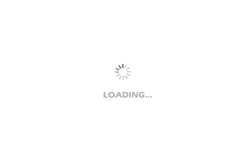
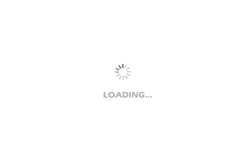
- Popular Resources
- Popular amplifiers
-
西门子S7-12001500 PLC SCL语言编程从入门到精通 (北岛李工)
-
Small AC Servo Motor Control Circuit Design (by Masaru Ishijima; translated by Xue Liang and Zhu Jianjun, by Masaru Ishijima, Xue Liang, and Zhu Jianjun)
-
Intelligent Control Technology of Permanent Magnet Synchronous Motor (Written by Wang Jun)
-
100 Examples of Microcontroller C Language Applications (with CD-ROM, 3rd Edition) (Wang Huiliang, Wang Dongfeng, Dong Guanqiang)
- Huawei's Strategic Department Director Gai Gang: The cumulative installed base of open source Euler operating system exceeds 10 million sets
- Analysis of the application of several common contact parts in high-voltage connectors of new energy vehicles
- Wiring harness durability test and contact voltage drop test method
- Sn-doped CuO nanostructure-based ethanol gas sensor for real-time drunk driving detection in vehicles
- Design considerations for automotive battery wiring harness
- Do you know all the various motors commonly used in automotive electronics?
- What are the functions of the Internet of Vehicles? What are the uses and benefits of the Internet of Vehicles?
- Power Inverter - A critical safety system for electric vehicles
- Analysis of the information security mechanism of AUTOSAR, the automotive embedded software framework
Professor at Beihang University, dedicated to promoting microcontrollers and embedded systems for over 20 years.
- LED chemical incompatibility test to see which chemicals LEDs can be used with
- Application of ARM9 hardware coprocessor on WinCE embedded motherboard
- What are the key points for selecting rotor flowmeter?
- LM317 high power charger circuit
- A brief analysis of Embest's application and development of embedded medical devices
- Single-phase RC protection circuit
- stm32 PVD programmable voltage monitor
- Introduction and measurement of edge trigger and level trigger of 51 single chip microcomputer
- Improved design of Linux system software shell protection technology
- What to do if the ABB robot protection device stops
- Keysight Technologies Helps Samsung Electronics Successfully Validate FiRa® 2.0 Safe Distance Measurement Test Case
- Innovation is not limited to Meizhi, Welling will appear at the 2024 China Home Appliance Technology Conference
- Innovation is not limited to Meizhi, Welling will appear at the 2024 China Home Appliance Technology Conference
- Huawei's Strategic Department Director Gai Gang: The cumulative installed base of open source Euler operating system exceeds 10 million sets
- Download from the Internet--ARM Getting Started Notes
- Learn ARM development(22)
- Learn ARM development(21)
- Learn ARM development(20)
- Learn ARM development(19)
- Learn ARM development(14)
- [Raspberry Pi 3B+ Review] Thread Suspension and Resumption & CPU Temperature Detection
- I am a beginner and I need answers to two questions.
- [Operation Tutorial] Practical operation of ATX-100 series wire harness tester!
- MSP430 low power event driven working mode
- How to achieve communication between heterogeneous processors - Mir takes you to play with the i.MX 8M Plus development board
- How to select switching power supply topology-Video sharing
- 【AT32F421 Review】+ Introduction and Development Environment Construction
- How to make an embedded device enumerate as a WinUSB device
- All the TWS wireless Bluetooth headset designs you want are here!
- [Share] Overview of debugging methods for ARM development