Power semiconductor devices play an important role in modern power control and drive systems. IGBT modules and IPM modules are two of the most common types of devices. They can both be used to control high-power loads and drive motors, but their internal structures and functions are different. So what do IPM and IGBT modules mean? Let's take a closer look at the differences between them.
1. What does IPM module mean?
IPM (Intelligent Power Module) is a powerful integrated circuit module that can be used to control and drive high-power electronic devices such as AC motor drives, frequency converters, inverters, etc. It is a highly integrated semiconductor device that usually includes multiple functional modules such as power switches, drive circuits, protection circuits, and control circuits.
IPM modules usually include a switching device such as a power MOSFET, IGBT (insulated gate bipolar transistor) or SiC (silicon carbide), and a drive circuit to control the on and off of these switching devices. In addition, IPM modules usually integrate power circuits, current and voltage sensors, over-temperature protection and short-circuit protection, etc., which can provide comprehensive protection measures to ensure the safety and reliability of high-power electronic equipment.
2. What does IGBT module mean?
IGBT module (Insulated Gate Bipolar Transistor Module) is a modular electronic component that integrates multiple IGBT chips, drive circuits, protection circuits, etc. It is a semiconductor device used in high-power power electronic equipment, commonly used in high-voltage, high-current AC/DC converters, inverters and DC/DC converters.
IGBT is a semiconductor device that combines the characteristics of MOSFET and BJT. It has the advantages of low on-resistance and high switching speed, and also has the characteristics of high voltage tolerance and strong current carrying capacity of BJT devices. Therefore, IGBT devices are widely used in high-power, high-frequency power electronic equipment. IGBT modules are usually composed of multiple IGBT chips, drive circuits, protection circuits, heat sinks, connectors, etc. Through the internal insulation isolation structure, the IGBT chip is isolated from the outside world to prevent external interference and electromagnetic interference. At the same time, the drive circuit and protection circuit inside the module can effectively control and protect the IGBT chip, improving the reliability and safety of the equipment.
3. What is the difference between IGBT module and IPM module?
IGBT modules and IPM modules are both power electronic devices, but they have the following differences:
1. Different integration levels: The IGBT module only contains one IGBT transistor and one drive circuit, while the IPM module integrates multiple devices and circuit modules and has a higher level of integration.
2. Different functions: IGBT module can only realize a single power switch function, while IPM module integrates multiple functional modules, such as power circuit, current and voltage sensors, over-temperature protection and short-circuit protection, etc., and can provide comprehensive protection and control functions.
3. Different application scopes: IGBT modules are usually used in situations where a single power switch is controlled, such as AC motor drives, frequency converters, inverters, etc.; while IPM modules are usually used in situations where multiple power switches are controlled, such as motor drives, UPS, power converters, etc.
4. Different reliability: The IPM module has higher reliability because it integrates multiple protection and control modules, which can fully protect the system from abnormal conditions such as overvoltage, overcurrent, overtemperature, etc.
5. Different costs: IPM modules have higher costs due to their higher integration and more comprehensive functions, while IGBT modules are relatively simple and have relatively lower costs.
In general, the IPM module is a more advanced power electronic device, which has higher integration, more functions and higher reliability than the IGBT module, and is suitable for more complex and advanced power control systems. The IGBT module is simpler and more economical, and is suitable for single power switch control occasions.
Why Silicon Carbide
Is it the future of automotive power modules?
The bandgap width of silicon carbide is about 3 times that of silicon-based materials, the critical breakdown field strength is about 10 times that of silicon-based materials, the thermal conductivity is about 3 times that of silicon-based materials, and the electron saturation drift rate is about 2 times that of silicon-based materials. Compared with silicon-based devices, the high-voltage, high-temperature, and high-frequency characteristics of silicon carbide materials can be applied to more severe working conditions, which can significantly improve efficiency and power density, and reduce the cost, volume, and weight of the application end.
Figure 1 Comparison of performance of various semiconductor materials
According to Yole data, from 2021 to 2027, the global silicon carbide power device market size will grow from US$1.09 billion to US$6.297 billion, with a compound annual growth rate of 34%; among them, the market size of silicon carbide for electric vehicles will grow from US$685 million to US$4.986 billion, with an annual compound growth rate of 39.2%. Electric vehicles (inverter + OBC + DC/DC converter) are the largest downstream application of silicon carbide, and its share will increase from 62.8% to 79.2%, and its market share will continue to rise.
Figure 2. Yole’s market analysis
Application Trends of Silicon Carbide in the Automotive Industry
Since the development of the electric vehicle industry, the industry is most concerned about the driving range. There are many factors that affect the driving range, including battery capacity, vehicle weight, and the power conversion efficiency of the power system. Power semiconductors are the core of power conversion. Silicon carbide power devices have advantages over silicon-based devices such as low conduction loss, high switching frequency, and high working voltage resistance. They can achieve higher system power conversion efficiency, and under the same power consumption, they can achieve more driving range than using silicon-based power devices. Therefore, the application demand for silicon carbide power devices in electric vehicles is becoming increasingly prominent. In electric vehicles, the application of silicon carbide power devices is mainly in two directions, one for motor drive inverters (motor controllers), and the other for on-board power systems, mainly including: power conversion systems (on-board DC/DC), on-board charging systems (OBC), on-board air conditioning systems (PTC and air compressors), etc.
Automotive Silicon Carbide Power Module
Industrialization and technical logic
At present, the global silicon carbide industry is dominated by the United States, Europe, and Japan. More than 70% of silicon carbide materials come from American companies. Europe has a complete silicon carbide substrate, epitaxy, device, and application industry chain, while Japan has a leading advantage in the development of silicon carbide chips, modules, and applications. China currently has a complete silicon carbide industry chain and is internationally competitive in some links such as material preparation and packaging and testing applications. Currently, the top few companies are all foreign companies, and domestic companies have not yet formed a certain market share. In the field of new energy vehicles, as my country's automobile electrification is at the forefront of the world, the local market is becoming a favorable factor for the rise of domestic semiconductor companies.
At present, global silicon carbide companies are actively exploring the automotive market, and the main applications include power discrete devices and power modules. Among them, the excellent characteristics of silicon carbide chips need to be perfectly displayed through packaging and circuit systems to achieve efficient and highly reliable power connection. Silicon carbide MOSFET power modules, which are made through professional design and advanced packaging technology, are the mainstream trend of electric vehicle applications.
At present, the design direction of the new SiC module is to make the structure more compact. By adopting double-sided silver sintering and copper wire bonding technology, as well as silicon nitride high-performance AMB ceramic plates, copper-based PinFin plates for liquid cooling, and induction terminals (welding and crimping compatible) for multi-signal monitoring, efforts are made to move towards low loss, high blocking voltage, low on-resistance, high current density, and high reliability. Good design and advanced process technology ensure that the performance advantages of silicon carbide MOSFET are maximized in the equipment.
Figure 5. Silicon Carbide MOSFET packaging requirements
Smaller cell size, lower specific on-resistance, lower switching loss, and better gate oxide protection are the main development trends of SiC MOSFET technology, which are reflected in better performance and higher reliability on the application side. In addition, the high power density, high junction temperature, and high frequency characteristics of SiC devices also put forward higher requirements for existing packaging technology. At present, China's power module packaging innovation is mainly moving in the following directions:
●More advanced connection materials and connection processes to withstand higher temperature changes
Three types of ceramic copper clad laminates are mainly used in power modules: AI2O3-DBC has the highest thermal resistance but the lowest manufacturing cost; AlN-DBC has the lowest thermal resistance but poor toughness; Si3N4-AMB ceramic material has a moderate thermal resistance, excellent toughness, better thermal capacity parameters, and reliability far exceeding AlN and AI2O3, which greatly improves the module's heat dissipation capacity, current capacity, and power density, making it very suitable for automotive-grade silicon carbide module applications.
Previous article:MagCode®-Magnetic Power Supply System Introduction
Next article:Design strategies and principles for grounding of automotive wiring harnesses
Recommended ReadingLatest update time:2024-11-16 14:25
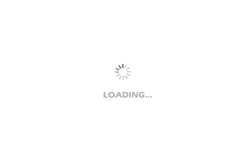
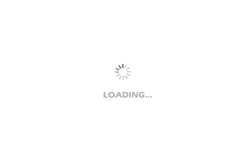
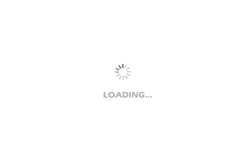
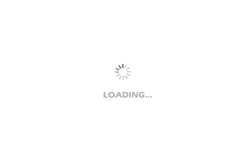
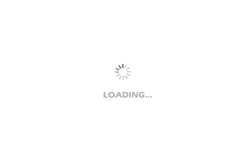
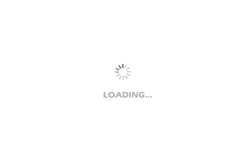
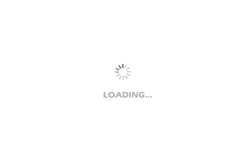
- Popular Resources
- Popular amplifiers
- Huawei's Strategic Department Director Gai Gang: The cumulative installed base of open source Euler operating system exceeds 10 million sets
- Analysis of the application of several common contact parts in high-voltage connectors of new energy vehicles
- Wiring harness durability test and contact voltage drop test method
- Sn-doped CuO nanostructure-based ethanol gas sensor for real-time drunk driving detection in vehicles
- Design considerations for automotive battery wiring harness
- Do you know all the various motors commonly used in automotive electronics?
- What are the functions of the Internet of Vehicles? What are the uses and benefits of the Internet of Vehicles?
- Power Inverter - A critical safety system for electric vehicles
- Analysis of the information security mechanism of AUTOSAR, the automotive embedded software framework
Professor at Beihang University, dedicated to promoting microcontrollers and embedded systems for over 20 years.
- Innolux's intelligent steer-by-wire solution makes cars smarter and safer
- 8051 MCU - Parity Check
- How to efficiently balance the sensitivity of tactile sensing interfaces
- What should I do if the servo motor shakes? What causes the servo motor to shake quickly?
- 【Brushless Motor】Analysis of three-phase BLDC motor and sharing of two popular development boards
- Midea Industrial Technology's subsidiaries Clou Electronics and Hekang New Energy jointly appeared at the Munich Battery Energy Storage Exhibition and Solar Energy Exhibition
- Guoxin Sichen | Application of ferroelectric memory PB85RS2MC in power battery management, with a capacity of 2M
- Analysis of common faults of frequency converter
- In a head-on competition with Qualcomm, what kind of cockpit products has Intel come up with?
- Dalian Rongke's all-vanadium liquid flow battery energy storage equipment industrialization project has entered the sprint stage before production
- Allegro MicroSystems Introduces Advanced Magnetic and Inductive Position Sensing Solutions at Electronica 2024
- Car key in the left hand, liveness detection radar in the right hand, UWB is imperative for cars!
- After a decade of rapid development, domestic CIS has entered the market
- Aegis Dagger Battery + Thor EM-i Super Hybrid, Geely New Energy has thrown out two "king bombs"
- A brief discussion on functional safety - fault, error, and failure
- In the smart car 2.0 cycle, these core industry chains are facing major opportunities!
- The United States and Japan are developing new batteries. CATL faces challenges? How should China's new energy battery industry respond?
- Murata launches high-precision 6-axis inertial sensor for automobiles
- Ford patents pre-charge alarm to help save costs and respond to emergencies
- New real-time microcontroller system from Texas Instruments enables smarter processing in automotive and industrial applications
- Design of NB Iot small weather station based on GD32E231 and NB IOT communication module
- Enthusiasts seek guidance from people who are destined to help them get started with microcontrollers
- Porter-2: Low voltage output feedback circuit processing
- EEWORLD University Hall--The production process of a PCB board
- MCU serial port sends data frame
- EEWORLD University ---- Python Chinese video tutorial
- China Academy of Electronics Science Recruitment [Embedded] [Algorithm], etc.
- RL78 MCU Timer
- Microbit expansion board, using RJ11 connector, including all information
- Class B amplifier question: Under what circumstances will the transistors be turned on at the same time? What are the conditions?