In recent years, with the development of society, PLC programmable controllers have been widely used in industrial production. At the same time, the requirements of technicians for their use are also increasing year by year, so the requirements for the normal and stable operation of the system are also getting higher and higher. The reliability of the PLC product itself can be guaranteed, but some incorrect operations in the application will cause certain effects. Today, the editor has sorted out some practical tips for daily PLC applications, hoping to help everyone in their daily use of PLC.
1. Grounding problem
The grounding requirements of the PLC system are relatively strict. It is best to have an independent dedicated grounding system. It is also necessary to pay attention to the reliable grounding of other equipment related to the PLC. When multiple circuit grounding points are connected together, unexpected currents will be generated, resulting in logical errors or circuit damage. The reason for the different grounding potentials is usually that the grounding points are separated too far in the physical area. When devices far apart are connected by communication cables or sensors, the current between the cable and the ground will flow through the entire circuit. Even in a short distance, the load current of large equipment can change between it and the ground potential, or directly generate unpredictable currents through electromagnetic effects. Between the power supplies of incorrect grounding points, destructive currents may be generated in the circuit, so that the equipment is damaged. The PLC system generally uses a single-point grounding method. In order to improve the ability to resist common-mode interference, shielded floating ground technology can be used for analog signals, that is, the shielding layer of the signal cable is grounded at one point, the signal loop is floating, and the insulation resistance with the earth should be no less than 50MΩ.
(II) Anti-interference processing
The environment of industrial sites is relatively harsh, and there are many high- and low-frequency interferences. These interferences are generally introduced into the PLC through the cables connected to the field equipment. In addition to grounding measures, some anti-interference measures should be taken in the design, selection and installation of cables: (1) Analog signals are small signals and are easily affected by external interference. Double-shielded cables should be used; (2) High-speed pulse signals (such as pulse sensors, counting encoders, etc.) should use shielded cables to prevent both external interference and interference of high-speed pulse signals on low-level signals; (3) The communication cables between PLCs have high frequencies. Generally, the cables provided by the manufacturer should be used. If the requirements are not high, shielded twisted-pair cables can be used; (4) Analog signal lines and DC signal lines cannot be routed in the same cable duct as AC signal lines; (5) The shielded cables introduced into and led out of the control cabinet must be grounded and should be directly connected to the equipment without passing through the wiring terminals; (6) AC signals, DC signals and analog signals cannot share the same cable. Power cables should be laid separately from signal cables. (7) During on-site maintenance, the following methods can be used to resolve interference: using shielded cables for the affected lines and re-laying them; adding anti-interference filtering codes to the program.
3. Eliminate inter-wire capacitance to avoid false operation
There is capacitance between each conductor of the cable. A qualified cable can limit this capacitance within a certain range. Even for qualified cables, when the cable length exceeds a certain length, the capacitance between each wire will exceed the required value. When this cable is used for PLC input, the capacitance between the wires may cause the PLC to malfunction, resulting in many incomprehensible phenomena. These phenomena are mainly manifested as: the exposed wiring is correct, but the PLC has no input; the input that the PLC should have is not there, but the input that it should not have is there, that is, the PLC inputs interfere with each other. To solve this problem, you should do the following: (1) Use cables with twisted cores; (2) Try to shorten the length of the cable; (3) Use cables separately for inputs that interfere with each other; (4) Use shielded cables.
(IV) Selection of output modules
Output modules are divided into transistor, bidirectional thyristor, and contact type: (1) The transistor type has the fastest switching speed (generally 0.2ms), but the smallest load capacity, about 0.2~0.3A, 24VDC, suitable for fast switching and signal connection equipment, generally connected with frequency conversion, DC devices and other signals, and attention should be paid to the impact of transistor leakage current on the load. (2) The advantage of the thyristor type is that it has no contacts, has AC load characteristics, and has a small load capacity. (3) Relay output has AC and DC load characteristics and a large load capacity. In conventional control, relay contact type output is generally used first. The disadvantage is that the switching speed is slow, generally around 10ms, and it is not suitable for high-frequency switching applications.
(V) Inverter overvoltage and overcurrent processing
(1) When the given voltage is reduced to slow down the motor, the motor enters the regenerative braking state. The energy fed back to the inverter by the motor is also high. This energy is stored in the filter capacitor, which increases the voltage on the capacitor and quickly reaches the set value of the DC overvoltage protection, causing the inverter to trip. The solution is to add a braking resistor outside the inverter and use the resistor to consume the regenerative power fed back to the DC side by the motor. (2) The inverter carries multiple small motors. When one of the small motors has an overcurrent fault, the inverter will alarm for an overcurrent fault, causing the inverter to trip, thereby causing other normal small motors to stop working. The solution is to install a 1:1 isolation transformer on the output side of the inverter. When one or several small motors have an overcurrent fault, the fault current will impact the transformer instead of the inverter, thereby preventing the inverter from tripping. After the experiment, it worked well and the previous normal motor shutdown fault did not occur again.
(VI) Marking input and output for easy maintenance
PLC controls a complex system. What you can see are two rows of staggered input and output relay terminals, corresponding indicator lights and PLC numbers, just like an integrated circuit with dozens of pins. Anyone who does not look at the schematic diagram to repair the faulty equipment will be helpless and the speed of finding the fault will be particularly slow. In view of this situation, we draw a table based on the electrical schematic diagram and stick it on the console or control cabinet of the equipment, indicating the electrical symbols and Chinese names corresponding to each PLC input and output terminal number, which is similar to the functional description of each pin of the integrated circuit. With this input and output table, electricians who understand the operation process or are familiar with the ladder diagram of this equipment can start the repair. But for those electricians who are not familiar with the operation process and cannot read the ladder diagram, they need to draw another table: PLC input and output logic function table. This table actually explains the logical correspondence between the input circuit (trigger element, associated element) and the output circuit (actuator) in most operation processes. Practice has proved that if you can skillfully use the input and output correspondence table and the input and output logic function table, you can easily repair electrical faults without drawings.
7. Inferring Faults through Program Logic
There are many types of PLCs commonly used in industry now. For low-end PLCs, the ladder diagram instructions are similar. For mid-to-high-end machines, such as S7-300, many programs are compiled using language tables. Practical ladder diagrams must have Chinese symbol annotations, otherwise it is difficult to read. If you can roughly understand the equipment process or operation process before reading the ladder diagram, it will seem easier. If electrical fault analysis is performed, the reverse search method or reverse deduction method is generally applied, that is, according to the input-output correspondence table, the output relay of the corresponding PLC is found from the fault point, and the logical relationship that satisfies its action is reversed. Experience shows that if a problem is found, the fault can be basically eliminated, because there are not many equipment with two or more fault points at the same time.
(VIII) PLC self-fault judgment
Generally speaking, PLC is an extremely reliable device with a very low failure rate. The probability of hardware damage such as PLC and CPU or software running errors is almost zero. PLC input points will hardly be damaged unless they are caused by strong electric intrusion. The normally open point of PLC output relay will have a long contact life unless the peripheral load is short-circuited or the design is unreasonable, and the load current exceeds the rated range. Therefore, when we look for electrical fault points, we should focus on the peripheral electrical components of PLC, and do not always suspect that there are problems with PLC hardware or programs. This is very important for quickly repairing faulty equipment and quickly resuming production. Therefore, the electrical fault inspection and repair of PLC control circuits discussed by the author does not focus on PLC itself, but on the peripheral electrical components in the circuit controlled by PLC.
Previous article:The structure and working principle of brushless DC motor
Next article:Three-phase motor star/delta step-down starting control circuit
Recommended ReadingLatest update time:2024-11-16 09:39
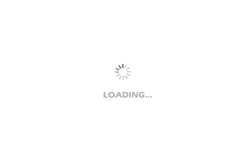
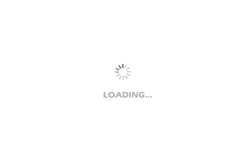
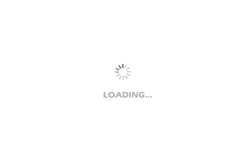
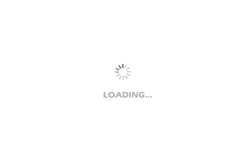
- Popular Resources
- Popular amplifiers
- Huawei's Strategic Department Director Gai Gang: The cumulative installed base of open source Euler operating system exceeds 10 million sets
- Analysis of the application of several common contact parts in high-voltage connectors of new energy vehicles
- Wiring harness durability test and contact voltage drop test method
- Sn-doped CuO nanostructure-based ethanol gas sensor for real-time drunk driving detection in vehicles
- Design considerations for automotive battery wiring harness
- Do you know all the various motors commonly used in automotive electronics?
- What are the functions of the Internet of Vehicles? What are the uses and benefits of the Internet of Vehicles?
- Power Inverter - A critical safety system for electric vehicles
- Analysis of the information security mechanism of AUTOSAR, the automotive embedded software framework
Professor at Beihang University, dedicated to promoting microcontrollers and embedded systems for over 20 years.
- Innolux's intelligent steer-by-wire solution makes cars smarter and safer
- 8051 MCU - Parity Check
- How to efficiently balance the sensitivity of tactile sensing interfaces
- What should I do if the servo motor shakes? What causes the servo motor to shake quickly?
- 【Brushless Motor】Analysis of three-phase BLDC motor and sharing of two popular development boards
- Midea Industrial Technology's subsidiaries Clou Electronics and Hekang New Energy jointly appeared at the Munich Battery Energy Storage Exhibition and Solar Energy Exhibition
- Guoxin Sichen | Application of ferroelectric memory PB85RS2MC in power battery management, with a capacity of 2M
- Analysis of common faults of frequency converter
- In a head-on competition with Qualcomm, what kind of cockpit products has Intel come up with?
- Dalian Rongke's all-vanadium liquid flow battery energy storage equipment industrialization project has entered the sprint stage before production
- Allegro MicroSystems Introduces Advanced Magnetic and Inductive Position Sensing Solutions at Electronica 2024
- Car key in the left hand, liveness detection radar in the right hand, UWB is imperative for cars!
- After a decade of rapid development, domestic CIS has entered the market
- Aegis Dagger Battery + Thor EM-i Super Hybrid, Geely New Energy has thrown out two "king bombs"
- A brief discussion on functional safety - fault, error, and failure
- In the smart car 2.0 cycle, these core industry chains are facing major opportunities!
- The United States and Japan are developing new batteries. CATL faces challenges? How should China's new energy battery industry respond?
- Murata launches high-precision 6-axis inertial sensor for automobiles
- Ford patents pre-charge alarm to help save costs and respond to emergencies
- New real-time microcontroller system from Texas Instruments enables smarter processing in automotive and industrial applications
- How to achieve automated testing of LCR?
- How to speed up the program running speed of Huada HC32F460 HC32F4A0?
- FPDLINK Spark Interference Optimization
- Why do electrolytic capacitors explode? Find out in one article!
- [Iprober 520 current probe] Calibration and use in PCB mode
- A brief history of hard disk interface evolution
- Hot plug and unplug
- EEWORLD University ---- STM32CubeMX and STM32Cube HAL basics
- [TI mmWave Radar Evaluation]_3_AWR1843BOOST Corridor Ranging Test Environment
- What is the relationship between the Internet of Things and embedded systems?