PLC and frequency converter have a relationship of inclusion and being included. Both PLC and frequency converter can complete some specific instructions to control motors. PLC is a program input execution hardware, and frequency converter is one of them.
However, the PLC covers a wider range than the frequency converter, and can be used to control more things, with a wider range of applications and more powerful performance. Of course, the PLC's control accuracy is also greater. The frequency converter cannot be programmed to change the power supply frequency, voltage and other parameters. Its output frequency can be set to a fixed value or dynamically controlled by the PLC.
PLC is programmable and is used to control electrical components or complete functions, communications and other tasks.
The communication between PLC and inverter needs to follow the universal serial interface protocol (USS), and the access method is determined according to the master-slave communication principle of the serial bus. The bus can connect a master station and up to 31 slave stations. The master station selects the slave station to transmit data according to the address characters in the communication message. When the master station does not require it to communicate, the slave station itself cannot send data first, and information cannot be directly transmitted between the slave stations.
There are generally three ways to connect PLC and inverter
01. Use the analog output module of the PLC to control the inverter. The analog output module of the PLC outputs a 0-5V voltage signal or a 4-20mA current signal as the analog input signal of the inverter to control the output frequency of the inverter. This control method has simple wiring, but it is necessary to select a PLC output module that matches the input impedance of the inverter, and the analog output module of the PLC is relatively expensive. In addition, voltage division measures must be taken to make the inverter adapt to the voltage signal range of the PLC. When connecting, pay attention to separate the wiring to ensure that the noise on one side of the main circuit is not transmitted to the control circuit.
02. Use the switch output of PLC to control the inverter. The switch output of PLC can generally be directly connected to the switch input terminal of the inverter. This control method has simple wiring and strong anti-interference ability. The switch output of PLC can be used to control the start/stop, forward/reverse, jog, speed and addition and subtraction time of the inverter, which can achieve more complex control requirements, but can only be adjusted in steps. When using relay contacts for connection, there is sometimes a phenomenon of misoperation due to poor contact. When using transistors for connection, it is necessary to consider factors such as the voltage and current capacity of the transistor itself to ensure the reliability of the system. In addition, when designing the input signal circuit of the inverter, it should also be noted that improper connection of the input signal circuit may sometimes cause malfunction of the inverter. For example, when the input signal circuit uses inductive loads such as relays, the noise caused by the surge current generated when the relay is opened and closed may cause malfunction of the inverter, which should be avoided as much as possible.
03. Connection between PLC and RS-485 communication interface. All standard Siemens inverters have an RS-485 serial interface (some also provide RS-232 interface), which adopts two-wire connection and is designed for industrial applications. A single RS-485 link can connect up to 30 inverters, and the inverter that needs to communicate can be found according to the address of each inverter or by broadcast information. There needs to be a master controller (master station) in the link, and each inverter is a subordinate control object (slave station).
Communication mode between PLC and inverter
01
The PLC's switch signal controls the output point and COM point of the inverter PLC (MR or MT type) to be directly connected to the inverter's STF (forward start), RH (high speed), RM (medium speed), RL (low speed), input terminal SG and other ports. PLC can control the start, stop and reset of the inverter through the program; it can also control the different combinations of the inverter's high speed, medium speed and low speed terminals to achieve multi-speed operation. However, because it uses switch quantity to implement control, its speed regulation curve is not a continuous and smooth curve, and it is impossible to achieve fine speed regulation.
02
PLC analog signal control inverter hardware: FX1N, FX2N PLC host, equipped with 1-way simple FX1N-1DA-BD expansion analog output board; or analog input and output mixed module FX0N-3A; or two-way output FX2N-2DA; or four-way output FX2N-4DA module, etc. Advantages: PLC program compilation is simple and convenient, the speed regulation curve is smooth and continuous, and the operation is stable. Disadvantages: In large-scale production lines, the control cable is long, especially when the DA module uses voltage signal output, the line has a large voltage drop, which affects the stability and reliability of the system.
03
PLC uses RS-485 communication method to control the inverter. This is the most commonly used method. PLC uses RS serial communication instruction programming. Advantages: simple hardware, lowest cost, can control 32 inverters. Disadvantages: large programming workload.
04
PLC uses RS-485 Modbus-RTU communication method to control the inverter. Mitsubishi's new F700 series inverter uses RS-485 terminals to communicate with PLC using Modbus-RTU protocol. Advantages: PLC programming with Modbus communication method is simpler and more convenient than RS-485 non-protocol method. Disadvantages: PLC programming workload is still large.
05
PLC uses fieldbus to control the inverter. Mitsubishi inverters can have built-in various types of communication options, such as FR-A5NC option for CC-Link fieldbus; FR-A5AP (A) option for Profibus DP fieldbus; FR-A5ND option for DeviceNet fieldbus, etc. Mitsubishi FX series PLC has corresponding communication interface modules to connect with it. Advantages: fast speed, long distance, high efficiency, stable operation, simple programming, and a large number of inverters that can be connected. Disadvantages: high cost.
06
Advantages of using extended memory: low cost, easy to learn and use, reliable performance Disadvantages: can only be used in systems with no more than 8 inverters.
PLC and inverter communication wiring diagram
After reading all the above content, do you understand how PLC and inverter communicate?
Previous article:Application of PLC technology in automation control of electrical equipment
Next article:PLC outputs random numbers between 0 and 100
Recommended ReadingLatest update time:2024-11-16 11:59
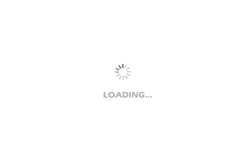
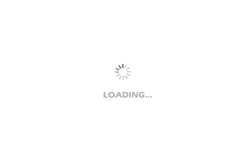
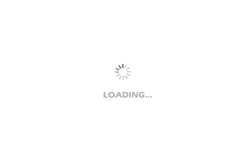
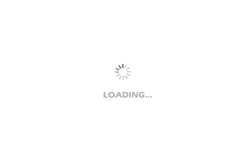
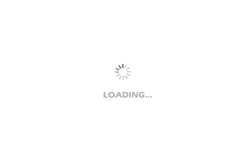
- Popular Resources
- Popular amplifiers
- Huawei's Strategic Department Director Gai Gang: The cumulative installed base of open source Euler operating system exceeds 10 million sets
- Analysis of the application of several common contact parts in high-voltage connectors of new energy vehicles
- Wiring harness durability test and contact voltage drop test method
- Sn-doped CuO nanostructure-based ethanol gas sensor for real-time drunk driving detection in vehicles
- Design considerations for automotive battery wiring harness
- Do you know all the various motors commonly used in automotive electronics?
- What are the functions of the Internet of Vehicles? What are the uses and benefits of the Internet of Vehicles?
- Power Inverter - A critical safety system for electric vehicles
- Analysis of the information security mechanism of AUTOSAR, the automotive embedded software framework
Professor at Beihang University, dedicated to promoting microcontrollers and embedded systems for over 20 years.
- Innolux's intelligent steer-by-wire solution makes cars smarter and safer
- 8051 MCU - Parity Check
- How to efficiently balance the sensitivity of tactile sensing interfaces
- What should I do if the servo motor shakes? What causes the servo motor to shake quickly?
- 【Brushless Motor】Analysis of three-phase BLDC motor and sharing of two popular development boards
- Midea Industrial Technology's subsidiaries Clou Electronics and Hekang New Energy jointly appeared at the Munich Battery Energy Storage Exhibition and Solar Energy Exhibition
- Guoxin Sichen | Application of ferroelectric memory PB85RS2MC in power battery management, with a capacity of 2M
- Analysis of common faults of frequency converter
- In a head-on competition with Qualcomm, what kind of cockpit products has Intel come up with?
- Dalian Rongke's all-vanadium liquid flow battery energy storage equipment industrialization project has entered the sprint stage before production
- Allegro MicroSystems Introduces Advanced Magnetic and Inductive Position Sensing Solutions at Electronica 2024
- Car key in the left hand, liveness detection radar in the right hand, UWB is imperative for cars!
- After a decade of rapid development, domestic CIS has entered the market
- Aegis Dagger Battery + Thor EM-i Super Hybrid, Geely New Energy has thrown out two "king bombs"
- A brief discussion on functional safety - fault, error, and failure
- In the smart car 2.0 cycle, these core industry chains are facing major opportunities!
- The United States and Japan are developing new batteries. CATL faces challenges? How should China's new energy battery industry respond?
- Murata launches high-precision 6-axis inertial sensor for automobiles
- Ford patents pre-charge alarm to help save costs and respond to emergencies
- New real-time microcontroller system from Texas Instruments enables smarter processing in automotive and industrial applications
- Interesting impedance transformation
- 220V switch control circuit
- [Synopsys IP Resources] Under the hood of ASIP Designer - Tool automation enables application-specific processing...
- [TI recommended course] #SimpleLink?MCU platform SDK code portability#
- To drive a 24V5A motor, what current should the freewheeling diode have?
- Analysis of the six major reasons for Wi-Fi wireless connection failure and solutions
- CC2640R2F supports Alibaba Cloud Link IoT platform
- Zhihuijun's new open source for National Day: Iron Man's robotic arm Dummy, interesting interactions, sewing grape demo, Hongmeng...
- Some understanding of MSP430 usage
- The price keeps going up.