For the traditional point-to-point connection method, we can see that the ECU-related sensors and actuators are directly connected to the ECU. When the number of sensors and actuators is small, this connection method can meet the requirements. However, with the continuous increase in the number of automotive electronic control functions, the number of sensors and actuators has increased. As you can imagine, if this connection method is adopted, the number of wires will increase. Due to the increase in the number of wires, the cost of wire processing, wires and connectors will increase, which will lead to an increase in the cost of the car. Then there is the increase in the weight of the wires, which leads to an increase in the weight of the car. Of course, the space for the arrangement of the wires is also a problem. At the same time, due to the increase in the number of wires and connector terminals, it will also have an adverse effect on the reliability of the car, and it is also difficult to diagnose the resulting faults. In addition, when we need to add sensors or actuators, we must require the ECU to have the corresponding hardware interface, which is very unfavorable for the expansion of a system. Therefore, we need new solutions to deal with these problems. The first solution is to connect the sensors and actuators directly to the CAN bus where the ECU is located. This solution brings new problems.
First of all, this method requires that both sensors and actuators must have interfaces, including transceivers and controllers. This will lead to a significant increase in the cost of sensors and actuators. At the same time, too many nodes on the bus will also lead to an increase in bus load. The second solution is to connect sensors and actuators to another CAN bus. The ECU in the middle can act as a gateway to complete the data exchange between other ECUs and sensors and actuators.
In this way, although the load rate of the above bus is not affected, it still cannot solve the cost problem caused by the interface. Therefore, a new solution is proposed. In this solution, the CAN bus connecting the sensor and actuator is replaced with a low-cost bus.
Then, the ECU in the middle can realize the function of the gateway and realize the data exchange between this low-cost bus and the CAN bus. This method can solve some of the problems mentioned above. This low-cost bus is the LIN bus to be discussed in this article.
After adopting the LIN bus, the previous point-to-point connection method is switched to this bus network connection method. We can see that sensors and actuators are connected to the ECU through a common communication medium, that is, the LIN bus. This connection method has the following advantages. First, the cost is reduced, and then the requirements for the layout space of the number of lines and the weight of the number of lines will also be reduced. At the same time, due to the reduction in the number of lines and connectors, reliability will also be improved. Through the bus connection method, faults are easier to diagnose. Finally, the system can be flexibly expanded. For example, if we need to add a sensor now, we can hang this sensor on the bus without making corresponding changes to the ECU hardware. The above is a brief introduction to the LIN bus.
Previous article:How to use LIN bus in automotive electronics development
Next article:What are the extended services of CANoe?
Recommended ReadingLatest update time:2024-11-16 13:29
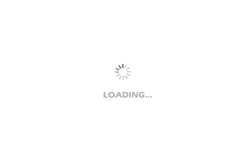
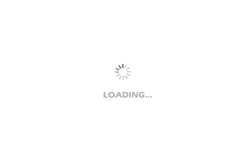
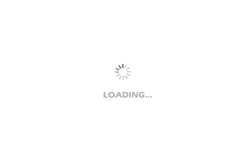
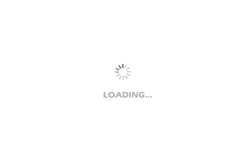
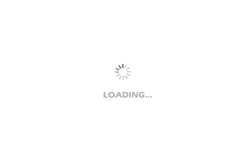
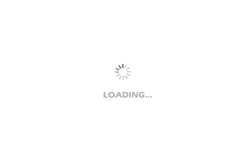
- Popular Resources
- Popular amplifiers
-
Analysis and Implementation of MAC Protocol for Wireless Sensor Networks (by Yang Zhijun, Xie Xianjie, and Ding Hongwei)
-
Introduction to Internet of Things Engineering 2nd Edition (Gongyi Wu)
-
西门子S7-12001500 PLC SCL语言编程从入门到精通 (北岛李工)
-
Modern Motor Control Technology (Wang Chengyuan, Xia Jiakuan, Sun Yibiao)
- Huawei's Strategic Department Director Gai Gang: The cumulative installed base of open source Euler operating system exceeds 10 million sets
- Analysis of the application of several common contact parts in high-voltage connectors of new energy vehicles
- Wiring harness durability test and contact voltage drop test method
- Sn-doped CuO nanostructure-based ethanol gas sensor for real-time drunk driving detection in vehicles
- Design considerations for automotive battery wiring harness
- Do you know all the various motors commonly used in automotive electronics?
- What are the functions of the Internet of Vehicles? What are the uses and benefits of the Internet of Vehicles?
- Power Inverter - A critical safety system for electric vehicles
- Analysis of the information security mechanism of AUTOSAR, the automotive embedded software framework
Professor at Beihang University, dedicated to promoting microcontrollers and embedded systems for over 20 years.
- Innolux's intelligent steer-by-wire solution makes cars smarter and safer
- 8051 MCU - Parity Check
- How to efficiently balance the sensitivity of tactile sensing interfaces
- What should I do if the servo motor shakes? What causes the servo motor to shake quickly?
- 【Brushless Motor】Analysis of three-phase BLDC motor and sharing of two popular development boards
- Midea Industrial Technology's subsidiaries Clou Electronics and Hekang New Energy jointly appeared at the Munich Battery Energy Storage Exhibition and Solar Energy Exhibition
- Guoxin Sichen | Application of ferroelectric memory PB85RS2MC in power battery management, with a capacity of 2M
- Analysis of common faults of frequency converter
- In a head-on competition with Qualcomm, what kind of cockpit products has Intel come up with?
- Dalian Rongke's all-vanadium liquid flow battery energy storage equipment industrialization project has entered the sprint stage before production
- Allegro MicroSystems Introduces Advanced Magnetic and Inductive Position Sensing Solutions at Electronica 2024
- Car key in the left hand, liveness detection radar in the right hand, UWB is imperative for cars!
- After a decade of rapid development, domestic CIS has entered the market
- Aegis Dagger Battery + Thor EM-i Super Hybrid, Geely New Energy has thrown out two "king bombs"
- A brief discussion on functional safety - fault, error, and failure
- In the smart car 2.0 cycle, these core industry chains are facing major opportunities!
- The United States and Japan are developing new batteries. CATL faces challenges? How should China's new energy battery industry respond?
- Murata launches high-precision 6-axis inertial sensor for automobiles
- Ford patents pre-charge alarm to help save costs and respond to emergencies
- New real-time microcontroller system from Texas Instruments enables smarter processing in automotive and industrial applications
- How much do you know about the "ADI Inside" behind these popular healthcare products?
- About ARM's interrupt service routine
- P-NUCLEO-WB55
- 4.3-inch split-screen display
- Recommend a 24-bit ADC module (not a chip), preferably with the same pin definition as the attachment, 12 pins, SPI interface...
- Reasons why the POE module does not supply power
- What are the types of LDOs used in portable mobile devices? Ripple test methods
- 【CH579M-R1】+Complete the read and write operations on AT24C32EEPROM
- How to burn the program to Renesas H8S/2398 (HD64F2398FV20)
- Questions about option byte