There are three main types of stepper motors on the market: PM (permanent magnet), VR (variable reluctance), and hybrid. What are the differences, which one should you use, and how do they work?
Let’s quickly review what a stepper motor does. A stepper motor rotates in specific “step” increments without the need for encoder feedback or complex PID loops. The amount of rotation and speed are easily controlled by the number of pulses and frequency, and stepper motors provide highly repeatable stopping accuracy of ±3 arc minutes (±0.05°). When a stepper motor is powered but stationary, it produces holding torque in the absence of an electromagnetic brake. They are ideal for cost-sensitive applications where the motor needs to stop accurately and provide holding torque.
The design of a stepper motor affects its characteristics. In the next few minutes, I will introduce the three types of stepper motors on the market and why you might prefer one over the other.
PM "Permanent Magnet" Type
This is a stepper motor whose rotor is made of two permanent magnet rotors slightly offset from each other. The permanent magnets are axially magnetized; this means that the north and south poles alternate and lie on the same axis as the motor shaft. When current is applied to the windings, the poles on the stator are magnetized and aligned with the opposite poles of the permanent magnet rotor. For example, the north pole will be directly aligned with the south pole.
A widely used PM type stepper motor is a 2-phase claw motor as shown below.
The figure below shows a rotor and a stator where current is applied so that pole A1 is magnetized to the south pole and pole A2 is magnetized to the north pole, thus attracting the opposite pole of the rotor's permanent magnet. If the current is switched from phase A to phase B, so that B1 is magnetized to the south pole and B2 to the north pole, the rotor will rotate 90° clockwise.
The step angle is expressed as follows using the number of poles (Np) and the number of phases (Nphase) of the rotor. If the number of poles or phases increases, the step angle decreases. However, as the number of poles increases, the magnetic force and torque also become weaker.
PM stepper motors are simple in construction and inexpensive to manufacture. Permanent magnets allow PM stepper motors to output higher torque. However, high-speed performance is limited due to high losses during rotation. PM stepper motors are often used for simple positioning because their resolution tends to be greater than other types (i.e.: 3.6° or greater). For higher resolution, half-stepping or micro-stepping is recommended. With micro-stepping, the drive's ability to precisely control the current in each phase becomes increasingly important in determining the motor's repeatable position accuracy. Another difference is that PM stepper motors use constant voltage drives, which are more difficult to use than constant current chopper drives.
VR "Variable Reluctance" Type
This is a type of stepper motor that provides teeth on the rotor and stator where the magnetic force is concentrated. It provides the simplest design of the three types discussed here. The figure below shows an 8-pole, 12-slot, 3-phase VR-type stepper motor. Most magnetic cores use ferromagnetic materials such as iron because it is abundant in the earth and can easily pass magnetic flux. The VR-type stepper motor has no magnets, which means it cannot output holding torque or braking torque when stationary.
The figure below shows an example of a 4 pole 6 slot VR type stepper motor. The "teeth" on the rotor are attracted to the poles on the stator. The stator poles on each side of the rotor are magnetized north and south by oppositely wound poles.
In the figure below, we show the "Phase B energized" state on the left. In this case, the tooth closest to the rotor will align with the closest pole on the stator. The rotor will rotate 30° counterclockwise until the teeth align with each other (see "Stop Position of Phase B"). Now, when Phase C is energized in the same way, the rotor will rotate 60° until the teeth align with Phase C.
B phase excitation B phase stop position C phase stop position
One advantage of the VR stepper motor is that it does not require the polarity of the stator magnetic poles to be changed, so its drive circuit can be simplified. Its disadvantage is that it cannot perform fine torque control because the torque is proportional to the square of the current, not the current. However, since it does not use permanent magnets, its high-speed performance is better than that of the PM stepper motor.
The step angle of a VR type stepper motor is expressed by the following formula. Np is the number of teeth of the rotor, and Nphase is the number of phases. For finer resolution, it is effective to increase the number of teeth of the rotor. However, if the number of stator slots is also increased, the structure becomes very complicated to manufacture. The figure below shows a 50-tooth rotor and stator design. This is a 4-phase stepper motor with coils divided into 4 groups. Inputting Np = 50 and Nphase = 4 will result in a step angle of 1.8°.
VR stepper motors have been around for a long time. These motors have less torque drop at higher motor speeds, so they are often a better choice than PM stepper motors in medium and high speed applications. However, they are known to generate more noise, so their range of applications is limited. VR stepper motors are not as common on the market as PM stepper motors.
Hybrid stepper motor
The "hybrid" stepper motor combines the design and benefits of both the permanent magnet and variable reluctance stepper motors. Therefore, the hybrid stepper motor uses both a permanent magnet rotor and a toothed rotor and stator in its design. With strong permanent magnets, toothed rotors, toothed stators, and a small air gap, the hybrid stepper motor is able to concentrate the magnetic flux better than the other two types. The low losses are achieved by stacking the magnetic laminations, and the magnetic flux passes easily.
The construction of a hybrid stepper motor starts with two rotor cups (Rotor 1 and Rotor 2) and an axially magnetized strong rare earth permanent magnet. Two ball bearings mount the rotors to the motor housing. There are either 50 teeth (1.8° per step) or 100 teeth (0.9° per step) on the rotors. One rotor is magnetized to the north pole and one rotor is magnetized to the south pole. Each tooth on the rotor cup becomes a magnetic pole.
In the two images below we show a top view of the two rotors; starting with the North Pole rotor at the top. The two rotor cups are different colors. Red is the North Pole rotor and blue is the South Pole rotor.
Since there are 50 teeth, the full pitch is 7.2°. The two rotor cups are offset by half a pitch (3.6°) so that the south pole tooth of rotor 1 lines up between the north pole teeth of rotor 2. From the cross-sectional view of the rotor, you can clearly see that the north and south pole teeth alternate due to the offset of the two rotor cups. When the drive energizes or energizes the windings, the stator poles become electromagnets and the permanent magnet rotor follows them through pull and push and stops in fixed increments. The north pole of the stator will attract the south pole of the rotor and vice versa.
There are eight stator poles in the stator. When the winding is wound around the main magnetic pole and current is applied, each magnetic pole is magnetized to the north pole or the south pole. The direction of the current can determine the magnetic pole. When excited, the two poles on the opposite side have the same polarity, and the two poles at 90° to these poles have opposite polarity. The main magnetic poles excited together are called "phases" and can be divided into two phases (phase A and phase B). This is why it is called a "two-phase" stepper motor.
The step angle of a hybrid stepper motor is inversely proportional to the number of small teeth ZR on the rotor and the number of phases n. The denominator 2 means that the main magnetic poles of the stator can be configured in two states: north pole and south pole. This is the fundamental design difference between VR type and hybrid stepper motors.
Tooth alignment deviation A phase excitation B phase excitation
The reason why the hybrid stepper motor rotates 1.8° per step is that due to the geometric design between the rotor and stator, the motor only moves a quarter of a tooth pitch per step. When the A phase is excited to the south pole and its stator teeth are directly aligned with the north pole teeth of the rotor, the stator teeth of the B phase are actually offset from the rotor teeth by 1.8°. This is called tooth arrangement offset and is the reason why the two-phase hybrid stepper motor rotates 1.8° per step.
For a stepper motor with 0.9° per step, both rotor teeth would need to be increased to 100. Anything over 100 teeth would be difficult to manufacture.
For hybrid stepper motors, rare earth permanent magnets can achieve high torque while maintaining the high resolution obtained by small teeth. In addition, the relationship between current and torque is close to proportional; making it easier to control than VR-type stepper motors. Hybrid stepper motors can also achieve higher resolution (i.e.: 0.72° per full step/500 steps per revolution). Higher resolution can be achieved through microstepping.
Summary
PM (Permanent Magnet) type: using permanent magnets, medium torque, medium and low speed
VR (Variable Reluctance) Type: Toothed rotor/stator, low torque, medium and high speed
Hybrid type: Combination of permanent magnets and teeth, a good combination of torque and speed
The most popular stepper motor on the market is the hybrid type, as it offers the best performance, but at a higher cost. Hybrid stepper motors are suitable for most applications, while permanent magnet or variable reluctance stepper motors are limited to certain applications. In recent years, stepper motors have become increasingly smarter due to technological improvements in functionality, distributed control, and ease of programming. Gearboxes and closed-loop feedback can be added to stepper motors to expand their range of applications. Working with a manufacturer that can provide all the necessary components and training can make life easier.
Previous article:Minimize machine footprint with right angle gear motors
Next article:Instantaneous forward/reverse operation of three-phase AC induction motor
Recommended ReadingLatest update time:2024-11-16 11:24
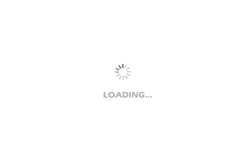
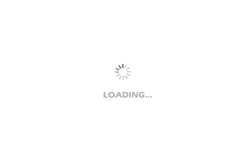
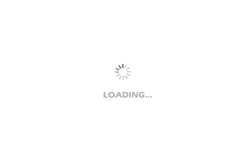
- Popular Resources
- Popular amplifiers
-
Microgrid Stability Analysis and Control Microgrid Modeling Stability Analysis and Control to Improve Power Distribution and Power Flow Control (
-
Virtualization Technology Practice Guide - High-efficiency and low-cost solutions for small and medium-sized enterprises (Wang Chunhai)
-
【2024 DigiKey Creative Competition】+ Portable Infrared Smart Smoking Device-Source Code
-
Analysis of ZVS Flyback Switching Power Supply Technology Based on Synchronous Rectification Controller_Chen Bo
- Huawei's Strategic Department Director Gai Gang: The cumulative installed base of open source Euler operating system exceeds 10 million sets
- Analysis of the application of several common contact parts in high-voltage connectors of new energy vehicles
- Wiring harness durability test and contact voltage drop test method
- Sn-doped CuO nanostructure-based ethanol gas sensor for real-time drunk driving detection in vehicles
- Design considerations for automotive battery wiring harness
- Do you know all the various motors commonly used in automotive electronics?
- What are the functions of the Internet of Vehicles? What are the uses and benefits of the Internet of Vehicles?
- Power Inverter - A critical safety system for electric vehicles
- Analysis of the information security mechanism of AUTOSAR, the automotive embedded software framework
Professor at Beihang University, dedicated to promoting microcontrollers and embedded systems for over 20 years.
- Innolux's intelligent steer-by-wire solution makes cars smarter and safer
- 8051 MCU - Parity Check
- How to efficiently balance the sensitivity of tactile sensing interfaces
- What should I do if the servo motor shakes? What causes the servo motor to shake quickly?
- 【Brushless Motor】Analysis of three-phase BLDC motor and sharing of two popular development boards
- Midea Industrial Technology's subsidiaries Clou Electronics and Hekang New Energy jointly appeared at the Munich Battery Energy Storage Exhibition and Solar Energy Exhibition
- Guoxin Sichen | Application of ferroelectric memory PB85RS2MC in power battery management, with a capacity of 2M
- Analysis of common faults of frequency converter
- In a head-on competition with Qualcomm, what kind of cockpit products has Intel come up with?
- Dalian Rongke's all-vanadium liquid flow battery energy storage equipment industrialization project has entered the sprint stage before production
- Allegro MicroSystems Introduces Advanced Magnetic and Inductive Position Sensing Solutions at Electronica 2024
- Car key in the left hand, liveness detection radar in the right hand, UWB is imperative for cars!
- After a decade of rapid development, domestic CIS has entered the market
- Aegis Dagger Battery + Thor EM-i Super Hybrid, Geely New Energy has thrown out two "king bombs"
- A brief discussion on functional safety - fault, error, and failure
- In the smart car 2.0 cycle, these core industry chains are facing major opportunities!
- The United States and Japan are developing new batteries. CATL faces challenges? How should China's new energy battery industry respond?
- Murata launches high-precision 6-axis inertial sensor for automobiles
- Ford patents pre-charge alarm to help save costs and respond to emergencies
- New real-time microcontroller system from Texas Instruments enables smarter processing in automotive and industrial applications
- Shouldn't we buy chips on Taobao?
- [ESP32-S2-Kaluga-1 Review] 3. Getting started with Ubuntu and updating under Ubuntu
- GD32L233C-START Development Board Study Notes (Part 3)
- EEWORLD University ---- "Embedded Artificial Intelligence" - Chinese Chatbot Development
- Can Software Radio Become Open Radio?
- Sincerely recruiting embedded software and hardware engineers
- The problem of sending 10 seconds of data through the network port
- EEWORLD University ---- RT thread env video
- What is the function of the forward connection of the op amp output to the voltage regulator diode here?
- I2C bus interface EEPROM application pen...