Mir ARM+FPGA architecture development board PCIE2SCREEN example analysis and test
This test content is the ARM+FPGA architecture-based Mir MYD-JX8MMA7 development board, and its ARM-side test routine pcie2screen, and introduces the modification of the FPGA-side program.
01. Test routine pcie2screen
The pcie2screen example is a test example for the MYIR_PCIE_5T_CMOS project of the MYD-JX8MMA7 development board. It is used to display the video captured by the camera connected to the FPGA. After running the program, a window titled demo will be displayed on the screen.
Use the mouse to click the ready button, and the demo window will display continuous video, indicating that the camera, DDR, and PCIE interface are all normal. If there is no camera connected, the program will display a messy image.
The source code of this test case is not included in the SDK, but can be obtained from the technicians of Mir Corporation. This example program is developed with Qt and uses OpenGL technology. The program includes the following main classes:
• MainWindow: QMainWindow subclass, which is the display window.
• uOpenglYuv: QOpenGLWidget subclass, used to display the captured image. The initializeGL function of this class is used to initialize OpenGL. The paintGL function is used to draw the image, and the core statement is:
glTexImage2D(GL_TEXTURE_2D, 0, GL_RGBA, vW, vH, 0, GL_RGBA, GL_UNSIGNED_BYTE, pRGB);
pRGB stores the data read from the FPGA. From this sentence we can see the format of the image required by the program.
• xdma_getImg: main thread class
• xdma_programe: encapsulates the RIFFA interface, in which read_pack is used to read FPGA data and is called cyclically by the main thread. Its function definition is as follows:
int xdma_programe::read_pack(char *pData, int len)
{
//int buffer[1920 * 1080];
//int buffer[1024 * 768];
int buffer[1280 * 720];
int i;
if(dev_fd != NULL)
{
fpga_send(dev_fd, 0, buffer, len / 4, 0, 1, 25000);
fpga_recv(dev_fd, 0, buffer, len / 4, 25000);
memcpy(pData, (char *)buffer, len);
return len;
}
else
{
return 0;
}
}
It can be seen from the function that before each data read, the function first writes data to the FPGA (the data is meaningless and is related to the FPGA's state machine), and reads in a whole frame of data each time.
02. Modification of FPGA-side program
The logic control of the FPGA side is in chnl_tester.v, which defines a state machine for controlling data transmission and reception. The state machine is defined as follows:
always @(posedge CLK or posedge RST) begin
if (RST) begin
rLen <= #1 0;
rCount <= #1 0;
rState <= #1 0;
rData <= #1 0;
vout_vs_r <= #1 0;
end
else begin
case (rState)
3'd0: begin // Wait for start of RX, save length
if (CHNL_RX) begin
rLen <= #1 CHNL_RX_LEN;
rCount <= #1 0;
rState <= #1 3'd1;
end
end
3'd1: begin // Wait for last data in RX, save value
if (CHNL_RX_DATA_VALID) begin
rData <= #1 CHNL_RX_DATA;
rCount <= #1 rCount + (C_PCI_DATA_WIDTH/32);
end
if (rCount >= rLen) begin
rState <= #1 3'd2;
end
end
3'd2: begin // Prepare for TX
if (read_valid) begin
rCount <= #1 0;
rState <= #1 3'd3;
end
end
3'd3: begin // Start TX with save length and data value
if (CHNL_TX_DATA_REN) begin
//rData <= #1 data_in;
rCount <= #1 rCount + (C_PCI_DATA_WIDTH/32);
if (rCount >= rLen)
rState <= #1 3'd4;
end
end
3'd4: begin
if (vout_vs_r)
rState <= #1 3'd5;
else begin
vout_vs_r <= #1 1;
rState <= #1 3'd4;
rCount <= #1 0;
end
end
3'd5: begin
if (vs_flag) begin
rState <= #1 3'd0;
vout_vs_r <= #1 0;
end
else
rState <= #1 3'd5;
end
endcase
end
end
We don't have a camera to test with, so we simply modify the program to send a blue gradient band signal.
The core modifications are as follows:
…
reg [31:0] rColor = 0;
…
assign CHNL_TX_DATA = (read_en)? {rColor, rColor}:64'd0;
…
3'd3: begin // Start TX with save length and data value
if (CHNL_TX_DATA_REN) begin
//rData <= #1 data_in;
// if (rCount % 5 == 4)
rColor <= #1 rColor + 1;
if(rColor >= 255)
rColor <= #1 0;
rCount <= #1 rCount + (C_PCI_DATA_WIDTH/32);
if (rCount >= rLen)
rState <= #1 3'd4;
end
end
…
03. Test results
We did not modify the test program on the ARM side, and still used the pcie2screen provided by the manufacturer, but re-burned the FPGA program. The program's running effect is as follows:
Mir MYC-JX8MMA7 core board and development board.
Mier MYC-JX8MMA7 core board and development board adopt ARM+FPGA processing architecture, NXP i.MX8M Mini and Xilinx Artix-7 processors, quad-core Cortex-A53, Cortex-M4, Artix-7 CPU, 1.8GHz main frequency, based on ARM+FPGA processing architecture, with high performance, low cost, low power consumption and other characteristics, both of which have their own functions and play the unique advantages of the original architecture. The Artix-7 CPU equipped with Zynq 7010 FPGA resources can meet the needs of high-speed data acquisition, and uses PCIE high-speed communication to support 200~300MB/S communication capabilities. It can provide excellent video and audio experience, combining the specific functions of the media with high-performance processing optimized for low power consumption, and has 1080p 60Hz H.265 and VP9 decoders to meet the requirements of high-definition display.
In order to facilitate developers' research and evaluation, Mir provides the matching MYD-JX8MMA7 development board, which is powered by 12V/2A DC and equipped with 1 Gigabit Ethernet interface, 2 SFP optical module interfaces, 1 USB2.0 protocol M.2 B-type socket 5G module interface, 1 SDIO/serial port protocol WIFI/Bluetooth interface, 1 HDMI display interface, 1 LVDS display interface, 1 MIPI CSI interface, 1 DVP camera interface, 1 audio input and output interface, 2 USB HOST Type A, 1 USB Type-C, 2 Micro SD, 1 FMC expansion interface, and 1 Raspberry Pi compatible expansion module interface.
About MiR, a leading embedded processor module manufacturer.
Previous article:Infineon will demonstrate at MWC 2023 how its latest semiconductor technologies can help build a more comfortable and environmentally friendly Internet of Things
Next article:Loongson Zhongke: China Unicom Cloud’s autonomous and controllable cloud has been successfully adapted to the LoongArch architecture
Recommended ReadingLatest update time:2024-11-16 14:57
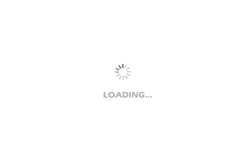
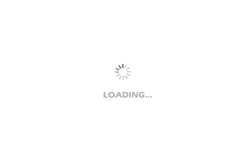
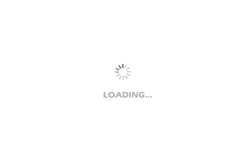
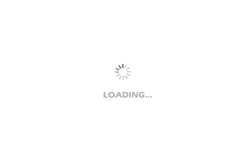
- Popular Resources
- Popular amplifiers
-
Analysis and Implementation of MAC Protocol for Wireless Sensor Networks (by Yang Zhijun, Xie Xianjie, and Ding Hongwei)
-
MATLAB and FPGA implementation of wireless communication
-
Intelligent computing systems (Chen Yunji, Li Ling, Li Wei, Guo Qi, Du Zidong)
-
Summary of non-synthesizable statements in FPGA
- Huawei's Strategic Department Director Gai Gang: The cumulative installed base of open source Euler operating system exceeds 10 million sets
- Analysis of the application of several common contact parts in high-voltage connectors of new energy vehicles
- Wiring harness durability test and contact voltage drop test method
- Sn-doped CuO nanostructure-based ethanol gas sensor for real-time drunk driving detection in vehicles
- Design considerations for automotive battery wiring harness
- Do you know all the various motors commonly used in automotive electronics?
- What are the functions of the Internet of Vehicles? What are the uses and benefits of the Internet of Vehicles?
- Power Inverter - A critical safety system for electric vehicles
- Analysis of the information security mechanism of AUTOSAR, the automotive embedded software framework
Professor at Beihang University, dedicated to promoting microcontrollers and embedded systems for over 20 years.
- Innolux's intelligent steer-by-wire solution makes cars smarter and safer
- 8051 MCU - Parity Check
- How to efficiently balance the sensitivity of tactile sensing interfaces
- What should I do if the servo motor shakes? What causes the servo motor to shake quickly?
- 【Brushless Motor】Analysis of three-phase BLDC motor and sharing of two popular development boards
- Midea Industrial Technology's subsidiaries Clou Electronics and Hekang New Energy jointly appeared at the Munich Battery Energy Storage Exhibition and Solar Energy Exhibition
- Guoxin Sichen | Application of ferroelectric memory PB85RS2MC in power battery management, with a capacity of 2M
- Analysis of common faults of frequency converter
- In a head-on competition with Qualcomm, what kind of cockpit products has Intel come up with?
- Dalian Rongke's all-vanadium liquid flow battery energy storage equipment industrialization project has entered the sprint stage before production
- Allegro MicroSystems Introduces Advanced Magnetic and Inductive Position Sensing Solutions at Electronica 2024
- Car key in the left hand, liveness detection radar in the right hand, UWB is imperative for cars!
- After a decade of rapid development, domestic CIS has entered the market
- Aegis Dagger Battery + Thor EM-i Super Hybrid, Geely New Energy has thrown out two "king bombs"
- A brief discussion on functional safety - fault, error, and failure
- In the smart car 2.0 cycle, these core industry chains are facing major opportunities!
- The United States and Japan are developing new batteries. CATL faces challenges? How should China's new energy battery industry respond?
- Murata launches high-precision 6-axis inertial sensor for automobiles
- Ford patents pre-charge alarm to help save costs and respond to emergencies
- New real-time microcontroller system from Texas Instruments enables smarter processing in automotive and industrial applications
- EEWORLD University Hall----Live Replay: New requirements for connectors in 5G multi-scenario terminal applications and Molex's 5G connection solutions
- MSP430F1232 Minimum System Test MCU AD10 Programming
- Top 10 Noise Issues in High-Resolution Delta-Sigma ADCs
- 【NXP Rapid IoT Review】+ 4. Simple temperature and humidity monitoring
- [CY8CKIT-149 PSoC 4100S Review] + LCD Usage
- RISC-V Manual Chinese Version
- Say goodbye to 2018 and welcome 2019. See how the three pillars of China Mobile IoT dominate the field
- Using MakeCode Driver on BrainPad Development Board
- Please tell me the function of STM32 WWDG window value
- 2. Sensors used in previous "Control" competitions