[Introduction] During the debugging of a PLC project, you may encounter all kinds of strange problems, signal interference is one of them, and it is difficult to find the cause of the problem. Today I will share two cases, hoping to help you.
Example A
1. Description of the phenomenon:
The AO point in the Siemens PLC sends out a 4-20mA current control signal, which is output to the Siemens inverter, but cannot control the inverter to start.
(II) Fault finding:
(1) Suspected AO board problem, using a multimeter to measure the 4-20mA output signal, the signal is normal. (2) Then suspected that there is a problem with the inverter control signal input terminal, replaced with a inverter of the same model, the problem still exists. (3) Use a handheld signal transmitter as a 4-20mA output signal source, output standard current signal to the inverter, the inverter starts, so we rule out the analog output board and inverter faults. (4) It is speculated that the inverter interference signal is transmitted to the analog channel. (5) Therefore, a signal isolation module is added to the PLC analog 4-20mA output channel, the isolator input terminals 5 and 6 are connected to the analog output module, the output terminals 1 and 2 are connected to the inverter, and the terminals 3 and 4 are connected to the external 24VDC power supply, the inverter starts normally. (6) Based on this, it is concluded that the root cause of the problem is the inverter interfering with the analog channel.
(III) Notes:
(1) The PLC power supply and the power system power supply (inverter power supply) are configured separately, and the PLC power supply should use an isolation transformer;
(2) The power line should be separated from the signal line as much as possible, and the signal line should be shielded;
(3) Regardless of analog signal input or analog signal output, analog channels must use signal isolation modules;
(4) Design software filters in PLC programs;
(5) Design the signal ground and power ground separately.
Example B
Some time ago, I saw an analysis and solution to the problem of analog interference. In our actual application, we will encounter many similar problems. Share it with everyone: "There are 10 250KW motors in the workshop, and the load is a high-pressure pump. The inverter uses Schneider ATV71 and is connected to the PLC through DP. The PLC uses Siemens 300, the pressure transmitter is Siemens, and the transmitter to the PLC is 4-20mA analog, and the shielded line is used in the middle.
After debugging, everything was normal after running for a week. After the manufacturer left, pump No. 8 suddenly appeared when it was turned on. The pressure was set to 40 kg, and the actual value was 70 kg. The actual value was set to 80 kg, but it was 110 kg. At first, I suspected that the sensor was faulty, but everything was normal after replacing it with other pumps. After that, the inverter was fully turned on, and pumps No. 3, 4, 5, 6, 7, 9, and 10 also had similar problems. It was speculated that the pressure sensor was interfered by the inverter. The manufacturer suggested adding metal pipe shielding. However, considering the difficulty of on-site construction (the control room is more than 30 meters away from the motor, and all cables are underground).
And I think the harmonic interference of the inverter should be the pressure value fluctuating up and down, and it is rare to see interference causing a linear increase. At first, I suspected that there was something wrong with the manufacturer's program, because the pressure value displayed on the display was always 40 kg, but the inverter output a frequency of 70 kg. The manufacturer disagreed with this view and said that they definitely used the Siemens standard PID block.
I couldn't figure it out. I accidentally discovered that the negative and shielding layers of the manufacturer's sensor were connected to the M of the PLC analog input terminal at the same time. After removing the shielding wire and connecting it to the ground of the equipment, the fault was eliminated. Inference: For a 2-wire sensor, the positive pole has a 24V voltage provided by the PLC, and the negative pole is where the sensor outputs a 4-20mA current. After the shielding wire and the negative pole are connected together, the induced electromotive force on the shielding wire generates a current that enters the PLC input terminal together, causing a superimposed current, thereby forming a linear increase in the pressure value. As a result, the same situation occurred within two days of operation, and what was more serious was that one of the pressure sensors was removed and there was still 40 kg of pressure. Finally, it was found that the negative pole stripping on the PLC input side was too long, short-circuited with each other, causing the signals of other channels to string out. Then I remembered that when I first started debugging, the manufacturer asked me if the equipment ground and the cabinet ground were not on the same ground. After the two ends of the pressure sensor shielding wire were grounded, the interference was particularly strong. It couldn't be displayed. I didn't think much about it and said it was single-ended grounding, and it turned out to be normal. Now I think that the current output side of each sensor was connected together through the shielding wire, causing a short circuit. After that, the ground wire on the sensor side was removed. Since the shielding wires were not connected together, the signal was normal.
Previous article:What is a machinery safety system? What does a machinery safety system require?
Next article:Programming principles of Siemens PLC ladder diagram language
Recommended ReadingLatest update time:2024-11-16 11:34
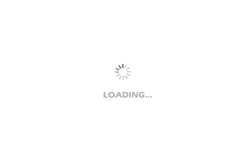
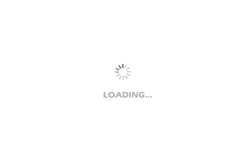
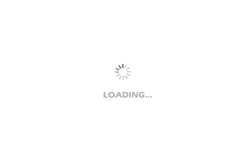
- Popular Resources
- Popular amplifiers
- Huawei's Strategic Department Director Gai Gang: The cumulative installed base of open source Euler operating system exceeds 10 million sets
- Analysis of the application of several common contact parts in high-voltage connectors of new energy vehicles
- Wiring harness durability test and contact voltage drop test method
- Sn-doped CuO nanostructure-based ethanol gas sensor for real-time drunk driving detection in vehicles
- Design considerations for automotive battery wiring harness
- Do you know all the various motors commonly used in automotive electronics?
- What are the functions of the Internet of Vehicles? What are the uses and benefits of the Internet of Vehicles?
- Power Inverter - A critical safety system for electric vehicles
- Analysis of the information security mechanism of AUTOSAR, the automotive embedded software framework
Professor at Beihang University, dedicated to promoting microcontrollers and embedded systems for over 20 years.
- Innolux's intelligent steer-by-wire solution makes cars smarter and safer
- 8051 MCU - Parity Check
- How to efficiently balance the sensitivity of tactile sensing interfaces
- What should I do if the servo motor shakes? What causes the servo motor to shake quickly?
- 【Brushless Motor】Analysis of three-phase BLDC motor and sharing of two popular development boards
- Midea Industrial Technology's subsidiaries Clou Electronics and Hekang New Energy jointly appeared at the Munich Battery Energy Storage Exhibition and Solar Energy Exhibition
- Guoxin Sichen | Application of ferroelectric memory PB85RS2MC in power battery management, with a capacity of 2M
- Analysis of common faults of frequency converter
- In a head-on competition with Qualcomm, what kind of cockpit products has Intel come up with?
- Dalian Rongke's all-vanadium liquid flow battery energy storage equipment industrialization project has entered the sprint stage before production
- Allegro MicroSystems Introduces Advanced Magnetic and Inductive Position Sensing Solutions at Electronica 2024
- Car key in the left hand, liveness detection radar in the right hand, UWB is imperative for cars!
- After a decade of rapid development, domestic CIS has entered the market
- Aegis Dagger Battery + Thor EM-i Super Hybrid, Geely New Energy has thrown out two "king bombs"
- A brief discussion on functional safety - fault, error, and failure
- In the smart car 2.0 cycle, these core industry chains are facing major opportunities!
- The United States and Japan are developing new batteries. CATL faces challenges? How should China's new energy battery industry respond?
- Murata launches high-precision 6-axis inertial sensor for automobiles
- Ford patents pre-charge alarm to help save costs and respond to emergencies
- New real-time microcontroller system from Texas Instruments enables smarter processing in automotive and industrial applications
- Schematics that New Electricians Need to Understand
- STM32 timer (automatic reload) experience sharing
- How to design a battery tester for various battery sizes, voltages and form factors
- The development board made of Quectel module BC26 is used to evaluate the power consumption in the DRX mode of the telecom NB-IoT network!
- Graphene battery, fast charging, wireless charging, central control screen, you read that right, this is the electric car of today!
- EEWORLD University Hall----Live Replay: Graphical interface helps rapid development, this is the MSP430? General MCU you want!
- [Sipeed LicheeRV 86 Panel Review] - 7 Waft-based Home Control Applications
- [NXP Rapid IoT Review] + Simulate door lock process and mobile phone control door opening
- Achieving 5G performance requires Qorvo GaN FEM and waveguide antenna technology
- Electric vehicle charging port communication protocol