As the first pure electric sports car of the Porsche brand, Taycan also has many innovative technologies. Its "flat wire motor" (Hair-Pin hairpin motor) not only has excellent driving performance, but is also a technology that will lead the next generation of new energy vehicle drive systems. At the Frankfurt Motor Show that just ended, Great Wall Motors and parts supplier Schaeffler demonstrated the technical strength of their respective flat wire motors. How strong is this technology? Why is it generally regarded as the "key" to open a new era of electric drive in the industry?
1. Compared with the round wire used in traditional motors, flat wire motors use flat wires. Its advantages are that the motor is more compact, saves more materials, and has stronger power.
2. Flat wire motors were first used by foreign automakers, such as Toyota Prius and Chevrolet Volt. There are few domestic application cases, and automakers have not yet adopted them on a large scale.
3. On the technical level, domestic flat wire motors face challenges in design, manufacturing, and raw materials. The industry is not yet mature, resulting in high initial application costs. When the market matures, flat wire motors will be able to reduce vehicle costs and improve their performance.
● What is a flat wire motor?
The counterpart of the flat wire motor is the "round wire motor". The difference between the flat wire and round wire is the shape of the wire used for the stator winding in the motor. Traditional motors use round wires, while flat wire motors use flat rectangular wires.
The reason why flat wire motors will become a future trend is determined by the development of new energy vehicle electric drive systems. Features such as miniaturization, integration, and high power density are the evolution direction of new energy vehicle electric drive systems. After all, drive systems with large size, heavy weight, and weak power are not welcome in the new energy vehicle market. Obviously, the use of flat wires can greatly increase the slot fill rate (referring to the proportion of space occupied in the slot after the coil is placed in the slot), because there are gaps between round wires, while flat wires are tighter. In layman's terms, the higher the slot fill rate, the more wires there are in the coil, the stronger the magnetic field generated, and the greater the power of the motor. Data shows that in the same space, flat wire motors can be filled with 20-30% more wires, which can be understood to some extent as increasing the motor power by 20-30%. Conversely, on the premise of achieving the same power density, the size of the flat wire motor will also be more compact.
Compared with traditional motors, flat wire structure has other advantages. It greatly increases the contact area between wires, so the heat dissipation capacity will be stronger. And because the winding volume is smaller, there are fewer consumables. Motors are key components that play a pivotal role in the process of converting electrical energy into mechanical energy. Reflected in the whole vehicle, flat wire motors can provide better acceleration performance and less noise, greatly improving the performance of the whole vehicle. In short, flat wire motors conform to the development trend of new energy vehicles. Whoever can take the lead in developing and mass-producing flat wire motors can better seize the market and seize the dividends of the explosion of new energy vehicles. ● Foreign countries take the lead in demonstration and application, while China is still in the early stages. Many years ago, only a few new energy vehicles produced by foreign automobile manufacturers adopted flat wire motor technology. For example, in 2007, Chevrolet Volt was equipped with a flat wire motor provided by Remy (which has been acquired by Magna); Nissan, Toyota and other automakers have also used this technology (the flat wire motor of Toyota's fourth-generation Prius comes from Denso of Japan). Today, domestic automakers and parts suppliers have also been involved in this technology. At this year's Frankfurt Motor Show, Great Wall Motors' majority-owned parts company Honeycomb Yichuang showcased its self-developed and produced "flat wire technology" electric drive integrated system. In addition, OEMs including SAIC, BYD and BAIC, as well as motor companies such as Founder Motor and Halla Motor have also started corresponding research.
Representative applications of flat wire motors abroad include the Chevrolet Volt and Toyota Prius, and many domestic car companies and motor manufacturers have started technology research and development.
Niu Mingkui, general manager of Founder Motor, said, "Domestic flat wire motors are generally in the initial stage. Many vehicle and parts companies are developing products. At present, there are 3-5 motor factories in China engaged in the development of flat wire motor technology, and about 4 vehicle factories are also conducting research and development." Another report shows that according to the research and development progress of domestic OEMs and motor companies, domestic flat wire motors will be industrialized as early as 2020, and the market penetration rate is expected to reach 67% in 2025. In fact, at present, the application of flat wire motors in the domestic market is relatively "cold". Niu Mingkui said, "There are still few cases of large-scale application of flat wire motors in China, and currently only one model equipped with this technology has been put on the market." He further explained that there are many companies and projects that develop products based on flat wire motors, and more companies have begun to conduct intensive research, and will develop more projects based on flat wire motors in the future.
Domestically, flat wire motors are still in the catching-up stage and the market is not yet mature. Although it is a future development trend, car companies have not yet made large-scale layouts.
An unnamed person (who is the technical director of a research institute of a large domestic independent brand automobile company) told Autohome that "there are not many applications in China at present. Just like fuel cells, although everyone knows that the technology is good, the various OEMs will not go into large-scale mass production in advance." Overall, flat wire motor technology was first applied by foreign car companies, and has achieved a good demonstration effect in the new energy drive motor market, while the domestic market is still catching up.
● Design/manufacturing and other aspects are challenging but can reduce vehicle costs
Although in the long run, flat wire motors are the future development direction of drive motors. While having many advantages, they also have disadvantages, such as difficulty in design, difficulty in process manufacturing, and greater wear and tear. From another perspective, pain points such as raw materials, production processes, and professional manufacturing equipment have become barriers to the industrialization of flat wire motors, which is why they have not yet been widely used.
Compared with round wire motors, flat wire motors also have their disadvantages, which can be simply summarized as difficult design, difficult process, difficult equipment, difficult flat wire, and lossy.
"Flat wire motor is a technology that is completely different from traditional motors in terms of product design and manufacturing process." Niu Mingkui said that especially the production process, such as coil forming, twisting, welding, impregnation, etc., all require new development. At present, it is still monopolized by European and American companies, which will become the main bottleneck for the domestic mastery of core technologies. "Whoever can master the full range of core technologies such as design and manufacturing can truly achieve technological breakthroughs in the field of flat wire motors." Niu Mingkui said. The current market situation is indeed the case. At present, most manufacturers with the ability to mass produce flat wire motors are international players, such as Denso, Hitachi Motor, and Schaeffler of Germany. In China, HUAYU Automotive, a parts company under SAIC Group, has achieved partial shipments of flat wire motors in 2017. The "3-5 motor factories" and "about 4 OEMs" mentioned above have very different capabilities in the development, production and manufacturing of flat wire motor technology. Niu Mingkui said, "Most manufacturers rely mainly on imported equipment to solve process problems. Only a small number of outstanding companies have achieved all-round capacity accumulation and technological breakthroughs from product development to production and manufacturing processes." In addition, another problem caused by upgrading from round conductors to flat rectangular cross-section conductors is that the conductor manufacturing technology at the upstream of the industrial chain also needs to be innovated simultaneously.
Due to the complex process and high precision requirements of flat wire, large-scale mass production is basically impossible through manual manufacturing and must rely on professional high-end equipment.
Technical difficulties are one aspect, and the resulting product cost-effectiveness is another. The above-mentioned anonymous person also mentioned that "flat wire motors are relatively difficult in design and manufacturing." This also reflects that before the market matures, there is a lack of partners to share the costs of research and development and other aspects, which leads to higher costs for car companies to apply this technology. "Profit is king" can just explain why car companies have not carried out large-scale mass production in advance. In view of the technical advantages of flat wire motors, when it crosses the critical point of technical cost reduction and scale cost reduction, the technology is still competitive in the market. Niu Mingkui believes that "compared with traditional round wire motors, flat wire motors can reduce the effective material cost by 8%-12%. If you consider the advantages brought to the performance of the whole vehicle, power consumption and other aspects, the flat wire motor can reduce the cost by about 15%."
Previous article:Introduction to Geely Thor Power Hi.X hybrid system and hybrid electric drive transmission
Next article:How to design and develop SOA based on existing vehicle architecture and software assets
Recommended ReadingLatest update time:2024-11-16 12:55
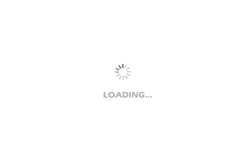
- Popular Resources
- Popular amplifiers
- Huawei's Strategic Department Director Gai Gang: The cumulative installed base of open source Euler operating system exceeds 10 million sets
- Analysis of the application of several common contact parts in high-voltage connectors of new energy vehicles
- Wiring harness durability test and contact voltage drop test method
- Sn-doped CuO nanostructure-based ethanol gas sensor for real-time drunk driving detection in vehicles
- Design considerations for automotive battery wiring harness
- Do you know all the various motors commonly used in automotive electronics?
- What are the functions of the Internet of Vehicles? What are the uses and benefits of the Internet of Vehicles?
- Power Inverter - A critical safety system for electric vehicles
- Analysis of the information security mechanism of AUTOSAR, the automotive embedded software framework
Professor at Beihang University, dedicated to promoting microcontrollers and embedded systems for over 20 years.
- Innolux's intelligent steer-by-wire solution makes cars smarter and safer
- 8051 MCU - Parity Check
- How to efficiently balance the sensitivity of tactile sensing interfaces
- What should I do if the servo motor shakes? What causes the servo motor to shake quickly?
- 【Brushless Motor】Analysis of three-phase BLDC motor and sharing of two popular development boards
- Midea Industrial Technology's subsidiaries Clou Electronics and Hekang New Energy jointly appeared at the Munich Battery Energy Storage Exhibition and Solar Energy Exhibition
- Guoxin Sichen | Application of ferroelectric memory PB85RS2MC in power battery management, with a capacity of 2M
- Analysis of common faults of frequency converter
- In a head-on competition with Qualcomm, what kind of cockpit products has Intel come up with?
- Dalian Rongke's all-vanadium liquid flow battery energy storage equipment industrialization project has entered the sprint stage before production
- Allegro MicroSystems Introduces Advanced Magnetic and Inductive Position Sensing Solutions at Electronica 2024
- Car key in the left hand, liveness detection radar in the right hand, UWB is imperative for cars!
- After a decade of rapid development, domestic CIS has entered the market
- Aegis Dagger Battery + Thor EM-i Super Hybrid, Geely New Energy has thrown out two "king bombs"
- A brief discussion on functional safety - fault, error, and failure
- In the smart car 2.0 cycle, these core industry chains are facing major opportunities!
- The United States and Japan are developing new batteries. CATL faces challenges? How should China's new energy battery industry respond?
- Murata launches high-precision 6-axis inertial sensor for automobiles
- Ford patents pre-charge alarm to help save costs and respond to emergencies
- New real-time microcontroller system from Texas Instruments enables smarter processing in automotive and industrial applications
- EEWORLD University Hall----Live Replay: Infineon & Intron Explanation- How to Choose a Suitable Automotive MOSFET
- Amway uses LT768 to realize TFT industrial serial port screen solution
- Neopixel Christmas Tree
- Gigabit Network Contactless Connector-SK202 Review Unboxing
- What are the methods of wireless bridge relay transmission?
- Diode selection
- The computer will automatically restart when the LabVIEW program is running
- Master these techniques to easily operate DC-DC circuits!
- TYPEC to HDMI 4K@60HZ docking station CS5265 design reference circuit diagram
- DFT design/digital backend PR/digital backend integration/system software/and other positions, Beijing/Shanghai/Nanjing